ВВЕДЕНИЕ
При строительстве и ремонте дорог приходится производить перемещение большого количества различных строительных материалов. При этом, помимо земляных работ, укладки песка, каменных материалов и асфальтобетонной массы, необходимо уложить трубы, построить мосты и другие сооружения, необходимые для эксплуатации дорог.
Для выполнения этих видов работ применяют подъемно-транс-
портные машины.
По характеру работ различают подъемно-транспортные машины периодического и непрерывного действия. В зависимости от назначения и конструкции подъемно-транспортные машины подразделяются на группы в соответствии с классификацией. Некоторые типы машин (домкраты) используются как вспомогательные механизмы для подъема грузов на небольшие расстояния при ремонтных работах. Другие грузоподъемные механизмы (лебедки) в основном используются в составе других машин (кранов). Группа грузоподъемных машин (тали и тельферы) применяется в складских хозяйствах и при проведении ремонтных работ.
Настоящие методические указания рассматривают сборочные единицы грузоподъемных машин, приводят методику подбора основных элементов и определяющих параметров грузоподъемных машин на примере грузовой лебедки с целью выполнения лабораторной работы.
ДЕТАЛИ МАШИН ОБЩЕГО НАЗНАЧЕНИЯ
Общие положения
Деталь – это неразъемная элементарная часть машины или механизма.
Обеспечение работоспособности машин и механизмов определяется жесткостью, прочностью, износостойкостью, а в ряде случаев – теплостойкостью и вибростойкостью их деталей. Эти свойства диктуются условиями эксплуатации.
Соединения
Соединения различных деталей или сборочных единиц разделяют на две основные группы: неразъемные и разъемные. Неразъемные соединения подразделяют на сварные и заклепочные, разъемные – на резьбовые, шпоночные и шлицевые.
Наиболее распространенными из неразъемных соединений являются сварные. Сварные соединения разделяют на стыковые, угловые, тавровые и нахлесточные.
Швы нахлесточных соединений в зависимости от направления усилий бывают лобовые, фланговые и косые.
Когда соединение работает в условиях вибрации или применение сварки ограничено, применяют заклепочные соединения, относящиеся также к неразъемным соединениям.
Основным элементом заклепочных соединений являются заклепки, которые бывают стержневыми и трубчатыми. Наиболее распространенными являются первые. Они различаются по форме закладных головок: полукруглых, потайных, полупотайных и др.
По способу соединения деталей заклепочные соединения бывают нахлесточные, стыковые с одной накладкой и стыковые с двумя накладками, однорядные и многорядные.
Наиболее распространенными видами разъемных соединений являются резьбовые. Резьбу выполняют по винтовой линии на цилиндрической поверхности – внешней (винт) или внутренней (гайка). Резьба на цилиндрической поверхности образуется путем создания канавок по винтовой линии. Профиль канавок определяет тип резьбы. В зависимости от числа винтовых линий различают одно-, двух- и многозаходные резьбы.
В зависимости от направления винтовой линии резьбы бывают право- и левозаходные. Для обеспечения самоторможения в резьбовых соединениях угол винтовой линии должен быть меньше угла трения.
Шпоночные соединения применяют для крепления на валах и осях деталей вращения. Для установки шпонок на валу и в ступице детали вращения вырезают канавки, куда закладывают соединительную деталь-шпонку. Наиболее распространенными видами шпонок являются призматические и сегментные.
Передачи
Передачами называют механизмы, предназначенные для передачи движения от ведущего элемента к ведомому с возможным изменением характеристики движения (направления, скорости, вида). Передачи могут быть механическими, гидравлическими, пневматическими, электрическими и комбинированными. Наиболее типичными в машиностроении являются механические передачи, которые основываются на использовании трения (фрикционные и ременные) и зацепления (зубчатые, цепные).
Для передач характерно понятие передаточного числа. Передаточное число передачи – это отношение частоты вращения ведущего к частоте ведомого элементов. Общие передаточные числа системы передач определяют произведением передаточных чисел отдельных пар.
Фрикционными передачами называют такие, у которых вращение от ведущего элемента ведомому передается с помощью сил трения при непосредственном контакте элементов. Эти передачи обеспечивают плавную и бесшумную работу, однако не позволяют реализовать постоянное передаточное число при изменяющихся нагрузках из-за возможного проскальзывания. Допуская отсутствие проскальзывания, передаточное число передачи определяется выражением
(1.1)
где ,
– диаметры ведущего и ведомого элементов;
,
– частоты вращения (диаметры) ведущего и ведомого элементов.
