Показатель | Диаметр детали | |||||
10-20 | 30-40 | 50-60 | 70-80 | 90-100 | 200-300 | |
Толщина наплавляемого слоя, мм | 0,5-0,8 | 1,0-1,2 | 1,4-1,6 | 2,0-2,5 | 0,8-1,0 | 0,8-1,0 |
Диаметр электрода, мм | 0,8 | 1,2 | 1,6 | 2,5 | 1,0 | 1,2 |
Сила тока, А | 70-90 | 90-150 | 140-200 | 280-450 | 100-300 | 150-190 |
Напряжение, В | 16-18 | 19-23 | 24-28 | 38-30 | 18-19 | 19-21 |
Скорость наплавки, м/ч | 40-45 | 35-40 | 30-20 | 11-20 | 70-80 | 20-30 |
Смещение электрода, мм | 2-4 | 5-8 | 7-12 | 9-15 | 8-10 | 18-20 |
Шаг наплавки, мм | 2,5-3,0 | 3,0-3,5 | 4,0-6,0 | 5,0-7,0 | 2,8-3,2 | 3,0-3,5 |
Вылет электрода, мм | 7-10 | 10-12 | 12-20 | 22-27 | 10-12 | 10-13 |
Расход углекислого газа, л/мин | 6-8 | 6-8 | 8-10 | 12-15 | 6-8 | 8-9 |
Наплавку в среде углекислого газа производят на постоянном токе обратной полярности. Тип и марку электрода выбирают в зависимости от материала восстанавливаемой детали и требуемых физико-механических свойств наплавленного металла. Скорость подачи проволоки зависит от силы тока, устанавливаемой с таким расчетом, чтобы в процессе наплавки не было коротких замыканий и обрывов дуги. Скорость наплавки зависит от толщины наплавляемого металла и качества формирования наплавленного слоя. Наплавку валиков осуществляют с шагом 2,5-3,5 мм. Каждый последующий валик должен перекрывать предыдущий не менее чем на 1/3 его ширины.
Твердость наплавленного металла в зависимости от марки и типа электродной проволоки составляет 200-300 НВ.
Расход углекислого газа зависит от диаметра электродной проволоки. На расход газа оказывают также влияние скорость наплавки, конфигурация изделия и наличие движения воздуха.
Механизированную сварку и наплавку в углекислом газе применяют при ремонте кабин, кузовов и других деталей, изготовленных из листовой стали небольшой толщины, а также для устранения дефектов резьбы, осей, зубьев, пальцев, шеек валов и т. д.
|
Добавление к аргону 10-12 % углекислого газа и 2-3 % кислорода способствует повышению устойчивости горения дуги и улучшению формирования наплавленного металла. Благодаря защите дуги струями аргона (внутренняя) и углекислого газа (наружная) в 3-4 раза сокращается расход аргона при сохранении качества защиты дуги.
К преимуществам способа относятся: – высокая производительность процесса (в 3-4 раза выше, чем при газовой сварке); высокая механическая прочность сварного шва; небольшая зона термического влияния; снижение потерь энергии дуги на световое излучение, так как аргон задерживает ультрафиолетовые лучи, а к недостаткам – высокая стоимость процесса (в 3 раза выше, чем при газовой сварке) и использование аргона.
Режим сварки определяется двумя основными параметрами: силой тока и диаметром электрода. Сила сварочного тока выбирается исходя из толщины стенки свариваемой детали (чем тоньше стенка, тем меньше сила сварочного тока) и составляет 100-500 А. Диаметр вольфрамового электрода 4-10 мм.
Устойчивость процесса наплавки и хорошее формирование наплавленного металла позволяют вести процесс на высоких скоростях – до 150 м/ч
и выше.
Для наплавки в среде защитных газов применяют специальные автоматы и установки АГП-2, АДСП-2, УДАР-300, УДГ-501; полуавтоматы А-547Р, Л-537, ПШП-10, преобразователи ПСГ-350, ПСГ-500.
