Проектный расчёт передачи
Определение допускаемoго контактного напряжения
Определим допускаемое контактное напряжение
примем 175,25МПа
Определение допускаемого напряжения изгиба
=0,25*460+0,08*700=171 МПа
Определение межосевого расстояния передачи
Предварительное значение межосевого расстояния находим по формуле
где - вспомогательный коэффициент (610 для эвольвентных, 530 для нелинейчатых червяков)
- момент на колесе, Н*м
- коэффициент, концентрации нагрузки
принимаем стандартное значение 160 мм
Основные параметры передачи
Число зубьев колеса
Модуль передачи
примем 6,3
Коэффициент диаметра червяка
примем 10
2.5. Размеры колеса и червяка
Делительный диаметр
Диаметр вершин зубьев
Диаметр впадин зубьев
Ширина венца
примем 65мм
Длина нарезаемой части
2.6 КПД передачи
- угол подъёма линии на начальном цилиндре
Приведённый угол трения примем для V=2.99 м/с 20
2.6. Проверочный расчёт на прочность
2.7 Силы в зацеплении
Окружная сила
2*42,52*1000/63=1350 Н
Радиальная сила
Осевая сила
2.8. Проверка зубьев по напряжениям изгиба
< 171 МПа
Где -коэффициент формы зуба (1,76)
- угол подъёма линии на начальном цилиндре
2.9. Тепловой расчет передачи
Определение температуры масла tm в корпусе червячной передачи
где tB - температура воздуха вне корпуса (в цеховых условиях tB=20
P1 - мощность на червяке, Вт; P1=3400 Вт
Кт - коэффициент теплоотдачи, зависящий от материала корпуса редуктора и интенсивности вентиляции помещения, Вт/(
Кт = 100 Вт/(
А- площадь свободной поверхности охлаждения корпуса редуктора, м2
Aр = (0,1...0,2)(20• ) = (0,1...0,2)(20*1602)=0,512…1.102 м2 (примем 0,53)
[tM] - допускаемая температура масла в корпусе. [tM]=70...80
![]() |
3 Расчет быстроходной зубчатой цилиндрической передачи редуктора
3.1 Данные
Таблица 3.1- Исходные данные
Параметр | Тихоходная передача редуктора |
1. Кинематические и силовые параметры: а) передаточное число u б) частота вращения шестерни п1, мин-1; в) вращающий момент шестерни Т1, Н·м; г) вращающий момент тихоходного вала ТТ, Н·м | u=uT=2 n1=nП=1530,6 -1 Т1=ТП=21,92 Н·м ТТ=42,52 Н·м |
2. Сведения о схеме передачи: а) вид передачи б) расположение колес относительно опор | косозубая Несимметричное |
3. Требуемая долговечность Lh, ч | Lh= 20000 |
3.2 Проектировочный расчет передачи
3.2.1 Выбор материала и твердости колес
Расчет выполняем для косозубой цилиндрической передачи редуктора, вал которого нагружен вращающим моментом ТТ =42,52Н·м. В соответствии с рекомендациями косозубой передачи и вращающем моменте материал колес передачи:
Таблица 3.2 - Материал и твердость колеса и шестерни
Зубчатое колесо | Марка стали | Термообработка | Твердость расчётная | sТ, МПа |
Шестерня | 40XH,35XM | Улучшение | Н1 = 285 HB Н2. = 250 HB | |
Колесо | 40XH,35XM | Улучшение | Н1 =250 HB Н2. = 250 HB |
3.2.2 Ориентировочное значение межосевого расстояния. Степень точности передачи
1.Ориентировочное значение межосевого расстояния:
10*(2+1)*3 21,92/2 =66,64 мм (3.1)
где значение коэффициента К=10; Т1 – вращающий момент шестерни, Н·м; u – передаточное число.
2. Окружную скорость передачи:
(2*3,14*66,64*1530) / (6*10000*(2+1)) =3,56 м / с (3.2)
Выбираем степень точности передачи: nCТ =8,0.