С учетом проскальзывания, имеем
(1.2)
где – коэффициент проскальзывания, зависящий от материала и состояния рабочих поверхностей фрикционных элементов.
Обычно передаточные числа фрикционных передач не превышают 10.
Ременными передачами называются такие, у которых движение от ведущего элемента к ведомому передается посредством плоского, круглого или клинового ремня, надетого на шкивы, геометрические оси которых находятся на значительном расстоянии одна от другой. Различают плоско -, клино -, кругло - и зубчато-ременные передачи.
Передаточное число в ременных передачах определяют так же, как и во фрикционных. Использование клиновых ремней позволяет увеличить передаваемые окружные усилия, а зубчатых – исключить проскальзывание.
Фрикционные и ременные передачи основаны на использовании сил трения между элементами.
Зубчатая передача предназначена для передачи вращательного движения между валами с параллельными, пересекающимися и перекрещивающимися осями, а также – для трансформации вращательного движения в поступательное, и наоборот.
В передачах с параллельными валами используют цилиндрические колеса (рис. 1.1).
В цилиндрических передачах применяют прямозубые, косозубые и шевронные колеса. Передачи с косозубыми и шевронными колесами менее шумны, поскольку при их работе происходит плавное зацепление по длине зуба; однако в косозубых передачах возникают нежелательные усилия осевого направления; у шевронных колес эти усилия уравновешиваются.
Зубчатые передачи с цилиндрическими колесами могут быть как с внешним, так и с внутренним зацеплением.
Конические зубчатые передачи позволяют передавать крутящий момент между валами, оси которых пересекаются, а гипоидные, винтовые и червячные – между валами, оси которых перекрещиваются.
Передаточное число зубчатых пар определяется выражением
(1.3)
где ,
– частоты вращения ведущего и ведомого колес;
,
– число зубьев ведущего и ведомого колес.
Рис. 1.1. Виды зубчатых передач и их элементов:
а – цилиндрическая передача с прямозубыми колесами; б – передача
с косозубыми колесами; в – передача с шевронными колесами; г – передача
с коническими колесами; д – реечная передача; е – червячная передача
Чаще всего для цилиндрических колес оно не превышает 10, для конических – 5. Для определения передаточного числа червячных передач в приведенную формулу вместо подставляют число зубьев червячного колеса, а вместо
– число заходов червяка (которое редко превышает три). Этим объясняются сравнительно большие значения передаточных чисел червячных пар, достигающие 80.
Для преобразования вращательного движения в поступательное, и наоборот, применяют реечную передачу.
Для получения значительных передаточных чисел используют редукторы, предназначенные, как правило, для понижения частоты вращения и увеличения крутящего момента (рис. 1.2). Редукторы представляют собой несколько пар зубчатых колес или червячных передач, объединенных в одном жестком корпусе, чаще всего работающих в масляной ванне. Редукторы могут быть одно -, двух - и многоступенчатыми.
Рис. 1.2. Виды исполнения редукторов:
а – одноступенчатый с цилиндрическими колесами;
б – одноступенчатый с коническими колесами; в – двухступенчатый
с коническими и цилиндрическими колесами; г – червячный редуктор
Цепные передачи относятся к передачам зацепления с гибкой связью. Их используют для передачи движения между параллельными валами, оси которых отстоят одна от другой на расстоянии до 8 м. Такие передачи состоят из двух звездочек и цепи, охватывающей звездочки и зацепляющейся за их зубья. На практике применяют цепи нескольких типов: втулочные, втулочно-роликовые, пластинчатые, крючковые и др.; одно -, двух - и многорядные. Передаточные числа цепных передач определяют так же, как и для зубчатых передач.
Валы, оси
Детали вращения устанавливают на валах и осях. Разница между ними заключается в том, что, в отличие от оси, воспринимающей лишь изгибающую нагрузку, вал передает и крутящий момент. Оси могут быть вращающимися и неподвижными.
Оси предназначены для того, чтобы кинематически обеспечивать вращательное движение неподвижно или свободно насаженных на нее деталей без передачи крутящего момента.