Вибродуговая наплавка. Этот способ наплавки является разновидностью дуговой наплавки металлическим электродом. Процесс наплавки осуществляется при вибрации электрода с подачей охлаждающей жидкости на наплавленную поверхность.
|
На рис. 5.9 дана принципиальная схема вибродуговой установки с электромеханическим вибратором. Деталь 3, подлежащую наплавке, устанавливают в патроне или в центрах токарного станка. На суппорте станка монтируют наплавочную головку, состоящую из механизма 5 подачи проволоки с кассетой 6, электромагнитного вибратора 7 с мундштуком 4. Вибратор создает колебания конца электрода с частотой 110 Гц и амплитудой колебания до 4 мм (практически 1,8-3,2 мм), обеспечивая размыкание и замыкание сварочной цепи. При периодическом замыкании электродной проволоки и детали происходит перенос металла с электрода на деталь. Вибрация электрода во время наплавки обеспечивает стабильность процесса за счет частых возбуждений дуговых разрядов и способствует подаче электродной проволоки небольшими порциями, что обеспечивает лучшее формирование наплавленных валиков.
Рис. 5.9. Схема установки для вибродуговой наплавки: 1 - насос; 2 - бак; 3 - деталь; 4 - мундштук; 5 - механизм подачи; 6 - кассета; 7 - вибратор; 8 - реостат; 9 - дроссель
Электроснабжение установки осуществляется от источника тока напряжением 24 В. Последовательно с ним включен дроссель 9 низкой частоты, который стабилизирует силу сварочного тока. Реостат 8 служит для регулировки силы тока в цепи. В зону наплавки при помощи насоса 1 из бака 2 подается охлаждающая жидкость (4-6%-й раствор кальцинированной соды в воде), которая защищает металл от окисления.
К преимуществам способа относятся: небольшой нагрев деталей; малая зона термического влияния; высокая производительность процесса; возможность получения наплавленного слоя без пор и трещин; минимальная деформация детали, которая не превышает полей допусков посадочных мест. К недостаткам способа относят снижение усталостной прочности деталей после наплавки на 30-40 %.
|
Качество соединения наплавленного металла с основным зависит от полярности тока, шага наплавки (подача суппорта станка на один оборот детали), угла подвода электрода к детали, качества очистки и подготовки поверхности, подлежащей наплавлению, толщины слоя наплавки и др.
Высокое качество наплавки получают при токе обратной полярности («+» на электроде, «–» на детали), шаге наплавки 2,3-2,8 мм/об и угле подвода проволоки к детали 15-30°. Скорость подачи электродной проволоки не должна превышать 1,65 м/мин, а скорость наплавки – 0,5-0,65 м/мин.
Наибольшая скорость наплавки
V н = (0,4–0,7) V пр, (5.1)
где V np – скорость подачи электродной проволоки, м/мин.
V пр = nsDh / (250 d 2h), (5.2)
где п – частота вращения детали, мин-1; s – шаг наплавки, мм/об; D – диаметр детали, мм; h – толщина наплавляемого слоя, мм; d – диаметр электродной проволоки, мм; h – коэффициент наплавки (h = 0,85-0,90).
Надежное сплавление обеспечивается при толщине наплавленного слоя, равной 2,5 мм.
Структура и твердость наплавленного слоя зависят от химического состава электродной проволоки и количества охлаждающей жидкости.
Индукционная наплавка (ИН) - процесс наплавки на основе преобразования в индукторе энергии высокочастотного электромагнитного поля в тепловую. Применяют следующие способы наплавки: порошкообразной шихтой, монолитным или брикетированным присадочным материалом, в огнеупорной среде, центробежный и жидким расплавом.
Наплавка порошкообразной шихтой. При наплавке порошкообразной шихтой (рис. 5.10) в качестве присадочного материала используют порошкообразную шихту, которая состоит из гранулированного сплава и флюсов на основе буры. Приготовленную шихту наносят равномерным слоем на поверхность наплавляемого изделия. Затем изделие с нанесенным слоем шихты вводят в индуктор ТВЧ, форма и размеры которого определяются конфигурацией упрочняемой поверхности. Питание индуктора осуществляется от ламповых высокочастотных установок с частотой 70 или 440 кГц.
