Влияние дефектов на прочность композитов
А.Н.Полилов
Институт машиноведения им. А.А.Благонравова РАН
Цель данной обзорно-аналитической работы – показать с применением различных механических моделей, как дефекты разных уровней и генезиса влияют на прочность волокнистых композитов – материалов, искусственно созданных с целью реализации биомеханических принципов сочетания прочности, надежности и живучести.
Среди огромного разнообразия конструкционных композитов [11], представляющих собой специально созданные неоднородные материалы, состоящие из матрицы (занимающей связную область) и армирующих элементов (несвязная область), разделённых явно выраженной границей раздела, можно выделить основные группы, отличающиеся: 1) по химическому составу матрицы (полимерная, металлическая, углеродная, керамическая), 2) по типу армирующих элементов (дисперсные частицы (нуль-мерные элементы), волокна, нитевидные монокристаллы – «усы» (одномерная арматура), пленки, фольги, ткани (двухмерная арматура), 3) по химическому составу волокон (стеклянные, углеродные, борные, керамические, органические, базальтовые, металлические), 4) по структуре армирования (нуль-мерное армирование – частицы, хаотические короткие волокна – скалярная мера армирования - указывается только объемное содержание наполнителя; одномерное армирование – однонаправленные короткие или непрерывные волокна – векторная мера армирования - указываются направление и объемная доля волокон; армирование фольгой, плёнками также можно считать векторным – указывается направление нормали и объёмная доля армирования; двухмерное армирование – ткани, ортогональная, косоугольная, многонаправленная укладка волокон в плоскости или по некоторой поверхности- указываются направления укладки и доля слоёв с данным направлением, например, (0m/ + 45n/90k) – m слоёв препрега уложено в основном направлении, по n слоёв под углами +450 и -450 к этому направлению и k слоёв – в перпендикулярном направлении при общем числе слоёв m+2n+k; трехмерное 3-Д - при плетении или прошивке уложенного пакета слоев),5) по технологии изготовления (намотка, выкладка, автоклавное прессование, формование в вакуумном мешке, экструзия, пултрузия, плетение). В этом многообразии материалов наибольшие перспективы имеют армированные волокнами пластики (стекло-, угле-, органопластики), позволяющие создавать прочные, легкие, оптимально армированные материалы-конструкции /12/. В них реализуются основные принципы создания прочных и надежных материалов, используемые Природой в древесине, кости, дентине зуба, раковине. Эти законы – направленность (совпадение направлений укладки волокон с направлениями основных усилий) и неоднородность (чередование сильных и слабых элементов, что обеспечивает нехрупкость, нечувствительность к трещинам).
Сложность структуры композитов приводит к необходимости рассматривать дефекты на различных уровнях и на разных стадиях изготовления компонентов, материалов, изделий, а также в связи с различными механическими, температурными, химическими, физическими воздействиями в процессе эксплуатации.
Следует отметить принципиальное отличие всей технологической цепочки производства композитных изделий от традиционных «металлических» технологий, которые включают в себя энергоёмкие и вредные в экологическом отношении процессы: «добыча руды и кокса – выплавка чугуна и стали – отливка – прокатка – изготовление заготовок – механическая обработка – сборка – отделка – покраска». Наибольший эффект может быть достигнут, когда удаётся реализовать «композитную» низкоэнергоёмкую (низкие температуры полимеризации) безотходную технологическую цепочку: «производство компонентов (волокна, матрицы) – создание полуфабрикатов (ткани, ленты, ровинг, препреги) – создание готовых изделий (интегральных – без механической обработки и сборки, с окраской в массе). На этих этапах могут возникать технологические дефекты различных структурных уровней:
- микродефекты в компонентах (волокнах, матрице, на границе раздела),
- минидефекты в полуфабрикатах (тканях, препрегах, слоях),
- макродефекты в композитных изделиях.
Как и для других конструкционных материалов, по своему происхождению дефекты в композитах можно разделить на:
- технологические (возникающие в процессе изготовления волокон, полуфабрикатов или изделий),
- конструкционные (связанные с необходимостью изменения формы детали в местах соединения композитных и металлических элементов - например, отверстия под заклепки или болты),
- эксплуатационные (развивающиеся в процессе монотонного, многократного, циклического или длительного нагружения. Развитием такого рода дефектов занимается относительно новая ветвь механики разрушения – механика повреждений - damage mechanics).