3.2.3 Допускаемые напряжения
3.2.3.1 Допускаемые контактные напряжения
Для расчета допускаемых контактных напряжений определяем:
1. Пределы контактной выносливости колес передачи:
sHlim1=2×HHВ+70=2*285+70=640 МПа; (3.3)
sHlim2=2×HHВ+70=2·250+70=570 МПа.
2. Коэффициенты запаса прочности:
3. Для расчета коэффициентов долговечности определяем: SH1= 1,1; SH2= 1,1;
а) базовое число циклов напряжений: NHG1 = 24300000; NHG2 =17100000
б) эквивалентное число циклов нагружения колес передачи:
NHE1=60×n1×c×Lh×μ =60×1530×1×20000 · 0,25=1836731999 (3.4)
где с – число вхождений зубьев колеса в зацепление за оборот, с = 1; μ - коэффициент эквивалентности.
NHE2 = NHE1 / u= 1836731999/2=459183000
Коэффициенты долговечности:
=0,66 (3.5)
0,84
Примем Zn1= 1 Zn2= 1
4. Коэффициенты шероховатости: zR1 = zR2 = 1.
5. Коэффициенты окружной скорости: zV1 = zV2, = 1.
Допускаемые контактные напряжения для шестерни и колеса:
640 * 1*0,9 / 1,1 = 523,82МПа; (3.6)
570 *1 * 0,9*1 / 1,1 = 466МПа
Принимаем [s] H =466,36 МПа.
3.2.3.2 Допускаемые напряжения изгиба
Длярасчета допускаемых напряжений изгиба определяем:
1. Пределы выносливости зубьев колес при изгибе: [s] Flim1= 498,75 МПа;[s] Flim2= 437,5 МПа
2. Коэффициенты запаса прочности: SF1 =1,75; SF,2 =1,75;
3. Для расчета коэффициентов долговечности определяем:
а) показатели степени кривой усталости: q = 6; q
= 6;
б) эквивалентное число циклов нагружения зубьев колес:
1836731999*0,065=119387580циклов (3.8)
459183000 *0,065= 59693790циклов
0,6
0,6
Принимаем: YN1= 1 ,YN2= 1
4. Коэффициенты шероховатости переходной поверхности между зубьями принимаем YR1,2 =1 (полагаем, что Rz< 40 мкм).
5. Коэффициент влияния реверсивности нагружения принимаем Y a = 1 (при одностороннем приложении нагрузки).
Допускаемые напряжения изгиба для зубьев шестерни и колеса:
(3.9)
498,75*1*1*1 / 1,75=285МПа
437,5*1*1*1 / 1,75 =250МПа
3.2.4 Межосевое расстояние передачи
Для расчета межосевого расстояния определяем:
1. Коэффициент ширины зубчатого венца: yba = 0,315
ybd= 0,5 ×yba× (u +1) =0,5×0,315×(2+1)=0,47 (3.10)
2. Коэффициент внешней динамической нагрузки принимаем КА = 1 (внешние динамические нагрузки включены в циклограмму нагружения, режим работы приводного вала конвейера является равномерным).
3. Коэффициент внутренней динамики нагружения: КHV= 1,06.
4. Коэффициент неравномерности- распределения нагрузки по ширине зубчатого венца в начальный период работы: = 1,02
Коэффициент, учитывающий приработку зубьев: КНw =0,22.
Коэффициент неравномерности распределения нагрузки после приработки:
KHb= 1+( -1)× КНw= 1+(1,07-1)×0,22 = 1,04 (3.11)
5. Коэффициент неравномерности распределения нагрузки между зубьями в начальный период работы: =1,04
Коэффициент распределения нагрузки между зубьями после приработки:
КНa= 1+0,15(nCТ -5) = 1+0,15(8,0-5)=1,04 (3.12)
Коэффициент нагрузки при расчете контактной прочности:
KH=KA×KHV×KHb×KHa= 1 * 1,06 * 1 * 1,04 = 1,102 (3.13)
Межосевое расстояние:
72,387 мм (3.14)
где - коэффициент, МПа
:
=410; Т1 – вращающий момент шестерни, Н·м; u – передаточное число; yba - коэффициент ширины венца.
Принимаем стандартное межосевое расстояние: аw =80мм.
