Тип производства, как общая организационно-техническая характеристика производства определяется главным образом степенью специализации рабочих мест, величиной производства и формой движения изделия на рабочем месте.
Тип производства и соответствующие ему формы организации работы определяют также характер технологического процесса и его построение.
Поэтому прежде чем приступить к проектированию технологического процесса механической обработки деталей, необходимо, исходя из заданной программы выпуска, установить тип производства - единичное, мелкосерийное, среднесерийное, крупносерийное или массовое.
Для предварительного определения типа производства можно использовать годовой объём выпуска и массы детали по таблице 4.
Таблица 4 – Зависимость типа производства от годового объёма выпуска и массой изделия.
Производство | Годовой объём выпуска, шт | ||
Легкий (массой до 10 кг.) | Средний (массой от 10 до 100 кг.) | Тяжелых (массой более 100 кг.) | |
Единичное | До 100 | До 10 | До 5 |
Мелкосерийное | 100 - 500 | 10 - 200 | 5 - 100 |
Среднесерийное | 500 - 5000 | 200 – 500 | 100 – 300 |
Крупносерийное | 5000 – 50000 | 500 – 5000 | 300 – 1000 |
Массовое | Более 50000 | Более 5000 | Более 1000 |
Масса детали – 0.478 кг
Согласно заданию годовой объём выпуска равен 900 шт. Предварительно выбираем среднесерийный тип производства.
Тип производства согласно ГОСТ 3 1108-74 характеризуется коэффициентом закрепления операций за одним рабочим местом или единицей оборудования.
Тип производства определяется коэффициентом Кз.о.:
(1.7)
где О – число всех различных операций.
Р – число рабочих мест.
Если Кз.о. > 40 – единичное производство;
Кз.о. = 20…40 – мелкосерийное производство;
Кз.о. = 10…20 – среднесерийное производство;
Кз.о. = 1…10 – крупносерийное производство;
Кз.о. = 1 – массовое производство.
Серийный тип производства характеризуется изготовлением ограниченной номенклатуры изделий партиями, повторяющимися через определённые промежутки времени. Серийное производство подразделяется на крупно-, средне-, мелкосерийное производство в зависимости от количества изделий в партии, их характера, трудоёмкости, частоты повтора серий в течение года. Подразделение на средне-, крупно-, мелкосерийное типы производства является в принципе условным, так при одном и том же количестве заданных для изготовления деталей, инструментов и оснастки в партии, но при различных их размерах, сложности и трудоёмкости, производство может быть отнесено к разным типам. В серийном производстве технологический процесс изготовления изделия преимущественно дифференцирован, т.е. разделён на отдельные самостоятельные операции, выполняемые на определённом оборудовании либо на определённом рабочем месте.
При серийном производстве обычно применяют универсальные, специализированные, агрегатные и другие металлорежущие станки. При выборе оборудования, оснастки и инструмента необходимо производить расчёты затрат и сроков окупаемости, а также ожидаемый экономический эффект от использования оборудования и технологического оснащения.
2 Технологическая часть
2.1 Определение количества деталей в партии и периодичность её запуска
1.
1.
1.1
1.2
1.3
Изготовление деталей или изделий партиями – характерная особенность серийного типа производства.
Производительная партия – группа заготовок одного наименования и типоразмера, запускаемых в обработку одновременно или непрерывно в течение определённого интервала времени.
Операционная партия – производственная партия или её часть, поступающая на рабочее место для выполнения технологической операции.
Размер операционной партии детали определяется по формуле:
, (2.1)
где N - количество деталей одного наименования и размера в годовом объёме выпуска изделий, шт.;
N = 900 шт.
t - необходимый запас заготовок на складе;
t = 5 шт.
Ф - число рабочих дней в году.
Ф = 247 дней.
= 18,31 ≈ 18 шт
Периодичность запуска партии определяется по формуле:
(2.2)
= 4,94 ≈ 5 дней
Следовательно, запуск партии будет производиться через каждые 5 дней.
2.2 Анализ базового технологического процесса
В базовом технологическом процессе в качестве заготовки принята штамповка. Конструкция детали имеет сложную форму, в связи с этим были
установлены большие припуски, а также напуски для упрощения формы заготовки. Это привело к увеличению веса заготовки – коэффициент использования материала составил 0,17, что является низким показателем.