После включения питания внутри индуктора возникает переменное электромагнитное поле. В электропроводящих телах, находящихся в электромагнитном поле, индуктируются токи. Происходит нагрев элементарных объемов материала и изделия в целом. Однако в данном случае наплавки шихта, расположенная между индуктором и нагреваемой (наплавляющей) поверхностью, в связи с большим сопротивлением металлического порошка незначительно реагирует на воздействие переменного электромагнитного поля. Наплавочная шихта является как бы «электропрозрачной» для возникающего в индукторе поля. Поэтому основное количество тепла будет выделяться в тонких поверхностных слоях основного металла, а присадочный материал (шихта) будет нагреваться главным образом в результате теплопередачи от наплавляемой поверхности. В этой связи температура плавления порошкообразного сплава, входящего в состав шихты, должна быть ниже температуры плавления основного (наплавляемого) металла. При этом скорость нагрева упрочняемой поверхности должна значительно превышать скорость отвода тепла в тело детали и потерь на излучение.
|

|

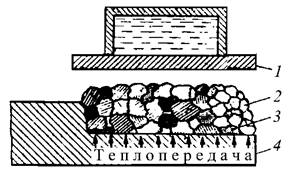
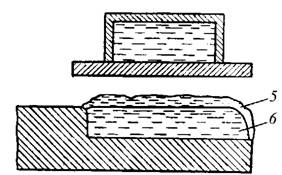
а б
Рис. 5.10. Схема способа индукционной наплавки порошкообразной шихтой: а – начало процесса; б – окончание процесса; 1 - индуктор ТВЧ, охватывающий деталь (нижняя его часть на рисунке не показана); 2 – частицы наплавляемого сплава; 3 – частицы флюса; 4 – деталь; 5 – слой жидкого флюса; 6 – жидкий присадочный сплав
|
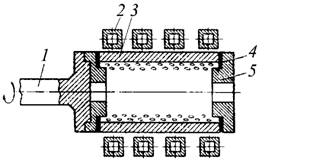
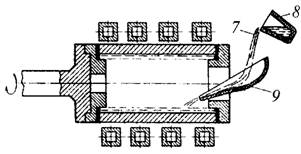
а б
Рис. 5.11. Принципиальная технологическая схема центробежной наплавки: а – присадочный металл в виде шихты; б – присадочный металл в виде расплава; 1 - шпиндель центробежной машины; 2 – индуктор ТВЧ; 3 – наплавляемая деталь; 4 – прокладки; 5 - крышка с отверстием; 6 – шихта; 7 – присадочный расплав; 8 – разливочный ковш; 9 - лоток из огнеупорного материала
После отключения питания индуктора ТВЧ происходит процесс кристаллизации наплавленного слоя сплава. Дальнейшая обработка заключается в удалении шлака и придании режущему (упрочненному) лезвию или всей детали окончательной формы известными методами – гибкой, заточкой и пр.
Рассмотренный вариант индукционной наплавки выгодно отличается от других известных тем, что возможна качественная наплавка не только механически обработанных поверхностей, но и покрытых слоем ржавчины или окалины. При наличии указанных видов загрязнений необходимо только незначительное увеличение количества флюса в шихте.
При наплавке порошкообразной шихтой используют флюсы, состоящие в основном из трех компонентов: буры, борного ангидрида и силикокальция. В практике индукционной наплавки используют флюсы двух типов: плавленые и в виде механической смеси различных компонентов. Плавленые флюсы получают в результате совместного предварительного плавления при температуре около 850 °С кристаллической буры, борной кислоты и силикокальция. Такие флюсы обозначают индексом П (плавленые) и цифрой, которая показывает массовое отношение количества борного ангидрида к буре. Например, у флюса марки П-1,5 отношение содержания борного ангидрида к буре равно 1,5.
Флюсы, представляющие собой механическую смесь буры, борного ангидрида и силикокальция, вводят непосредственно в наплавочную шихту в виде исходных компонентов (табл. 5.4). Однако такие флюсы имеют ряд существенных недостатков: компоненты флюса не подлежат длительному хранению; происходит значительное газовыделение в процессе наплавки; имеются токсичность борного ангидрида, а также гигроскопичность отдельных компонентов.
Таблица 5.4
Состав шихты для индукционной наплавки
Толщина слоя шихты, мм | Наплавочный материал - сормайт № 1, % | Компоненты флюса (механическая смесь), % | ||
Борный ангидрид | Бура | Силикокальций | ||
1,5 | ||||
3,0 | 7,5 | 2,5 | ||
4,5 |
В отличие от механических смесей плавленые флюсы практически не растворимы в воде. Это позволяет использовать наплавочные пасты с пластификаторами, содержащими воду. Токсичные в отдельности компоненты после сплавления образуют инертное при комнатной температуре соединение. При использовании флюсов группы П заметно улучшается формирование поверхности наплавленного сплава.
