Колесная пара является наиболее ответственным узлом вагона, от исправного состояния которого в решающей степени зависит безопасность движения. Колесные пары несут на себе массу всего вагона, направляют его по рельсовому пути и воспринимают жесткие и разнообразные по направлению удары от неровности пути, собственных дефектов и стыков рельсового пути. При торможении колесная пара имеет значительный износ от тормозных колодок, а при движении юзом на поверхности колеса образуются выработки, называемые ползунами. Особенно быстро износ гребня колеса происходит при прохождении поездом кривых участков пути. Большинство пассажирских вагонов в пути следования делают частые остановки, которые происходят после срабатывания автоматических тормозов. При торможениях отдельные участки колес нагреваются до высоких температур и получают местную закалку с образованием участков повышенной твердости, на которых в дальнейшем из-за ударных нагрузок появляются трещины, что приводит к разрушению металла по поверхности колеса.
В настоящее время в России для вагонов, эксплуатируемых со скоростями движения до 160 км/ч, используются типы колесных пар, приведенные в табл. 2.1.
Тип колесной пары определяется типом оси и диаметром колес, а также конструкцией подшипников и способом крепления их на оси. Буквы РУ и Ш в обозначении типа оси означают: Р — роликовая, т.е. для подшипников качения; У — унифицированная, т.е. для грузовых и пассажирских вагонов; Ш — крепление подшипников на оси при помощи шайбы.
На тележках пассажирских вагонов последних лет постройки используют дисковые тормоза. В этом случае на средней части оси имеются посадочные места для крепления тормозных дисков. Колесные пары пассажирских вагонов, эксплуатируемые со скоростями движения более 160 км/ч для увеличения устойчивости и снижению износов имеют измененный профиль поверхности катания колеса.
Колесная пара (рис. 2.1) состоит из оси с напрессованными на неё двумя колесами. Наружная поверхность колеса, соприкасающаяся с рельсом, называется поверхностью катания. Профиль поверхности катания имеет определенную форму и размеры. Гребень обода направляет колесную пару и предохраняет вагон от схода с рельсов. Колесная пара является тем элементом, который обеспечивает непосредственный контакт вагона и пути. От точности геометрических размеров и других параметров колесной пары в значительной мере зависят безопасность движения и ходовые качества вагона.
Колесные пары РУ 1-950 и РУ1Ш-950 отличаются друг от друга устройствами шеек осей. Колесные пары типа РВ2Ш-957-Г выпускаются для грузовых вагонов новой постройки с нагрузкой от оси на рельсы до 245,2 кН (25,0 тс). Для грузовых вагонов Разработаны и проходят испытания колесные пары с осевыми нагрузками 30 и 27 тс.
Таблица 2.1
Ширина обода нового колеса — 130 мм. Диаметр колеса измеряют по кругу катания, которым называется совокупность точек на поверхности катания колеса, удаленных от внутренней грани на расстояние 70 мм. В этом же сечении следует измерять толщину обода колеса. Расстояние между кругами катания колес одной колесной пары — 1580 мм.
Расстояние между внутренними боковыми поверхностями колес составляет 1439—1442 мм.
![]() |
2.2. Конструкция осей
Ось служит для размещения колес и буксовых узлов. Она представляет собой круглый стержень переменного по длине поперечного сечения, каждая часть которого имеет свое название и назначение.
![]() |
Ось (рис. 2.2) имеет шейки 1 для размещения роликовых подшипников; предподступичные части 2, служащие ступенью перехода от шейки к подступичнои части оси и предназначенные для установки лабиринтных колен букс; подступичные части 3, на которые прочно насаживают колеса; среднюю часть 4. Все части оси имеют цилиндрическую форму. Средняя часть выполняется цилиндрической или с коническими переходами от подступичных осей к средней
части оси. Оси колесных пар с дисковыми тормозами имеют цилиндрическую часть с посадочными местами для тормозных дисков. Колесные пары с приводом генератора от средней части оси также могут иметь посадочные места для установки деталей крепления привода на оси.
Для снижения концентрации напряжений в местах изменения диаметров оси делают плавные переходы — галтели, выполненные определенным радиусом. Снижение концентрации напряжения, вызнанных посадкой деталей подшипников качения, достигается разгружающей канавкой, расположенной у начала галтели на шейке оси. На торцах всех типов осей имеются центровые отверстия для установки и закрепления оси или сформированной колесной пары в центрах токарных станков. Основной деформацией в оси является деформация поперечного изгиба. Поэтому в соответствии с нагрузками наименьший диаметр имеют шейки, а наибольший — подступичные части. Средние части имеются конические переходы от подступичных частей к середине оси. Некоторые оси имеют цилиндрическую форму средних частей. Увеличение диаметра подступичнои части оси обусловлено также наличием напряжений от посадки колеса и влияния коррозии трения.
