Сталь | Способ раздачи* | Диаметр трубы, мм, не более | Толщина стенки трубы, мм, не более | Раздача А**, %, не более |
Углеродистая Низколегированная: теплоустойчивая конструкционная | Вхолодную С нагревом Вхолодную С нагревом Вхолодную С нагревом | 84-200 |
Аустенитная Вхолодную 83 6 6
Вхолодную 84-100 10 4
Мартенситно- ферритная и мартенситная
Вхолодную 100 6 4
* Раздачу с нагревом следует производить при температуре концов трубы 900—1000 °С из низколегированных теплоустойчивых сталей, при 700—900 °С — из низколегированных конструкционных и углеродистых сталей.
** Подсчитывают по формуле А = (Д 2 - Д 1 ) 100/ Д 1, где Д 1 и Д 2 — внутренний диаметр трубы соответственно до и после раздачи.
После механической обработки длина наплавки l должна быть не менее: Диаметр трубы, мм l, мм
До 219 20
Свыше 219 до 273 30
Более 273 50
Толщина наплавки должна быть не более 6 мм. Наплавку можно выполнять ручной дуговой или ручной аргонодуговой сваркой неплавящимся электродом с использованием присадочных материалов, которые применяют для сварки стыка, при режиме подогрева и охлаждения, предусмотренном для данных стыков. Наплавку следует производить кольцевыми (спиральными) валиками в направлении изнутри трубы к ее торцу. Термообработку места наплавки перед сваркой стыка не проводят;
г) приварка впритык к элементу (трубе, патрубку, тройнику, арматуре) с меньшим внутренним диаметром кольца шириной b = 18—20 мм и наружным диаметром, равным внутреннему диаметру другого стыкуемого элемента (рис. 6.3, д).
При сборке стыка элемент с большим внутренним диаметром надвигается на приваренное кольцо с соблюдением требований к сборке и сварке как к обычному стыку с подкладным кольцом. Такой способ может быть применен к трубопроводам из углеродистой и низколегированной конструкционной стали при разности внутренних диаметров стыкуемых элементов не более 8 мм.
6.1.7. При соосной стыковке труб с различными наружными диаметрами размер h (рис. 6.4)
должен быть не более:
для труб из углеродистой и низколегированной сталей — 30% толщины более тонкой трубы, но не более 5 мм;
для труб из стали аустенитного, мартенситного и мартенситно-ферритного классов при номинальной толщине стенки 10 мм и менее — 15% толщины более тонкой трубы.
В обоих случаях плавный переход от одной детали к другой со стороны раскрытия шва должен быть обеспечен за счет наклонного расположения поверхности шва.
Когда смещение (несовпадение) стыкуемых труб по наружной поверхности из-за разности наружных диаметров превышает указанное, конец трубы с большим наружным диаметром должен быть обработан механическим способом (обточкой) согласно одному из эскизов рис. 6.4.
Рис. 6.4. Схема обработки концов труб при стыковке элементов, имеющих разные наружные диаметры:
а — соединения трубы с трубой; б — соединения трубы с литыми, коваными и штампосварными деталями и арматурой; в — соединения трубы с арматурой,
фасонными и трубными деталями с комбинированной разделкой кромок
6.1.8. Вмятины на концах труб следует исправлять с помощью домкратов или других разжимных устройств при условии, что глубина вмятины не превышает 3,5% наружного диаметра трубы (Д н), а толщина стенки для труб из углеродистых и низколегированных сталей не более 20, из аустенитных — 10, из мартенситных и мартенситно-ферритных — 6 мм.
Вмятины на трубах из углеродистых и низколегированных сталей допускается исправлять вхолодную или с нагревом (табл. 6.1), из аустенитных, мартенситных и мартенситно-ферритных
— только вхолодную.
Концы труб с вмятинами глубиной более 3,5% Д н а также с забоинами и задирами глубиной более 5 мм следует обрезать или исправлять путем наплавки.
6.1.9. Кромки литых, кованых, штампованных, штампосварных деталей должны быть обработаны под сварку на заводе-изготовителе. В случае необходимости обработки таких деталей в условиях монтажа или ремонта она должна производиться по заводским нормалям либо в соответствии с требованиями п. 6.1.6, б, в или п. 6.1.7 по согласованию с заказчиком (владельцем оборудования).
6.1.10. В монтажных и ремонтных условиях допускается исправлять гибы путем подгибки или отгибки, если:
на трубах наружным диаметром не более 108 мм из углеродистых и низколегированных конструкционных сталей угол подгибки или отгибки не превышает 15°, из хромомолибденовых и хромомолибденованадиевых сталей — 10°;
на трубах наружным диаметром более 108 мм угол подгибки или отгибки не превышает 10° и
5° соответственно.