Таблица 5 - Маршрут обработки детали Кронштейн.
Операция | Наименование и содержание операции | Оборудование | Приспособление |
Контрольная. Проверка наличия необходимых клейм, бирок, отсутствия механических повреждений. Контроль на прямолинейность. | Контрольный стол Стол подготовительных работ | ||
Подготовка. Получение заготовки в МАСКе | Стол подготовительных работ | ||
Разметка | Плита 1000*630 | ||
Фрезерная | ВМ127М | Тиски 7200-0220 ГОСТ 16518-96 | |
Слесарная | Верстак | ||
030К | Контрольная. Проверка габаритных размеров и наличие маркировки индивидуального номера детали | Контрольный стол | |
035К | Контрольная(УЗК) Проверка сплошности материала заготовки согласно технологической карте ТКНК-У | УД2-12 | |
Комплексная обработка в центрах ЧПУ Обрабатывается контур детали | DMU60mb | Тиски ALLMATIC TC-125 Измерительная головка Renishaw MP-60 | |
Слесарная | Верстак | ||
050К | Контрольная. Проверка расположения, размеров и шероховатости | Контрольный стол | Шаблоны |
Комплексная обработка в центрах ЧПУ Обработка паза, карманов, отверстий, полок. | DMU60mb | Тиски ALLMATIC TC-125 | |
Продолжение таблицы 5 | |||
Измерительная головка Renishaw MP-60 | |||
Слесарная | Верстак | ||
065К | Контрольная. Проверка размеров, толщин, радиусов, фаски, паза. | Плита 1-1-1000*630 | Шаблоны ШЦI-150-0,1 |
Комплексная обработка в центрах ЧПУ тоцовка | DMU60mb | Тиски ALLMATIC TC-125 Измерительная головка Renishaw MP-60 | |
Слесарная. | Верстак | Шаблоны | |
080К | Контрольная. Проверка толщин и шероховатости. | Контрольный стол | |
Слесарная. Зенкование. Снятие заусенец, опиловка острых кромок, зачистка радиусов скруглений, припиливание ступенек. | Верстак | ||
090к | Контрольная. Проверка шероховатости радиусных переходов, фаски. Опломбирование. | Контрольный стол | |
Обезжиривание | |||
Транспортировка. На люминесцентный контроль. | Электрокар | ||
105К | Контрольная. Проверка наличия клейм и целостности пломб. | Плита | |
Транспортировка. Нанесения покрытия и контроля на отсутствие трещин | Электрокар | ||
115К | Контрольная. Проверить наличие клейм о проведении покрытия и контроля на отсутствие трещин после анодирования, проверить целостность пломб | Контрольный стол | |
120К | Контрольная. Измерить массу детали. | ЭП-006 | |
Маркирование | Стол подготовителя работ | ||
Продолжение таблицы 5 | |||
130К | Контрольная. Проверка наличия клейм цеха покрытия, отсутствия механических повреждений и трещин, правильность нанесения маркировки. Клеймить окончательно на детали. | Контрольный стол |
Механическая обработка детали Кронештейн в основном производится на станках с ЧПУ, опиловка и сверление направляющих отверстий производится на верстаке в слесарных операциях. При обработке на станках с ЧПУ используются специальные приспособления, стандартные инструменты.
В целом последовательность обработки поверхностей, применяемые при этом схемы базирования и крепления, позволяют обеспечить необходимое качество изготовления детали.
2.3 Краткая характеристика разрабатываемого технологического процесса
В проектируемом технологическом процессе изготовления детали, предлагаю в качестве заготовки применить горячую штамповку. Горячая штамповка обеспечивает минимальный расход материала и минимальный припуск на механическую обработку, а также понижение веса заготовки. Помимо этого снижение припуска обусловлено введением предварительной обработки на универсальных станках для подготовки баз, что снижает погрешность базирования при обработке на станках с ЧПУ.
В связи с применением горячей штамповки снизилось время на обработку заготовки, так же уменьшился расход режущего инструмента. Так как снизилось время на обработку, снизились расходы на заработную плату рабочим.
