Основные положения и классификация способов. Наплавкой называется процесс нанесения слоя металла на поверхность заготовки или изделия способами сварки плавлением. В случае применения сварки давлением употребляют термин «наварка». Классификация способов наплавки приведена на рис. 5.2.
Способы наплавки как и способы сварки классифицируют по трем группам признаков: физическим, термическим и технологическим. По физической группе признаков (источнику нагрева) способы наплавки можно разделить на три группы: термические, механические и термомеханические (рис. 5.2). Большинство из рассмотренных на рисунке способов, в свою очередь, подразделяют по техническим (способ защиты металла при наплавке, степень механизации и непрерывности) и технологическим (род тока, количество электродов, внешнее воздействие) признакам.
Термические способы наплавки. Ручная дуговая наплавка штучными электродами является универсальным и пригодным для наплавки деталей различной формы способом, выполняется во всех пространственных положениях. Основа способа – ручная дуговая сварка (см. параграф 6.1) с незначительными отличиями по маркам применяемых электродов и режимам. Так, например, при наплавке кроме сварочных электродов ГОСТ 10051-75 рекомендует применять наплавочные электроды, выбираемые в зависимости от содержания углерода и легирующих элементов в основном металле. Наплавку ведут электродами Æ 3 мм при толщине наплавляемого слоя менее
1,5 мм и электродами Æ 4-6 мм - при большей толщине слоя. Для обеспечения минимального проплавления основного металла при достаточной устойчивости горения дуги плотность тока должна составлять 11-12 А/мм2 [145].
|
Основные достоинства способа: универсальность, гибкость, простота, доступность, возможность получения наплавки любого состава. Недостатки способа: низкая производительность, тяжелые условия труда, непостоянство качества наплавленного слоя, большое проплавление основного металла.
Рис. 5.2. Способы наплавки
Полуавтоматическая и автоматическая дуговая наплавка предусматривает применение всех основных способов механизированной дуговой сварки: под флюсом, в среде защитных газов, самозащитными проволоками и лентами. Наиболее широко используется наплавка под флюсом одной проволокой или лентой (холоднокатаной, порошковой, спеченной). Для увеличения производительности применяют многодуговую и многоэлектродную наплавку. Легирование наплавленного металла осуществляют, как правило, через электродный металл, легирующие флюсы применяют редко. Дуговую наплавку в среде защитных газов (СО2, Ar, Ne, N или их смеси) используют редко. Значительное распространение получила дуговая наплавка самозащитными порошковыми проволоками и лентами, в которых стабилизация дуги, легирование и защита расплавленного металла от воздуха обеспечиваются компонентами сердечника электрода.
Достоинствами метода являются универсальность, высокая производительность, возможность широкого легирования. К недостаткам метода следует отнести большое проплавление основного металла, особенно при наплавке проволоками.
Электрошлаковая наплавка основана на использовании тепла, выделяющегося при прохождении электрического тока через шлаковую ванну. Основные схемы такой наплавки даны на рис. 5.3. Наплавку можно вести в горизонтальном положении с принудительным и свободным формированием наплавленного слоя, а также в вертикальном и наклонном положениях в основном с принудительным формированием такого слоя.
|
Достоинствами метода являются: высокая производительность (достигающая сотен килограммов наплавленного металла в час), получение за один проход слоев большой толщины, высокая устойчивость процесса в широком диапазоне плотностей тока (0,2-300 А/мм2), возможность наплавки сталей со склонностью к образованию трещин, возможность придания наплавке необходимой формы. К недостаткам метода относятся: сложность и уникальность оборудования, большая длительность подготовки, невозможность получения слоев малой толщины, перегрев основного металла в зоне термического влияния из-за большой погонной энергии.
