Материал для изготовления корпусных деталей – серый чугун марки СЧ15.
Размеры основных элементов чугунного литого корпуса и крышки (цилиндрического редуктора).
Толщина стенки корпуса:
= 0,025
+ 1
8
= 0,025·90 + 1
= 3,25
8
Примем толщину стенки корпуса 8 мм
Толщина стенки крышки:
1 = 0,02·90 + 1
8
Примем толщину стенки крышки 8 мм
Толщина верхнего фланца корпуса и нижнего фланца крышки:
b = b1 = 1,5
b1 = 1,5·8 = 12 мм
Толщина нижнего фланца корпуса:
p = 2,35·
p = 2,35·8 = 19 мм
Толщина ребер жесткости:
m = (0,85…1,0)
m = 1·
m = 8 мм
Диаметр фундаментальных болтов:
d1 = 0,03 +12
Изм. |
Лист |
№ докум. |
Подпись |
Дата |
Лист |
КР.ПМ.12.ВКМ.03.5.86.СБ |
d1 = 0,03·90 + 12
d1 = 14,7 мм
Принимаем 4 болта М16
Ширина опорной поверхности:
А = 2,4· d1 + 1,5·
А = 2,4·16 + 1,5·8
А = 38,4 + 12 = 50,4 мм
А = 51 мм
D отверстия под фундаментальный болт:
d01 = d1 + 1 = 16 + 1 = 17 мм
Высота:
h = 0,5· = 0,5·8 = 4 мм
Диаметр болтов, крепящих крышку к корпусу:
d2 0,7· d1
d2 0,7·16 = 11,2 мм
Принимаем болты М12
Диаметр болтов (винтов), крепящих смотровую крышку:
d3 0,3·d1 = 0,3·16 = 4,8 мм
Принимаем болты (винты) М6
Диаметр штифта:
dш 0,5·16 = 8 мм
Длина штифта:
lш = b + b1 + 5 = 12 + 12 + 5 = 29 мм
Принимаем штифт 8h10 30 ГОСТ 3129-70 – 2 шт
Изм. |
Лист |
№ докум. |
Подпись |
Дата |
Лист |
КР.ПМ.12.ВКМ.03.5.86.СБ |
Изм. |
Лист |
№ докум. |
Подпись |
Дата |
Лист |
КР.ПМ.12.ВКМ.03.5.86.СБ |
К1 = 43 мм
Расстояние от края фланца до оси болта:
С1 = 19 мм
Ширина верхнего фланца корпуса:
К2 = 32 мм
Расстояние от края:
С2 = 14 мм
Рис. 5.1Размеры основных элементов корпуса и крышки
6.
Изм. |
Лист |
№ докум. |
Подпись |
Дата |
Лист |
КР.ПМ.12.ВКМ.03.5.86.СБ |
|
6.1 Ведомый вал
6.1.1 Шпонка на выходном участке вала:
по диаметру выходного участка вала d2 = 19 и его длине l2 = 28 мм выбираем основные размеры шпонки и шпоночных пазов:
b = 6 мм
h = 6 мм
t1 = 3,5 мм
t2 = 3,3 мм
l = l2 – (4…10) = 18 мм
Предварительно подобрана шпонка:
6 6
18 ГОСТ 23360 – 78
Проверяем подобранную шпонку по напряжениям смятия:
=
[
], (6.1)
=
– b = 28 – 6 = 22
рабочая длина шпонки;
z = 1;
допускаемое напряжение смятия [ ] = 110 МПа;
=
= 66,76 МПа
66,76 МПа 110 МПа
Прочность шпонок обеспечена
6.1.2 Шпонка под колесом
По диаметру вала под колесом и длине ступицы выбираем геометрические размеры шпонки и шпоночных пазов ( = 30 мм)
Изм. |
Лист |
№ докум. |
Подпись |
Дата |
Лист |
КР.ПМ.12.ВКМ.03.5.86.СБ |
h = 8 мм
t1 = 5 мм
t2 = 3,3 мм
lш = l2 - (4…10) = 36 мм
Предварительно выбираем шпонку 10 8
36 ГОСТ 23360-78
=
=
= 35,24 МПа (6.2)
35,24 МПа 110 МПа
Прочность шпонки обеспечена
6.2 Ведущий вал
6.2.1 Шпонка на выходном конце
По диаметру выходного конца вала d1 = 13 мм и его длине l1 = 28 мм выбираем основные размеры шпонки и шпоночных пазов:
b = 5 мм
h = 5 мм
t1 = 3 мм
t2 = 2,3 мм
lш = l1 – (4…10) = 22 мм
Предварительно подобрана шпонка: 5 x 5 x 22 x ГОСТ 23360 – 78
Проверяем подобранную шпонку по напряжению смятия:
=
[
], (6.3)
Рабочая длина шпонки: = l – b = 28 – 5 = 23 мм;
z = 1;
допускаемое напряжение смятия [ ] = 110 МПа;
Изм. |
Лист |
№ докум. |
Подпись |
Дата |
Лист |
КР.ПМ.12.ВКМ.03.5.86.СБ |



Прочность шпонок обеспечена
6.2.2 Шпонка под шестерней
По диаметру ведущего вала под шестерней = 25 мм и длине lст = 36 мм
Выбираем основные размеры шпонок и шпоночных пазов:
|
b = 8 мм
h = 7 мм
t1 = 4 мм
t2 = 3,3 мм
lш = b1 – (4…10) = 32 мм
Предварительно подобрана шпонка 8 х 7 х 32 ГОСТ 3129 – 70
Проверяем подобранную шпонку по напряжению смятия:
=
[
], (6.4)
Рабочая длина шпонки: lp = l – b = 36 – 8 = 28 мм;
z = 1;
Допускаемое напряжение смятия [ ] = 110 МПа;
=
= 11
110
Прочность шпонок обеспечена
7.