Трубы из хромомолибденовых и хромомолибденованадиевых сталей независимо от толщины стенки при подгибке следует подогревать в месте подгибки до 710—740 °С. Трубы из низколегированных конструкционных и углеродистых сталей можно подгибать в холодном состоянии при толщине стенки до 20 мм, при большей толщине — с подогревом до 650—680 °С. После подгибки нагретый участок необходимо обернуть асбестом. Место подгибки должно
находиться вне гиба трубы; при ее диаметре более 100 мм место подгибки должно быть на расстоянии не менее 200 мм от гиба.
Температуру контролируют с помощью термокарандаша, термоэлектрического преобразователя (ТП) или термокраски. Термообработка места подгибки не требуется.
6.1.11. Подгибка и отгибка труб из сталей аустенитного класса диаметром менее 100 мм при толщине стенки не более 10 мм может быть допущена в монтажных условиях на угол не более
10° и должна осуществляться в холодном состоянии без последующей термообработки.
6.1.12. Подгибку труб из стали мартенситного и мартенситно-ферритного класса в условиях монтажа можно производить в холодном состоянии, угол подгибки должен быть не более 10°.
Сборка стыков труб
6.2.1. Конструкции сварных соединений должны быть указаны в проектно-конструкторской документации.
Основные рекомендуемые конструкции стыков сварных соединений даны в табл. 6.2. Допускается применение сварных соединений с другими конструктивными размерами подготовки кромок, если при этом обеспечивается надлежащее качество соединения.
6.2.2. При сборке стыков труб под сварку следует пользоваться центровочными приспособлениями, предпочтительно инвентарными, непривариваемыми к трубам. Рекомендуются приспособления, приведенные в приложении 11.
При сборке стыков труб из хромомолибденовых и хромомолибденованадиевых сталей с помощью уголков (см. рис. П.11.1 приложения 11) приварка этих элементов к трубам должна производиться электродами типа Э42А или Э50А с предварительным подогревом места приварки согласно данным табл. 6.3. Уголки могут быть удалены (механическим путем или газовой резкой) после наложения не менее трех первых слоев стыкового шва. Места приварки этих деталей к трубам должны быть зачищены и тщательно осмотрены для выявления поверхностных трещин. В случае обнаружения дефекта это место должно быть выбрано с помощью абразивного инструмента. Если после выборки дефекта толщина трубы будет меньше допустимой расчетной, производится наплавка в соответствии с рекомендациями раздела 19.
Уголки должны быть изготовлены из стали марок 20, Ст2 или Ст3.
Таблица 6.2
|
|
Тип разде лки | Конструктивные элементы подготовленных кромок свариваемых деталей | Способ сварки | Конструктивные размеры | Наружный диаметр трубы, Д н, мм | |||
S, мм | а, мм | b, мм | , градусы | ||||
Тр-1 | РАД Г ААД РД АФ | 1-3 1-3 2-3 4-8 | 0,3(1±0,5) 1±0,5 0,3 1±0,5 1,5+0,5 | — — — — — | — — — — — | ||
Тр-2 | РД, МП РД, МП АФ | 3-5 6-14 15-25 | 1+0,5 1,5±0,5 2+0,5 | 1±0,5 | 30±3 (25-45) | РД, МП - независимо, АФ - более 200 | |
К(РАД), К(ААД) | 4-25 | 0,5(1,5±0,5) | |||||
РАД, ААД Г | 2-10 3-8 | 0,5(1,5±0,5) 1,5±0,5 |
Тр-3 | РД | По п. 6.2.9 | — | 15±2 | > 100 | ||
Тр-3а | РД | По п. 6.2.9 | — | 7+1 | > 100 | ||
Тр-3б | АФ | 4-5 > 5 | 4+1 6+1 | — | 12+2 12+2 | > 200 > 200 | |
Тр-3в | МП | 8+1 | — | 15±2 | |||
Тр-3г | РД | По п. 6.2.9 | — | 30±3 (25-45) | > 100 | ||
Тр-3д | МП | 8+1 | — | ||||
Тр-6 | МПК(РА Д), К(ААД) | 2±0,5 0,5(1,5±0,5) | 1,5+0,5 1,5+0,5 | 10±2 10±2 | |||
Тр-7 | К(РАД), К(ААД) | > 5 | 0,5(1,5±0,5) | 3±0,2 | 15±2 |
|
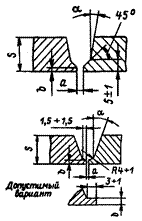
2. Зазор «а» для способов сварки РАД, ААД, К(РАД), К(ААД) указан без скобок в случае выполнения
корневого слоя шва (первого прохода) без присадочной проволоки, в скобках — с присадочной проволокой.
3. В седьмой графе в скобках приведены допустимые пределы угла скоса кромок «», отличного от оптимального из-за неточности обработки или из-за изготовления труб по другим стандартам или техническим условиям.
Таблица 6.3