|
|
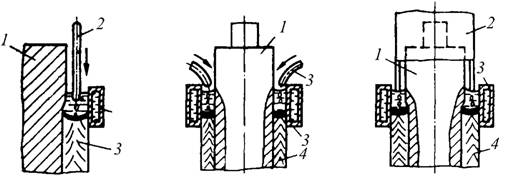
а б в
г д е
ж з
Рис. 5.3. Схемы электрошлаковой наплавки: а - плоской поверхности в вертикальном положении; б - цилиндрической детали проволоками; в - электродом-трубой; г - зернистым присадочным материалом; д - композиционного сплава; е - плоской поверхности в наклонном положении; ж - жидким присадочным металлом; з - горизонтальной поверхности с принудительным формированием; 1 - основной металл; 2 - электрод; 3 - кристаллизатор; 4 - наплавленный металл; 5 - дозатор; 6 - тигель; 7 - флюс
а б в
г д е
ж з
Рис. 5.4. Схемы плазменной наплавки: а - плазменной струей с токоведущей присадочной проволокой; б - плазменной струей с нейтральной присадочной проволокой; в - комбинированной (двойной) дугой одной проволокой; г - то же, двумя проволоками; д - горячими проволоками; е - плавящимся электродом; ж - с внутренней подачей порошка в дугу; з - с внешней подачей порошка в дугу; 1 - защитное сопло; 2 - сопло плазмотрона; 3 - защитный газ; 4 - плазмообразующий газ; 5 - электрод; 6 - присадочная проволока; 7 - изделие; 8 - источник питания; 9 - источник питания дуги прямого действия; 10 - трансформатор; 11 - источник питания дуги плавящегося электрода; 12 - порошок; 13 - порошок твердого сплава
|
Плазменная наплавка основана на использовании плазменной дуги в качестве источника нагрева. Как правило, наплавку выполняют на постоянном токе прямой и обратной полярности. Наплавляемая деталь может быть электрически нейтральной (наплавка плазменной струей или, что чаще, включается в электрическую цепь источник питания дуги, т. е. наплавка плазменной дугой). Плазменная наплавка имеет относительно невысокую производительность (4-10 кг/ч), но благодаря минимальному проплавлению металла позволяет получать требуемые свойства наплавленного металла уже в первом слое и тем самым повысить качество и сократить объем наплавочных работ.
Существует несколько схем плазменной наплавки (рис. 5.4), но наибольшее распространение получила плазменно-порошковая наплавка, как наиболее универсальный метод получения наплавки любого состава. Так же существует несколько схем включения плазмотронов, показанных на рис. 5.5.
а б в
Рис. 5.5. Схемы включения плазмотронов:
а - закрытая; б - открытая; в - комбинированная
Основными достоинствами метода являются: высокое качество, малая глубина проплавления основного металла при высоком качестве сцепления, возможность наплавки тонких слоев, высокая культура производства. К недостаткам следует отнести относительно невысокую производительность и необходимость в сложном оборудовании.
Наплавка деталей под слоем флюса. Схема дуговой наплавки под флюсом цилиндрических деталей приведена на рис. 5.6. Деталь 5 устанавливают в патроне или центрах специально переоборудованного токарного станка, а наплавочный аппарат – на его суппорте. Электродная проволока подается из кассеты 2 роликами подающего механизма наплавочного аппарата в зону горения электрической дуги. Движение электрода вдоль сварочного шва обеспечивается вращением детали, а по длине наплавленной поверхности продольным движением суппорта станка. Наплавка производится винтовыми валиками с взаимным их перекрытием примерно на 1/3. Сыпучий флюс 4, состоящий из отдельных мелких крупиц, в зону горения дуги поступает из бункера 3. Под воздействием высокой температуры часть флюса плавится, образуя вокруг дуги эластичную оболочку, которая надежно защищает расплавленный металл от действия кислорода и азота. После того как дуга переместилась, жидкий металл твердеет вместе с флюсом, образуя на наплавленной поверхности ломкую шлаковую корку. Флюс, который не расплавился, может быть снова использован. Электродная проволока подается с некоторым смещением от зенита «е » наплавляемой поверхности в сторону, противоположную вращению детали. Это предотвращает оте-кание жидкого металла сварочной ванны. Режимы наплавки, устанавливаемые в зави-симости от диаметра наплавляемой поверх-ности детали, приведены в табл. 5.1.
Для наплавки используют наплавоч-ные головки А-580М, ОКС-5523, А-765 или наплавочные установки СН-2, УД-209 и др.
При наплавке плоской поверхности наплавочная головка или деталь совершает поступательное движение со смещением электродной проволоки на 3-5 мм поперек движения после наложения шва заданной длины. Наплавку шлицев производят в про-дольном направлении путем заплавки впа-дин, устанавливая конец электродной про-волоки на середине впадины между шли-цами. Основные параметры наплавки плос-ких поверхностей приведены в табл. 5.2. Твердость и износостойкость наплав-пленного слоя в основном зависят от применяемой электродной проволоки и марки флюса.
Для наплавки используют электрод-ную проволоку: для низкоуглеродистых и низколегированных сталей – из малоуглеродистых (Св-08, Св-08А), марганцовистых (Св-08Г, Св-08ГА, Св-15Г) и кремниймарганцовистых (Св-08ГС, Св-08Г2С, Св-12ГС) сталей; с большим содержанием углерода – Нп-65Г,
Нп-80, Нп-ЗОХГСА, Нп-40Х13 и др.
