ЗАДАНИЕ 1
Определяю предельные отклонения, размеры, допуски, зазоры, натяги и строю поля допусков.
Исходные данные:
Dн = dн = 210 мм – номинальный диаметр.
Н7– основная посадка в системе основного отверстия.
H4– основная посадка в системе вала.
В системе отверстий (CA) выбираем посадки для основного отверстия Н10: и предельные отклонения вала
Посадка с зазором
Переходная
Посадка с натягом
В системе вала (CB) выбираем посадку для основного вала и предельные отклонения.
Посадка с зазором
Посадка переходная
Посадка с натягом
Посадки | Отклонение, мкм | Предельные Размеры, мм | Допуск, мкм | Зазор, мкм | Натяг, мкм | Допуск посадки | ||||||||
D | d | D | d | D | d | S | N | T | ||||||
ES | es | Dmax | dmax | TD | Td | Smax | Smin | Sср | Nmax | Nmin | Nср | TS,TN мкм | TS,TN мм | |
EJ | ej | Dmin | dmin | |||||||||||
![]() | +46 | -15 -44 | 210,046 | 209,985 209,956 | - | - | - | 0,194 | ||||||
![]() | +46 | +45 +17 | 210,046 | |||||||||||
![]() | +46 | +79 +50 | 210,046 | 60,99 60,53 | - | - | - | -67 | 0,166 | |||||
Таблица 1.1 Посадки в СА для соединения Ø 210мм в десятом квалитете
Посадки | Отклонение, мкм | Предельные Размеры, мм | Допуск, мкм | Зазор, мкм | Натяг, мкм | Допуск посадки | ||||||||
D | d | D | d | D | d | S | N | T | ||||||
ES | es | Dmax | dmax | TD | Td | Smax | Smin | Sср | Nmax | Nmin | Nср | TS,TN мкм | TS,TN мм | |
EJ | ej | Dmin | dmin | |||||||||||
![]() | +130 +100 | -19 | 60,130 60,100 | 59,981 | 105,5 | - | - | - | 0,049 | |||||
![]() | -9 -39 | -19 | 59,991 59,961 | 59,981 | - | - | - | - | 0,049 |
|
Таблица1.2. Посадки в СВ для соединения Ø 60мм в шестом квалитете
-133 -19 59,867 59,981 | ![]() ![]() | ![]() ![]() ![]() ![]() ![]() | ||||||||||||||||||||||||||||||||||||
Расчётные формулы:
Параметры посадок, образующих соединения в системе отверстие и системе вала, рассчитывают по зависимостям.
Предельные значения определяются;
для вала - dmax = dн + es; dmin = dн + ei; (1.1; 1.2)
для отверстие - Dmax = Dн + ES Dmin = Dн + EI; (1.3; 1.4)
где dн, Dн – номинальные размеры вала и отверстия;
es, ES – верхние отклонение вала и отверстия;
ei, EI – нижнее отклонение вала и отверстия.
В эти формулы отклонения поставляют со своими знаками специальной справочной литературы [1, ч.1, с.90 и 125].
Величины допусков определяют;
для вала - Td = dmax - dmin = es – ei; (1.5)
для отверстие - TD = Dmax - Dmin = ES – EI. (1.6)
Для посадок с натягом величины натяга определяют:
Nmax= dmax- Dmin= es- EI; (1.7)
Nmin= dmin- Dmax= ei- ES (1.8)
Средний натяг есть среднее арифметическое между наибольшим и наименьшим натягами:
Ncр = (Nmax+Nmin)/2 (1.9)
Для посадок с зазором величины зазоров определяют:
Smax= Dmax- dmin = ES- ei; (1.10)
Smin= Dmin- dmax = EI- es (1.11)
Средний зазор есть среднее арифметическое между наибольшим и наименьшим зазором:
Sср= (Smax+Smin)/2 (1.12)
Для переходных посадок наибольшие значения натяга и зазора определяют:
Nmax= dmax- Dmin= es- EI; (1.13)
Smax= Dmax- dmin = ES- ei (1.14)
Средний натяг в переходных посадках рассчитывают по формулам:
Ncр = (Nmax+Nmin)/2 = (Nmax+ Smax)/2 (1.15)
где Nmin=- Smax= ei- ES (результат среднего натяга со знаком минус будет означать, что среднее значение для посадки соответствует зазору).