Валы не только кинематически обуславливают вращательное движение деталей, но и передают крутящий момент.
Валы и оси по форме поперечного сечения бывают: сплошные, полые, со шпоночным пазом, шлицевые, профильные.
Опорные части валов и осей называют цапфами; концевые цапфы называют шипами, промежуточные – шейками. Опорные части валов и осей, передающие осевую нагрузку, называют пятами (рис. 1.3).
Рис. 1.3. Валы и оси:
а – сплошной вал; б – полый вал; в – шпоночный вал;
г – шлицевой вал; д – профильные валы. 1 – шип; 2 – шейка; 3 – пята
Соответственно под «шип» устанавливается подшипник, под «пяту» – подпятник. В местах расположения «шейки» – устанавливается разборная опора.
Подшипники
Подшипники – это опорные устройства, предназначенные для поддержания вращающихся осей, валов и других деталей и восприятия передаваемых от них радиальных и осевых усилий.
Наибольшее распространение в приводах получили подшипники качения, обладающие рядом преимуществ: большой несущей способностью на единицу ширины подшипника в осевом направлении; высоким к.п.д.; отсутствием специальных требований к валам и осям по термообработке в местах установки подшипников; отсутствием необходимости использовать цветные металлы.
Недостатками подшипников качения являются пониженная долговечность при большой частоте вращения и значительных динамических нагрузках, а также невозможность использовать их в конструкциях, имеющих разъем в радиальном направлении. Все это ограничивает возможность их применения в ряде устройств, где необходима высокая скорость вращения (> 30...50 м/с) или обязателен разъем (например, в коленчатых валах).
По виду трения, возникающего в рабочих элементах опорных устройств, различают подшипники скольжения (рис. 1.4) и качения (рис. 1.5).
По конструкции и функциональному назначению различают: радиальные, радиально-упорные и упорные (см. рис. 1.5).
По типу тела качения подшипники бывают: шариковые, роликовые. Ролики, в свою очередь, подразделяются на цилиндрические, конические, бочкообразные, винтовые, игольчатые (рис. 1.6).
Рис. 1.4. Подшипники скольжения:
а – неразъемный; б – разъемный;
1 – корпус; 2 – вкладыш; 3 – масленка; 4 – крышка
По числу рядов тел качения подшипники бывают однорядными и двухрядными.
Рис. 1.5. Подшипники качения:
1 – наружное кольцо; 2 – внутреннее кольцо; 3 – тело качения; 4 – сепаратор;
а – радиальный подшипник; б – упорный подшипник; в – радиально-упорный
подшипник; г – роликовый подшипник; д – шариковый радиально-упорный
подшипник; е – игольчатый подшипник; ж – шариковый двухрядный
самоустанавливающийся подшипник; з – упорный подшипник
Рис. 1.6. Типы тел качения:
а – шариковый; б – роликовый цилиндрический; в – роликовый конический;
г – роликовый бочкообразный; д – роликовый игольчатый;
е – роликовый винтовой
Муфты
Муфты служат для соединения валов между собой и являются элементами, передающими вращательное движение и крутящий момент с одного вала на другой, расположенные соосно.
В зависимости от функционального назначения, муфты делятся на группы:
· Глухие муфты применяются для постоянного во время эксплуатации соединения соосных валов в одну жесткую схему.
· Компенсирующие муфты применяются при возможном некотором относительном смещении валов, продольном, поперечном, угловом или комбинированном. Рационально выбранная конструкция компенсирующей муфты в значительной мере устраняет влияние несоосности осей валов, что особенно важно, если соединяются агрегаты, установленные на отдельных фундаментах или недостаточно жестких рамах.
· Предельные муфты автоматически предотвращают возможность передачи недопустимых значений крутящего момента или частоты вращения (как минимальной, так и максимальной) с одного вала на другой, а также обеспечивают вращение вала или установленной на нем детали в одном направлении.
· Управляемые муфты предназначаются для соединения или разъединения валов в неподвижном состоянии, на холостом ходу или под нагрузкой с помощью механизмов управления. Такие муфты применяются в механизмах, нуждающихся во время эксплуатации в частых пусках, остановках, реверсировании или изменении режима работы.