Изм. |
Лист |
№ докум. |
Подпись |
Дата |
Лист |
КР.ПМ.12.ВКМ.03.5.86.СБ |
7.1 Ведомый вал
Предварительно был подобран подшипник 205 с динамической грузоподъемностью С табл = 11 кН
Определяем радиальную нагрузку на подшипнике:
R = =
= 284,5 Н (7.1)
Определяем эквивалентную нагрузку:
Q = VRKбKт (7.2)
V = 1 – динамический коэффициент
Kб = 1,6 – коэффициент безопасности
Kт = 1 – температурный коэффициент
Q = 1·284,5·1,6·1 = 455,2
Определяем динамическую нагрузку:
= Q·
С
табл (7.3)
С = 455,2·
= 455,2·2,7 = 1228 Н = 1,228 кН
1,228 кН 11 кН
Предварительно подобранный подшипник подходит
7.2.Ведущий вал
Предварительно был подобран подшипник 204 с динамической грузоподъемностью С табл = 10 кН
Проверяем по динамической грузоподъемности:
Сr = Q (7.4)
Изм. |
Лист |
№ докум. |
Подпись |
Дата |
Лист |
КР.ПМ.12.ВКМ.03.5.86.СБ |
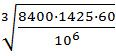

Предварительно подобранный подшипник подходит.
8.
Изм. |
Лист |
№ докум. |
Подпись |
Дата |
Лист |
КР.ПМ.12.ВКМ.03.5.86.СБ |
8.1. Ведомый вал. Расчетная схема ведомого вала:
RA = Rb = R = 284,5
Mu max = RA· (8.1)
l – расстояние между точками приложения реакции подшипника
l = b1 + 2x + B = 28 + 20 + 16 = 77 мм
x = 10 мм, В = 16 мм
|
Mumax = 284,5· = 10953 Н·мм
8.1.1 Определяем основные характеристики циклов изменений напряжений. Нормальное напряжение изменяется по симметричному циклу, тогда постоянное напряжение цикла = 0, а амплитуда цикла:
=
, (8.2)
= 3767,8
Опасное сечение находится в точке приложения силы Fm. Концентратором напряжения в этом сечении является шпоночный паз, тогда b = 10, t1 = 5
=
-
(8.3)
=
-
= 2128,5
=
= 5,14 МПа
Касательные напряжения изменяются по пульсирующему циклу, тогда основные характеристики цикла (амплитуду и среднее значение цикла) определяем по формуле:
=
=
, (8.4)
где Т = Т2 = 34884;
W нетто – полярный момент сопротивления:
W нетто =
-
(8.5)
W нетто =
-
= 4778 мм3
=
=
= 3,65 МПа (8.6)
= 335 МПа - предел выносливости материала
Предел выносливости материала по касательным напряжениям:
= 0,58
(8.7)
= 0,58
335 = 194,3
Изм. |
Лист |
№ докум. |
Подпись |
Дата |
Лист |
КР.ПМ.12.ВКМ.03.5.86.СБ |
=
80 + 1,9 = 2 Н/мм2 (8.8)
=
80 + 1,7 = 1,84 Н/мм2 (8.9)
Определяем коэффициенты, учитывающие масштабный фактор:
=
= 0,865
0,87 (8.10)
=
= 0,75 (8.11)
= 0,1 – коэффициент, учитывающий влияние постоянной составляющей цикла
Определяем коэффициент запаса выносливости по нормальным напряжениям:
=
=
= 28,2 (8.12)
=
=
= 9,32 (8.13)
Изм. |
Лист |
№ докум. |
Подпись |
Дата |
Лист |
КР.ПМ.12.ВКМ.03.5.86.СБ |
=
(8.14)
=
= 27,6
[n] = 2…5
n = 27,6 [5]
Прочность вала обеспечена
8.2 Ведущий вал. Расчетная схема ведущего вала.