В качестве наплавочных материалов используют металлические порошки, а также монолитные и брикетированные материалы. В состав наплавочных материалов входят химические элементы, обеспечивающие требуемые свойства покрытия. Например, для износостойких покрытий это будут Cr, Ni, Mn, Cu, W, Fe, C, B, Si и др.
Известно, что металлические порошки практически не реагируют на действие переменного электромагнитного поля индуктора ТВЧ, а их нагрев осуществляется главным образом в результате теплопередачи от основного (наплавляемого) металла. В этой связи сплавы, которые используются для индукционной наплавки, должны отвечать некоторым дополнительным
требованиям:
температура плавления сплава должна быть ниже температуры плавления основного металла не менее чем на 100–150 °С;
наплавочный материал должен быть в виде порошка определенного гранулометрического состава;
сплав должен иметь минимальную магнитную проницаемость.
Износостойкость наплавленного сплава зависит от числа твердых составляющих в структуре сплава. В области восстановления и упрочнения деталей применяют два различных способа управления содержанием твердых составляющих в наплавке:
изменением химического состава сплава;
введением в шихту труднорастворимых примесей, образующих в результате взаимодействия с легкоплавкой связкой специфические композитные материалы – псевдосплавы.
Принципиальная технологическая схема индукционной наплавки центробежным способом приведена на рис. 5.11 и не требует пояснений, так как все основные положения рассмотрены выше.
Комплекс оборудования для индукционной наплавки включает:
генератор высокой частоты (машинный, ламповый, ионный, тиристорный);
индуктор тока высокой частоты (ТВЧ) одновитковый или многовитковый;
конденсаторную батарею, компенсирующую низкий коэффициент мощности индуктора;
закалочный трансформатор;
контактор для подключения и отключения тока нагрузки;
линии передач тока высокой частоты от источника питания до индуктора;
систему водяного охлаждения;
высокочастотные измерительные приборы (амперметр, вольтметр, ваттметр, фазометр);
измерительные трансформаторы напряжения и тока.
В зависимости от функционального назначения установки дополнительно укомплектовывают плавильной печью, станком для закалки, кузнечным нагревателем, аппаратурой для поддержания и контроля режима нагрева. В ряде случаев для нагрева используют промышленную частоту, и тогда генератор отсутствует. При питании однофазной нагрузкой вместо генератора устанавливают устройство, преобразующее трехфазную систему в однофазную, которое обеспечивает симметричную нагрузку сети. Нагреваемую деталь помещают внутри индуктора или около него. Переменное магнитное поле индуктора вызывает появление индуктированного тока в детали, в результате чего происходит ее нагрев.
Основными достоинствами способа ИН являются: высокая производительность; возможность механизации и автоматизации; малая глубина проплавления основного металла; возможность наплавки тонких слоев. Недостатки ИН: низкий КПД процесса; необходимость использования для наплавки только материалов с меньшей, чем у основного металла, температурой плавления, достаточно сложное оборудование, зависимость конструкции индуктора от формы наплавляемой детали, что делает нецелесообразным применение способа для мелкосерийного производства.
Лазерная наплавка (ЛН) - процесс наплавки, основанный на получении высококонцентрированной световой энергии в лазере и преобразовании ее в тепловую. Применяют три способа ЛН: оплавление предварительно нанесенных паст; оплавление напыленных слоев; наплавка с подачей присадочного порошка в зону оплавления. В установках для лазерной сварки и наплавки применяют генераторы с рубиновым квантовым генератором или с газовым генератором, в котором в качестве рабочего тела используют смесь углекислого газа, азота и гелия (рис. 5.12).