Глухие муфты (рис. 1.7) используются для соединения валов, оси которых смещены не более чем на 0,002–0,005 мм, в тех приводах машин, где требуется жесткое соединение отдельных валов в один составной вал, чтобы он работал как цельный. Глухие муфты подразделяются на втулочные и фланцевые.
Компенсирующие муфты (рис. 1.8) подразделяются на жесткие и упругие.
В жестких муфтах, к которым относятся зубчатые, цепные, кулачково-дисковые и шарнирные компенсация несоосного расположения валов осуществляется за счет предусмотренной конструкцией возможности некоторого смещении жестких деталей муфты.
В упругих муфтах такое смещение осуществляется за счет деформации упругого силового элемента муфты. Компенсирующие муфты получили широкое распространение в промышленности благодаря своим положительным свойствам. Упругие втулочно-пальце-
вые муфты МУВП получили наиболее широкое применение в практике за счет простоты конструкции, надежности в эксплуатации, легкости монтажа и демонтажа.
Рис. 1.7. Муфты глухие:
а – втулочная; б – фланцевая;
1 – ведущий вал; 2 – ведомый вал; 3 – втулочная муфта; 4 – шпонка
Предельные муфты (рис. 1.9) по своей функции в приводе машин ограничивают одни из параметров передачи: момент, направление передачи момента, частоту вращения. В соответствии с этим их можно разделить на три группы: предохранительные, обгонные и центробежные.
Обгонные муфты (рис. 1.9 а) представляют собой муфты свободного хода и передают крутящий момент только в одном направлении до тех пор, пока угловая скорость вращения ведомого звена не превысит угловую скорость вращения ведущего. Если скорость вращения ведомого вала по тем или иным причинам превзойдет скорость ведущего вала, муфта автоматически размыкает соединение валов, но как только указанное неравенство исчезнет- муфта вновь соединяет валы.
Рис. 1.8. Компенсирующие муфты:
а – жесткая; б – упругая (МУВП); 1 – полумуфта ведущего вала;
2 – промежуточный компенсирующий элемент; 3 – полумуфта ведомого вала
Предохранительные муфты момента служат для защиты механизмов от перегрузки. Если момент сопротивления на ведомом валу достигнет определенной заранее заданной опасной для деталей и сборочных единиц привода величины, то предельная муфта срабатывает, предотвращая возможность дальнейшего возрастания момента. Пример предохранительной фрикционной муфты представлен на рис. 1.9 б.
Центробежные муфты предназначаются для автоматического включения (или выключения) в работу устройства, с помощью которого крутящий момент передается от ведущего вала к ведомому при достижении ведущим валом определенной скорости вращения. Эти муфты позволяют во многих случаях снизить пусковые нагрузки, так как обеспечивают разъединение ведущего и ведомого валов до того момента, пока ведомый вал не достигнет заданной скорости.
Рис. 1.9. Предельные муфты:
а – обгонная; б – предохранительная фрикционная
Управляемые муфты (рис. 1.10) предназначаются для соединения или разъединения валов в неподвижном состоянии, на холостом ходу или под нагрузкой с помощью механизмов управления.
Такие муфты могут использовать фрикционный принцип действия, иметь зубчатое зацепление, кулачковое и др.
Рис. 1.10. Управляемые муфты:
а – муфта с зубчатым зацеплением; б – конусная муфта
ГРУЗОПОДЪЕМНЫЕ МАШИНЫ
Подъемно-транспортные машины предназначены для подъема, опускания и перемещения штучных, пакетированных и насыпных грузов в промышленности, строительстве, сельском хозяйстве и на транспорте. В зависимости от назначения, подъемно-транспортные машины классифицируются по функционально-подобным группам. В общем случае этих групп может быть сформировано три. Это группа грузоподъемных машин, группа погрузочно-разгрузочных машин, группа транспортирующих машин.
Группа грузоподъемных машин включает в себя домкраты, конструкция которых представлена на рис. 2.1, лебедки, краны, подъемники.
Рис. 2.1. Схемы домкратов:
а – винтовой; б – реечный; в – гидравлический; 1 – корпус; 2 – винт; 3 – оголовок;
4 – трещотка; 5 – гайка; 6 – рукоятка; 7 – собачка; 8 – ось; 9 – стопор;
10 – пружина; 11 – храповое колесо; 12 – рейка; 13 – лапка; 14 – зубчатое колесо;
15 – рабочий цилиндр; 16 – поршень; 17 – перепускной клапан;
18 – уплотнительная манжета плунжера; 19 – плунжер; 20 – бак рабочей
жидкости; 21 – пружина клапана; 22 – клапан всасывающий;
23 – клапан нагнетательный
Лебедки – грузоподъемные машины, которые в основном используются в составе других машин (кранов).
