ВВЕДЕНИЕ
Курсовой проект по деталям машин является первой самостоятельной работой студентов, при выполнении которой приобретаются навыки расчета и конструирования деталей и узлов машин, используются методы, нормы и правила проектирования, обеспечивающие получение надежных, долговечных и экономичных конструкций.
Объектами курсового проектирования являются обычно приводы различных машин и механизмов, например, ленточных и цепных конвейеров, винтовых толкателей, испытательных стендов, приводов общего назначения.
Тематика курсового проектирования имеет вид комплексной инженерной задачи, включающей выбор электродвигателя, кинематические и силовые расчеты, выбор материалов и расчеты на прочность, вопросы конструирования и выполнения конструкторской документации.
В настоящем методическом пособии приведены кинематический и силовой расчеты привода, дана методика выбора электродвигателя, изложены методики проектного и проверочного расчетов цилиндрических и конических зубчатых передач, а также червячных передач с цилиндрическими червяками.
Методика расчета цилиндрических зубчатых передач соответствует ГОСТ 21354 [3]. Методика составления компоновочной схемы редуктора и его конструктивная проработка приведены в пособии [7], а указания по выполнению курсового проекта и по оформлению конструкторской и текстовой документации в пособии [8].
Расчеты рекомендуется выполнять в единицах системы СИ – в м, мм, Н, кН, Н×м, Па, МПа, кВт, м/с. Достаточная точность расчетов: для сил – в десятке чисел Н, для моментов – в десятых долях чисел Н×м и для напряжений – в десятых долях чисел МПа; при этом 0,5 и больше считается за единицу, а меньшая дробь отбрасывается. Для линейных размеров в миллиметрах берутся только целые числа. Лишь в особых случаях нужна большая точность – до десятых и даже до сотых долей миллиметра, например при конусах, винтовой нарезке и в профилировании зубьев.
Исходные данные для расчета указаны в задании на курсовой проект. Недостающие данные студент устанавливает по своему усмотрению и согласовывает их с руководителем курсового проекта.
1 ОБЩИЕ ПОЛОЖЕНИЯ РАСЧЕТА ЗУБЧАТЫХ ПЕРЕДАЧ НА ПРОЧНОСТЬ
Термины и обозначения геометрических, кинематических и силовых параметров соответствуют ГОСТ 16530–83, ГОСТ 16531–83 и ГОСТ 21354–87.
Приняты следующие основные буквенные обозначения расчетных параметров:
F – окружная сила, Н;
К – коэффициент, учитывающий влияние отдельных факторов на расчетную нагрузку;
s – коэффициент запаса прочности;
Т – расчетная нагрузка (вращающий момент), Н×м;
w – удельная окружная сила, Н/мм;
Y – коэффициент, учитывающий влияние отдельных факторов при расчете изгибной прочности;
Z – коэффициент, учитывающий влияние отдельных факторов при расчете контактной прочности;
s – напряжение, МПа..
Приняты следующие основные и дополнительные индексы для буквенных обозначений расчетных параметров, относящихся:
F – к изгибной прочности;
Н – к контактной прочности;
Р – к допускаемому напряжению;
1 – к шестерне;
2 – к колесу.
Отсутствие цифрового индекса означает отношение к любому зубчатому колесу передачи.
2 КИНЕМАТИЧЕСКИЙ РАСЧЕТ ПРИВОДА
2.1 Выбор электродвигателя
В общем машиностроении применяются асинхронные двигатели трехфазного тока с короткозамкнутым ротором, которые непосредственно включаются в сеть (ГОСТ Р 51689). Для двигателей серии АИР предусмотрено множество модификаций и исполнений и они более универсальны.
Двигатели характеризуются номинальной мощностью Рном. (кВт) и асинхронной частотой вращения nс (мин–1) при отсутствии нагрузки (холостой ход).
У нагруженного двигателя частота вращения ротора (nном.) всегда меньше синхронной:
nном = nс (1–s),
где s – скольжение.
Номинальному (паспортному) режиму эксплуатации электродвигателя соответствует номинальная частота nном и номинальная мощность Рном. В этом режиме электродвигатель работает длительное время без перегрева. Момент, соответствующий Рном, является номинальным – Тном.
При выборе электродвигателя необходимо учитывать следующие положения:
– так как для рассчитываемого привода требуемой мощности подходят двигатели с различной синхронной частотой вращения nс = 3000, 1500, 1000, 750 мин–1, то необходимо рассмотреть несколько вариантов и остановиться на оптимальном;
– чем ниже частота вращения вала электродвигателя, тем больше его габаритные размеры, масса и стоимость. Высокооборотные двигатели, напротив, имеют меньшие значения по этим показателям. Поэтому применение тихоходного двигателя с nс = 750 мин–1 возможно при достаточном обосновании;
– согласовать характеристику выбранного двигателя с режимом нагрузки механизма Тпуск/Тном (в соответствии с графиком нагрузки в задании на курсовой проект):
Если это условие не соблюдается для данного типа двигателя, то необходимо выбрать другой тип.