Рис. 5.12. Схема установки для лазерной сварки и наплавки с рубиновым генератором: 1 – наплавляемая деталь; 2 – сопло для подачи защитного газа аргона; 3 – фокусирующая линза; 4 – поворотное зеркало; 5 – полупрозрачное зеркало; 6 – лазерный луч; 7 – отражатель; 8 – намотка; 9 – рубиновый стержень; 10 – заднее зеркало; 11 – конденсаторная батарея; 12 – наносимый порошок
В этой установке рубиновый стержень облучается импульсной лампой, питаемой от конденсаторной батареи. Отражатель и заднее зеркало направляют лазерный луч на полупрозрачное зеркало и через поворотное зеркало и фокусирующую линзу на наплавляемую деталь. В зону наплавки вводят наплавляемый порошок. Для защиты расплавленного металла в зону наплавки подается аргон. Всероссийское научно-производственное объединение «Ремдеталь» разработало комплект оборудования для лазерной наплавки, включающий газовый лазер ЛГП-702 номинальной мощностью 800 Вт, установку для наплавки СКС-011-1-02 с оснасткой для лазерной обработки, приспособление для управления лазерным лучом и систему газообеспечения. Наплавляют самофлюсующиеся порошки-типа СНГН или ПГ-СР. Также разработана универсальная установка для использования лазеров мощностью
0,7-2,5 кВт. Лазерной наплавкой восстанавливают впускные и выпускные клапаны, распределительные валы, золотники гидрораспределителей и другие детали.
Достоинства способа: требуемые состав и свойства наплавленного металла можно получить уже в первом слое; малое проплавление основного металла при высокой прочности сцепления; небольшие деформации деталей в момент наплавки; возможность получения тонких наплавляемых слоев (< 0,3 мм); наплавка труднодоступных поверхностей и подвод излучения к нескольким рабочим местам. Недостатки: небольшая производительность (до 5 кг/ч), низкий КПД процесса, сложное и дорогое оборудование.
Газовая наплавка (ГН) - процесс, при котором металл нагревается и расплавляется пламенем газа, сжигаемого в смеси с кислородом в специальных горелках. В качестве горючего газа чаще всего применяется ацетилен, а также пропан-бутановая смесь, природный газ, водород и др. Наплавку ведут с присадкой прутков либо с вдуванием порошков в газовое пламя.
Достоинства способа: универсальность и гибкость технологии; малое проплавление основного металла, возможность наплавки слоев малой и большой толщины. Недостатки: невысокая производительность; нестабильность качества наплавки.
5.2.2. Механические способы наплавки (наварки)
Наплавка трением заключается в быстром вращении присадочного прутка (1500-4000 об/мин) с прижатием к наплавляемой поверхности, его нагреве и намазывании на поверхность изделия. Этот способ пока еще не нашел широкого применения. В то же время одним из вариантов этого способа является наплавка металлическими щетками (см. параграф 5.9), которая может найти широкое применение.
Плакирование с использованием взрыва - процесс образования покрытия путем приваривания листа к детали или другому листу с использованием энергии взрыва.
Достоинства: отсутствие проплавления основного металла; минимальные деформации при сварке; возможность образования покрытия из металла на другом металле, соединение которых другими способами затруднено или невозможно. Недостатки: необходимость повышенной предосторожности, требующая устройства специальных камер и полигонов; длительность подготовки; ограниченность номенклатуры деталей; невозможность нанесения покрытий на детали сложной формы.
5.2.3. Термомеханические способы наплавки
Электроконтактная наплавка - процесс соединения основного и присадочного металлов под воздействием пластической деформации и импульсов тока. В качестве присадочного материала используют стальную ленту, проволоки, порошки и их смеси. Толщина наплавленного слоя 0,2-1,5 мм, зона термического влияния не более 0,5 мм.
Достоинства: отсутствие проплавления основного металла; минимальное коробление; возможность наплавки малой толщины. Недостатки: небольшая производительность (не более 1,5 м2/ч); ограниченная номенклатура наплавляемых деталей.
Прочие термомеханические способы наплавки. Плакирование прокаткой и экструдированием на ремонтных предприятиях не применяется, поэтому здесь не рассматривается. Более подробно о всех способах наплавки см. [20, 29, 55, 74, 75, 82, 85, 93, 103, 105, 113, 118, 126, 143–145, 163, 169].
Способы напыления
Сущность и способы напыления. Напыление является одной из групп способов нанесения металлических покрытий на изношенные поверхности восстанавливаемых деталей. Сущность процесса состоит в напылении предварительно расплавленного металла на специально подготовленную поверхность детали струей сжатого газа (воздуха). Мелкие частицы расплавленного металла достигают поверхности детали в пластичном состоянии, имея большую скорость полета. При ударе о поверхность детали они деформируются и, внедряясь в ее поры и неровности, образуют покрытие.
