Оценка пожарной опасности технологического процесса цеха производства полиэтилена методом низкого давления.
Студент группы ПБ-419
Алёшин А.В
Руководитель проекта
Мухамеджанова Е.Я.
ОГЛАВЛЕНИЕ
Введение …………………………………………………………………… | |
1. Краткое описание технологического процесса…………………………. | - |
2. Анализ пожаровзрывоопасных веществ ………………………………... | - |
3. Оценка пожароопасной среды аппарата при их нормальной работе….. | - |
4. Пожаровзрывоопасность аппарата при эксплуатации которого возможен выход горючки наружу, без повреждения конструкции……………….. | - |
5. Анализ возможных причин повреждения аппаратов и разработка необходимых средств защиты ……………………………………………………... | - |
6. Анализ возможности появления характерного технологического источника зажигания ……………………………………………………………... | - |
7. Возможные пути распространения пожара ……………………………… | - |
8. Расчёт категории производственного помещения на взрывопожарную опасность ……………………………………………………………………….. | - |
9. Противопожарная профилактика, мероприятия. Вопросы экологии ….. | - |
![]() |
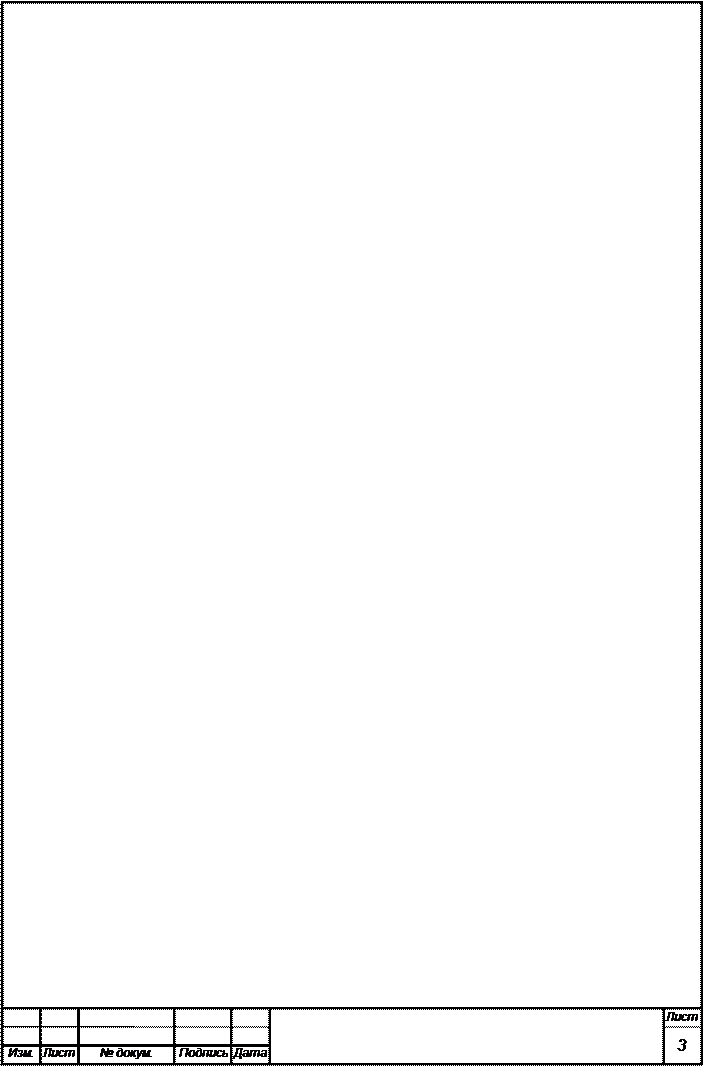
В самом начале работы сразу же хочется выделить основную цель нашего курсового проекта, суть которой сводится к оценки пожарной опасности на предприятии технологического производства полиэтилена методом низкого давления. Это делается для профилактики пожаров и пожароопасных ситуаций при производстве, недопущение жертв среди людей и потери материальных ценностей, снижение угроз, последтвий пожара и т.п.
