(4)
Угол между вектором статической силы Rст и вертикалью
(5)
Расчет показал, что в системе колесно-моторного блока электровоза 2ЭС5К появилось отклонение статической нагрузки на моторно-осевом подшипнике от вертикали на угол β = 7,03, которое предопределяет появление зазора между осью колесной пары и вкладышем подшипника в направлении вертикальной оси (рис. 3). В случае наличия такого зазора при прохождении колесом рельсовых стыков возникает импульсная сила, которая определяет ударный характер взаимодействия оси колесной пары и вкладыша МОП, что в свою очередь может привести к эффекту наклепа и разрушению материалов контактирующих тел.
а) б)
Рис. 3. Взаимное расположение оси колесной пары и вкладыша МОП в статическом положении: А – точка контакта; ∂ – зазор в вертикальном направлении
На основе расчетной схемы на рис. 4, и с использованием законов изменения количества движения и кинетического момента получены выражения для расчета составляющих импульса и скоростей центра оси колесной пары после воздействия стыка:
; (6)
; (7)
|
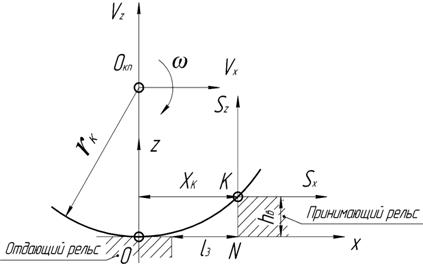
Рис. 4. Схема для расчета стыкового воздействия
на моторно-осевые подшипники
(8)
где J и m - соответственно момент инерции и масса колесной пары.
(9)
(10)
. (11)
Так как <<1, то можно принять, что
Тогда вертикальная составляющая импульсной скорости колесной пары
(12)
Для исследования взаимодействия оси колесной пары и вкладыша подшипника на основе формул теории упругости для контактного взаимодействия двух цилиндров длиной lв получено выражение для расчета упругой силы F, возникающей в области контакта при сближении цилиндров:
(13)
где Z – сближение МОП и оси колесной пары; lв – длина вкладыша МОП; μ1, μ2, Е1, Е2 – коэффициенты Пуассона и модули упругости соответственно вкладышей МОП и оси колесной пары.
Поведение центра тяжести колесной пары от действия импульса со стороны стыковой неровности представлено уравнением:
(14)
с начальными условиями
где Ж – контактная жесткость.
(15)
Закон движения центра тяжести колесной пары при прохождении стыковой неровности имеет вид:
(16)
здесь
Максимальное сближение оси колесной пары и вкладышей подшипников соответствует максимальному смятию материала вкладыша и максимальному значению упругой силы в области контакта:
(17)
(18)
Для оценки напряженного состояния материалов контактирующих тел найдем распределение силы F по области контакта, используя расчетную схему на рис. 5, где О1 – координата центра МОП; О2 – координата центра оси колесной пары; R – радиус внутренней поверхности вкладыша МОП; r – радиус оси колесной пары.
|
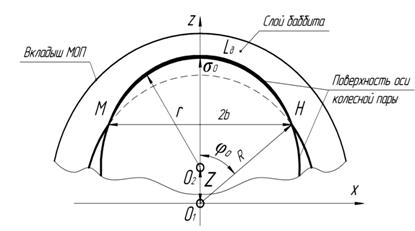
Рис. 5. Расчетная схема контактного взаимодействия
оси колесной пары со слоем баббита вкладыша
моторно-осевого подшипника
Напряжение в центре дуги МН
(19)
Длина дуги МН
(20)
где
|
Рис. 6. Зависимость напряжения в материале МОП от скорости электровоза
Из этого следует, что изменение конструктивной компоновки КМБ на электровозе 2ЭС5К по сравнению с электровозом ВЛ80 привело к возникновению существенных импульсных напряжений в материале вкладышей МОП при движении по рельсовому пути, что способствует интенсивному износу и негативно влияет на работоспособность подшипникового узла.
