В.П. Смоленцев А.И.Болдырев
ТЕОРИЯ ЭЛЕКТРИЧЕСКИХ
И ФИЗИКО-ХИМИЧЕСКИХ МЕТОДОВ ОБРАБОТКИ
Учебное пособие
Воронеж 2007
ГОУВПО «Воронежский государственный
технический университет»
В.П. Смоленцев А.И.Болдырев
Е.В.Смоленцев Г.П.Смоленцев
ТЕОРИЯ ЭЛЕКТРИЧЕСКИХ
И ФИЗИКО-ХИМИЧЕСКИХ МЕТОДОВ
ОБРАБОТКИ
Допущено
учебно-методическим объединением по образованию
в области автоматизированного машиностроения (УМО АМ) в качестве учебного пособия для студентов, обучающихся по направлению «Конструкторско-технологическое обеспечение машиностроительных производств»
Воронеж 2007
УДК 621.9
Теория электрических и физико-химических методов обработки: Учеб. пособие / В.П.Смоленцев, А.И.Болдырев, Е.В.Смоленцев, Г.П.Смоленцев. Воронеж: ГОУВПО «Воронежский государственный технический университет, 2007. 376 с.
ISBN
Рассмотрены вопросы теории электрических и физико-химических методов обработки. Показана физическая сущность технологических приемов, моделирование протекающих процессов, раскрыта связь между теоретическими зависимостями и технологическими возможностями методов обработки.
Издание соответствует требованиям Государственного образовательного стандарта высшего профессионального образования по направлению 151000 «Конструкторско-технологическое обеспечение автоматизированных машиностроительных производств», специальности 151001 «Технология машиностроения», дисциплине «Теория электрических и физико-химических методов обработки».
Табл. 13. Ил. 152. Библиограф.: 15 назв.
Рецензенты: кафедра автоматизации производственных процессов Воронежской государственной лесотехнической академии (зав. кафедрой д-р техн. наук, проф., засл. деят. науки и техники РФ, В.С.Петровский);
д-р техн. наук, проф. В.П.Мельников
ISBN © Смоленцев В.П., Болдырев А.И.,
Смоленцев Е.В., Смоленцев Г.П.
© Оформление. ГОУВПО «Воро-
нежский государственный техни-
ческий университет», 2007
ВВЕДЕНИЕ
Процессы, протекающие при использовании электрических методов обработки, имеют принципиальные отличия от традиционной теории резания. У большинства изучаемых новых методов формообразование происходит под действием электрического, электромагнитного или ультразвукового поля, а механическое воздействие, аналогичное процессу резания, присутствует только в некоторых комбинированных видах формообразования, в частности в случае использования в качестве обрабатывающей среды абразивных порошков. В остальных случаях процесс протекает без прямого контакта инструмента с заготовкой (имеется зазор), а формирование зоны обработки происходит путем воздействия полей, т.е. по совершенно новым закономерностям, не рассматриваемым в других дисциплинах.
Для изучения теории электрических и физико-химических методов обработки от студентов требуется знание электротехники, гидродинамики, электрохимических процессов, акустики, теплотехники, теоретической механики, сопротивления материалов и др.
Раздел комбинированной обработки изучается на базе классических законов физики, химии, теории вероятности, оптимизации.
Электрические методы обработки находят ограниченное по объему применение в машиностроении, но их использование позволяет изготовить сложные наукоемкие изделия, отвечающие требованиям современного рынка промышленной продукции, что является главным условием признания страны в качестве современной индустриальной державы. Поэтому специалисты, заканчивающие технический вуз, должны владеть знаниями в области процессов и технологий нетрадиционной обработки (к которым относятся электрические методы) на уровне подготовки инженеров промышленно развитых стран. Последнее открывает возможность наладить обмен инженерными и научными кадрами в рамках Европейской образовательной системы, в которую в ближайшее время должна вступить Россия.
