Лабораторная работа №3
Уширение при прокатке
Общие сведения
При прокатке наряду с уменьшением толщины заготовки (обжатием) и увеличением длины (вытяжкой), происходит увеличение ширины заготовки (уширение). Под уширением Δb понимают разность между шириной заготовки после прокатки b1 и до прокатки b0, т.е.
Δb = b1 - b0. (14)
Уширение сопутствует любому процессу прокатки, как в холодном, так и в горячем состоянии.
В большинстве случаев уширение представляет собой отрицательное явление: снижает общую вытяжку при прокатке, способствует утонению кромки. В результате неравномерной деформации в кромках возникают значительные растягивающие напряжения, которые могут вызвать трещи- нообразование.
Уширение при сортовой прокатке используют как средство лучшего заполнения калибра.
Умение рассчитать уширение требуется при горячей прокатке листовой заготовки для уменьшения количества боковой обрези, при расчете ширины слитка, а также для правильной установки эджерных валков.
На величину уширения влияет большое количество факторов:
1) величина обжатия;
2) толщина заготовки;
3) число пропусков;
4) температура прокатываемого металла;
5) коэффициент трения;
6) диаметр валков;
7) ширина, полосы.
Для расчета уширения известно большое количество формул, из которых наиболее правильными считаются формулы, выведенные на основании отношения
1п (b1/b0)
1п (h1/h0)
Одна из таких формул, полученная как следствие основных законов течения пластической среды, имеет вид
где θ - показатель уширения, который определяют по графику (рис.12).
Функция представлена в виде номограммы (рис. 13).
1 – Δh=0,0-1,0 4 – Δh=2,1-2,5
2 – Δh=1,1-1,5 5 – Δh=2,6-3,0
3 – Δh=1,6-2,0 6 – Δh=3,1-3,5
Рисунок 12 - Графики для определения показателя уширения θ
Рисунок 13 – Номограмма для определения функции λ θ/(1-θ)
Кроме того, уширение можно рассчитать по формуле Зибеля:
![]() |

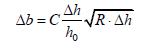
Установлено, что уширение распределяется равномерно по ширине полосы. Однако, рассматривая процесс уширения при прокатке, нужно помнить о законе наименьшего сопротивления, а т. к. периферийные слои полосы встречают меньшее сопротивление своему перемещению в ширину, то они и уширяются больше, что и приводит к появлению растягивающих напряжений и образованию трещин на кромках.
Методика проведения работы
Часть 1. Влияние обжатия на величину уширения
Алюминиевые отожженные (или свинцовые) образцы толщиной h0 = 3,0; 4,0; 5,0; 7,0 мм, шириной b0 = 30 мм, длиной 10 = 60 мм, прокатывают до толщины h1 = 2,5 мм на сухих (протертых ацетоном и мелом) валках. Для установки зазора между валками предварительно прокатывают черновой образец. До прокатки образец размечают (рис.14) и измеряют в трех точках ширину, длину между крайними рисками (10 = 50 мм) и толщину.
Рисунок 14 – Образец для определения уширения
После прокатки в этих же точках измеряют толщину h1, длину между крайними рисками, ширину и берут среднее b1, сравнивают ее с расчетной шириной по формулам (15) и (16). Все данные заносят в табл. 3.1 и строят графики на миллиметровке в координатах b1 - Δh для рассчитанного и измеренного значения b1.
Таблица 3.1
|
Часть 2. Влияние ширины полосы на уширение
Алюминиевые образцы шириной 5, 10, 20, 50 мм; длиной 60 мм и толщиной 2 мм прокатывают с одинаковым обжатием за проход Δh = 1 мм. Тщательно замеряют толщину и ширину образцов до и после прокатки. Во избежание искажения результатов образцы следует задавать в валки строго перпендикулярно. По формулам (14), (15) и (16) определяют расчетную ширину образца. Все результаты измерений заносят в табл. 3.2 и на миллиметровой бумаге строят график зависимости уширения Δb от отношения
b0/h0).
Таблица 3.2
№ образца | h0, мм | h1 , мм | Δh, мм | λ | b0, мм | b1 , мм | Δb, мм | b1 расчетная, мм | |
по формуле (15) | по формуле (16) | ||||||||
Из алюминия или свинца изготавливают две одинаковые треугольные пластины толщиной h0=2 мм (рис. 15).
Рисунок 15 – Пластины для определения уширения в
зависимости от ширины
Тщательно замеряют толщину и ширину пластин в каждой точке 1, 2, 3, 4, 5, 6. Затем пластины складывают и одновременно прокатывают с обжатием Δh =1 мм. Тщательно замеряют толщину и ширину после прокатки в тех же точках. Исходя из закона постоянства объема и пренебрегая уширением, по формуле
l1 = l0 • λ
находят теоретическую длину полосы и строят теоретический треугольник АВС. По замеренным данным строят действительный треугольник AFD.
Заштрихованная площадь характеризует уширения. Все данные заносят в табл. 3.3.
Таблица 3.3
Точка | h0, мм | h1 , мм | Δh, мм | λ | b0, мм | b1 , мм | Δb, мм | b1 расчетная, мм | |
по формуле (15) | по формуле (16) | ||||||||
Часть 3. Влияние коэффициента трения на уширение
Два алюминиевых образца размером 2х40х60 мм прокатывают на стане с Dв = 100 мм с одинаковым обжатием Δh =1 мм: один на сухих (протертых ацетоном) валках, другой на смазанных машинным маслом. Тщательно замеряют толщину и ширину до и после прокатки. Проводят расчеты ширины по формулам (14) (15) и (16). Все данные заносят в табл. 3.4.
Таблица 3.4
Состояние валков | h0, мм | h1 , мм | Δh, мм | λ | b0, мм | b1 , мм | Δb, мм | b1 расчетная, мм | |
по формуле (15) | по формуле (16) | ||||||||
Со смазкой | |||||||||
Без смазки |
Вывод_______________________________________________________________________________________________________________________________________________________________________________________________________________________________________________________________