ТРИ СЕКРЕТА ПРОЧНОСТИ КОМПОЗИТОВ
Попытки создания новых прочных материалов только за счет усиления химических связей не приводят к желаемому результату [2]. Действительно, теоретическая прочность материалов sтеор оценивается значением E/5 - Е/6, где Е – модуль Юнга материала. Если бы реальные материалы обладали такой прочностью, конструкции практически никогда бы не ломались. Однако за счет неизбежно существующих дефектов кристаллической структуры, из-за образования дислокаций, дисклинаций, микротрещин, вызывающих около своей вершины огромную концентрацию напряжений, реальная прочность sреал оказывается в 10 – 100 раз ниже теоретической. Например, модуль упругости стали составляет Е = 210 ГПа. Следовательно, теоретическая прочность стали равна sтеор = 35000 - 42000 МПа, а на практике реальная прочность стали примерно в 30 – 50 раз ниже: sреал = 800-1000 МПа, и только в специальных стальных волокнах, так называемой рояльной проволоке, удается достичь прочности порядка 5000 МПа = 1/8 sтеор. Долгие годы теоретическая прочность казалась недостижимой. Путь приближения к ней связан с первым секретом прочности.
1.1. Масштабный эффект прочности волокон. В 1920 г. была опубликована ставшая классической работа А. Гриффитса /1/, в которой он привел данные по резкому возрастанию прочности стеклянных волокон с уменьшением их диаметра. Одна из основных причин – уменьшение длины микродефектов, которая не может превышать диаметра волокна. Полученная Гриффитсом оценка прочности s=Ö2Eg/L в зависимости от длины дефекта L (где Е – модуль Юнга, g - удельная работа разрушения, аналог поверхностной энергии для хрупких материалов /4/) показывает, что с уменьшением диаметра d (d » L) прочность приближается к теоретической (рис.1). Это важнейшее достижение науки о материалах – возможность получения сверхпрочных волокон неметаллической природы – было реализовано также в нитевидных монокристаллах – усах, представляющих собою кристаллы с сильно искажённой решеткой, по сути, это единственная винтовая дислокация, которая не может развиваться, и разрушение происходит при исчерпании прочности химических связей, равной теоретической прочности. Таким образом, первый секрет прочности волокнистых композитов состоит в возможности реализовать очень высокую, близкую к теоретической, прочность в тонких волокнах, служащих арматурой для композита.
|
|


|
|
|

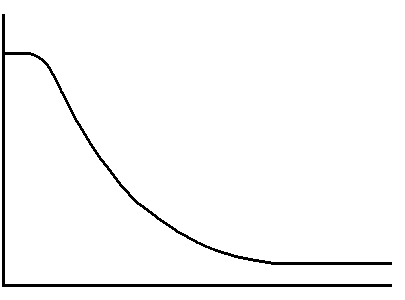
Рис. 1. Зависимость прочности от диаметра волокна.
1.2. Остановка трещины поверхностью раздела. Второй секрет прочности связан с механизмом снятия повышенных напряжений около дефектов, трещин, что делает композитный материал нехрупким, нечувствительным к трещинам поперек волокон. Около кончика трещины в нагруженном нормально направлению трещины материале (рис. 2, а) возникает значительная концентрация напряжений, приводящая обычно к росту трещины и к разрушению. Местное повышение напряжений в анизотропной пластине с эллиптическим отверстием с полуосями а и в, характеризуемое теоретическим коэффициентом концентрации напряжений, равным отношению наибольшего напряжения в т. А к среднему приложенному напряжению,
Кт=sму/sоу = 1+ а/в (b1+b2)/b1b2, где параметры b1 и b2 выражаются через упругие модули композита /10/ (для изотропного материала b1 = b2 = 1), должно приводить к значительному снижению прочности, особенно при в/а = e ® 0. Однако реальное снижение прочности, характеризуемое эффективным коэффициентом концентрации напряжений Кэ = sг/sт или коэффициентом снижения прочности 1/ Кэ (где sг и sт – прочности гладкого образца и образца с трещиной), оказывается всегда намного меньше, т.е. Кэ всегда ниже, чем Кт.
Рис. 2 Концентрация напряжений в эллиптической трещине.