Пособие написано авторами с использованием материалов учебного пособия по электрофизическим и электрохимическим методам обработки материалов [ 1, 2 ], достижений в рассматриваемой области за последние годы, опыта преподавания учебных курсов в технических заведениях страны. Особенно это касается комбинированных методов обработки, где многие вопросы теории рассматриваются авторами впервые.
Учебное пособие подготовлено в рамках гранта Президента РФ для поддержки молодых российских ученых и ведущих научных школ (МК-3225.2007.8).
Замечания и пожелания для совершенствования содержания пособия авторы просят направлять по адресу: 394026, г. Воронеж, Московский пр., 14, ВГТУ, кафедра «Технология машиностроения» профессору Смоленцеву В.П.
1. КЛАССИФИКАЦИЯ ЭЛЕКТРИЧЕСКИХ МЕТОДОВ
ОБРАБОТКИ (ЭМО)
Известные в технике методы обработки с формообразованием микро- и макроповерхностей можно классифицировать по видам воздействий на объект (заготовку). К ним относятся следующие воздействия
- тепловое, при котором часть объема заготовки разогревается до испарения (плавления) и локально удаляется с обрабатываемого участка;
- химическое, в котором в результате химических реакций, протекающий под воздействием электрического поля, металл на заданных участках заготовки переходит в новое состояние и удаляется рабочей средой;
- магнитное, при котором создается силовое поле, воздействующее на заготовку или промежуточный (исполнительный) инструмент (например, на абразивные токопроводящие зерна);
- ядерное, воздействующее на материал заготовки в форме облучения. Под действием облучения в материале происходит перестройка структуры на молекулярном уровне, что вызывает изменение обрабатываемости;
- механическое постоянное, изменяющее технологические показатели комбинированных процессов и влияющее на интенсивность воздействия внешнего поля на заготовку;
- механическое импульсное, воздействующее одновременно или в паузах между подачей в зону обработки энергии полей. Такой процесс свойственен ультразвуковой размерной обработке и механическим видам формообразования, совмещенным с наложением электрических (электромагнитных) полей.
На рис. 1.1 показан классификатор ЭМО.
Электроэрозионная обработка (рис. 1.1) осуществляется за счет тепловых процессов вместе разряда, вызывающего дискретное локальное удаление микрообъемов материала при формообразовании или осаждение металла на заготовку при восстановлении формы изношенной детали.
Рис. 1.1. Классификатор электрических методов обработки
Аналогичный процесс происходит в случае лучевой обработки. Однако в отличие от ЭЭО при ЛО плавление микроучастков заготовки может происходить в широком диапазоне времени воздействия импульса или даже при длительном непрерывном действии луча.
Ультразвуковую размерную обработку относят к импульсным комбинированным методам формообразования. Здесь ультразвуковое высокочастотное поле преобразуется в колебательные движения, воздействующие на абразивные зерна, производящие обработку. Кроме того, ультразвуковые колебания используются в резании для интенсификации процессов.
В импульсных методах (рис. 1.1) реализуется магнитное воздействие совместно с электрическим полем. Процессы формообразования здесь имеют много общего с электроэрозионным методом, хотя формообразование осуществляется без плавления и испарения материала.
Комбинированные методы объединяют от 2 до 6 видов воздействий и позволяют добиться наиболее высоких технологических показателей. Очевидно, что в области обработки металлов такие методы имеют большое будущее. В настоящее время известно не более 25 видов комбинированных методов, из которых только 10-12 используются в производстве, хотя теоретически установлено, что при синтезе возможных воздействий может быть спроектировано более 800 новых технологических процессов с разнообразными возможностями. Разработка новых КМО требует создания теорий их проектирования и обоснования целесообразности применения.