Для повышения точности обработки и уменьшения вспомогательного и подготовительно-заключительного времени предлагаю использовать следующую оснастку:
- кондуктор для сверления базовых отверстий при обработке на сверлильном станке;
- комбинированный инструмент для обработки базовых отверстий при обработке на сверлильном станке;
- станочные приспособления для обработки детали на станках с ЧПУ.
Краткое описание обработки:
Технологический процесс обработки можно разделить на три основных этапа:
1) обработка базовых поверхностей (нижней стороны детали). Обработка базовых отверстий;
2) обработка на станках с ЧПУ с двух сторон;
3) доработка детали и отделочные операции.
Первый этап.
Цель этапа: обработка базовых поверхностей, двух базовых отверстий.
Обработка базовых поверхностей производится на универсальном фрезерном станке 6Н13П.
Режущий инструмент:
- фреза концевая 2223-1060 ГОСТ 16225-81 Р6М5 (D50; L200; Lp75; z3; R0);
Затем деталь устанавливается в кондуктор, производится сверление базовых отверстий на радиально-сверлильном станке 257.
Режущий инструмент:
- сверло-зенкер диаметром 15-15,9 Р6М5 ДП.151901.15.34.04.05;
- сверло-зенкер диаметром 11-11,9 Р6М5 ДП.ХХХХ.ХХ.ХХ.ХХ.ХХ;
Мерительный инструмент:
- штангенциркуль ШЦI-150-0,1 ГОСТ 166-89.
Средство контроля:
- калибр-пробка 8133-0932 Н9 ГОСТ 14810-69;
- контрольное приспособление ДП.151901.15.34.03.06.СБ.
Второй этап.
Цель этапа: Обработка детали на станке с ЧПУ DMU50, с использованием станочных приспособлений.
Деталь базируется на двух установочных пальцах диаметром 16g8 и 12g8.
Режущий инструмент фирмы Sandvik Coromant:
- фреза концевая Coromill390 RA390-020ЕН20-11М (D20; L125; L 83;
Lp27; R0; z2), Пластина R390-11 T3 24E-PM1030 (R3)
- фреза концевая Coromill390 RA390-016ЕН1-11L (D16; L100; L 70; Lp27; R0; z2), Пластина R390-11 T3 24E-PM1025 (R3)
- фреза концевая Coromill390 RA390-016М19-11L (D16; L100; L 68; Lp25; R0; z3), Пластина R390-11 T3 24E-PM1025 (R3)
- фреза концевая Coromill390 RA390-014EH14-11F (D14; L100; L 68; Lp25; R0; z2), Пластина R390-11 T3 24E-PM1025 (R3)
- фреза концевая Coromill Plura R216.42-08030 AK16A (D8; L100; L 75; Lp16; R4; z2),
Мерительный инструмент:
- стенкомер С-10А ГОСТ 11358-89;
- штангенциркуль ШЦЦ-1-150-0,01 ГОСТ 166-89;
- штангенциркуль ШЦII-300-0,01 ГОСТ 166-89;
- угломер ГОСТ 5378-88.
Средства контроля:
- шаблон контурный ШК-1;
- шаблон ШК-2;
- шаблон ШК-3;
- шаблон ШК-4;
- калибр-пробка 8133-0944 Н9 ГОСТ 14810-69;
- набор радиусных шаблонов №2 ГОСТ 4126-66;
- образцы шероховатости ГОСТ 9378-94.
Третий этап.
Цель этапа: доработка всех поверхностей.
Доработка отверстия диаметром 16Н8:
- развёртка 2366-3453 Н8 ГОСТ 19268-73 Р6М5 (D16; L196; Lp48; z4).
Отрезка прилива:
- фреза концевая 2223-1060 ГОСТ 16225-81 Р6М5 (D50; L200; Lp75; z3; R0);
Снятие заусенцев, припиловка, доработка поверхностей, покрытие и маркирование.
2.4 Выбор вида заготовки и метод её получения
В современном производстве одним из основных направлений развития технологии механической обработки является использование черновых заготовок с экономичными конструктивными формами, обеспечивающими возможность применения наиболее рациональных и экономичных методов и способов обработки, т.е. обработки с наименьшими производственными отходами.
Выбор вида заготовки для механической обработки во многих случаях является одним из весьма важных вопросов разработки процесса изготовления детали.