В металлах снижение концентрации напряжений около кончика трещины происходит за счёт пластических деформаций, но даже в композите из упругих и хрупких компонентов (например, стеклянные волокна и эпоксидная матрица) происходит остановка трещин из-за наличия непрочных поверхностей раздела. Причина заключается в том, что перед кончиком трещины (рис. 2) возникает сложное напряженное состояние, и кроме основных напряжений sу, достигающих наибольшего значения sум в вершине трещины с координатами (а,0), существуют поперечные напряжения sх и касательные напряжения tху. Они и вызывают разрушение поверхности раздела, параллельной направлению нагружения (оси у), и вновь образованная микротрещина вдоль границы раздела является ловушкой для первоначальной макротрещины. В /3/ было рассчитано отношение максимальных поперечных напряжений sхм, разрывающих поверхность раздела, к максимальным напряжениям вдоль волокон sум и оно при e®0 для изотропного случая равно примерно 1/5. Гордон /2/ утверждал, что если поперечная прочность составляет меньше, чем 1/5 от продольной, то магистральная трещина вызовет перед собой разрушение поверхности раздела, и продольная микротрещина остановит развитие магистральной, поперечной волокнам трещины. В противном случае, если прочность связи волокно-матрица слишком велика, трещина будет беспрепятственно пересекать поверхности раздела, и материал будет вести себя хрупким образом. В /5/ на основе решения задачи теории упругости для ортотропной пластины с эллиптическим отверстием /10/ получено точное аналитическое выражение для этого отношения:
sхм/sум = t b1b2/ (t4/3 + t 2/3 + 1)3/2, где t = b1/b2, в изотропном случае это отношение равно
1/ (3 Ö 3) = 0.192, что согласуется с численными расчетами, проведенными в /3/. Однако наибольшие значения нормальные sхм0 и касательные tху* напряжения достигают в некоторых точках В контура трещины, и поэтому расщепление границы раздела волокно-матрица начинается на контуре отверстия или трещины (рис. 2, b). Для наибольших напряжений на контуре получены отношения sхм0/sум = t b1b2/ (t 2+ 1)2 и tхум/sум = (3 Ö (3 /2)t b1(t + 1)(А+2В)-1(А-В)-1/2, где В=(t 2 + 1), А = (В2 +12 t 2)-1/2. В изотропном случае первое отношение равно 0.25=¼, а второе (3Ö3)/16=0.325, с ростом анизотропии (t®¥) наибольшие поперечные напряжения esхм и esхм0 стремятся к нулю, а наибольшие касательные напряжения etхум стремятся к конечному пределу и tхум/sхм0®¥, то есть касательные напряжения оказывают большее влияние на разрушение границы раздела, чем поперечные. Анализ условий разрушения поверхности раздела позволяет указать оптимальные упруго-прочностные свойства границы раздела для заданных свойств волокон /5/, когда одновременно достигаются условия разрыва волокон и разрушения поверхности раздела, и слабая поверхность раздела в композите не допускает хрупкого разрушения, реализуя механизм остановки трещины.
Способность к торможению трещин за счет непрочных поверхностей раздела – одно из главных преимуществ композитов. Благодаря этому, удается одновременно повышать прочность и трещиностойкость композитов, в то время как для традиционных сплавов наблюдается обратная тенденция: рост прочности (снижение пластических свойств), как правило, сопровождается снижением трещиностойкости (а значит, надёжности), что особенно опасно при низких температурах, например, в емкостях для жидкого гелия (сверхпроводимость), где композиты оказываются чрезвычайно эффективными.
1.3. Статистический характер прочности волокон. Третий секрет прочности состоит в возможности реализации в композитах высокой прочности бездефектных участков волокон. Стеклянные, углеродные, борные и другие волокна содержат различные дефекты (поверхностные, внутренние), случайным образом распределенные по длине волокон. Это обусловливает особый статистический характер распределения прочности волокон (рис. 3) и делает необходимым исследовать не только среднюю прочность волокон, но и функцию распределения прочности. Для обычных материалов требуют, чтобы средняя прочность была бы как можно выше, а разброс прочности от образца к образцу (характеризуемый коэффициентом вариации) - как можно ниже. В случае волокнистого однонаправленного композита одинаковая прочность всех волокон (прямая вертикальная линия 1 на графике функции плотности распределения прочности – рис. 3) привела бы к мгновенному разрушению при достижении приложенными напряжениями этой прочности. Такой материал ненадежен, он «не предупреждает» о близком разрушении. Напротив, желательно, чтобы вначале происходили разрывы волокон в слабых местах, предупреждая (например, сигналами акустической эмиссии или снижением эффективного модуля упругости) о близящемся разрушении, в то время как прочные участки волокон продолжали бы нести нагрузку. Около разрыва волокна нагрузка перераспределяется на соседние волокна, которые остаются неразорванными, так как маловероятно попадание в одно сечение нескольких дефектов одновременно. При плотной гексагональной упаковке каждое волокно окружают 6 волокон, поэтому при разрыве одного волокна коэффициент перегрузки на соседние волокна составит примерно 7/6, при двух разорванных соседних волокнах – 10/8, при трех - 13/10 и т.д. В месте обрыва продольное напряжение в волокне отсутствует, однако, на некотором расстоянии Lэ вдоль волокна от места обрыва, которое называется эффективной длиной, напряжение в волокне выравнивается практически до среднего значения, как и в неразорванных волокнах. Таким образом, волокно «помнит» о своем разрыве только на участке эффективной длины Lэ, а вне этого участка ведёт


|
|
|

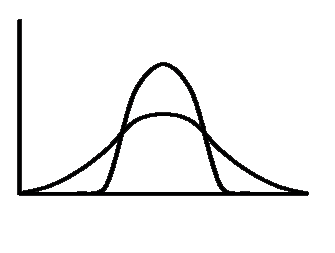






ДЕФЕКТЫВ КОМПОНЕНТАХ.