2. ЭЛЕКТРОЭРОЗИОННАЯ ОБРАБОТКА (ЭЭО)
2.1. Сущность и виды
В науке и технике само явление электрической эрозии, т. е. разрушение контактов под действием электрических разрядов, было известно давно. В частности, искровые и дуговые разряды возникают при разрыве или отключении электрических цепей. Электрической эрозии подвержены контакты реле, выключателей, рубильников и других подобных устройств. Электрическая эрозия – очень вредное явление, сокращающее срок службы и снижающее надежность электрических устройств. Много исследований было посвящено устранению или хотя бы уменьшению такого разрушения контактов.
Над этой проблемой в годы Великой Отечественной войны работали советские ученые Б.Р. Лазаренко и Н.И. Лазаренко. Поместив электроды в жидкий диэлектрик и размыкая электрическую цепь, ученые заметили, что жидкость мутнела уже после первых разрядов между контактами. Они установили: это происходит потому, что в жидкости появляются мельчайшие металлические шарики, которые возникают вследствие электрической эрозии электродов. Ученые решили усилить эффект разрушения и попробовали применить электрические разряды для равномерного удаления металла. С этой целью они поместили электроды (инструмент и заготовку) в жидкий диэлектрик, который охлаждал расплавленные частицы металла и не позволял им оседать на противолежащий электрод. В качестве генератора импульсов использовалась батарея конденсаторов 2, заряжаемых от источника постоянного тока; время зарядки конденсаторов регулировали реостатом 1 (рис. 2.1). Так появилась первая в мире электроэрозионная установка. Электрод-инструмент 3 перемещали к заготовке 4. По мере их сближения возрастала напряженность поля в пространстве между электродом-инструментом и заготовкой. Это пространство называют межэлектродным промежутком (МЭП) или просто промежутком. При достижении определенной напряженности поля на участке с минимальным расстоянием между поверхностями электродов, измеренным по перпендикуляру к обрабатываемой поверхности и называемым минимальным межэлектродным зазором, возникал электрический разряд (протекал импульс) тока, под действием которого происходило разрушение участка заготовки. Продукты обработки попадали в диэлектрическую жидкость 5, где охлаждались, не достигая электрода-инструмента, и затем осаждались на дно ванны. Через некоторое время электрод-инструмент прошил пластину 4. Причем контур отверстия точно соответствовал профилю инструмента.
![]() | |||
| |||
Так, явление, считавшееся вредным, было применено для размерной обработки материалов. Изобретение электроэрозионной обработки имело выдающееся значение. К традиционным способам формообразования (резанию, литью, обработке давлением) прибавился совершенно новый, в котором непосредственно использовались электрические процессы. Б.Р. Лазаренко и Н.И. Лазаренко были удостоены Государственной премии СССР. Позднее Б.Р. Лазаренко был избран академиком АН Молдавской ССР, где и работал до конца жизни (1910—1979).
Первоначально для осуществления ЭЭО применялись исключительно искровые разряды, создаваемые конденсатором в так называемом RС-генераторе (рис. 2.1). Поэтому новый процесс в то время называли электроискровой обработкой.
В начале 50-х годов были разработаны специальные генераторы импульсов, благодаря которым обработку можно было проводить не только па коротких искровых разрядах, но и на более продолжительных— искродуговых и дуговых разрядах. Чтобы отличить новые условия осуществления процесса, его стали называть электроимпульсной обработкой.
Поскольку для формообразования во всех случаях применяют одно и то же явление — электрическую эрозию, в настоящее время эти процессы считают разновидностями ЭЭО и используют определения электроискровой режим ЭЭО и электроимпульсный режим ЭЭО.
В настоящее время применяют несколько технологических схем электроэрозионной обработки.
1. Прошивание — удаление металла из полостей, углублений, отверстий, пазов, с наружных поверхностей. На рис. 2.2 показаны схемы изготовления углубления (а) и фасонного
|
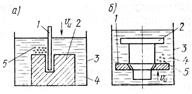
стержня (б). Электрод-инструмент 1 поступательно перемещается к заготовке 2 со скоростью . Оба электрода помещены в ванну 3, заполненную диэлектриком 4. Продукты обработки 5 выбрасываются в межэлектродный промежуток и оседают на дно ванны. Прошиванием можно получать поверхности как с прямой, так и с криволинейной осью.