Существует несколько видов заготовок:
- сортовой прокат;
- штамповки;
- поковки;
- литьё.
Преимущества сортового проката: является экономически выгодным типом заготовок для единичного и мелко-серийного типа производства из-за низкой цены производства по сравнению со штамповками, поковками и литьём.
Недостатки: потеря большого количества материала, повышенный износ инструмента.
Преимущества штамповки, поковки, литья: минимизированы потери материала, пониженный износ инструмента по сравнению сортовым прокатом. Применяется в средне-, крупно-серийном и массовом типах производства.
Недостатки: дороговизна вследствие необходимости разработки и производства специальных штампов, форм.
Для изготовления детали я выбрала в качестве заготовки горячую штамповку из-за того, что материал детали В95оч не пригоден для литья, и штамповка по сравнению с поковкой обеспечивает высокую точность заготовок и малый отход металла. Применение сортового проката в данном случае экономически не выгодно.
Для изготовления штамповки согласно справочному материалу я задала припуск на сторону два миллиметра, что обеспечивает достаточный запас материала для механической обработки детали и для достижения требуемых точности размеров и качества поверхностей детали. Выбранные штамповочные уклоны способствуют равномерному остыванию заготовки после штампования и свободному выходу из штампа. Плоскость разъёма штампа выбрана так, чтобы конструкция заготовки обеспечивала свободное её извлечение из штампа.
Повышенная точность размеров штамповок достигается постоянством хода пресса и определённости нижнего положения ползуна, что позволяет уменьшить отклонения размеров штамповок на высоте. Штампы не контролируют на сдвиг, так как в конструкции пресса и штампа предусмотрено надёжное направление ползуна направляющих станины, а для точного совпадения верхней и нижней части штампа – направляющие колонки и втулки. Этот метод позволяет увеличить коэффициент использования материала, вследствие более совершенной конструкции штампов, снабжённых верхним и нижним выталкивателями, что позволяет уменьшить штамповочные уклоны, припуски, напуски и допуски и, тем самым, приводит к экономии металла, уменьшению последующей обработки штамповок резанием.
Горячие штамповочные заготовки могут получать различными способами в зависимости от конструкции, размеров и материала.
Изготовление штамповок производится:
1) на молотах.
2) на кривошипных горячештамповочных прессах:
- на гидропрессах;
- на фрикционных прессах;
- выдавливанием.
Я предлагаю использовать изготовление штампа на кривошипных горячештамповочных прессах с выталкивателями. Они обеспечивают улучшенные условия труда, вследствие меньших шумовых эффектов, вибраций и сотрясений почвы, более высокая производительность.
При проектировании формы заготовки я использую напуск для последующего обеспечения базы при механической обработки детали.
2.5 Расчёт припусков
2.
2.1.
2.2.
2.3.
2.4.
2.5.
2.1
2.2
2.3
2.4
2.5
2.5.1 Аналитический метод
За расчётный размер принимаю толщину поперечного ребра, равную 3 мм.
Таблица 6 – Расчётные данные.
Параметры расчёта, мкм | ||||||||
Переход | IT | ∆ | Rz | h | ρ | ![]() | zmin | znom |
0. Штамповка | +1000 -600 | - | - | - | ||||
1. Фрезерование черновое | 92,7 | 99,6 | ||||||
2. Фрезерование чистовое | 3,7 | 99,6 | 99,6 |
IT – допуск размеров на штамповку;
Rzi-1 – шероховатость поверхности после предыдущего перехода;
hi-1 – глубина дефектного слоя после предыдущего перехода;
zобщ - общий припуск на сторону, мм:
zобщ = znom2+znom1, (2.3)
где znom2, znom1 – номинальные припуски на переходы, мм;
znomi – номинальный припуск на сторону, мм:
znomi = zmini+∆i-1 (2.4)
где ∆i-1 – поле допуска перехода в соответствии с квалитетом точности, мкм.
zmini – минимальный припуск на сторону, мм
zmini = , (2.5)
где ρi-1 – пространственное отклонение после предыдущего перехода, мкм;
, (2.6)
где ρк – коробление заготовки, мкм;
, (2.7)
где ∆k = 0,6 – кривизна заготовки, мкм;
L = 249 - длина заготовки, мм;
ρк = = 1494 мкм.