|
Допуск посадки определяются:
допуск натяга TN = Nmax – Nmin= Td+ TD; (1.16)
допуск зазора TS = Smax – Smin= Td+ TD; (1.17)
допуск переходной посадки (допуск натяга или допуск зазора)
TN= TS= Nmax – Nmin= Smax – Smin= Td+ TD; (1.18)
Допуск посадки в общем случае TN= TS= Td+ TD. (1.19)
![]() | |||||||||||||
![]() | |||||||||||||
![]() | |||||||||||||
![]() | |||||||||||||
![]() | |||||||||||||
![]() | |||||||||||||
![]() |
Рисунок 1. Схема расположения полей допусков в СА
![]() ![]() | |||
![]() | |||
|
|
0 EI=0 ei=0,053
![]() ![]() ![]() ![]() ![]() |
|
ei=-0,264
![]() ![]() | |||
![]() |
Рисунок 2. Схема расположения полей допусков в СВ
![]() | ||||||||||||||||
![]() | ||||||||||||||||
![]() | ||||||||||||||||
![]() | ![]() | |||||||||||||||
![]() | ![]() | |||||||||||||||
![]() | ||||||||||||||||
ES=0,130
![]() ![]() ![]() ![]() ![]() |
EI=0.100
0 es=0
|
![]() | |||
![]() | |||
ei=0.019
EI= -0.039
![]() | ![]() | ||||
![]() | |||||
ES=-0.087
![]() ![]() |
EI=-0.133
![]() |
ЗАДАНИЕ 2
Расчёт и выбор посадки с зазором
Исходные данные:
D = 30 мм – номинальный диаметр подшипника
L = 50 мм –длина подшипника
n = 2800 об/мин – частота вращения вала
Р = 600 H – нагрузка на цапфу
Инд. 30 – масло для смазки – η=0,026
ω=π*n/30=3,14*2800/30=293,06 рад/с
2.1 Определяем среднее удельное давление в подшипнике:
(2.1)
2.2 Определяем значение произведения:
(2.2)
2.3 Наивыгоднейший тепловой режим работы подшипника при
|
наименьшем коэффициенте трения наступает при установившемся движении, когда h = 0,25*S. Подставляя значение h в формулу (2.2) получим наивыгоднейший зазор:
(2.3)
2.4 Расчётный зазор, по которому выбираем посадку, определяем по формуле:
(2.4)
где RZ1 =3,2 мкм и RZ2 = 6,3мкм – шероховатость поверхностей вала и
отверстия по ГОСТ 2789-73.
2.5 Чтобы большая часть подвижных соединений при сборке имела зазор,
близкий к расчётному при выборе стандартных посадок необходимо
выполнение условия:
Sср.станд. = Sрасч. (2.5)
Smax=233 мкм
Smin=65 мкм
Smax+Smin/2=159
2.6 Выбираем посадки в соответствии с ГОСТ 25347-82 в системе
Отверстия в первую очередь предпочтительные. Для выбранной посадки построим схему расположения полей допусков. (рис 3)
2.7 Выбранную посадку необходимо проверить на наименьшую толщину
маслянистой пленки hmin, при которой обеспечивается жидкостное
трение:
(2.6)
Для обеспечения жидкостного трения нужно соблюдать условие:
0.033*10-3 ≥ 3,2*10-6+6,3*10-6 верно.