Лебедки предназначены для создания тягового усилия в одном направлении. Как правило, в состав конструкции лебедки входят двигатель (обычно – это электрический двигатель), понижающий редуктор, барабан, канат (трос), грузозахватное устройство (обычно это крюк). Лебедки могут эксплуатироваться как самостоятельные механизмы, так и в составе более сложных механизмов (например, кранов). Различают лебедки подъемные и тяговые. Подъемные лебедки используют при подъеме и опускании свободно подвешенного груза или грузовой площадки, перемещающейся по направляющим. Тяговые лебедки применяют при перемещении тележек с грузом по горизонтальной или слегка наклонной плоскости.
Рис. 2.2. Схемы лебедок:
а – лебедка с ручным приводом (общий вид и кинематическая схема);
б – лебедка реверсивная с электроприводом; в – лебедка
с зубчато-фрикционным приводом; 1 – барабан; 2 – рама (щека);
3 – зубчатые колеса; 4 – рукоятка; 5 – грузоупорное тормозное устройство;
6 – двухступенчатый редуктор; 7 – тормоз; 8 – электродвигатель;
9 – фрикционная коническая муфта сцепления;
10 – храповой механизм (останов)
Лебедки (рис. 2.2) предназначены для подъема и перемещения груза с помощью стального каната или цепи, навиваемых на барабан. Различают лебедки общего и специального назначения. Лебедки специального назначения входят в состав конструкции кранов, экскаваторов, бульдозеров, скреперов, бетономешалок и других механизмов.
Лебедки с ручным приводом используют на монтажных работах в качестве вспомогательного оборудования, когда скорость подъема груза не имеет существенного значения. Тяговое усилие таких лебедок составляет 5...100 кН.
Барабаны (рис. 2.3) различают для многослойной и однослойной навивок канатов. Барабаны для многослойной навивки применяют только при больших длинах навиваемого каната. При многослойной навивке барабаны бывают с гладкой поверхностью. При однослойной навивке применяют нарезные барабаны, что увеличивает поверхность контакта каната и барабана и уменьшает износ каната.
Рис. 2.3. Схемы барабанов:
а – конструкция барабана; б – схемы запасовки канатов;
1 – нормальная канавка; 2 – глубокая канавка
На барабане конец каната закрепляется различными способами: накладкой, клином, нажимными болтами. Канат в месте крепления не должен подвергаться резкому изгибу. Для уменьшения натяжения каната в месте его крепления на барабане всегда должен оставаться запас не менее 1,5...2 витков.
Тормозные устройства реверсивных лебедок с приводом от электродвигателя имеют различные конструктивные варианты двухколодочных электромагнитных тормозов (рис. 2.4). Наиболее известны конструкции электромагнитных тормозов с короткоходовым электромагнитом (ход якоря 2...4 мм) и длинноходовым электромагнитом, а также с электрогидравлическим толкателем.