2. Электроэрозионное шлифование, схема которого показана на рис. 2.3. Металлический электрод-инструмент
|
1 в форме диска совершает вращательное и поступательное движение к заготовке 2 со скоростью . Заготовка может вращаться, как показано на рис. 2.3. Жидкость подают поливом из насадки 3. При небольших габаритах заготовок процесс может протекать в ванне с рабочей жидкостью. Шлифование может быть как встречным, так и попутным.
3. Разрезание профильным или непрофилированным инструментом включает разделение заготовки на части — отрезание — и получение непрямолинейного контура — вырезание, которое выполняется только непрофилированным электродом-инструментом. Профильный электрод-инструмент 1 при разрезании деталей (рис. 2.4, а) может быть
выполнен в форме диска или пластины. Его перемещают к заготовке 2 со скоростью и в плоскости его вращения вдоль детали. Обработка выполняется в ванне 3 с диэлектрической жидкостью 4. Если разрезание выполняется пластиной с одним поступательным перемещением ее к заготовке, то это будет прошивание. В случае использования непрофилированного электрода (рис. 2.4, б) инструмент 1 выполняют в форме круглой проволоки диаметром 0,02... 0,3 мм или стержня, которые могут перемещаться в различных направлениях со скоростью
в любой части заготовки 2. Для устранения влияния износа электрода-инструмента на точность прорезаемых пазов проволоку или стержень перемещают (обычно перематыванием) вдоль оси со скоростью
. Разрезание выполняют в ванне с диэлектрической жидкостью.
4. Электроэрозионное упрочнение, включающее легирование и наращивание поверхности, обычно осуществляют на воздухе. Частицы расплавленного металла инструмента на воздухе не успевают остыть и оседают на поверхности заготовки, образуя на ней слой сплава, насыщенного легирующими элементами электрода-инструмента (либо легирующим компонентом из состава рабочей среды). Кроме того, нанесенный на заготовку слой закален до высокой твердости и имеет за счет этого повышенную износостойкость.
2.2. Механизм
Общее описание процесса. Удаление металла с заготовки происходит в среде диэлектрика за счет микроразрядов, расплавляющих часть металла. Рассмотрим основные стадии протекания электроэрозионного процесса снятия припуска. По мере сближения электрода-инструмента с заготовкой напряженность электрического поля возрастает обратно пропорционально расстоянию между электродами:
, где
— разность потенциалов электрода-инструмента и заготовки;
— зазор между электродами.
Наибольшая напряженность возникает на участке, где межэлектродный зазор минимален. Расположение этого участка зависит от местных выступов, неровностей на инструменте и заготовке, от наличия и размеров электропроводных частиц, находящихся в межэлектродном промежутке. На рис. 2.5 показано формирование расчетного зазора s между электродом-
![]() | |||
| |||
инструментом 3 и заготовкой 4. Зазор зависит от высоты местного микро- или макровыступа на заготовке. Напряженность поля в районе выступа будет наибольшей, что повышает вероятность пробоя межэлектродного промежутка в этой точке. Кроме того, напряженность будет зависеть от наличия электропроводных частиц 1 в диэлектрике 2. Частица 1 с размером
уменьшает расчетный зазор до размера
. Если не учитывать возможности присутствия в промежутке таких частиц, то следовало бы в расчетах принять зазор равным
. Поскольку истинный зазор будет меньше, чем расстояние между электродами, то напряженность поля на участках, где имеются электропроводные частицы, окажется выше.