ρсм – смещение штампов при штамповке.
ρсм = 1,4 мм = 1400 мкм
мкм
, (2.8)
где Ку – коэффициент уточнения элементов.
Ку1 = 0,06
Ку2 = 0,04
96,54 мкм
мкм
ε – погрешность установки на данном переходе, мм:
ε = , (2.9)
где εз – погрешность закрепления, мм;
εз = 0.
εб - погрешность базирования, мм;
εб = , (2.10)
где Lmax = 249 длина заготовки, мм;
tgα - тангенс угла перекоса заготовки, мм.
tgα = , (2.11)
где Smax1 и Smax2 - максимальные диаметральные зазоры между базовыми пальцами и отверстиями в заготовке, мм;
L - расстояние между центрами базовых отверстий, мм.
Рисунок 1 - поле допуска посадки базовых отверстий на установочные пальцы ложемента.
Smax1 = Smax2 = 76 мкм = 0,076 мм
L = 152.39 мм
tgα = = 0,0004 мм
εб = 0,0004*249 = 0,0996 мм
zmin1 = = 192 мкм
zmin2 = = 99.6 мкм
znom2 = 99.6+400 = 534 мкм = 0,499 мм
znom1 = 192+2000 = 2192 мкм = 2,192 мм
zобщ = 499+2192 = 2691 мкм = 2.691 мм
Lрасч – расчётный размер:
Lрасч = 3+2*2.691 = 8,382 мм
Округляем расчётный размер до целого и принимаем 8 мм. Разницу между принятым и расчётным размерами, равную 0,382 мм, добавляем к черновому фрезерованию.
Таблица 7 - Промежуточные размеры с предельными отклонениями:
Переход | Промежуточный размер | Припуск |
3-0,250 | 1662 мкм | |
4,662-0,400 | 3.338 мкм | |
![]() |
2.5.2 Статистический метод
При длине заготовки 249 мм и шероховатостями Ra 1,6, и Ra 3,2 рекомендуемый припуск на сторону равен 2 мм. [6, с. 251, табл. 8.43]
Таблица 8 – Размеры на детали и на заготовке
Размер на детали, мм | Размер на заготовке, мм |
2.5 | 6.5 |
6.5 | 10.5 |
R17 | R19 |
R25 | R27 |
2.6 Выбор оборудования
Технологическое оборудование – орудие производства, в которых для выполнения определённой части технологического процесса размещаются материалы или заготовки, средства воздействия на них, а также технологическая оснастка и при необходимости источник энергии. К технологическому оборудованию относятся литейные машины, прессы, станки, печи, гальванические ванны, испытательные стенды и т.п.
Выбор станочного оборудования является одной из важных задач при разработке технологического процесса механической обработке заготовки. От правильного его выбора зависят: производительность изготовления делали, экономное использование производственных площадей, механизации, и автоматизации ручного труда, электроэнергии и в итоге себестоимость изделия.
В зависимости от объёма выпуска изделий выбирают станки по степени специализации и высокой производительности, а также станки с числовым программным управлением.
При выборе станочного оборудования необходимо учитывать:
- тип производства;
- метод достижения заданной точности при обработке;
- необходимую производительность;
- соответствие станка размерам детали;
- мощность станка;
- удобство управления и обслуживания станка;
- габаритные размеры и стоимость станка;
- возможность оснащения высокопроизводительными приспособлениями и средствами механизации и автоматизации.