б |
а |
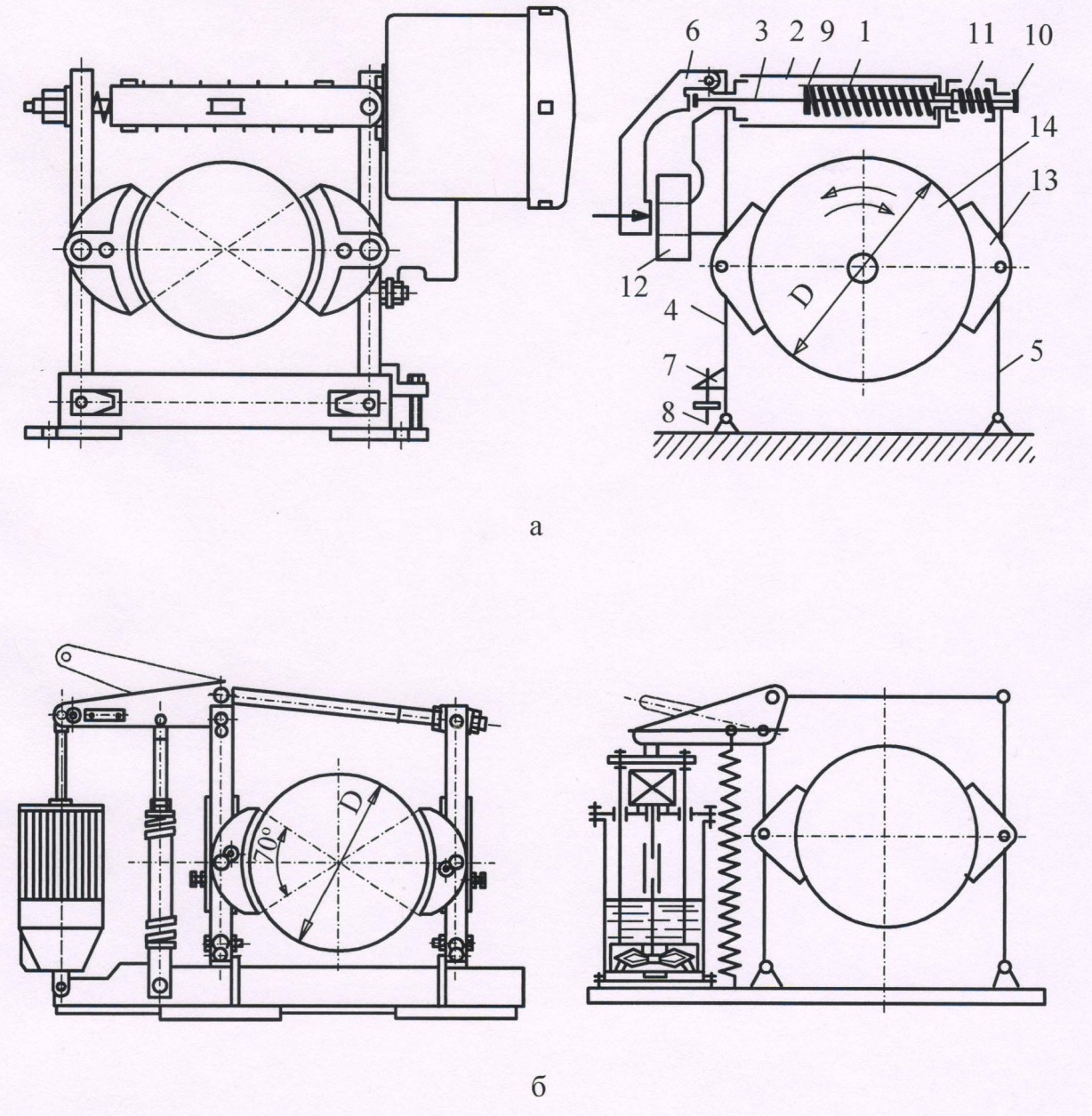
Рис. 2.4. Общий вид и схемы электромагнитных тормозов:
а – общий вид и схема электромагнитного тормоза
с короткоходовым электромагнитом; б – общий вид и схема колодочного
тормоза с электрогидравлическим толкателем
В конструкции электромагнитного тормоза с короткоходовым магнитом прижатие тормозных колодок к шкиву (в качестве которого используется соединительная муфта) производится пружиной 1 через тягу 2 и шток 3 на рычаги-стойки 4 и 5. При включении электродвигателя лебедки, ток проходит и по катушке электромагнита, вызывая сближение катушки 12 и скобы-якоря 6, который, в свою очередь, смещает шток 3, сжимающий пружину 1 и разводящий концы рычагов-стоек 4 и 5, шарнирно закрепленных в основании. При смещении рычагов-стоек 4 и 5 между тормозными колодками 13 и шкивом 14 образуется зазор, который обеспечивает свободное вращение барабана лебедки при подъеме или опускании груза.
Для ограничения отвода колодок имеется упор 7 с регулировочным винтом 8. Усилие пружины регулируют гайкой 9, а величину отхода колодки – гайкой 10. Для отвода рычага-стойки 5 установлена вспомогательная пружина 11. При отключении катушки электромагнита пружина, разжимаясь, смещает тягу и шток в противоположные стороны, возвращая концы рычагов-стоек 4 и 5, а вместе с ними и колодки, в первоначальное положение. При этом усилие в пружине создает достаточное давление между колодками и шкивом, в результате чего возникает трение, препятствующее вращению шкива.