В вагонных колесных парах наибольшее применение нашли оси Двух типов: РУ1 и РУ1Ш. Обе предназначены для размещения подшипников качения и различаются конструктивным исполнением шеек в зависимости от способа торцевого крепления подшипников: гайкой или шайбой. Конструктивное исполнение оси РУ1 (рис. 2.2, а) характеризуется наличием на ее концах резьбовых частей М110 для гаек, а на торцах — пазов с двумя резьбовыми отверстиями (резьба М12) для размещения стопорных планок и крепления их болтами.
Ось РУ1Ш (рис. 2.2, б) имеет на торцах четыре резьбовых отверстия (резьба М20) для крепления приставной шайбы болтами. Ось при этом получается короче, а ее изготовление упрощается. В эксплуатации имеются оси и с тремя резьбовыми отверстиями. Свободные участки торцов осей используют для нанесения клейм и знаков об изготовлении, формировании и освидетельствовании колесных пар.
Диаметры отдельных частей оси d1, d2, d3, d4 ( см. рис. 2.2) соответственно составляет 130, 165, 194 и 172 мм. Гарантийный срок эксплуатации осей установлен 8,5 лет, а средний срок службы — 15 лет.
Для грузовых вагонов новой постройки с повышенными осевыми нагрузками выпускается колесная пара с усиленной осью типа РВ2Ш с нагрузкой на рельсы до 245,2 кН (25,0 тс). Колесная пара состоит из оси типа РВ2Ш с торцевым креплением подшипников передней крышкой и тремя болтами М24 (или четырьмя болтами М20) и цельнокатаных колес из стали марок 2 или Т. У оси типа РВ2Ш диаметр шейки — 150 мм, диаметр предподступичной части — 185 мм, диаметр подступичнои части — 210 мм. Средняя часть имеет цилиндрическую форму диаметром 180 мм.
Завершены испытания пустотелых осей. Их применение обусловлено тем, что наибольшие напряжения при изгибе и кручении возникают в наружных волокнах оси и наименьшие — внутри ее. Поэтому у пустотелых осей величина моментов сопротивления при изгибе, кручении практически такие же, как и у сплошных, но масса у них меньше, что позволяет экономить металл. Пустотелые оси могут быть изготовлены прокаткой на специальных станках и методом центробежной отливки. По сравнению со сплошными осями полые оси имеют массу на 100—110 кг меньше, в результате расход металла на изготовление оси сокращается на 15 %. Ось имеет увеличенный диаметр подступичнои части, что позволяет повысить прочность соединения колеса с осью.
Вагонные оси изготавливают из стали ОС методом ковки, штамповки, винтовой прокатки или радиально-ротационного горячего деформирования. В процессе изготовления оси проходят специальную термообработку — нормализацию с обязательной проверкой механических характеристик. Оси должны быть подвергнуты механической обработке и упрочнению накаткой роликами по всей длине оси, включая галтели. Каждая ось при изготовлении и ремонте испытывается магнитопорошковым и ультразвуковым методами неразрушающего контроля и выборочно — на растяжение и твердость.
Конструкция колес
Основным поставщиком колес для подвижного состава России является Выксунский металлургический завод — крупнейший в Европе колесопрокатный комплекс, выпускающий 850 тыс. колес ежегодно (на 2012 г.). Вагонные колеса, особенно поверхность катания, являются наиболее изнашиваемыми и повреждаемыми частями вагона, поэтому к материалу колес, их размерам, форме и технологии изготовления всегда предъявлялись повышенные требования. На основании многолетнего опыта эксплуатации в настоящее время к серийному изготовлению приняты цельнокатаные стальные колеса с номинальным диаметром 957 мм.
Конструкция и основные размеры колеса приведены на рис. 2.3. Цельнокатаное колесо имеет обод /, диск 2 и ступицу 3; ширина обода — 130 мм. Поверхность обода 4 называется поверхностью катания. Переход от ступицы к ободу выполнен в форме диска, расположенного под некоторым углом к этим частям, что придает колесу упругость и снижает воздействие динамических сил. Диск слегка конусный: у ступицы его толщина больше, чем у обода. Толщина обода — 70 мм. Внутренняя поверхность обода а называется внутренней гранью, а наружная б — наружной.