Распространение синтетических материалов в промышленности и в быту обусловливается их ценными свойствами: высокой механической прочностью, эластичностью, сопротивляемостью истиранию, большой химической стойкостью против кислот, щелочей и других химических соединений, неэлектропроводностью, прозрачностью, легкой окрашиваемостью, простотой изготовления изделий и их обработки. Однако почти все синтетические смолы и волокна являются горючими материалами, не обладающими высокой термической стойкостью. При воздействии тепла многие пластмассы и синтетические волокна плавятся и разлагаются, выделяя огнеопасные и токсичные пары и газы.
|
Процессы производства пластических масс и химических волокон многостадийны, сложны и почти все пожаро- и взрывоопасны. Это объясняется тем, что сырьем и вспомогательными веществами при производстве пластмасс и волокон являются огнеопасные газы — этилен, ацетилен, пропилен, формальдегид и др.; жидкости—сероуглерод, ацетон, бензол, бензин, циклогексан, метиловый спирт и др. и твердые вещества — целлюлоза, капролактам, диметилтерефталат, нитрил акриловой кислоты, соль АГ и др. Для химических реакций используют катализаторы и инициаторы, представляющие собой взрывоопасные, воспламеняющиеся на воздухе вещества (металлоорганические катализаторы) или сильные окислители, способные разлагаться со взрывом и вызывать воспламенение других веществ (порофоры, перекиси). В процессе переработки сырье претерпевает многообразные превращения и видоизменения, образуя промежуточные соединения, представляющие собой в большинстве случаев также взрывоопасные газы и легковоспламеняющиеся жидкости. Высокая температура процесса вызывает необходимость использования специальных теплоносителей, которые являются также горючими жидкостями. Высокотемпературные органические теплоносители (ВОТ), находясь в рубашках и змеевиках аппаратов, увеличивают общее количество горючих веществ в цехе, а часто и сами являются причиной пожаров и взрывов.
|
Наличие в цехах значительного количества горючих веществ, разветвленной сети трубопроводов с жидкостями и газами, технологических проемов в строительных конструкциях, сложных систем пневматической транспортировки порошковой продукции и вентиляционных устройств создает благоприятные условия для развития начавшегося пожара.
Пожар по своей химической сущности представляет процесс горения. При горении происходит окисление вещества, чаще всего кислородом воздуха. Чтобы пожар возник и стал распространяться, необходимы определенные условия: наличие горючего вещества и его взаимоконтакт с воздухом (в некоторых случаях окислительно-восстановительные процессы протекают и без кислорода воздуха), а также их взаимоконтакт с источником тепла, способного нагреть горючее вещество до температуры самовоспламенения. Начавшийся пожар может развиваться и причинять значительный ущерб в том случае, если имеются пути для его распространения (скопление твердых горючих веществ, разлив жидкостей, сгораемые строительные конструкции, незащищенные проемы в противопожарных стенах и перекрытиях, отсутствие преград на производственных коммуникациях, воздуховодах и т. д.). Эти закономерности возникновения и развития пожара должны быть положены в основу предупреждения и тушения пожаров.
|
Таким образом, оценивая пожарную опасность технологического процесса производства пластмасс и химических волокон, в каждом отдельном случае устанавливают, при каких условиях в аппаратах, производственных помещениях или на открытых площадках может образоваться горючая среда, по каким причинам появляются источники воспламенения и каковы пути вероятного распространения пожара. На основе этого определяют категорию пожарной опасности и разрабатывают комплекс защитных мероприятий.
1. Краткое описание технологического процесса
Производство полиэтилена методом низкого давления
Технологическая схема производства полиэтилена низкого давления состоит из четырех основных стадий: синтеза металлоорганического катализатора и приготовления рабочего раствора катализатора; полимеризации этилена; отмывки полиэтилена от катализатора; сушки полиэтилена.