– допустимая перегрузка по мощности для двигателей при переменной нагрузке до 10…12%, при постоянной нагрузке до 5…8%; допустимая недогрузка до 15…20%.
Для того, чтобы оценить работу привода при переменной нагрузке, необходимо привести эту работу к равноценному режиму с постоянной нагрузкой. Среднеквадратичный момент, неизменяемый в течение цикла, эквивалентный по величине потерь действительной переменной нагрузке, определяется по формуле
|

где к 0, к 1, к 2 … к i – доля вращающего момента от номинального момента Т;
а 0, а 1, а 2 … а i – доля от времени t работы передачи за весь срок службы.
Величины коэффициентов к0, кi, а 0, а i указаны в задании на курсовой проект на графике нагрузки.
Величина номинального момента Т определяется по формуле
|
где Ft – окружная сила на выходном валу привода;
D – диаметр ведомого звена, на котором приложена сила Ft.
Среднеквадратичная мощность на ведомом звене за период цикла с учетом пусковых периодов определяется по формуле
|
где u – окружная скорость ведомого звена.
Требуемая мощность двигателя
|
|
hобщ = h1h2h3...,
где h1,h2,h3…– КПД отдельных звеньев кинематической цепи, ориентировочные значения которых приведены в таблице 2.1
Таблица 1 – Ориентировочные значения КПД
Тип передачи | h |
Зубчатая: цилиндрическая закрытая открытая коническая закрытая открытая | 0,96... 0,98 0,94... 0,96 0,95…0,97 0,93…0,95 |
Червячная при передаточном отношении (числе заходов червяка): свыше 30 (z1 = 1) свыше 14 до 30 (z1 = 2) свыше 8 до 14 (z1 = 4) | 0,70... 0,80 0.75... 0,85 0,80... 0,90 |
Цепная открытая | 0,92…0,95 |
Муфта соединительная | 0,98 |
Подшипники качения (одна пара) | 0,99 |
Примечания: 1 Для передач с учетом потерь в подшипниках в одной ступени. 2 В многопоточных редукторах учитывать КПД одного потока. |
Для выбранного двигателя необходимо выписать из ГОСТ Р 51689 [6] следующие данные:
1) обозначение двигателя и его исполнение;
2) номинальная мощность Рном;
3) номинальная частота вращения вала nном с учетом скольжения;
4) диаметр вала d1 (для цилиндрического конца), d2 (для конического конца);
5) длина посадочного участка вала l1 (для цилиндрического конца), l2 (для конического конца).
2.2 Определение передаточного отношения привода и его ступеней
Общее передаточное отношение привода
|

где nвых – частота вращения выходного вала привода, мин–1.
|

|
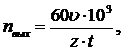
где Dб – диаметр барабана, м;
u – скорость ленты или цепи конвейера, м/с;
z – число зубьев тяговой звездочки конвейера;
t – шаг тяговой цепи, мм.
|
iобщ = iП × iР,
где iП – передаточное отношение ременной или цепной или открытой передачи, входящих в привод;
iР – передаточное отношение редуктора.
Если в схеме привода отсутствуют эти передачи, то
iобщ = iР; iР = iБ × iТ,
где iБ и iТ – передаточные отношения быстроходной и тихоходной ступеней редуктора.
Передаточные отношения iБ (быстроходной) и iТ (тихоходной) ступеней двухступенчатых редукторов определяются по соотношениям, приведенным в таблице 2.
Таблица 2 – Разбивка общего передаточного отношения по ступеням
Тип редуктора | Передаточное отношение быстроходной ступени iБ |
Цилиндрический двухступенчатый, выполненный по развернутой схеме | ![]() |
Цилиндрический двухступенчатый с раздвоенной тихоходной ступенью | ![]() |
Цилиндрический двухступенчатый с раздвоенной быстроходной ступенью | ![]() |
Цилиндрический двухступенчатый соосный с внешним зацеплением | ![]() |
Цилиндрический двухступенчатый соосный с внутренним зацеплением | ![]() |
Коническо–цилиндрический | ![]() |
Цилиндрическо–червячный | ![]() |
Червячно–цилиндрический | iБ = 8, если iр < 50 iБ =iр/6,3, если iр > 50 |
Червячный двухступенчатый | ![]() |
Коническо–червячный | ![]() |
Передаточное отношение тихоходной ступени редуктора
|

В таблице 3 приведены передаточные отношения отдельных видов одноступенчатых передач.