Основными достоинствами напыления как способа нанесения покрытий при восстановлении деталей являются высокая производительность процесса, небольшой нагрев деталей (120-180 °С), высокая износостойкость покрытия, простота технологического процесса и применяемого оборудования, возможность нанесения покрытий из любых металлов и сплавов. К недостаткам процесса относят пониженную механическую прочность покрытия и сравнительно невысокую прочность сцепления его с поверхностью детали.
В зависимости от вида тепловой энергии, используемой в аппаратах для напыления при расплавлении металла, различают следующие способы напыления: газопламенное, электродуговое, детонационное и плазменное.
Газопламенное напыление. Осуществляется при помощи специальных аппаратов, в которых плавление напыляемого металла производится ацетилено-кислородным пламенем, а его распыление - струей сжатого воздуха (рис. 5.13). Проволока подается с постоянной скоростью роликами.
Рис. 5.13. Распылительная головка газопламенного металлизатора: 1 - смесительная камера; 2 - каналподачи кислорода; 3 - проволока; 4 - направляющая втулка; 5 – канал подачи ацетилена; 6 - канал подачи сжатого воздуха; 7 - ацетилено-кислородное пламя;
8 - газометаллическая струя; 9 - напыляемая поверхность
Преимуществами газопламенного напыления являются небольшое окисление металла, мелкое его распыление, достаточно высокая прочность покрытия. К недостаткам относят сравнительно невысокую производительность процесса (2-4 кг/ч).
Электродуговое напыление производится аппаратами, в которых расплавление металла осуществляется электрической дугой, горящей между двумя проволоками, а распыление - струей сжатого воздуха (рис. 5.14). Подача проволоки в зону горения электрической дуги осуществляется роликами, приводимыми в движение в ручных аппаратах воздушной турбиной, а в станочных - электродвигателем.
Рис. 5.14.Схема электродугового металлизатора: 1 -напыляемая поверхность; 2 - направляющие наконечники; 3 - воздушное сопло; 4 - механизм подачи проволоки; 5 - проволока
Основными преимуществами электродугового напыления являются достаточно высокая производительность процесса (от 3 до 14 кг/ч), сравнительная простота применяемого оборудования и экономичность. К недостаткам относят повышенное окисление металла и большую пористость
покрытия.
Детонационное напыление. При этом способе напыления расплавление металла, его распыление иперенос на поверхность детали достигаются за счет энергии взрыва смеси ацетилена и кислорода. При напылении металла в камеру охлаждаемого водой ствола аппарата (рис. 5.15) подаются в определенном соотношении ацетилен и кислород. Затем в камеру вводится с помощью струи азота напыляемый порошок с размером гранул 50-100 мкм. Газовую смесь поджигают электрической искрой. Взрывная волна сообщает частичкам порошка высокую скорость полета, которая на расстоянии 75 мм от среза ствола достигает 800 м/с. После нанесения каждой дозы порошка ствол аппарата продувается азотом для удаления продуктов сгорания. Этот процесс повторяется автоматически с частотой 3-4 раза в секунду. За один цикл на поверхность детали наносится слой металла толщиной до 6 мкм.
Преимуществами этого способа напыления являются большая производительность процесса, высокая прочность сцепления покрытия с поверхностью детали, невысокая температура на поверхности детали (не более 200 °С). К недостаткам процесса относят высокий уровень шума (до 140 дБ), что обусловливает необходимость выполнения работ по нанесению покрытий в специальной звукопоглощающей камере.
Плазменное напыление. Для расплавления и переноса металла на поверхность детали используются тепловые и динамические свойства плазменной струи (рис. 5.16). В качестве плазмообразующего газа применяют азот, который дает температуру 10000-15000 °С.
Рис. 5.15. Схема детонационного напыления: 1 - электрическая свеча;
2 - камера; 3 - ствол; 4 - напыляемая поверхность
Рис. 5.16. Схема плазменного напыления: 1 - порошковый дозатор; 2 - вольфрамовый катод; 3 - рубашка водяного охлаждения; 4 - изоляционная прокладка; 5 - сопло плазмотрона (анод); 6 - электрическая дуга; 7 - трубка подачи порошка; 8 - металлоплазменная струя; 9 - напыляемая поверхность
Напыляемый материал в виде порошка вводится в сопло плазмотрона из дозатора при помощи транспортирующего газа (азота). Дозатор определяет расход порошка и, следовательно, производительность процесса напыления. Расход порошка можно плавно регулировать в пределах от 3 до 12 кг/ч). Попадая в плазменную струю, металлический порошок расплавляется и, увлекаемый плазменной струей, наносится на поверхность детали, образуя покрытие.