Если электроды сблизить до расстояния нескольких десятков микрометров, то в отдельных местах напряженность поля может достигнуть значения, при котором в месте наименьшего зазора возникает электрический разряд, через промежуток протекает ток, т. е. имеет место направленное движение электронов. В электрическом поле, возникшем в межэлектродном пространстве, в направлении, обратном движению электронов, происходит перемещение более тяжелых частиц – ионов. Электроны, имеющие меньшую массу, быстро достигают положительно заряженной поверхности заготовки и нагревают металл, вызывая расплавление и испарение его в месте прохождения тока. В результате образуется углубление в форме сферической лунки (рис. 2.6, а) радиусом . Вылетевшие из лунки
![]() | |||||
![]() | |||||
| |||||
частицы металла охлаждаются жидкостью, которая находится в зазоре, и застывают в виде шариков. В качестве жидкости используют различные диэлектрики: масла, керосин, дистиллированную воду. При воздействии серии разрядов поверхность приобретает форму с явно выраженными углублениями в виде лунок (рис. 2.6, б). Такие лунки формируют микрорельеф, характеризующий шероховатость поверхности.
Поверхностный слой дна лунок испытывает воздействие термического цикла нагрева и быстрого охлаждения жидкостью. Свойства этого слоя отличны от свойств металла в глубине заготовки. В электроискровом режиме большинство ионов, имеющих значительную массу, не успевает достичь отрицательно заряженного электрода и вызвать удаление материала с его поверхности. Съем металла происходит преимущественно с анода, который выбирают в качестве заготовки. Количество ионов, достигающих поверхности инструмента, определяет интенсивность его износа. Очевидно, чем меньше будет износ инструмента, тем точнее можно получить деталь. Для этого стремятся сформировать импульс с меньшей длительностью, чтобы ионы не успевали достичь катода. Однако при этом возрастает время обработки и снижается производительность. Полярность, при которой заготовка является анодом, называют прямой. Электроэрозионная обработка, при которой используют электроискровой режим, обычно осуществляется при прямой полярности включения электродов.
Если увеличивать длительность импульсов тока, то растет интенсивность съема металла с катода (инструмента) потоком ионов. Можно подобрать такое время протекания тока, при котором доля съема металла электронами составит лишь незначительную часть от общего объема удаленного с электродов материала. Поэтому здесь необходимо катодом выбрать заготовку. Полярность, при которой анодом является электрод-инструмент, называют обратной. Обработку материалов при электроимпульсном режиме осуществляют при обратной полярности включения электродов. Полярность зависит не только от длительности импульса, но и от используемых в качестве электродов материалов. Для снижения износа электрода-инструмента от воздействия потока электронов его выполняют из материалов, слабо разрушающихся под действием искровых разрядов, графитовых и медно-графитовых композиций. Для количественной оценки применяют понятие относительного износа — отношения массы или объема материала, удаленного с электрода-инструмента, к массе или объему металла, снятого с заготовки.
При электроконтактном методе импульсы тока формируются непосредственно в промежутке. Схема метода приведена на рис. 2.7. Процесс протекает в диэлектрике 2. Поверхности
![]() | |||
| |||
электрода-инструмента 1 и заготовки 3 не являются идеально гладкими — на них имеются неровности. При вращении электрода-инструмента выступы приближаются к заготовке вплоть до контакта. На определенном расстоянии между электродами происходит разряд, переходящий в дуговой и вызывающий расплавление металла. Процесс этот кратковременный, поскольку за счет вращения электрода-инструмента выступ на его поверхности удаляется от заготовки и разряд в среде диэлектрика быстро затухает. При этом методе длительность и частота импульсов тока будет зависеть от формы и числа выступов на наружной поверхности инструмента и от скорости его вращения. Вращающийся электрод-инструмент сам регулирует параметры импульсов, поэтому не требуется специального генератора, а используется постоянный или переменный ток низкого напряжения. Электроконтактную обработку проводят при прямой полярности.