В третьем разделе проведен анализ существующего технологического процесса заливки баббитом вкладышей МОП, обоснованы основные параметры и технологические режимы центробежного литья, получены рациональные режимы и параметры заливки вкладышей МОП баббитом Б16 в условиях ремонтного локомотивного депо.
Приведенные выше результаты исследований позволили сделать вывод о том, что для снижения негативного влияния конструктивных особенностей КМБ электровозов 2ЭС5К на работоспособность моторно-осевых подшипников требуется при ремонте обеспечивать соответствие характеристик антифрикционного баббитового слоя вкладышей МОП техническим требованиям. Необходимость совершенствования технологического процесса заливки вкладышей подшипников подтверждается и результатами анализа причин отказов и неисправностей МОП, значительная часть которых носит технологический характер: недостаточная толщина слоя баббита, нарушение химического состава и низкая твердость заливки дефектных подшипников, трещины между корпусом и баббитовым слоем вкладыша.
При изготовлении биметаллических подшипников в условиях депо применяется центробежный метод заливки подшипникового сплава Б16, одним из основных преимуществ которого следует считать направленность затвердевания металла, в результате чего в отливках отсутствуют усадочные раковины и рыхлоты, повышаются механические свойства. Основными режимами и параметрами этого метода являются частота и режим вращения формы в процессе формирования отливки, температура заливаемого металла и скорость его заливки в форму, температура нагрева формы перед заливкой металла, способ заливки металла в форму, время остывания отливки в форме. При расчете режимов заливки подшипникового сплава Б16 был применен гидростатический метод.
В условиях ремонтного депо при заливке корпусов вкладышей МОП баббитом используется станок с горизонтальной осью вращения. Для расчета частоты вращения формы использована зависимость для литья тонкостенных втулок и гильз:
(21)
где H – высота отливки; – соответственно внутренний и внешний радиусы отливки;
– поправочный коэффициент (по результатам эксперимента
= 2,2).
Для проверки условия получения отливок без слоистости и неоднородности определяется скорость наращивания жидкого слоя
(22)
где – толщина стенки отливки, t – продолжительность заливки.
Оптимальная продолжительность заливки баббита Б16
(23)
здесь – коэффициент продолжительности заливки;
– преобладающая толщина стенки отливки,
– масса жидкого металла, приходящегося на одну отливку.
Объем металла в форме в любой момент времени заливки
(24)
где – секундный расход металла, выраженный через объем,
– наружный радиус;
– высота отливки;
– толщина залитого слоя.
Решая уравнение относительно , получаем толщину залитого слоя как функцию времени:
(25)
Искомая скорость перемещения фронта жидкого металла в направлении оси вращения () определиться как первая производная пути по времени:
(26)
где .
Процесс заполнения формы начинается со скорости, которая определяется заданными начальными условиями – секундным расходом и величиной боковой поверхности формы:
(27)
Толщина затвердевшего слоя металла:
(28)
где – толщина твердой области в зависимости от времени
от начала процесса затвердевания отливки,
– коэффициент затвердевания, характеризующий скорость движения зоны затвердевания.
(29)
где – температура кристаллизации заливаемого металла,
– коэффициент теплоаккумуляции материала литейной формы,
– плотность заливаемого металла,
– скрытая теплота кристаллизации металла.
Искомая радиальная скорость перемещения фронта затвердевания
(30)
|
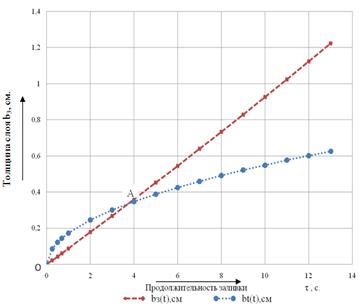
Рис. 7. Изменение толщины залитого слоя и
затвердевшего слоя во времени для процесса
заливки баббита Б16
Для предупреждения образования расслоения металла необходимо, чтобы скорость перемещения фронта затвердевания была меньше скорости наращивания слоя жидкого металла: <
.