Для обработки данной детали применяются следующие станки: вертикально-фрезерный станок 6Н13П, радиально-сверлильный станок 257, фрезерный станок с ЧПУ DMU50
|
|
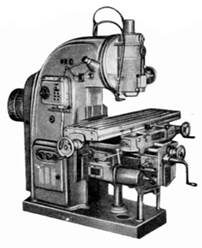
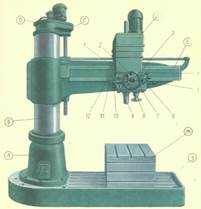
|
Таблица 9 - Технические характеристики станка 6Н13П:
Параметры | Величина |
Рабочая поверхность стола (мм) | 320х1250 |
Мощность двигателя (кВт) | 7.5 |
КПД станка | 0.8 |
Число оборотов шпинделя: Min:Max | 31.5:1650 |
Подача стала продольные и поперечные (мм/мин) Min:Max | 25:1250 |
Подачи вертикальные (мм/мин) Min:Max | 8:400 |
Таблица 10 - Технические характеристики станка 257:
Наибольший диаметр сверления, мм | |
Пределы вылета оси шпинделя от колонны, мм | 500-2000 |
Пределы расстояния от торца шпинделя до плиты, мм | 600-1750 |
Наибольшее осевое перемещение шпинделя, мм | |
Число скоростей вращения шпинделя | |
Пределы чисел оборотов вращения шпинделя в минуту | 11,2-1400 |
Количество величин подач | |
Пределы величин подач шпинделя, мм/об | 0,04-2 |
Мощность главного электродвигателя, кВт |
Таблица 11 - Технические характеристики станка DMU50
Технические характеристики | DMU 50 eVo linear | |
Перемещения по осям X/Y/Z | мм | 500/450/400 |
Мощность главного привода (40/100% DC) | кВт | 35/25 |
Крутящий момент | Нм | 130/87 |
Число оборотов | об/мин | 18000(24000/42000)* |
Быстрые перемещения X/Y/Z | м/мин | 80/50/50 |
Количество инструментов | 30(60/120)* | |
Управляемый наклонно-поворотный стол* | мм | Ø500х380* |
Диапазон наклона | град | 0-108 |
Нагрузка на стол | кг |
Таблица 12 - Система измерения перемещения:
Разрешающая способность | Ось | Размер | Допуск |
Точность ввода | X, Y, Z | мм | 0.001 |
Позиционный допуск | X, Y, Z | мм | 0.010 |
2.7 Выбор приспособлений и режущих инструментов
Технологическая оснастка – это средства технического оснащения, дополняющие технологическое оборудование для выполнения определённой части технологического процесса.
Приспособление - это основная часть технологической оснастки, предназначенная для установки или направления предмета труда или инструмента при выполнении технологической операции. Использование приспособлений способствует повышению точности и производительности обработки, контроля деталей и сборки изделий, обеспечивает механизацию и автоматизацию технологических процессов, снижение квалификации работ, расширение технологических возможностей оборудования и повышение безопасности работ. Современное механосборочное производство располагает большим парком приспособлений, значительную часть которых составляют станочные приспособления.
Приспособления предназначены главным образом для установки объекта, в качестве которого выступает заготовка, деталь или сборочная единица. Установка включает в себя базирование объекта и его закрепление. Поэтому основными частями приспособления являются корпус, базирующие (установочные) и зажимные элементы.
Дополнительно приспособления могут выполнять следующие функции:
- обеспечивать направление режущего инструмента;
- служить базой для установки контрольно-измерительных приборов;
- осуществлять механический или автоматический зажим объекта в приспособлении;
- увеличивать жёсткость при установке базируемого объекта;
- изменять положение детали вместе с приспособлением. Для этого приспособления могут иметь направляющие (кондукторные) втулки, пневмо-гидро- и электроприводы, устройства автоматики, подводимые опоры и др.
Для изготовления детали Кронштейн применяется специальное фрезерное
приспособление с гидравлическим приводом зажима ДП.151901.15.34.03.03.СБ для фрезерной операции на станке с ЧПУ. Использование данного приспособления позволит сократить временные затраты на наладку станка, на установку и закрепление детали, повышает точность базирования и закрепления.
- фреза концевая 2223-1060 ГОСТ 16225-81 Р6М5 (D50; L200; Lp75; z3; R0);
- сверло-зенкер диаметром 15-15,9 Р6М5 ДП.151901.15.34.03.05;
- сверло-зенкер диаметром 11-11,9 Р6М5 ДП.хххххх.хх.хх.хх.хх;
- развёртка 2366-3453 Н8 ГОСТ 19268-73 Р6М5 (D16; L196; Lp48; z4).
- фреза концевая Coromill390 RA390-020ЕН20-11М (D20; Lp27; R0; z2), Пластина R390-11 T3 24E-PM1030 (R3), цанга 391.200-4063, Адаптер EH20-A24.7-SH-185 силовой прецизионный патрон 392.41014-6332100B.