Изгибающий момент, Н·мм:
Mu max = RA· , (8.2)
где RA = Rb = R = 284,5;
х = 10;
В = 15;
l = b1 + 2x+ B
l = 41 + 2·10 + 15 = 76
Mu max = 284,5 · = 10811 Н·мм (8.3)
8.2.1 Определяем основные характеристики циклов изменений напряжений. Нормальное напряжение изменяется по симметричному циклу, тогда постоянное напряжение цикла = 0, а амплитуда цикла:
=
,
Наиболее нагруженное сечение под шестерней, тогда b = 6, t1 = 3
=
-
=
-
= 1359
Изм. |
Лист |
№ докум. |
Подпись |
Дата |
Лист |
КР.ПМ.12.ВКМ.03.5.86.СБ |
=
= 7,95
Касательные напряжения изменяются по пульсирующему циклу, тогда основные характеристики цикла: амплитуда и среднее значение напряжения цикла.
=
,
где Т = Т1 = 11628 Н·мм
- полярный момент сопротивления;
=
-
=
-
= 2892,2
=
=
= 2
Предел выносливости материала - = 335 МПа
Предел выносливости материала по касательным напряжениям:
= 0,58
335 = 194,3
Эффективные коэффициенты концентрации напряжений, Н/мм2
= 2
= 1,84
Коэффициенты, учитывающие масштабный фактор
= 0,88
= 0,77
= 0,1 – коэффициент, учитывающий влияние постоянного цикла
Определяем коэффициент запаса выносливости по нормальным напряжениям:
=
=
= 18,5
=
=
= 39
Общий коэффициент запаса выносливости:
Изм. |
Лист |
№ докум. |
Подпись |
Дата |
Лист |
КР.ПМ.12.ВКМ.03.5.86.СБ |
n =
[n],
n = = 59,1
5
Прочность вала обеспечена.
9.
Изм. |
Лист |
№ докум. |
Подпись |
Дата |
Лист |
КР.ПМ.12.ВКМ.03.5.86.СБ |
9.1 Выбираем по действующим контактным напряжениям и окружной скорости сорт масла:
И-Г-А-46 ГОСТ 17479,4-87
9.2 Объем заливаемого в редуктор масла, (л):
= LMh
10-6
L – расстояние между стенками корпуса редуктора по оси валов;
L = +2x,
= 41 мм – ширина шестерни;
х = 10 мм – осевой зазор;
L = 41 + 2·10 = 61;
М – расстояние между стенками корпуса редуктора перпендикулярно оси валов;
М = аw ф + + 2x = 90 +
= 183
h = hм+ У
hм 3m
10;
У = 4х
h = 3 1,5 + 4
10 = 44,5 мм
принимаем h = 45 мм
= 75·275
52
10-6 = 1,073
1,1 л
10.
Изм. |
Лист |
№ докум. |
Подпись |
Дата |
Лист |
КР.ПМ.12.ВКМ.03.5.86.СБ |
10.1 Ведомый вал. Муфта между редуктором и исполнительным механизмом
Подбираем муфту по расчетному крутящему моменту:
Тр2 = Т2Кр,
где Кр = 1,5 – коэффициент режима работы
Тр2 = 34884·1,5 = 52326
Выбираем по расчетному крутящему моменту основные размеры муфты и ее элементов:
D0 = 68; dn = 10; ln = 19; d1 = М8;
z = 6; db = 19; lb = 15; d0 = 20.
Проверка деталей на прочность по напряжению изгиба:
=
[
],
=
80
Проверяем втулки муфты на смятие:
=
]
=
2
Выбранная муфта подходит.
10.2 Ведущий вал. Муфта между электродвигателем и редуктором
Подбираем муфту по расчетному крутящему моменту:
Тр1 = Т1Кр,
где Кр = 1,5 – коэффициент режима работы
Тр1 = 11628·1,5 = 17442
Выбираем по расчетному крутящему моменту основные размеры муфты и ее
Изм. |
Лист |
№ докум. |
Подпись |
Дата |
Лист |
КР.ПМ.12.ВКМ.03.5.86.СБ |
D0 = 58; dn = 10; ln = 19; d1 = М8;
z = 4; db = 19; lb = 15; d0 = 20.
Проверка деталей на прочность по напряжению изгиба:
=
[
],
=
80
Проверяем втулки муфты на смятие:
=
]
=
2
Прочность элементов муфты обеспечена.