Полиспастами называют систему подвижных и неподвижных блоков, огибаемых канатом. Полиспасты различной кратности применяют в качестве рабочих органов грузоподъемных машин (кранов, лебедок). Кроме изменения направления движения каната, полиспаст позволяет получить выигрыш в окружном усилии на барабане или в скорости подъема груза в зависимости от схемы исполнения полиспаста. Соответственно, необходимо отметить, что если полиспаст дает выигрыш в силе, то одновременно имеет место потеря в скорости, и наоборот.
Под кратностью i полиспаста понимают отношение скорости навивки каната на барабан к скорости подъема груза, или отношение веса поднимаемого груза к окружному усилию на барабане без учета КПД. У простых полиспастов (рис. 2.5) кратность полиспаста равна количеству нитей, на которых подвешен груз. Различают полиспасты простые и сдвоенные. В сдвоенных полиспастах средний неподвижный блок (уравновешивающий) уравнивает возможную разность натяжения каната в двух ветвях.
Рис. 2.5. Полиспасты:
а – двукратный полиспаст; б – трехкратный полиспаст; в – четырехкратный
полиспаст; г – сдвоенный двукратный полиспаст; д – двукратный сдвоенный
полиспаст; е – крюковая обойма подвижных блоков и грузозахватные
приспособления; 1 – подвижные блоки; 2 – щеки; 3 – гайка; 4 – траверса;
5 – однорогий крюк; 6 – двурогий крюк; 7 – грузовая петля
В сдвоенных полиспастах кратность определяется как количество рабочих ветвей, деленное на 2. В ответственных механизмах, как правило, применяются сдвоенные полиспасты.
Использование обратного полиспаста дает выигрыш в скорости подъема груза, но при этом соответственно увеличивается прилагаемое усилие.
Подвижные блоки компонуются в крюковую обойму.
Блоки (рис. 2.6) применяют для изменения направления движения каната. Профиль ручья блока выполняют так, чтобы обеспечить беспрепятственный вход и выход каната.
Рис. 2.6. Общий вид блоков и расположения грузоподъемного каната
Канаты относятся к такелажному оборудованию, в состав которого также входят цепи и стропы. Канатыбывают стальные, пеньковые и капроновые. Пеньковые канаты применяют редко, так как они обладают низкой механической прочностью. Капроновые канаты считаются более надежными. Стальные канаты изготавливают из проволоки диаметром 0,5...2 мм (реже 3...5 мм). Проволоки предварительно свиваются в пряди, а пряди свивают вокруг пенькового сердечника, который придает канату гибкость и является хранилищем смазочного материала. Стальные канаты являются сложным и ответственным видом проволочных изделий. Они имеют большое количество типов и конструкций и различаются по форме поперечного сечения как самого каната, так и его элементов, а также по физико-химическим характеристикам проволок и сердечников. Стальные канаты (рис. 2.7) должны отвечать действующим государственным стандартам в соответствии с ГОСТ 3241-91»Канаты стальные, технические условия». В соответствии с настоящим стандартом канаты имеют следующую классификацию.
1. По конструкции:
· одинарной свивки (спиральные);
· двойной свивки;
· тройной свивки.
2. По типу свивки прядей:
· с точечным касанием проволок между слоями – ТК;
· с линейным касанием проволок между слоями – ЛК;
· с комбинированным точечно-линейным касанием проволок – ТЛК.
3. По форме поперечного сечения:
· круглые;
· плоские.
4. По форме поперечного сечения прядей:
· крупнопрядные;
· фасоннопрядные.
5. По степени крутимости:
· крутящиеся;
· малокрутящиеся.
6. По материалу сердечника:
· с органическим сердечником из натуральных или синтетических материалов – ОС;
· с металлическим сердечником – МС.
7. По способу свивки:
· нераскручивающиеся – Н;
· раскручивающиеся Р.
8. По степени уравновешенности:
· рихтованные – Р;
· нерихтованные.
9. По направлению свивки каната:
· правой;
· левой – Л.
10. По сочетанию направлений свивки канатов и его элементов в канатах двойной и тройной свивки.
11. По механическим свойствам:
· канаты марок ВК, В, I.
