Тема: Ремонт приборов систем питания двигателей
План лекции
1. Общая технология ремонта топливной аппаратуры
2. Планировка отделения по ремонту газотопливной аппаратуры АТП
Содержание лекции:
Общая технология ремонта топливной аппаратуры
Совокупность ремонтных операций, выполняемых в определенной последовательности, представляет собой технологию ремонта. В зависимости от объема и условий выполнения ремонта технология может быть различной.
Капитальный ремонт топливной аппаратуры автомобилей выполняют на специализированных авторемонтных заводах в централизованном порядке. При этом применяется маршрутная технология восстановления приборов, предусматривающая поточный метод производства. Эта технология предполагает высокое оснащение ремонтного процесса современными техническими средствами и оборудованием, которые свойственны крупносерийному производству. Капитальный ремонт топливной аппаратуры целесообразен в том случае, если затраты на него не превышают себестоимости производства новых приборов. Это условие выполнимо для приборов системы питания дизельных двигателей. Для карбюраторных и инжекторных двигателей, имеющих сравнительно простое конструктивное исполнение приборов системы питания, капитальный ремонт топливной аппаратуры не предусматривается.
В условиях автотранспортного предприятия выполняют ремонт топливной аппаратуры в объеме текущего ремонта. Он включает три этапа:
- снятие неисправных приборов с автомобилей (выполняется на рабочих постах в зоне ТО-2 или в зоне ТР;
- проверка, ремонт, регулировка и испытание приборов (выполняется в топливных участках АТП или на специализированных ремонтных предприятиях);
- установка отремонтированных приборов на автомобиль.
Общая схема технологии ремонта топливной аппаратуры автомобилей в автотранспортных предприятиях представлена на рис. 1.
Приемка приборов в ремонт.
После снятия с автомобиля неисправные приборы топливной аппаратуры подготавливают к передаче в ремонт: очищают от грязи, сливают масло, воду и топливо из внутренних полостей. Затем приборы снабжают необходимой технической документацией (нарядом на ремонт и др.) и в полном комплекте транспортируют и передают в топливные отделения или участки (карбюраторный, бензотопливный, дизтопливный, газотопливный).
При поступлении приборов в топливный участок осуществляется их приемка.
Рис. 1 Схема технологического процесса ремонта приборов топливной аппаратуры |
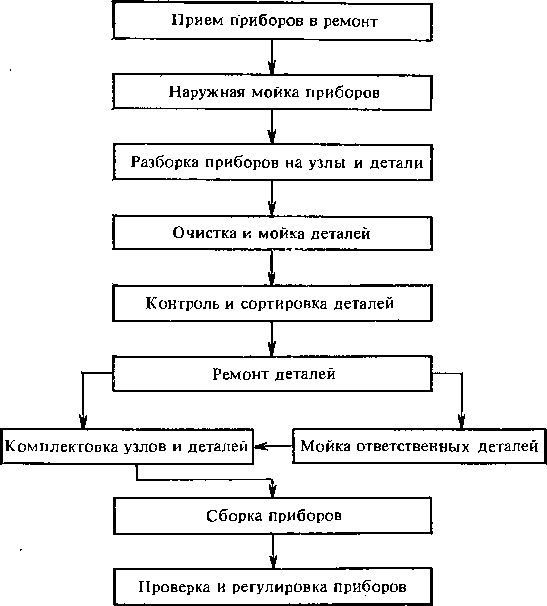
При приемке устанавливают комплектность, техническое состояние прибора и оформляют приемо-сдаточную документацию.
Комплектность приборов проверяют наружным осмотром, сверяя с технической документацией (техническим описанием или комплектовочной ведомостью).
Техническое состояние прибора определяют также наружным осмотром и проверкой на контрольных приборах или испытательных стендах. На основании результатов определения технического состояния приборов принимается решение об объёме и последовательности выполнения операций их текущего ремонта.
Приемо-сдаточной документацией являются наряд на ремонт, накладная на передачу или приемо-сдаточный акт, В них отмечают срок службы прибора до ремонта, наличие неисправностей и состояние базовых деталей (наличие выбраковочных признаков).
Наружная мойка приборов является обязательной перед разборкой и ремонтом. Приборы, поступившие в топливный участок для ремонта, моют в ванне с керосином или в моечной машине, очищают волосяными щетками и продувают сжатым воздухом. Для мойки топливной аппаратуры применяют струйные моечно-очистительные машины или установки. Они могут работать на пароводяной смеси, холодной или горячей воде, а также на моющих растворах. В качестве моющих растворов рекомендуется применять синтетические моющие средства, например «Аэрол». Это сильнопенящееся и нетоксичное средство со специфическим запахом применяется в концентрации 2-3 г/л раствора.
Применение каустической соды в качестве моющего средства следует избегать, так как она опасна для здоровья и вызывает коррозию деталей из цветных металлов. Также не допускается использовать для мойки деталей из алюминиевых и цинковых сплавов щелочные растворы, применяемые для мойки сальных и чугунных деталей, так как алюминий и цинк растворяются в щелочах.
Качество мойки считается удовлетворительным, если с поверхности приборов системы питания удалены грязь, пыль, отложения и подтеки масла.