По мере съема металла с заготовки электрод-инструмент перемещают в зависимости от схемы обработки либо вдоль обрабатываемой поверхности (шлифование), либо по нормали к ней (разрезание) со скоростью .
Если процесс протекает в воздушной среде, то возникают более длительные дуговые разряды, чем при процессе в жидкости, так как после контакта между инструментом и заготовкой дуга может гореть довольно длительное время. При этом расплавленный металл может достигать противолежащей поверхности и там застывать, т. е. могут протекать одновременно два процесса — размерный съем и наращивание металла. Под действием тепла дуги выплавляются большие участки заготовки, процесс происходит интенсивно и сопровождается сильным световым излучением.
Электроэрозионное легирование ведут при обратной полярности, и частицы расплавленного металла оседают на катоде (заготовке).
Стадии протекания. Первой стадией эрозионного процесса является пробой межэлектродного промежутка в результате образования зоны с высокой напряженностью поля. Для диэлектрических жидкостей, применяемых при электроэрозионной обработке, напряженность поля в момент разряда достигает десятков мегавольт на метр. Под действием разряда происходит ионизация промежутка, через который между электродами 1 и 2 (рис. 2.8) начинает протекать электрический ток, т. е.
|
образуется канал проводимости 3 — сравнительно узкая цилиндрическая область, заполненная нагретым веществом (плазмой), содержащим ионы и электроны. Через канал проводимости протекает ток, при этом скорость нарастания его силы может достигать сотен килоампер в секунду. На границах канала происходит плавление металла, образуются лунки. На этой стадии форма лунки близка к сферической.
Второй стадией является образование около канала проводимости газового пузыря из паров жидкости и металлов. Вследствие высокого давления (до 2·107 Па) канал проводимости стремится расшириться, сжимая окружающую его газовую фазу. Вследствие инерции сначала газовый пузырь и окружающая его жидкость неподвижны. Затем начинается их расширение. Граница канала проводимости движется с высокой скоростью в радиальном направлении (рис. 2.9). Ско-
|
рость расширения может достигать 150... 200 м/с. На наружной границе образуется так называемый фронт уплотнения, в котором давление скачкообразно меняется от исходного в жидкости до высокого его значения на границе
Третьей стадией будет прекращение тока, отрыв ударной волны от газового пузыря и продолжение его расширения по инерции. Ударная волна гасится окружающей жидкостью.
В начале этой стадии (рис. 2.10) в межэлектродном промежутке находятся жидкий металл 2 в углублениях электродов 1 и 6 газовый пузырь 3, внутри которого имеются пары 4 металлов заготовки и инструмента; жидкий диэлектрик 5.
Когда газовый пузырь достигнет наибольшего размера, давление внутри него резко падает. Содержащийся в лунках расплавленный металл вскипает и выбрасывается в межэлектродный промежуток.
Не всякий импульс, вырабатываемый генератором, вызывает эрозию электродов. Может оказаться, что в момент
![]() |
поступления импульса велик межэлектродный зазор, напряжение, создаваемое генератором, мало для пробоя зазора. Проявляется влияние и других факторов. При большом удалении лунки от выхода из межэлектродного промежутка, например в крупногабаритных заготовках, вынос твердых частиц из межэлектродного промежутка становится замедленным и процесс эрозионной обработки может прекратиться. Для его поддержания применяют принудительное прокачивание диэлектрической жидкости через зону обработки.
Если материал заготовки хрупкий, то под действием высоких температур возможно не только выплавление металла, но и его скалывание и удаление достаточно крупными частицами.
При изготовлении углублений разряды возникают не только на рабочей стороне электрода-инструмента, но и на его боковых поверхностях. Поэтому кроме рабочего зазора, регулируемого скоростью подачи инструмента, формируется боковой зазор, зависящий от размера износа электрода-инструмента.