Для проверки достоверности полученных результатов был проведен натурный эксперимент. Заливки вкладышей производились в одну смену одним и тем же расплавом баббита Б16 по традиционной технологии и по усовершенствованному технологическому процессу. Результаты эксперимента (рис. 8) показали, что баббитовый слой вкладыша МОП, полученный по предложенной технологии, имеет лучшие качественные показатели, чем полученный по традиционной технологии, т. е. имеет мелкозернистую и плотную структуру сплава (рис. 8, а) с однородным распределением твердой фазы (SnSb) и эвтектики (SnSb) + (Cu6Sn5) по всему объему, твердость – в пределах 28 – 30 НВ согласно нормативу. Таким образом улучшены антифрикционные свойства баббитовой заливки, что обеспечит работоспособность и качество функционирования в эксплуатации моторно-осевого подшипника и КМБ в целом.
а) б)
Рис. 8. Микроструктура баббитового слоя, полученного по оптимизированной (а) и по традиционной (б) технологи заливки вкладышей МОП
Полученные основные параметры и режимы процесса заливки баббита Б16 были использованы при разработке типового технологического процесса заливки вкладышей МОП, утвержденного Дирекцией по ремонту тягового подвижного состава – филиалом ОАО «РЖД».
В четвертом разделе представлены технологические и технические разработки по совершенствованию технологического процесса сборки колесно-моторных блоков электровозов с опорно-осевым подвешиванием ТЭД, который во многом определяет работоспособность КМБ после ремонта. При сборке колесно-моторных блоков с опорно-осевым подвешиванием ТЭД устанавливаются особые требования по точности сопряжения, контролю параметров отклонений и взаимного расположения сборочных единиц, деталей и узлов. Для обеспечения необходимой точности позиционирования колесной пары относительно моторно-осевых горловин остова тягового электродвигателя при сборке построена размерная цепь КМБ, которая является совокупностью взаимосвязанных размеров, образующих замкнутый контур и непосредственно участвующих в обеспечении гарантированного зазора. Размерный анализ КМБ выполнен вместе с расчетом размерной цепи технологического оборудования (рис.9) для обеспечения заданной точности сопряжений и технологических параметров при сборке.
Рис. 9. Размерный анализ технологической позиции сборки КМБ с опорно-осевым подвешиванием тяговых электродвигателей
Определены следующие предельные отклонения, мм: S1 = 542,5 – 0,66; S2 = 556,5 – 0,66; S3 = 1100 – 1,2+1,2.
Создан усовершенствованный комплект нестандартного технологического оборудования для ремонта колесно-моторных блоков с опорно-осевым подвешиванием тяговых электродвигателей, использование которого позволяет механизировать трудоемкие операции при сборке КМБ, повысить качество и сократить время простоя в ремонте (рис. 10). На технические решения по нестандартному оборудованию получено положительное решение ФГУ ФИПС о выдаче патента на полезную модель. За счет применения разработанного оборудования в технологическом процессе ремонта КМБ время на выполнение сборки колесно-моторного блока сократилось на 0,34 часа, степень механизации выполняемых операций возросла до 85 %, уменьшилась трудоемкость выполняемых работ.
Созданное оборудование заняло первое место на проведенном в 2009 г. по поручению старшего вице-президента ОАО «РЖД» В.А. Гапановича конкурсе по разработке и изготовлению нестандартного оборудования технологического участка для выкатки, разборки и сборки колесно-моторных блоков (КМБ) локомотивов. Разработанное оборудование для ремонта КМБ имеет лучшие показатели по уровню механизации и производительности, отличается простотой конструктивных решений, надежностью в работе и ремонтопригодностью. Конструкция универсальна и с минимальными изменениями может быть использована для любых колесно-моторных блоков с опорно-осевым подвешиванием тяговых двигателей. Комиссия ОАО «РЖД», проводившая приемочные испытания, рекомендовала оборудование для использования при ремонте электровозов серий ВЛ-10, ВЛ80, ВЛ85, 2ЭС4К и 2ЭС5К.