3.2.5 Модуль зацепления
Длярасчета минимального значения модуля определяем:
1. Ширину зубчатого венца колеса: b2=yba× aw =0,315×80=25,2мм.
Расчетное значение b2 = 25мм приводим к нормальному линейному размеру b2=25 мм
2. Коэффициент внешней динамической нагрузки: КА = 1.
3. Коэффициент внутренней динамики нагружения: КFV= 1,04.
4. Коэффициент неравномерности распределения нагрузки по ширине зубчатого венца:
KFb= 0,18+0,82× =0,18+0,82×1,07=1,06 (3.15)
5. Коэффициент неравномерности распределения нагрузки между зубьями:
KFa= =1,18
Коэффициент нагрузки при расчете изгибной прочности:
KF=KA×KFV×KFb×KFa= 1×1,04×1,06×1,18=1,3 (3.16)
Минимальное значение модуля:
2800*21,92*(2+1) / 80*25*250=0,53; m =1 (3.17)
где Km - коэффициент для косоозубых Km = 2800; b2 – ширина зубчатого венца колеса.
3.2.6. Основные размеры передачи
1. Число зубьев, угол наклона, коэффициент смещения:
а) Определяем минимальный угол наклона зубьев:
bmin arcsin(4× m/b2)=arcsin(4×1/25)=9,210 (3.18)
принимаем предварительно bmin =9,21
б) Суммарное число зубьев:
ZS = (2× аw× cos bmin)/m=(2×80×cos9,21°)/1=157,9 (3.19)
Расчетное значение округляем в меньшую сторону до целого. Принимаем ZS = 157.
в) Фактический угол наклона зубьев:
b = arccos(ZS × т /(2× аw)) = arccos(157×1/(2×80))=11,11 (3.20)
г) Число зубьев шестерни и колеса:
Z1 = ZS /(u +1)=157/(2+1)=52;
Z2 = ZS - Z1 =157-52 =105. (3.21)
2. Фактическое передаточное число:
uФ= Z2/ Z1=105 /52=2,02 (3.22)
3. Основные геометрические параметры:
1) делительное межосевое расстояние
a=(Z1+ Z2) × m/(2 × cosb)=(52+105) ×1/(2×cos11,110)=80мм; (3.23)
2) коэффициент уравнительного смещения
D y = (а - aw)/ m = (80 - 80)/1 = 0;
3) делительный диаметр шестерни и колеса
d1 = Z1 m/cosb = 52×1/cos11,11° =52,99мм; (3.24)
d2 = Z2 m/cosb = 105×1/cos11,11° =107,01 мм;
4) начальный диаметр шестерни и колеса
dw1= d1; dw2= d2;(т.к а=аw;x1=x2=0)
5) диаметр вершин зубьев шестерни и колеса
da1=d1+2 × m=52,99 +1×2=54,99 мм
da2=d2+2 × m=107,01+1 ×2=109,01 мм (3.25)
6) диаметр впадин зубьев шестерни и колеса
df1=d1-2,5 × m=52,99- 2,5*1×=50,49 мм
df2=d2-2,5 × m=107,01- 2,5×1=104,51 мм (3.26)
7) ширина зубчатого венца колеса и шестерни
b2=yba × aw =0,315×80=25м; b1=b2+5=25 +5=30мм
примем b1= 30 мм
3.3 Проверочный расчет передачи
3.3.1 Расчет на контактную прочность
s
=
=377,8МПа (3.27)
= 8400(Н½/мм)
Контактная прочность обеспечена:sH=377,8МПа < [s]H =466,36 МПа,
недогрузка составляет 22%
3.3.2 Расчет на прочность при изгибе
1) Силы в зацеплении:
Окружная сила
2*1000*21,92 / 52,99=827 кН; (3.28)
Радиальная сила
827tg20 / cos 11,11=307 кН; (3.29)
Осевая сила
827* tg11,11 =162 кН. (3.30)
2) Коэффициенты формы зуба:
3.47 + 13.2*cos3 11,11 / 52 =3,71 (3.31)
3.47 + 13.2*cos3 11,11 / 105 = 3,59
3) Коэффициент, учитывающий угол наклона зуба:
1 – 11,11/100 =0,889 (3.32)
Условие ≥ 0,7 выполняется.