2.3 Моделирование процесса
Основные закономерности. Основные технологические показатели процесса (точность, качество поверхности, производительность) зависят от количества выплавленного за один импульс металла из лунки, определяемого энергией импульса, временем действия импульсов и частотой их следования. Энергия импульса как работа электрического тока зависит от произведения силы тока
на напряжение
за время
протекания импульса:
. (2.1)
В первом приближении энергию можно рассчитывать по средним значениям силы тока и напряжения:
. (2.2)
Среднее значение напряжения пробоя =(0,5...0,75)
, где
— напряжение холостого хода при разомкнутых электродах. Напряжение
легко контролировать в процессе обработки.
При электроискровом режиме принимают = 40... 180 В. Если используют электроимпульсный режим, то
=18... 36 В. Электроконтактная обработка в жидкой среде протекает при
=18... 40 В. в воздухе — при
= 3... 12 В.
Среднюю силу тока определяют через ее значение при коротком замыкании электродов:
=(0,5... 0,75)
. Силу тока короткого замыкания можно устанавливать и контролировать по приборам станка. Ее выбирают в зависимости от обрабатываемого материала и требуемой шероховатости поверхности. Для стали при черновой обработке
=20... 120 А, при чистовой обработке
=0,5... 5 А, для твердых сплавов
=0,05... 0,2 А.
Длительность импульсов обратно пропорциональна частоте
их следования. Поскольку между импульсами имеются паузы, то при расчете
необходимо учитывать скважность
— отношение периода
повторения импульсов к их длительности (
):
. (2.3)
Длительность импульса для черновой обработки сталей = 200... 105 мкс, для чистовой обработки
= 5... 200 мкс. Для твердых сплавов длительность импульса еще на 2... 3 порядка ниже. При электроэрозионной обработке используются импульсы различной формы (рис. 2.11), но одной полярности (униполярные).
![]() | |||
|
Форма импульсов подбирается такой, чтобы при определенных параметрах импульса получить наибольшее углубление на заготовке, т. е. достичь наиболее эффективного использования подводимой энергии. Так, увеличение тока в импульсе в два раза позволяет для определенного диапазона режимов поднять скорость эрозии в 2,5... 3 раза. В рабочем диапазоне режимов выбирают определенное соотношение максимального значения силы тока в импульсе к его длительности.
Тепловые процессы на электродах. Точно рассчитать температуру в окрестностях области разряда не представляется возможным, так как нет сведений о тепловых потоках, начальной конфигурации поверхности электрода и другой информации. Поэтому решение носит приближенный характер. Разряд, в частности, принимают стационарным точечным источником теплоты, теплофизические параметры — неизменными в течение времени протекания процесса, усредняют по времени тепловые потоки, методика нахождения температуры одинакова для обоих электродов.
Схема расчета показана на рис. 2.12. Точечный источник
![]() |
1 излучает теплоту равномерно во все стороны. Из-за малых размеров зазора большая его часть попадает на электрод 2. Граница плавления металла будет перемещаться по сфере, принимающей последовательные положения а, б, в, г, до окончания действия импульса напряжения. Для расчета принимаем, что потерь теплоты в межэлектродном пространстве не происходит. Из теории теплопередачи известно, что приращение температуры твердого тела зависит от энергии импульса , расстояния
до источника теплоты, удельной теплоемкости
и плотности
материала электрода, потерь энергии:
, (2.4)
где — температура в точке, находящейся в зоне действия импульса;
— начальная температура электрода;
— коэффициент полезного использования энергии импульса;
—безразмерный параметр температуры, учитывающий температуропроводность
электрода, время
действия источника тепла:
.
Здесь — критерий Фурье.
Для расчета необходимо знать значение коэффициента , который характеризует долю энергии импульса, используемую на расплавление металла. Он учитывает следующие потери теплоты:
на нагрев и испарение жидкости, образование ударной волны и газового пузыря. Эти потери оцениваются коэффициентом : при электроискровом режиме
, при электроимпульсном режиме
;
на нагрев второго электрода; потери уч