![]() |


![]() | |||||||
![]() | |||||||
![]() | |||||||
![]() | |||||||
ES=+0,084
![]() ![]() |
0EI=0
|

![]() |
ei=-0,049
![]() |
ЗАДАНИЕ 3
Расчёт и выбор неподвижной посадки
Исходные данные
D = 85 мм
d1 = 0 мм
d2 =160 мм
L = 120 мм
Мкр =5*103 Нм
Сталь 45
ƒ=0,15
3.1 Определяем удельного давления на сопрягаемых поверхностях
неподвижного соединения определяем в зависимости от вида нагрузки:
- при действии крутящего момента Мкр, Нм
(3.1)
3.2 Наименьший натяг в соединении определяем на основании
зависимостей, известных из решения задачи Лемы для толстостенных
цилиндров:
(3.2)
где E1 и E2 - модуль упругости.
E = 2,1*10¹¹ н/м² (для стали)
С1 и С2 – коэффициенты, определяем по формулам:
(3.3)
где μ1, μ2 - коэффициенты Пуассона для материала вала и отверстия
μ1 = 0,3 = μ2 (для стали).
3.3 Расчётный натяг, по которому выбираем посадку, определяем по
формуле:
(3.4)
3.4 Выбор стандартной посадки производим из условия относительной
неподвижности соединяемых деталей:
Nmin станд ≥ N расч (3.5)
49*10-6 мкм≥ 34,25*10-6 мкм
3.5 Удельное давление, возникающее при наибольшем натяге выбранной
посадки, определяем из формулы:
(3.6)
4 Возникающие при этом напряжение в охватывающей (отверстие) и
охватываемой (вал) детали будут соответственно равны:
(3.7)
(3.8)
7. Если σ1 и σ2 меньше предела текучести материала деталей соединения, т.е. σ1 < σT1, и σ2 < σT2, то посадка выбрана правильно.
σ1 < σT1, σ2 < σT2
684,4*105 < 36*107 Н/м² 1368,8*105 < 36*107 Н/м²
Посадка выбрана правильно.
es=0,086
![]() ![]() |
ei=0,071
|
0 EI=0
![]() |
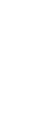
Расчёт исполнительных размеров гладких предельных калибров
Исполнительными размерами калибров называются размеры, которые проставляются на рабочих чертежах калибров, т.e. размеры, по которым должны изготавливаться новые калибры.
4.1 Определяем предельные отклонения и предельные размеры деталей для заданной посадки:
D max = 30,084 мм; dmax = 29,935 мм;
D min =30 мм; dmin = 29,883 мм.
4.2 Схема расположения полей допусков калибров-пробок, для контроля отверстия:
Z = 9 мкм, 0,009 мм;
Y = 0 мкм;
α = 0 мкм;
H = 4 мкм, 0,004 мм;
4.3 Определяем предельные размеры калибров-пробок по следующим формулам:
P – ПРmax = D min + Z + H/2 = 30+0,009+0,004/2=30,011 мм; (4.1)
P – ПРmin = D min + Z – H/2 =30+0,009-0,004/2=30,007 мм; (4.2)
P – ПРизн = D min –Y = 30-0=30 мм; (4.3)
Р – HEmax = D max + H/2 = 30,084+0,004/2=30,086 мм; (4.5)
P – HEmin = D max – H/2 = 30-0,004/2=29,998 мм; (4.6)
4.4 Схема расположения полей допусков калибров скоб, для контроля вала:
Z1 = 3 мкм, 0,003 мм;
Y1 = 3=0,003 мкм;
d1 = 0 мкм;
H1 = 4 мкм, 0,004 мм;
HР = 1,5 мкм, 0,0015 мм.
4.5 Определяем предельные размеры калибров скоб по следующим формулам:
P – ПРmax = d max – Z1 + H1/2 =29,935-0,003+0,004/2=29,934 мм; (4.7)
Р – ПРmin = d max – Z1 – H1/2 = 29,935-0,003-0,004/2=29,930 мм; (4.8)
P – ПРизн = d max + Y1 = 29,935+0,004/2=29,937 мм; (4.9)
Р – HEmax =d min + H1/2 = 29,935+0,004/2=29,937 мм; (4.10)
P – HEmin = d min – H1/2 =29,935-0,004/2=29,933 мм; (4.11)
4.6 Определяем контрольные калибры для контроля скоб по следующим формулам:
К – ПР = d max – Z1 + Hp/2 = 29,935-0,003+0,0015/2=29,93876 мм; (4.12)
K – HE = d min + Hp/2 = 29,883+0,00015/2=29,88375 мм; (4.13)
K – ПРиз = d max +Y1 + Hp/2 = 29,935+0,003+0,0015/2=29,93875 мм. (4.14)
Рисунок 5. Схема полей допусков калибров-пробок для контроля отверстия.