![]() |
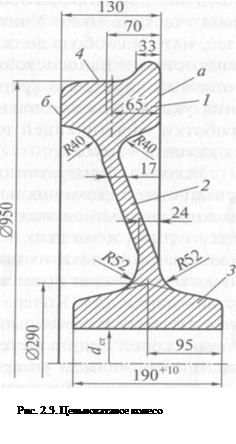
Рис.2.4 Профиль катания колеса
Стандартный профиль поверхности катания (см. рис. 2.4) образован гребнем, скруглением 15 мм, как у головки рельса, для снижения износа, конической поверхностью с конусностями 1:10 1:3,5 и фаской 6x45°.
Гребень направляет движение и предохраняет колесную пар от схода с рельсов. Он имеет высоту 28 мм и толщину 33 мм, измеренную на высоте 18 мм; угол наклона наружной грани гребня составляет 60°. Наличие конусностей 1:10 и 1:3,5 центрирует ко лесную пару на рельсовом пути и обеспечивает прохождение кривых участков пути. Учитывая сложные условия эксплуатации ко лес, материал обода должен обладать большой прочностью, ударно вязкостью и износостойкостью; металл ступицы и диска — необходимой вязкостью (упругостью). Ободья колес для удовлетворения указанным требованиям подвергают после механической об работки упрочняющей термической обработке путем прерывисто закалки и отпуска.
Условия эксплуатации колес грузовых и пассажирских вагонов различны, поэтому их изготовляют из различных материалов. Пассажирские вагоны эксплуатируются с высокими скоростями и частыми торможениями, остановками, поэтому для колес пассажирских вагонов локомотивной тяги и немоторных вагонов электро и дизель-поездов применяется сталь, менее склонная к закалке, сталь марки «Л». Колеса грузовых вагонов работают в условиях более высоких напряжений в контакте колеса и рельса, поэтому дл таких колес используется сталь марки 2 ГОСТ 10791 с увеличенным содержанием углерода до 0,55—0,65 %, а в настоящее врем — сталь марки «Т» с твердостью обода 320—360 НВ.
Для перспективных вагонов с осевыми нагрузками 25—30 тс освоено производство колес из сталей марок «Т» или 2 с криволинейным диском. Как показал опыт эксплуатации, колеса из стал марки «Т» в 9—10 раз реже требуют ремонта обточкой, и излом дисков в таких колесах практически прекратились. Криволинейна форма диска и увеличение его толщины около обода до 19—22 м значительно повысили прочность колес.
В процессе изготовления колес на боковой поверхности обода наружной стороны в горячем состоянии наносят специальные знаки и клейма в последовательности: две последние цифры года изготовления, марка стали колеса, номер плавки, номер предприятия изготовителя, клейма приемки, порядковый номер колеса, а также клейма государств-собственников. Для повышения надежности колес разработан метод непрерывной вакуумной разливки стали, что улучшило ее химический состав и структуру. Современные методы термообработки позволили довести твердость материала обода до 350—380 НВ, обеспечивающую значительное увеличение срока эксплуатации колесных пар до образования предельно допустимых дефектов. Диск упрочняется наклепом дробью, толщина обода обеспечивает возможность многократного восстановления профиля поверхности катания путем обточки колесных пар на станках в вагоноремонтных предприятиях.
В вагонном депо Николаевка Московской ж.д. для увеличения межремонтной эксплуатации колесных пар производят плазменные напыления поверхности катания, снижающие в несколько раз интенсивность образования износов.
Профиль колесных пар поездов, эксплуатируемых со скоростями более 160 км/ч, изменен и имеет дополнительную конусность 1:50, а также увеличенный до 65° угол наклона наружной грани гребня. Кроме того, этот профиль имеет горизонтальную площадку длиной 9,3 мм, расположенную от круга катания к внутренней рани колеса. Такая форма профиля уменьшает извилистое движение колесных пар, повышает их устойчивость, что особенно важно при увеличении скоростей движения.
Одним из мероприятий дальнейшего повышения надежности колес является применение колес с механической обработкой по всем поверхностям обода, диска и ступицы, а также использование для колес специальной бейнитной стали. Выксунский металлургический завод освоил выпуск колес для высокоскоростного движения.