Рис. 10. Вид технологической позиции сборки КМБ в ТЧР Московка
Разработана техническая документация для производственного процесса сборки колесно-моторных блоков при текущем ТР-3 и среднем ремонтах СР, позволяющая обеспечивать соблюдение нормативных сроков ремонтных операций и выпуск из ремонта электровозов согласно программному заданию, оптимизировать технологический процесс ремонта.
В пятом разделе проведена оценка экономической эффективности от использования нестандартного технологического оборудования и технологической документации для сборки колесно-моторных блоков электровозов. Расчетный экономический эффект от внедрения этих разработок составит 350 тыс. р. на программу ремонта 450 КМБ в год, и капиталовложения должны окупиться за 5,8 года.
ОСНОВНЫЕ РЕЗУЛЬТАТЫИ ВЫВОДЫ
В результате проведенных исследований выполнены научно обоснованные технические и технологические разработки, направленные на совершенствование технологии ремонта колесно-моторных блоков магистральных грузовых электровозов. Применение разработанных технологий и технологического оборудования позволит механизировать технологические операции при ремонте КМБ, повысить качество ремонта и сократить время простоя электровоза в ремонте. Таким образом, за счет совершенствования технологии ремонта обеспечивается работоспособность колесно-моторных блоков в эксплуатации.
Основные научные и практические результаты диссертационной работы состоят в следующем:
1. Исследованы конструктивные особенности колесно-моторных блоков с опорно-осевым подвешиванием тяговых электродвигателей и на основе уравнений статического равновесия показано, что изменение компоновки КМБ в электровозах новой серии 2ЭС5К привело к перераспределению статических нагрузок в узлах колесно-моторного блока и появлению зазора между осью колесной пары и вкладышем моторно-осевого подшипника в направлении вертикальной оси.
2. Разработана математическая модель для определения влияния импульсных воздействий на работоспособность моторно-осевых подшипников при прохождении электровозом рельсового стыка с учетом конструктивных параметров колесно-моторного блока.
3. Выполнен качественный и количественный анализ влияния технологических параметров на работоспособность колесно-моторных блоков. Установлено, что существенное влияние на качество функционирование колесно-моторных блоков в эксплуатации оказывают физико-механические свойства антифрикционного слоя вкладышей моторно-осевых подшипников и параметры сопряжений и взаимных расположений деталей КМБ при их сборке.
4. Разработан технологический процесс заливки баббитом вкладышей моторно-осевых подшипников, позволяющий повысить качество антифрикционного баббитового слоя и эксплуатационные характеристики моторно-осевых подшипников.
5. Разработанные технологическая инструкция и комплект технологической документации внедрены в ОАО «ВНИИЖТ» в типовой технологический процесс заливки баббитом Б16 вкладышей моторно-осевых подшипников и переданы на локомотиворемонтные заводы и в ремонтные локомотивные депо для использования при ремонте КМБ.
6. Создан усовершенствованный комплект нестандартного технологического оборудования для ремонта колесно-моторных блоков с опорно-осевым подвешиванием тяговых электродвигателей, применение которого позволяет механизировать трудоемкие операции при сборке КМБ, повысить качество выполнения ремонтных операций, сократить время простоя в ремонте. На технические разработки по нестандартному оборудованию получено положительное решение ФГУ ФИПС о выдаче патента на полезную модель.
7. Разработана техническая документация для производственного процесса сборки колесно-моторных блоков при текущем ТР-3 и среднем СР ремонтах, позволяющая обеспечивать соблюдение нормативных сроков ремонтных операций и выпуск из ремонта электровозов согласно программному заданию, оптимизировать технологический процесс ремонта.
8. Разработанные комплект нестандартного технологического оборудования технологической позиции сборки колесно-моторных блоков и техническая документация внедрены в технологические процессы текущего ТР-3 и среднего СР ремонтов электровозов в ремонтном локомотивном депо Московка Западно-Сибирской дирекции по ремонту тягового подвижного состава – структурного подразделения Дирекции по ремонту тягового подвижного состава – филиала ОАО «РЖД». Расчетный экономический эффект от внедрения этих разработок составит 350 тыс. р. на программу ремонта 450 КМБ в год.