Синтез металлоорганического катализатора
Вкачестве основной части катализатора используется триэтилалюминий — А1(С2Н5)3 или диэтилалюминийхлорид — А1(С2Н5)2С1. Другой составной частью является четыреххлористый титан — TiCl4. Готовый катализатор представляет собой раствор указанных веществ в бензине или смеси бензина с циклогексаном.
Применение триэтилалюминия обеспечивает получение жесткого полимера с большим молекулярным весом. При использовании диэтилалюминийхлорида получается более эластичный полимер с меньшим молекулярным весом. Такой полимер легко подвергается переработке и успешно применяется при производстве кабелей и в других отраслях промышленности. Поэтому для полимеризации этилена иногда применяют диэтилалюминийхлорид. Оба катализатора получаются на одном и том же оборудовании без изменения технологической схемы в две стадии. На первой стадии получают промежуточный продукт — сесквигалоид—при взаимодействии алюминия с хлористым этилом (или бромистым этилом), на второй — триэтилалюминий (диэтилалюминийхлорид), действием на сесквигалоид металлическим натрием (реакция симметризации).
При уменьшении количества металлического натрия, расходуемого на реакцию взаимодействия с сесквигалоидом, а также уменьшении скорости его подачи в зону реакции в качестве конечного продукта будет получаться диэтилалюминийхлорид по уравнению
2А12 (С2Н5) Х3 + 3Na ЗА1 (С2Н6)2 X + 3NaX + А1.
технологическая схема синтеза алюминийорганического катализатора.
В реактор сесквигалоида заливается бензин из мерника(50% полезного объема реактора), затем из бункера подается порошкообразный алюминий. Загружают реактор при работающей мешалке. Смесь подогревается до 40—50°С веретенным маслом, циркулирующим в рубашке аппарата, после чего в него заливается из мерникарасчетное количество бромистого этила для активации алюминия. Процесс активации проводится при температуре 40—60°С и давлении 0,3 атм. Для поддержания рабочей температуры реактор охлаждается, так как активация сопровождается выделением тепла. По окончании процесса смесь нагревается до 100—120°С, затем в реактор из мерникаподается хлористый этил. Подачей хлористого этила регулируется давление в реакторе в пределах 3—4 атм. В этих условиях образуется сесквигалоид по приведенной выше реакции. Раствор сесквигалоида га бензине охлаждается и подается к реактор для получения триэтилалюминия или диэтилалюминийхлорида. После подогрева раствора до 130—135°С в него подается расплавленный металлический натрий из мерника. Натрий передавливается маслом, которое закачивают из мерникадозировочным насосом. При подаче натрия в количестве 6% к весу чистого сесквигалоида в качестве готового продукта получают триэтилалюминий, при подаче натрия до 28% получают диэтилалюминийхлорид. Реакция взаимодействия натрия с сесквигалоидом проходит при 130—140°С и давлении 3—4 атм. Реактор симметризации охлаждается, так как реакция сопровождается выделением тепла. В реакторе образуется алюминийорганический катализатор и твердый остаток, называемый шламом, содержащий NaCl, NaBr, NaAl. После завершения реакции симметризации содержимое реактора выдерживается в течение 3 ч (процесс дозревания). Смесь охлаждается до 24°С и подается в отстойникдля отделения раствора от шлама. Осветленный раствор фильтруется на керамическом фильтре и поступает в смесительдля разбавления до 5%-ной концентрации. Шлам промывается бензином или циклогексаном и поступает из отстойника в реакторна обезвреживание метиловым спиртом, подаваемым из мерника. Реактор охлаждается водой для поддержания температуры в пределах 50—60°С, так как обработка шлама метанолом сопровождается выделением тепла. После завершения процесса обезвреживания шлама производится отгонка избыточного мета нола путем подогрева реактора паром. Пары метанола проходят через конденсатор-холодильники жидкость, через сепаратор поступает в сборник. Сухой шлам охлаждается, выгружается при помощи шнекав мешки и отвозится в отвал.