4) Коэффициент, учитывающий перекрытие зубьев:
=0,8.
Напряжения изгиба для зубьев колеса и шестерни:
827*1,43*3,59*0,897*0,8 / 25*1 =108,1МПа (3.33)
108,1 *3,71 / 3,59 = 111,7МПа. (3.34)
Прочность зубьев на изгиб обеспечена:
=108,1 МПа ≤
250МПа;
= 111,7
=282,5 МПа.
4. Эскизная компоновка редуктора
Таблица 4.1 – Параметры для эскизной компоновки
Параметр | Расчет |
1) δ- толщина стенки корпуса | δ≥0,025∙ aw +3≥0,025∙160+3=7 мм |
2) δ ![]() | δ ![]() |
3) b - толщина фланца корпуса и крышки | b =1,5∙δ=1,5∙7=10,5 мм |
4) b ![]() | b ![]() |
5) размер болтов | |
а) болт фундам. (М18, 4шт.) | ![]() |
б) у бобышек | ![]() ![]() |
в) на фланце | ![]() ![]() |
г) болты смотрового люка | ![]() ![]() |
6)толщина ребер корпуса и крышки | m=1,0∙ δ=16 мм |
7) диаметр прилива | |
крышка привинтная | ![]() ![]() ![]() ![]() |
8) расстояние между стяж. болтами | <10* ![]() |
9) диаметр штифта | ![]() ![]() |
4.1 Конструирование валов
4.1.1 Быстроходный вал
d (4.1)
где Т – вращающий момент быстроходного вала, Т =21,92 Н*м
d
19,4мм,.
принимаем d= 20 мм
d = d
= d+ 2· t
(4.2)
d > d
+ 3· r (4.3)
где d - диаметр ступени под уплотнение, d
- диаметр ступени под подшипник, d
- диаметр ступени буртика подшипника, t
- высота заплечника, r - радиус фаскиподшипника; t
=3 мм, r =1,5 мм.
d = d
= 20+2·3= 23мм, принимаем d
= d
= 25 мм,
d > 25+3·1,5=29,5 по ГОСТ 6636-69 округляем до ближайшего значения: d
= 30 мм.
d > d
+ (7…9)· m (4.4)
где m - модуль зацепления;
d = 50,49 мм
d
> 30+7·1= 37мм.
Условие не выполняется – шестерню выполняем заодно с валом.
Рисунок 4.1 – Вал быстроходный
4.1.2 Промежуточный вал
d
(4.5)
где Т – вращающий момент шестерни, Т =42,52 Н*м
d
29,7мм, принимаем d
=30 мм.
d = d
= d+ 2· t
d = d
=30 +2·3= 36мм, принимаем d
= d
=40 мм (4.6)
d > d
+ 3· f (4.7)
где d - диаметр ступени под уплотнение, d
- диаметр ступени под подшипник, d
- диаметр ступени буртика подшипника, d
- диаметр вала под колесом, d
- диаметр ступени буртика колеса, r - радиус фаскиподшипника, f- размер фаски колеса; r = 2 мм, f = 1мм.
d >40+ 3*2=46 мм, принимаем d
=46 мм,
d
=46 мм.
Рисунок 4.2 – Вал промежуточный
4.1.3 Тихоходный вал
d (4.9)
где Т – вращающий момент тихоходного вала, Т =637,8 Н*м
d 47,37мм, принимаем d= 50 мм.
d = d
> d+ 2· t
(4.10)
d > d
+ 3· r (4.11)
d =d
(4.12)
где d - диаметр ступени под уплотнение, d
- диаметр вала под колесом, d
- диаметр ступени под подшипник, d
- диаметр ступени буртика подшипника, t
- высота заплечника, r - радиус фаскиподшипника; t
= 4 мм, r = 3 мм.
d = d
> 50 + 2·4=56 мм, принимаем d
= d
= 55 мм,
d > 55 + 3·3= 64мм, принимаем d
= 65 мм,
d =d
= 65м.