12. По виду покрытия поверхности проволоки в канате:
· из проволоки без покрытия;
· из оцинкованной проволоки.
13. По назначению:
· грузолюдские – ГЛ;
· грузовые – Г;
14. По точности изготовления:
· нормальной;
· повышенной – Т.
Рис. 2.7. Стальные проволочные канаты:
а – структура каната; б – одинарной свивки; в – двойной односторонней свивки; г – крестовой свивки; д – спиральный (закрытый);
1 – пряди; 2 – проволока; 3 – сердечник; 4 – верхний слой пряди
Для тяжелонагруженных канатов и канатов, работающих в условиях высоких температур, в качестве сердечника используют одну из прядей. В грузоподъемных машинах применяют канаты крестовой свивки, которые имеют большую жесткость, хорошо сопротивляются расплющиванию и раскручиванию при огибании блоков и барабанов. Канат, изготовленный из проволочек различного диаметра, имеет линейный контакт проволочек между прядями. Прочность таких канатов на 10...15% выше, чем прочность обычного.
В грузоподъемных машинах применяют канаты диаметром d к =
= 4,2…65 мм, свитые из шести прядей, в каждой из которых 19 или
37 проволочек.
3. ЛАБОРАТОРНАЯ РАБОТА «ИЗУЧЕНИЕ КОНСТРУКЦИИ И
ВЫБОР ОСНОВНЫХ ПАРАМЕТРОВ ГРУЗОВОЙ ЛЕБЕДКИ КРАНА»
Цель и задачи работы
Изучение устройства и конструкции грузовой лебедки крана, ознакомление с деталями машин общего назначения и наиболее распространенными сборочными единицами грузоподъемных машин, освоение методики подбора основных элементов и определяющих параметров грузоподъемных машин на примере грузовой лебедки.
Исходные данные
Работа выполняется по вариантам индивидуальных заданий (табл. 3.1) и в соответствии с кинематической схемой лебедки
(рис. 3.1). Варианты схем полиспастов представлены на рис. 3.2.
Рис. 3.1. Кинематическая схема лебедки:
1 – грузовой барабан; 2, 5 – муфты; 3 – редуктор; 4 – тормоз; 6 – двигатель
Рис. 3.2. Варианты схем полиспастов по заданию
Таблица 3.1
Варианты индивидуальных заданий
№ варианта | Грузоподъемность Q, кН | Скорость подъема груза V гр, м/мин | Высота подъема груза Н, м | Продолжительность включения ПВ, % | Номер схемы по рис. 3.2 |
Методика и последовательность выполнения работы
1. Определение усилия в канате механизма подъема:
кН, (3.1)
где – передаточное число или кратность полиспаста;
– общий КПД полиспаста (зависит от количества блоков m конструкции полиспаста и КПД одного блока
,
;
– вес крюковой подвески (
), кН; Q – грузоподъемность лебедки, кН;
– коэффициент сдвоенности (
= 1 при простом полиспасте,
= 2 при сдвоенном полиспасте).
Наибольшее допустимое разрывное усилие в канате:
кН, (3.2)
где – коэффициент запаса прочности, принимаемый для грузовых канатов лебедок с машинным приводом:
пв, % | |||||
![]() | 4,5 | 5,0 | 2,5 | 6,0 | 9,0 |
Режим работы | Самый легкий | Легкий | Средний | Тяжелый | Особо тяжелый |
По найденному разрывному усилию выбираем канат, исходя из данных, приведенных в табл. 3.2. Разрывное усилив каната должно быть В отчет вносятся основные характеристики каната: тип каната, диаметр (мм), расчетный предел прочности проволочек при растяжении (МПа), разрывное усилие (кН), выполняется эскиз выбранного каната, т.е. поперечное сечение и схема свивки.
Таблица 3.2
Канаты ЛК-Р по ГОСТ 2688-80
Диаметр каната, мм | Масса 100 м каната, кг | Временное соп
Поиск по сайту©2015-2025 poisk-ru.ru
Все права принадлежать их авторам. Данный сайт не претендует на авторства, а предоставляет бесплатное использование. Дата создания страницы: 2017-10-12 Нарушение авторских прав и Нарушение персональных данных |
Поиск по сайту: Читайте также: Деталирование сборочного чертежа Когда производственнику особенно важно наличие гибких производственных мощностей? Собственные движения и пространственные скорости звезд |