2.1. Дефекты в армирующих элементах. Наибольший интерес представляют тонкие носители прочности – волокна, и в них в процессе изготовления и эксплуатации могут возникать различные типы дефектов в зависимости от химической природы волокна. Стеклянные волокна в процессе изготовления путем выдавливания через фильеры приобретают внутренние и поверхностные трещины, которые могут значительно снизить прочность хрупких волокон. Чтобы избежать влияния поверхностных трещин, на волокна перед дальнейшей переработкой (скручиванием в нити, жгуты, намоткой на бобины, плетением тканей) наносят тонкий слой замасливателя, поверхностное натяжение которого как бы стягивает берега трещины, препятствуя её распространению.
Углеродные волокна, наиболее перспективные в связи с их очень высокими потенциальными свойствами (прочность до 10000 МПа, температура работы до 3000 0 С), имеют сложное внутреннее строение, они состоят из вытянутых плоских микроволокон – фибрилл, разориентация которых (обычно средний угол разориентации составляет 5 – 100) очень сильно влияет на прочность и продольный модуль упругости. Например, вытяжка в процессе графитизации волокон, то есть повышение степени ориентации фибрилл вдоль продольной оси, способна повысить модуль упругости волокна в 10 раз с 70 до 700 ГПа. Это вызвано тем, что плоские углеродные кристаллы располагаются вдоль фибрилл, и в этом направлении действуют сильные валентные связи, а между собой фибриллы соединены относительно слабо. Поэтому необходимо в процессе изготовления волокон контролировать возникновение таких дефектов как разориентация фибрилл, нарушения структуры углеродных кристаллитов, что возможно, например, методами рентгеновской диагностики или растровой электронной микроскопии.
Борное волокно изготавливается осаждением из газовой фазы на вольфрамовую нить, при этом образуется борид вольфрама на границе раздела «нить-волокно» (вольфрам-бор), появляются кольцевые и радиальные трещины, что вызывает дробление волокон при растяжении. С ростом температуры процесса происходит рост кристаллов бора, что также может резко снизить их прочность.
Органические волокна (арамидные типа «Кевлар», полиэтиленовые и др.) имеют низкую прочность при сжатии и изгибе, в процессе такого нагружения происходит внутренняя потеря устойчивости полимерных цепочек, из которых состоят волокна, поэтому в деталях, испытывающих сжимающие нагрузки, используют гибридные композиции органических и углеродных волокон. Технологии должны минимизировать наличие в волокнах таких дефектов, как скручивание, изгиб полимерных цепочек, обеспечивая равномерную структуру волокна.
2.2. Дефекты в матрицах. Разные типы матриц: полимерные, металлические, углеродные, керамические, стеклянные - обладают различными характерными дефектами, возникающими как в процессе изготовления изделия, так и при его эксплуатации.
В металлических матрицах основные дефекты связаны с примесями, осажденными интерметаллидными фазами, нарушением кристаллической структуры, пластическими деформациями вокруг армирующих элементов из-за концентрации напряжений при нагружении и с остаточными напряжениями, возникающими в процессе отверждения композита.
В полимерных матрицах возможны дефекты из-за неравномерного содержания компонентов: отвердителя, пластификатора, стабилизатора, красителя и др. Возможно также неполное удаление пузырьков газа, выделяемого при химических реакциях полимеризации, для их устранения необходимо предусмотреть повышение давления в процессе изготовления изделия на стадии желатинизации, отверждения смолы, при выделении газообразной фазы.
Углеродные матрицы, получаемые из полимерных путем высокотемпературной карбонизации, обладают многочисленными порами, которые в дальнейшем, на стадии формования готового изделия, заполняются пироуглеродом из газовой фазы.
2.3. Поверхности раздела «волокно-матрица» в полимерных и металлических композитах - это один из главных источников дефектов, снижающих прочность (особенно – длительную и усталостную). В композитах с полимерной матрицей основные дефекты на границах раздела - расщепления, непроклеи, образование промежуточных соединений, переходных слоев. Около поверхностей раздела в композитах с металлической матрицей возникают: интерметаллидные включения, дополнительная осажденная фаза, микропластичность из-за концентрации напряжений вблизи армирующих элементов. Все эти дефекты служат зародышами для трещин, постепенно развивающимися при циклическом или длительном нагружении, что приводит к снижению долговечности изделия.