Рисунок 4.3 – Вал тихоходный
4.2 Конструирование зубчатых колёс
![]() |
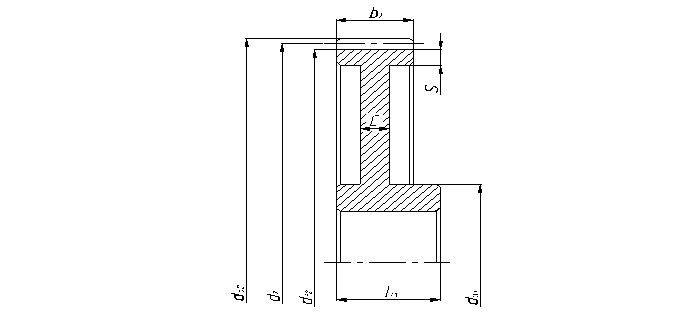
Рисунок 4.4 – Колесо зубчатое
Таблица 4.2 – Параметры для конструирования зубчатых колес
быстроходная ступень | тихоходная ступень | |
d2 | 107,01 | |
da2 | 109,01 | 264,6 |
df2 | 104,51 | 236,8 |
b2 | ||
dK | ||
S | - | |
C | 19,5 | |
dст | 46,5 |
b2 = lступ dK – из расчётов валов
da2, df2, d2 – из распечаток
C ≈ 0,3·b2
S ≥ 2,5·m + 2 мм, где m – модуль передачи
dст = 1,55·dK
![]() |
4.3 Конструирование подшипниковых узлов
Рисунок 4.5 – Подшипники
Таблица 4.3 – Данные для конструирования подшипников
Вал редуктора и обозначение подшипника | Размеры, мм | ||
α=26° | d | D | B |
Быстроходный | |||
Промежуточный | |||
Тихоходный |
4.4 Конструирование корпусных деталей
Для установки и крепления подшипников в корпусе применяются приветные крышки. В качестве уплотнений используются манжеты.
а) б) в)
Рисунок 4.6 – Крышки привертные: а) глухая, б) сквозная, и манжета (в)
Основные размеры крышек:
Для быстроходного вала:
D=62 мм; δ=5мм; d=6 мм; z=4; δ1=6 мм; DФ=86мм; с=6 мм.
Для промежуточного вала:
D=80 мм; δ=6мм; d=8 мм; z=4; δ1=7,2 мм; DФ=112мм; с=8 мм.
Для тихоходного вала:
D=120 мм; δ=7 мм; d=10 мм; z=6; δ1=8,4 мм; DФ=160 мм; с=10 мм.
5 Расчёт тихоходного вала на прочность
5.1 Расчёт вала на прочность по напряжениям изгиба и кручения
Рисунок 5.1 – Эпюры моментов на тихоходном валу
а =52мм, b = 52 мм, c =132мм, l=104 мм– размеры с чертежа;
Ft =1350 Н, Fr = 493 H, Fa=1230 H, d = 252 мм;
637,8 =1260 Н
Плоскость YOZ
= (-1260*(52+52+132)+493*52-1230*252/2)/(52+52) =-4041Н
--4041+493-1260=3275 Н
Плоскость XOZ
(1350*52) /(52+52) =675 Н
1350-675= 675 Н
3300Н
4096 Н
Плоскость YOZ
Сечение I и II
3275*52-1230*252/2=14063 Н·мм
1260*132=166320 Н·мм
Плоскость XOZ
Сечение I
675*52=35100 Н·мм
37560 Н·мм (5.1)
498000 Н·мм (5.2)
166320Н·мм
595000 Н·мм
33 мм (5.3)
33 мм
- 60 МПа
5.1. Расчёт тихоходного вала на выносливость.
, (5.4)
Материал вала-шестерни сталь 40XH,35XM, для которой 950МПа,
800МПа,
350МПа,
210МПа
Сечение (шпоночная канавка)
Для сечения 1 моменты сопротивления вала при изгибе и кручении с учётом ослабления шпоночной канавкой
3,14 *653 / 32 – 18*7*(65-7)2 / 2*58 =16320 мм3 (5.5)
3,14 *653 / 16 – 18*7*(65-7)2 / 2*58 = 35466 мм3 (5.6)
где b- ширина шпоночной канавки
t- высота (по ГОСТу 23360-78)
Находим амплитуды циклов σа, τа и средние составляющие σm, τm циклов напряжений при изгибе и кручении.