Полимеризация этилена
Полимеризация этилена при низком давлении, как было сказано выше, осуществляется в среде жидких углеводородов, способных растворять триэтилалюминий или диэтилалюминийхлорид и четыреххлористый титан. В качестве растворителей катализатора используют смесь бензина и циклогексана в соотношении примерно 2,5:1 (по объему). Чтобы реакция полимеризации шла с приемлемой скоростью, т. е. была в достаточной степени управляема, а полученный полимер имел требуемый молекулярный вес, — концентрация катализатора и сокатализатора в растворителе должна быть в пределах 0,2—0,3%, давление 2,5—3 атм и температура 75—85°С.
Для получения высокого качества полимера этилен не должен содержать примесей кислорода, сернистых соединений и других веществ. Такой этилен получают низкотемпературной ректификацией с последующим процессом селективного гидрирования.
Контакт этилена с раствором катализатора происходит в полимеризаторах (реакторах) периодического или непрерывного действия. Полиэтилен образуется по реакции
n(С2Н4) (-СН 2-СН2-)n+Q
Выделяющееся при реакции тепло отводится в реакторах малого объема (до 3 м3) водой, подаваемой в рубашку, а в аппаратах большого объема (20—25 м3) — за счет охлаждения циркулирующего этилена и испарения при этом части растворителя.
Технологическая схема процесса полимеризации этилена:
Из цеха катализаторов в мерники подается 5%-ный раствор диэтилалюминийхлорида и четыреххлористого титана. Отмеренное количество катализаторов самотеком поступает в смеситель-разбавитель, где катализаторы перемешиваются и при работающей мешалке разбавляются бензином и циклогексаном до концентрации 0,2%. Аппарат имеет рубашку для обогрева раствора до 50°С. Сформированный катализаторный комплекс насосом,закачивается в полимеризатор и поддерживается в нем на определенном постоянном уровне. Этилен подают в нижнюю часть полимеризатора по трубам. Поступая в аппарат через систему эрлифта, этилен обеспечивает перемешивание реакционной массы, отводит тепло полимеризации и частично полимеризуется в полиэтилен. Не вступивший в реакцию этилен, нагретый и насыщенный парами растворителя, отводится из верхней части полимеризатора в циркуляционную систему.
Циркуляция этилена осуществляется следующим образом. Этилен при температуре 80°С проходит последовательно циклонные отделители, в которых улавливаются брызги растворителя и частички полиэтилена. Далее этилен проходит конденсатор-холодильник. В холодильнике этилен и пары растворителя охлаждаются водой до 40°С. При этом часть паров конденсируется и полученная смесь поступает на разделение в аппарат. Этилен, охлажденный и частично очищенный от растворителя, поступаетснова в полимеризатор, смешиваясь по пути со свежим этиленом. Таким образом, температура полимеризации поддерживается изменением количества и температуры циркулирующего этилена.
Растворитель, содержащий полиэтилен, из отделителей при помощи насоса возвращается в полимеризатор вместе с циркулирующим этиленом (по линиям ). Кроме того, осуществляется непрерывная циркуляция смеси в самих отделителях.
Образующийся полимер в виде суспензии (смеси) полиэтилена в растворителе (соотношение 1: 10) отводится из полимеризатора в сборник. В сборнике происходит выделение растворенного этилена, так как давление в нем (0,1 атм). ниже, чем в полимеризаторе, а температура 70°С. Выделившийся этилен для улавливания паров растворителя проходит холодильник, сепаратори поступает па очистку или на факел. Суспензия полиэтилена из сборниканасосомподается в сборник, из которого насосомподается на дальнейшую обработку.