Разборка приборов на сборочные единицы (узлы) и детали. Приборы системы питания разбирают, как правило, на слесарных верстаках с использованием тисков для закрепления приборов или на рабочих столах. Для разборки приборов применяют стенды, приспособления и специальный инструмент. Разборка осуществляется в определенной последовательности, согласно операционных карт и с соблюдением общих правил по разборке, не допуская повреждений поверхностей деталей. После разделения деталей необходимо тщательно отскоблить прокладки и очистить поверхности деталей от их остатков. Плохо снимаемый с поверхности материал можно смочить специальным химическим составом, чтобы размягчить, после чего он легко соскабливается. Скребки должны быть изготовлены из меди, это уменьшает вероятность повреждения детали.
Очистка и мойка деталей. После разборки отдельные детали приборов вновь моют в ванне с керосином с помощью волосяных щеток, очищают от отложений и нагара, продувают сжатым воздухом или вытирают чистыми салфетками.
Контроль и сортировку деталей выполняют с целью определения степени износа и пригодности детали к ремонту или эксплуатации. Детали сортируют на годные к эксплуатации, не подлежащие ремонту и требующие ремонта. Рассортированные детали в зависимости от их состояния отправляют в утиль, на комплектование или в ремонт.
Комплектование деталей — это подбор комплекта деталей для одной сборочной единицы (узла) в целом. Например, нагнетательные секции насоса высокого давления можно скомплектовать по паре плунжер — гильза.
Ремонт деталей приборов системы питания в АТП сводится к работам по их восстановлению, не требующим сложного оборудования. К ним относятся притирка рабочих поверхностей клапанов и их седел, запорных игл и распылителей форсунок, плунжерных пар, замена потерявших упругость пружин, восстановление целости трубопроводов, резьб, заделка трещин в корпусах, поплавках и др.
При наличии специального оборудования и приспособлений выполняют более сложные ремонтные работы: осталивание или хромирование изношенных поверхностей кулачков, толкателей, поршней насосов.
Шейки кулачкового вала ТНВД ремонтируют вибродуговой наплавкой с последующим шлифованием и доведением до необходимого размера.
После ремонта детали приборов системы питания очищают от следов механической обработки, комплектуют по техническим условиям и собирают.
Собранные приборы прирабатывают, регулируют и испытывают на стендах, затем устанавливают и регулируют на автомобилях.
Планировка отделения ремонта газотопливной апаратуры АТП
Приборы систем питания газобаллонных автомобилей, неисправность которых не может быть устранена на постах технического обслуживания и ремонта автомобилей, снимают и направляют в отделение по ремонту газовой аппаратуры и арматуры. Варианты планировок отделения приведены на рис. 158.
К помещениям отделения предъявляются особые требования. Минимально допустимая высота помещения, обусловленная санитарными нормами, должна быть от пола до потолка 3,2 мм, от пола до выступающих конструктивных элементов перекрытия 2,6 м. Полы должны быть ровными с нескользкой поверхностью, бензомаслостойкими, из несгораемого материала. Под помещениями, занятыми отделением, запрещается устраивать подвалы, колодцы и подпольные каналы (пустоты).
Помещение для ТО и ремонта газовой аппаратуры должно быть оборудовано искусственной приточно-вытяжной вентиляцией с двукратным обменом воздуха, а также противопожарной сигнализацией и средствами пожаротушения.
Снятое с автомобиля газовое оборудование имеет неприятный специфический запах одорирующих веществ и сернистых соединений, а также остатки пропан-бутанового газа, поэтому шкаф для их хранения должен иметь в нижней части принудительную вытяжную вентиляцию.
Секционный стеллаж-шкаф с переставными полками и выдвижными ящиками для хранения 20 комплектов газового оборудования (рис.159) имеет принудительный отсос воздуха производительностью 0,25 м3/час. Для предохранения газовой аппаратуры от повреждений секции стеллажа выполнены из материала меньшей твёрдости (дерево, пластмасса), чем агрегат аппаратуры.
При мойке газового оборудования применяют те же машины и средства, что и при мойке бензиновой и дизельной топливной аппаратуры. Газовые приборы размещают на верстаках, оборудованных тисками и устройством отсоса воздуха.
На участке ТО и ремонта газового оборудования осуществляют дефектовку, сборку, проверку и регулировку его деталей и сборочных единиц (узлов) Монтажно-демонтажные, слесарные и регулировочные работы выполняют с помощью специального комплекта инструментов мод.И-139 (рис.160) Инструменты имеют медное покрытие, позволяющее применять их во взрывоопасной среде.
Проверку и регулировку газового оборудования выполняют на специальных стендах. Рабочие параметры и герметичность сборочных единиц (узлов) газового оборудования проверяют сжатым воздухом или инертным газом при рабочем давлении 1,6 Мпа. Сжатый газ подается из баллонов высокого давления (до 20 Мпа) и редуцируется до испытательного давления. Шкаф для хранения этих баллонов и тележка для их перемещения размещены на участке энергообеспечения IV. Для проверки и регулирования газового смесителя и карбюратора-смесителя участок оборудуют безмоторной установкой, вакуумная часть которой размещена в отдельном помещении (участок III на рис.158)