= 498000 / 16320 =30,5 (5.7)
637800 / 2*35466 = 9,3 (5.8)
,
- коэффициенты абсолютных размеров (
= 0,85
=0,75)
-коэффициент влияния шероховатости поверхности (для шлифованного вала
=1)
- коэффициент влияния упрочнения (
=1)
-коэффициенты чувствительности материала к асимметрии цикла
,
- эффективные коэффициенты концентрации напряжений для шпоночной канавки
=2,15
=2,05
В сечении 2 два источника концентрации напряжений, поэтому необходимо для каждого из них сопоставить величины соотношения и
Шпоночная канавка = 3,5
=2,6
Напряженная посадка =3,4
=2,5
В расчётах учитываем источник концентрации с наибольшим соотношением
=3,5 (5.9)
=2,6 (5.10)
Коэффициенты запаса по нормальным и касательным напряжениям (по изгибу и кручению)
Сечение 1
=350 / 3,5*30,5 = 3,33
=210 / (2,6*9,3 + 9,3*0,05) = 8,6
Коэффициент запаса усталостной прочности вала в сечении 1
2,96 > [S]=2
6 Расчёт на долговечность подшипников тихоходного вала
6.1 Подготовка исходных данных
- Lh = 20000 часов
- n2 =765,31 мин-1
- RA=Fr1=3300 Н, RB=Fr2=4096 Н
- Fа =1230 Н
- подшипники №46311
- dВН =55 мм
- Cr=82,8 кН, Cor=51,6 кН
6.2 Составление расчётной схемы
Рисунок 6.1 – Схема подшипников
6.3 Определение коэффициентов радиального и осевого нагружения
Принимаем e =0,68
1230 / 1*3300 =0,37 (6.1)
e > 0,37 X=1, Y=0
1230 / 1*4096 =0,30 (6.2)
e > 0,30 X=1, Y=0
6.4 Определение эквивалентной нагрузки
(6.3)
P1=(1*3300 + 0)*1.3*1=4290 Н
P2=(1*4096 +0)*1.3*1=5325 Н
6.5 Определение приведенной эквивалентной нагрузки
(6.4)
где – коэффициент напряжённости
61948,30часов ≥ Lh=20000, выбранный подшипник обеспечивает оптимальный ресурс работы в оптимальных условиях эксплуатации.
7 Расчёт шпоночных соединений
МПа, (7.1)
где Т – момент на валу, d – диаметр вала, h – высота шпонки, t – глубина паза, l – рабочая длина шпонки.
7.2Промежуточный вал
2* 42,52 / 30* (8-5)*100 =62мм
10 мм
8 мм
5 мм,
8+10=18мм
7.3 Тихоходный вал
2* 637,8 / 65* (12-7,5)*100 =36мм
20 мм
14 мм
7,5 мм,
36+20=56мм
Рисунок 7.1 – Шпоночное соединение
8 Выбор муфты
Тр=Кр*Т,
Где Кр - коэффициент режима работы
Т - номинальный вращающий момент, Н*м
Тип машин-Конвейеры ленточные, (Кр=1,25….1,5)
Конвейеры цепные, (Кр=1,5….1,8)
Тр=Кр*Т=1,5*21,92=956,7Н*м
Упругие муфты работают при больших оборотах и сравнительно небольших вращающих моментах, зубчатые муфты наоборот применяют при небольших частотах вращения и большом крутящем моменте.
Рисунок 8.1 Муфта упругая
Упругие муфты компенсируют несоосность валов, смягчают толчки и удары за счёт деформации упругого элемента. Муфта компенсирует радиальное смещение вала до 0,6 мм, угловое смещение до 1’ и небольшое осевое смещение вала для проверки прочности рекомендуется поводить расчёт пальца по напряжениям изгиба, а резину по напряжениям смятия.
(8.1)
(8.2)
D1 | |
Z | |
D п | |
l р |
Таблица 8.1 Данные муфты
где