Лабораторная работа №4
Опережение при прокатке
Общие сведения
В процессе прокатки в зоне деформации происходит скольжение металла по валкам таким образом, что скорость металла на выходе из валков больше окружной скорости валков, а на входе металла в валки - меньше. Такое явление называется опережением и отставанием. Зона деформации состоит из зоны опережения и зоны отставания (рис. 16). Эти две зоны разделяются нейтральным сечением, положение которого характеризуется нейтральным углом γ.
Рисунок 16 – Определение опережения экспериментальным путем
Опережение является скоростным параметром процесса прокатки и в значительной степени определяет характер распределения и величину давления прокатки, и играет особенно большую роль при прокатке в многоклетьевых непрерывных станах.
Обозначим скорость входа металла в валки V0, скорость выхода металла из валков - V1, а окружную скорость валков - V (рис.16). В нейтральном сечении скорость металла и скорость валков одинаковы. Опережение выражается в процентах и может быть найдено по формуле
Если известно положение нейтрального сечения (т.е. угол γ), опережение может быть найдено по формуле Дрездена:
где R - радиус валков, мм; h1 - толщина полосы после прокатки, мм; γ - нейтральный угол, рад.
Угол у можно определить по формуле И.М. Павлова:
|
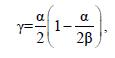
где α - угол захвата, рад; β - угол трения, численно равный коэффициенту трения.
Коэффициент опережения
ξ = 1 + S, (21)
Тогда входная скорость металла будет
|

где ξ/λ - отставание.
Выходная скорость
V1= ξ·V, (23)
где V - окружная скорость валков, равная
V = π D / t (24)
где t - время, необходимое для одного оборота валка; D - диаметр валка.
Опережение может быть найдено также опытным путем. На валок наносят керном метку при прокатке полосы, эта метка дает отпечаток (рис. 16). Так как расстояние между отпечатками на полосе больше длины окружности валка, то опережение будет
(25)
где l 1 - расстояние между двумя метками на полосе; l 0 - длина окружности валка.
На опережение влияют следующие факторы: коэффициент трения, толщина полосы, величина обжатия, диаметр валков и др.
Методика проведения работы
Часть 1. Влияние коэффициента трения и толщины полосы на опережение
Две алюминиевые полосы размером 2x40x500 мм прокатывают с постоянным обжатием Δh = 0,5-0,7 мм: одну в сухих валках, другую - со смазкой машинным маслом. При прокатке по секундомеру замеряют время одного оборота валка.
Отмечают расстояние между отпечатками на полосе l1, толщину полосы до и после прокатки.
Длину окружности валка определяют по формуле
|

По этим данным находят опережение по формулам (25) и (20) и сравнивают эти величины, а также находят входную и выходную скорость металла по формулам (22) и (23). Коэффициент трения при холодной прокатке алюминия со смазкой машинным маслом равен μ = 0,08-0,09, без смазки - μ = 0,2-0,25, а угол захвата а определяют по формуле
|

Все данные заносят в таблицу 4.1.
Таблица 4.1
h0, мм | h1 , мм | Δh, мм | Длина окружность валка, l0, мм | Расстояние между отпечатками на полосе, l1, мм | α, рад | γ, рад | Sопыт. % | Sрасчет. % | V0, м/с | V1, м/с |
| ||||||||||
Прокатка в валках, смазанных машинным маслом | ||||||||||
Часть 2.Влияние величины обжатия на опережение
Четыре свинцовых образца толщиной h0 = 2,0; 2,5; 3,0; 3,5 мм, шириной b0 = 30 мм и длиной 10 = 500 мм прокатывают за один проход до толщины h1 = 1,7 мм на сухих обезжиренных валках на стане с диаметром валков Dв = 100 мм. После прокатки тщательно измеряют толщину полосы и расстояние между отпечатками. По формуле (26) рассчитывают длину окружности валка.
По формулам (19), (21), (22), (23) и (25) находят опережение и скорость входа и выхода полосы из валков, коэффициент опережения.
Все данные заносят в таблицу 4.2.
Таблица 4.2
h0, мм | h1 , мм | Δh, мм | Длина окружность валка, l0, мм | Расстояние между отпечатками на полосе, l1, мм | Sопыт. % | Sрасчет. % | ξ | V0, м/с | V1, м/с |
По данным таблицы 4.2 строят график изменения опережения в зависимости от величины обжатия.
Вывод___________________________________________________________________________________________________________________________________________________________________________________________________________________________________________________________________________