- фреза концевая Coromill390 RA390-016ЕН1-11L (D16; Lp27; R0; z2), Пластина R390-11 T3 24E-PM1025 (R3), цанга 391.160-4063, Адаптер EH16-A24.7-SH-185 силовой прецизионный патрон 392.41014-6332100B
- фреза концевая Coromill390 RA390-016М19-11L (D16; Lp25; R0; z3), Пластина R390-11 T3 24E-PM1025 (R3), цанга 391.160-4063, Адаптер EH16-A24.7-SH-185 силовой прецизионный патрон 392.41014-6332100B
- фреза концевая Coromill390 RA390-014EH14-11F (D14; Lp25; R0; z2), Пластина R390-11 T3 24E-PM1025 (R3), цанга 391.140-4063, Адаптер EH14-A24.7-SH-185 силовой прецизионный патрон 392.41014-6332100B
- фреза концевая Coromill Plura R216.42-08030 AK16A (D8; L100; L 75; Lp16; R4; z2), цанга 391.080-4063, силовой прецизионный патрон 392.41014-6332100B
2.8 Методы и средства контроля детали
Под контролем в широком смысле имеется в виду понятие, включающее в себя определение как количественных, так и качественных характеристик, например, контроль дефектов наружной поверхности, контроль внутренних пороков металла и др.
В технике наряду с понятием «контроль» широко применяется понятие «измерение».
Измерение – нахождение физической величины с помощью специальных технических средств.
Точность измерений – качество измерений, отражающее близость их результатов к истинному значению измеряемой величины.
Погрешность измерения – отклонение результата измерения от истинного значения измеряемой величины.
Под методом измерения понимается совокупность используемых измерительных средств и условий их применения.
Измерительные средства – это технические устройства, используемые при измерениях и имеющие нормированные метрологические свойства.
Для измерения внутренних и наружных размеров детали используются штангенциркули, ШЦЦ-1-150-0,01 ГОСТ 166-89, ШЦII-300-0,01, ГОСТ 166-89 стенкомер С-10А ГОСТ 11358-89.
Для контроля:
- сложных элементов детали используются шаблоны ШК-2, ШК-4;
- отверстий используются калибр-пробки 8133-0961 Н8 ГОСТ 14810-69,
- соосность отверстий проверяются ДП.151901.15.34.03.06.СБ;
- углов элементов детали используется угломер ГОСТ 5378-88;
- радиусов сопряжений используются набор радиусных шаблонов №2 ГОСТ 4126-66;
- шероховатости обработанных поверхностей используются образцы шероховатости ГОСТ 9378-94.
2.9 Расчёт режимов резания
Существует два метода определения режимов резания: аналитический и статистический.
При определении режимов обработки аналитическим методом сначала
устанавливают глубину резания в миллиметрах. Глубину резания назначают по возможности наибольшую, в зависимости от требуемой степени точности и шероховатости обрабатываемой поверхности и технологических требований на изготовление детали. После установления глубины резания устанавливается подача станка. Подачу назначают максимально возможную, с учётом погрешности и жёсткости технологической системы, мощности привода станка, степени точности и качества обрабатываемой поверхности, по нормативным таблицам и согласовывают с паспортными данными станка. От правильно установленной подачи во многом зависит качество обработки и производительности труда. Для черновых технологических операций назначают максимально допустимую подачу. После установления глубины резания и подачи определяют скорость резания по эмпирическим формулам с учётом жёсткости технологической системы.
При определении режимов обработки статистическим (табличным) методом используют нормативные в зависимости от выбранного типа производства и установленного вида обработки заготовки. Табличный метод определения режимов резания сравнительно прост. Определение режимов резания табличным методом широко применяют в производственных условиях, т.к. этот метод даёт возможность ускорить разработку технологических процессов и сократить сроки подготовки к запуску изготовления данного изделия.
Инструмент к фрезерному станку 6Н13П.
1) фреза концевая 2223-1060 ГОСТ 16225-81 (D50; L200; Lp75; z3; R0) Р6М5.