Основными преимуществами плазменного напыления являются: достаточно высокая производительность процесса (до 12 и более кг/ч), более высокие, чем при других способах напыления, физико-механические свойства покрытия (например, износостойкость в 1,5-2 раза выше, чем у закаленной стали 45); возможность нанесения покрытий из любых сплавов толщиной
от 0,1 до 10 мм; полная автоматизация процесса напыления. Прочность сцепления покрытия с деталью выше, чем при других способах напыления, но она все же не превышает 15-50 МПа при испытании на отрыв и меньше, чем при наплавке плазменным способом. Недостатками способа являются: недостаточная, в ряде случаев, прочность сцепления покрытий с основой, наличие пористости (2-15 %), препятствующей применению многих плазменных покрытий в коррозионных средах без дополнительной обработки, невысокий коэффициент полезного действия энергии плазменной струи при нагреве порошка (2-8 %).
Напыляемые материалы. В качестве напыляемых материалов при восстановлении деталей применяют проволоку или порошковые сплавы. При газопламенном и электродуговом напылении обычно используют проволоку. Среднеуглеродистую проволоку применяют при восстановлении посадочных поверхностей на стальных и чугунных деталях. Для деталей, работающих в условиях трения, рекомендуется применять стальную проволоку с повышенным содержанием углерода.
При плазменном и детонационном напылении применяют порошковые сплавы. Для получения износостойких покрытий рекомендуется применять порошковые сплавы на основе никеля или более дешевые славы на основе железа с высоким содержанием углерода. Сплавы на основе никеля обладают высокими технологическими и эксплуатационными свойствами. Наличие в их структуре твердых составляющих (карбидов и боридов) и сравнительно мягкой основы (твердого раствора) позволяет получать покрытия с высокими эксплуатационными свойствами.
Порошковые сплавы на основе никеля (табл. 5.5) обладают рядом ценных свойств: низкой температурой плавления (950-1050 °С), твердостью HRCэ 35-60 в зависимости от содержания бора, жидкотекучестью, высокой износостойкостью и свойством самофлюсования благодаря наличию в составе бора и кремния, которые активно отнимают кислород от окислов. Основной их недостаток - высокая стоимость, которая снижает эффективность применения этих сплавов при восстановлении деталей.
Таблица 5.5
Порошковые сплавы для напыления на основе никеля
(по ГОСТ 21448-75)
Марка порошка | Содержание в сплаве различных элементов | Твердость HRCэ | ||||
Железо | Хром | Кремний | Углерод | Бор | ||
ПГ-СР2 | < 5,0 | 12-15 | 2,0-3,0 | 0,2-0,5 | 1,5-2,1 | > 35 |
ПГ-СР3 | < 5,0 | 13,5-16,5 | 2,5-3,5 | 0,4-0,7 | 2,0-2,8 | > 45 |
ПГ-СР4 | < 5,0 | 15-18 | 3,0-4,5 | 0,6-1,0 | 2,8-3,8 | > 55 |
Таблица 5.6
Порошки на основе никеля, применяемые в качестве подслоя
при напылении (по ТУ 14-1-3282-81 НПО «Тулачермет»)
Марка порошка | Химический состав, % (по массе) | Температура плавления, °С | Твердость HRCэ | Прочность сцепления, МПа | |
Титан | Алюминий | ||||
ПН-70Ю30 | - | 28-33 | > 40 | 30-35 | |
ПН-85Ю15 | - | 12-15 | > 40 | 40-45 | |
ПН-55Т45 | 43-47 | - | 50-60 | 45-50 |
Сплавы на основе железа свысоким содержанием углерода типа ПГС1 (Сормайт-1) имеют высокую твердость (HRCэ56-63), высокую износостойкость, недефицитны, но более тугоплавки (1250-1300 °С) и не обладают свойством самофлюсования.