Таблица 5.1
Режимы наплавки цилиндрических поверхностей
Диаметр детали, мм | Сила тока, А | Скорость, м/ч | Смещение электрода е, мм | |
подачи проволоки | наплавки | |||
40-50 | 110-130 | 70-100 | 14-18 | 4-5 |
60-70 | 170-180 | 70-120 | 20-24 | 5-6 |
80-90 | 170-200 | 120-150 | 20-24 | 6-7 |
90-100 | 170-200 | 120-150 | 20-24 | 7-8 |
Таблица 5.2
Основные параметры наплавки плоских поверхностей
Износ, мм | Сила тока, А | Проволока | |
Скорость подачи, м/ч | Диаметр, мм | ||
2-3 | 160-220 | 100-125 | 1,6-2,0 |
2-4 | 320-350 | 150-200 | 1,6-2,0 |
4-5 | 350-460 | 180-210 | 2,0-3,0 |
5-6 | 650-750 | 200-250 | 4,0-5,0 |
В зависимости от способа изготовления флюсы для автоматической наплавки делят на плавленые, керамические и флюсы-смеси. Плавленые флюсы содержат стабилизирующие и шлакообразующие элементы, но в них не входят легирующие добавки, поэтому они не могут придавать слою, наплавленному малоуглеродистой, марганцовистой и кремниймарганцовистой проволоками, высокую твердость и износостойкость. Из плавленых флюсов наиболее распространены АН-348А, АН-60, ЮСу-45, АН-20, АН-28.
Керамические флюсы (АНК-18, АНК-19, АНК-30, КС-Х14Р, ЖСН-1) кроме стабилизирующих и шлакообразующих элементов содержат легирующие добавки, главным образом в виде ферросплавов (феррохрома, ферротитана и др.), дающие слою, наплавленному малоуглеродистой проволокой, высокую твердость (без термообработки) и износостойкость.
Наплавка в среде углекислого газа. Этот способ восстановления деталей отличается от наплавки под флюсом тем, что в качестве защитной среды используется углекислый газ.
Сущность способа наплавки в среде углекислого газа (рис. 5.7) заключается в том, что электродная проволока из кассеты непрерывно подается в зону сварки. Ток к электродной проволоке подводится через мундштук и наконечник, расположенные внутри газоэлектрической горелки. При наплавке металл электрода и детали перемешивается. В зону горения дуги под давлением 0,05-0,2 МПа по трубке подается углекислый газ, который, вытесняя воздух, защищает расплавленный металл от вредного действия кислорода и азота воздуха.
При наплавке используют токарный станок, в патроне которого устанавливают деталь 8, на суппорте крепят наплавочный аппарат 2 (рис. 5.8 ). Углекислый газ из баллона 7 подается в зону горения. При выходе из баллона 7 газ резко расширяется и переохлаждается. Для подогрева его пропускают через электрический подогреватель 6. Содержащуюся в углекислом газе воду удаляют с помощью осушителя 5, который представляет собой патрон, наполненный обезвоженным медным купоросом или силикагелем. Давление газа понижают с помощью кислородного редуктора 4, а расход его контролируют расходомером 3.
Рис. 5.7. Схема наплавки в среде углекислого газа: 1 – мундштук; 2 – электродная проволока; 3 – горелка; 4 – наконечник; 5 – сопло горелки; 6 – электрическая дуга; 7 – сварочная ванна; 8 – наплавленный металл; 9 – наплавляемая деталь
Рис. 5.8. Схема установки для дуговой наплавки в углекислом газе: 1 – кассета с проволокой; 2 – наплавочный аппарат; 3 – расходомер; 4 – редуктор; 5 – осушитель; 6 – подогреватель; 7 – баллон с углекислым газом; 8 – деталь
К достоинствам способа относятся: – меньший нагрев деталей; возможность наплавки при любом пространственном положении детали; более высокая по площади покрытия производительность процесса (на 20-30 %); возможность наплавки деталей диаметром менее 40 мм; отсутствие трудоемкой операции по отделению шлаковой корки, а к недостаткам – повышенное разбрызгивание металла (5-10 %); необходимость применения легированной проволоки для получения наплавленного металла с требуемыми свойствами; открытое световое излучение дуги.
Для наплавки применяют следующее оборудование: наплавочные головки АБС, А-384, А-409, А-580, ОКС-1252М; источники питания ВС-200, ВСУ-300, ВС-400, ПСГ-350, АЗД-7,5/30; подогреватели газа; осушитель, заполненный силикагелем КСМ крупностью 2,8–7 мм; редукторы-расходомеры ДРЗ-1-5-7 или ротаметры PC-3, PC-3A, РКС-65, или кислородный редуктор РК-53Б. При наплавке используют материалы: электродную проволоку Св-12ГС, Св-0,8ГС, Св-0,8Г2С, Св-12Х13, Св-06Х19Н9Т, Св-18ХМА,
Нп-ЗОХГСА; порошковую проволоку ПП-Р18Г и др.
Режимы наплавки, выполняемой на цилиндрических деталях, приведены в табл. 5.3.
Таблица 5.3