υ - скорость резания, м/мин:
, (2.12)
где Cʋ - поправочный коэффициент;
q, m, x, y, u, p – показатели степеней;
Cʋ = 185,5; q = 0,45; m = 0,33; x = 0,3; y = 0,2; u = 0,1; p = 0,1;
D = 50 – диаметр фрезы, мм;
T = 120 – стойкость фрезы, мин;
t =1– глубина резания, мм;
Sz = 0,18 – подача на зуб, мм;
В =10,5– ширина фрезерования, мм;
z = 3 – количество зубьев фрезы;
Kυ – общий поправочный коэффициент на скорость резания, учитывающий фактические условия резания:
Kυ = , (2.13)
Kmυ = 1 – коэффициент на обрабатываемый материал;
Knυ = 0,9 – коэффициент, учитывающий состояние поверхности заготовки;
Kuυ = 1 – коэффициент на инструментальный материал.
Kυ = 1*0,9*1 = 0,9
= 199 м/мин
n - частота вращения шпинделя, об/мин:
, (2.14)
где ʋ - скорость резания, м/мин;
π – математическая константа;
D – диаметр фрезы, мм.
= 1267 об/мин
Принимаем частоту вращения шпинделя согласно паспортным данным станка:
nпасп = 1200 об/мин
Sm - минутная подача, мм/мин:
, (2.15)
= 648 мм/мин
Принимаем минутную подачу согласно паспортным данным станка:
630 мм/мин
υрасч – расчётная скорость резания, м/мин:
, (2.16)
= 188,4 м/мин
2) изменяются условия резания.
t = 1 мм
Sz = 0,2 мм
В = 50 мм
= 170,01 м/мин
Принимаем частоту вращения шпинделя согласно паспортным данным станка:
= 1082,86 об/мин
nпасп = 1000 об/мин
= 480 мм/мин
Принимаем минутную подачу согласно паспортным данным станка:
400 мм/мин
υрасч – расчётная скорость резания, м/мин:
, (2.17)
= 157 м/мин
1) cверло-зенкер диаметром 15 - 15,9 ДП.151901.15.34.03.05
Режимы резания при обработке сверлением.
υ - скорость резания, м/мин:
, (2.18)
где Cʋ - поправочный коэффициент;
q, m, y – показатели степеней;
Cʋ = 40,7; q = 0,25; m = 0,125; y = 0,45
D = 15 – диаметр элемента сверла, мм;
T = 60 – стойкость сверла, мм;
t = 15 – глубина резания, мм;
S = 0,7– подача на оборот, мм/об;
Sпасп = 0,63 – подача на оборот согласно паспортным данным станка, мм/об;
Kυ – общий поправочный коэффициент на скорость резания, учитывающий фактические условия резания:
Kυ = , (2.19)
где Kmυ = 0,8 – коэффициент на обрабатываемый материал;
Kiυ = 1 – коэффициент, учитывающий глубину обрабатываемого отверстия;
Kuυ = 1 – коэффициент на инструментальный материал.
Kυ = 0,8*1*1 = 0,8
= 47,61 м/мин
= 891 об/мин
Принимаем частоту вращения шпинделя согласно паспортным данным станка:
nпасп = 800 об/мин
= 37,68 м/мин
Режимы резания при обработке зенкерованием, м/мин:
, (2.20)
где Cʋ - поправочный коэффициент;
q, m, y, x – показатели степеней;
Cʋ = 27,9; q = 0,2; m = 0,125; y = 0,4; x = 0,1
D = 15,9 – диаметр элемента зенкера, мм;
T = 25 – стойкость зенкера, мин;
t = 0,5 – глубина резания, мм;
S = 0,63 – подача на оборот, мм/об;
Sпасп = 0,63 – подача на оборот согласно паспортным данным станка, мм/об;
= 42,18 м/мин
= 844 об/мин
Принимаем частоту вращения шпинделя согласно паспортным данным станка:
nпасп = 800об/мин
= 39,9 м/мин
2) cверло-зенкер диаметром 11 - 11,9 ДП.151901.15.34.03.05
Режимы резания при обработке сверлением.
υ - скорость резания, м/мин:
, (2.21)
где Cʋ - поправочный коэффициент;
q, m, y – показатели степеней;
Cʋ = 40,7; q = 0,25; m = 0,125; y = 0,45
D = 11 – диаметр элемента сверла, мм;
T = 40 – стойкость св