При восстановлении посадочных поверхностей под подшипники в чугунных корпусных деталях применяют стальной порошок ПЖ-5М с добавкой 1-2 % порошка алюминия АКП. Для повышения прочности сцепления покрытия с поверхностью детали рекомендуется напылять подслой из порошков, состав и свойства которых приведены в табл. 5.6.
Технология напыления. Процесс нанесения покрытий включает подготовку детали к напылению, нанесение покрытий и обработку детали после напыления. Подготовка детали к напылению служит для обеспечения прочного сцепления покрытия с поверхностью детали. Она включает в себя обезжиривание и очистку детали от загрязнений, механическую обработку и создание шероховатости на поверхности детали. При механической обработке с поверхности детали снимают слой металла, чтобы после окончательной обработки напыленной детали на ее поверхности оставалось покрытие толщиной не менее 0,5-0,8 мм.
Для получения на поверхности детали необходимой шероховатости ее подвергают дробеструйной обработке или накатывают (зубчатым роликом). Дробеструйную обработку проводят в специальных камерах чугунной колотой дробью ДЧК-1,5 при режиме:расстояние от сопла дробеструйного аппарата до детали 25-50 мм, давление сжатого воздуха 0,5-0,6 МПа, угол наклона струи к поверхности детали 45°, время обработки 2-5 мин.
Накатку для создания шероховатости применяют при восстановлении деталей с твердостью не более НВ400. Нанесение покрытия на поверхность детали производят на оборудованных токарных станках или в специальных камерах. При напылении на токарных станках деталь устанавливают в патрон станка, а метализационный аппарат - на суппорт. При использовании специальных камер они должны иметь соответствующие механизмы для взаимного перемещения детали и металлизатора. Пост напыления оборудуют вытяжной вентиляцией.
Качество покрытия и производительность процесса в значительной степени зависят от режима напыления (табл. 5.7, 5.8).
Таблица 5.7
Режимы газопламенного и электродугового напыления
Режим обработки | Газопламенное напыление | Электродуговое напыление |
Расстояние напыления, мм | 100-150 | 75-100 |
Скорость вращения детали, м/мин | 10-15 | 15-20 |
Окончание табл. 5.7
Режим обработки | Газопламенное напыление | Электродуговое напыление |
Продольная подача аппарата, мм/об | 1,5-2 | 1,5-2 |
Диаметр проволоки, мм | 1,5-3 | 1,5-2,5 |
Сила тока, А | - | 120-180 |
Напряжение, В | - | 25-30 |
Скорость подачи проволоки, мин | 4,5-6 | 2-3 |
Производительность напыления, кг/ч | 2-3 | 6-8 |
Давление сжатого воздуха, МПа | 0,3-0,5 | 0,5-0,6 |
Давление ацетилена, МПа | 0,01-0,06 | - |
Давление кислорода, МПа | 0,3-0,5 | - |
Таблица 5.8
Режимы газопламенного напыления
цилиндрических поверхностей
Режим обработки | Газопламенное напыление | Электродуговое напыление |
Сила тока, А | 300-350 | 260-300 |
Напряжение, В | 70-80 | 70-80 |
Плазмообразующий газ | Азот | Азот |
Расход азота, л/мин | 25-30 | 28-30 |
Расход транспортирующего газа (азота), л/мин | 2,5-3 | 3-5 |
Расстояние напыления, мм | 125-150 | |
Диаметр сопла плазмотрона, мм | 5-6 | 5-6 |
Напыляемый материал | ПГ-СР3, ПГ-СР4 | ПЖ-5М |
Размер гранул порошка, мкм | 50-100 | 100-160 |
Расход порошка, кг/ч | 6-8 | 6-8 |
Скорость вращения детали, мин | 15-20 | 10-15 |
Продольная подача плазмотрона, мин | 0,3-0,5 | 0,3-0,4 |
После нанесения покрытия деталь медленно охлаждают до температуры окружающей среды и обрабатывают покрытие до требуемого размера.
В зависимости от твердости покрытия, требуемой точности и шероховатости поверхности деталей применяют обработку резанием или шлифованием.
Оборудование для напыления. При напылении металла на детали применяют специальные аппараты и установки. Для газопламенного напыления используют аппараты МГИ-1-57 и ГИМ-1 (табл. 5.9).
Таблица 5.9
Аппараты для газопламенного напыления