H=0.088 0
Dmax=30.84 |
Рисунок 6. Схема полей допусков калибров скоб для контроля вала.
ЗАДАНИЕ 5
Расчёт и выбор посадок для подшипников качения
Исходные данные:
номер подшипника № 228
класс точности 0:
нагрузка PH = 6000 Н
5.1 По номеру подшипника устанавливаем габаритные размеры подшипника.
D = 250 мм – наружный диаметр
d = 140 мм – внутренний диаметр
В = 42 мм – ширина кольца
r = 4,0мм – радиус фаски
Установочные размеры сопрягаемых с подшипником деталей
D2 max = 236 мм – диаметр заплечика корпуса;
d2 min = 153 мм – диаметр заплечика вала;
5.2 По характеру нагрузки подшипника определяем интенсивность радиальной нагрузки на посадочной поверхности циркуляционного нагруженного кольца при условии, что вращается вал.
PR =FR / b * K1* K2* K3; (5.1)
b = B – 2r = 42-2*4=34=0,034 м –рабочая ширина посадочного места
K1 – динамический коэффициент посадки, зависящий от характера нагрузки
K1 = 1 (при умеренных толчках и вибрации)
K2 - коэффициент, учитывающий степень ослабления посадочного натяга при полом вале или тонкостенном корпусе
K2 = 1 (при сплошном вале)
K3 – коэффициент неравномерности распределения радиальной нагрузки FR
K3 =1 (для радиальных и радиально упорных подшипников с одним нагруженным кольцом)
PR = (6000/0,034)*1*1*1=176,5 кH/м2
5.3 По величине определяем посадку для циркулярнно-нагруженного кольца подшипника на вал или в корпус:
Ø140
5.4 Nmax = es - EI =0,0125-(-0,025) = 0,0375 мм = 37,5 мкм (5.2)
es=+0,0125
0 ES=0
ei=-0,0125
EI=-0,025
Рисунок 7. Схема расположения полей допусков соединения внутреннего кольца подшипника и вала (СА).
5.5 Определяем посадку для местно нагруженного кольца подшипника:
Ø250
Рисунок 8. Схема расположения полей допусков соединения наружного кольца подшипника с корпусом (СВ).
5.6 Определяем Smax и Smin значения радиального зазора для подшипников
нормального ряда и определяем среднее значение начального зазора.
Smax = 53 мкм,
Smin = 18 мкм,
S1= Sср = (Smax – Smin)/2 =(53+18)/2=35,5 мкм. (5.3)
5.7 Определяем значение приведённого среднего диаметра беговой дорожки внутреннего кольца.
d0 = d+(D-d)/4 = 140+(250-140)/4 = 167,5 мм. (5.4)
5.8 Определяем величину диаметральной деформации беговой дорожки
внутреннего кольца подшипника.
∆d1max =Nэф *d0 / d = 31,87*(167,5/140) = 38,1 мкм; (5.5)
где Nэф –эффективный натяг
Nэф = 0,85*Nmax = 0,85*37,5= 31,87 мкм; (5.6)
5.9 Определяем посадочный зазор S подшипника при посадки его на вал.
S2 = S1 - ∆d1max = 35,5 –38,2 =-2,7 мкм. (5.7)
7 ряд
Smax = 91 мкм,
Smin = 46мкм,
S1= Sср = (Smax – Smin)/2 =(91+46)/2=68,5 мкм
d0 = d+(D-d)/4 = 140+(250-140)/4 = 167,5 мм.
S2 = S1 - ∆d1max =68,5–38,2 =30,3 мкм