Передаточные отношения редукторов серийного выпуска округляются до стандартных значений ряда:
для цилиндрических и конических передач (ГОСТ 25301–95): 1.25; 1,6; (1,8); 2; (2,24); 2,5; (2,8); 3,15; (3,55); 4; (4,5); 5; (5,6); 6,3; (7,1); 8; (9); 10; (11,2); 12,5; (14); 16; (18); 20; (22,4); 25; (28); 31,5; (35,5); 40; (45); 50; (56); 63; (71); 80; (90); 100.
Для червячных передач с числом витков z1 = 1; 2; 4: (ГОСТ 2144–75):
8; (9); 10; (11,2); 12,5; (14); 16; (18); 20; (22,4); 25; (28); 31,5; (35,5); 40; (45); 50; (56); 63; (71); 80.
Значения без скобок предпочтительны.
Фактическое передаточное отношение всего привода не должно отличаться более, чем на 2,5% при i £ 4,5 и более, чем на 4% при i > 4,5.
Таблица 3 – Передаточные отношения передач
Тип передачи | Значения передаточных отношений | |
оптимальный | наибольший | |
Зубчатая цилиндрическая: тихоходная ступень во всех редукторах при твердости £ 350 НВ 40…56 HRСЭ 56…63 HRCЭ быстроходная ступень в редукторе с развернутой схемой при твердости £ 350 НВ 40…56 HRСЭ 56…63 HRCЭ быстроходная ступень в редукторе соосном при твердости £ 350 НВ 40…56 HRСЭ 56…63 HRCЭ | 2,5 … 5 2,5 … 5 2 … 4 3,15 … 5 3,15 … 5 2,5 … 4 4 … 6,3 4 … 6,3 3,15 … 5 | 6,3 6,3 5,6 7,1 6,3 |
Коробка передач при любой твердости | 1 … 2,5 | 3,15 |
Коническая при твердости £ 350 НВ ³ 40 HRCЭ | 1 … 4 1 … 4 | 6,3 |
Червячная | 16 … 50 | |
Цепная | 1,5 … 4 |
Частота вращения валов коробок передач представляет собой геометрическую прогрессию со знаменателем j. Поэтому если минимальная частота вращения вала n1, то n2 = n1×j; n3 = n1×j2 = n2×j; n4 = n1×j3 = n3×j; ni = n1×ji–1 = ni–1×j;
Наиболее употребительны значения j = 1,41; 1,34; 1,25; 1,18.
2.3 Определение вращающих моментов и частоты вращения валов
Частота вращения валов редуктора
Быстроходная ступень | Тихоходная ступень | |
Вал шестерни Вал колеса | n1 = nном n2 = n1 / iБ | n3 = n2 n4 = n2 / iТ |
|
nвых = n1 / iР× iП = n1 / iБ × iТ × iП
Вращающие моменты на валах редуктора
Быстроходная ступень | Тихоходная ступень | |
Вал шестерни Вал колеса | Т1 = Т / iП × iР × hП × hР × hм × hо Т2 = Т1 × iБ × hБ | Т3 = Т2 Т4 = Т2 × iТ × hТ |
Наличие параметров i и h в формулах определяется по кинематической схеме привода.
Здесь hБ, hТ – КПД зубчатой передачи или червячной передачи в одной ступени;
hо – КПД опор приводного вала.
Результаты расчета, выполненные по подразделу 2.3 для всех валов, свести в таблицу по форме таблицы 4..
Таблица 4 – Кинематические и силовые параметры привода
Номер вала | Частота вращения n, мин–1 | Вращающий момент Т, Н×м |
… |
3 ВЫБОР МАТЕРИАЛОВ. ТЕРМИЧЕСКАЯ И ХИМИКО – ТЕРМИЧЕСКАЯ ОБРАБОТКА
Материал зубчатых колес должен обеспечить: для закрытых передач – высокую сопротивляемость выкрашиванию поверхностных слоев зубьев, для открытых передач – высокую прочность зубьев на изгиб и износостойкость передачи. Этим требованиям отвечают термически обрабатываемые углеродистые и легированные стали. В малонагруженных передачах применяют чугуны и пластмассы. Важнейшими критериями при выборе материалов являются масса и габариты передачи.
Нагрузочная способность передач редукторов лимитируется контактной прочностью. Допускаемые контактные напряжения в зубьях пропорциональны твердости материалов, а несущая способность передач пропорциональна квадрату твердости. Это указывает на целесообразность широкого применения для зубчатых колес сталей, закаливаемых до высокой твердости.
Наибольшую твердость зубьев Н = 55…63 HRCЭ обеспечивают химико-термические упрочнения: поверхностное насыщение углеродом или азотом и последующая закалка.
Цементация – поверхностное насыщение зубьев углеродом с последующей закалкой и низким отпуском, обеспечивает высокую нагрузочную способность и стабильность свойств. Недостатки способа – большое коробление. Применяется для высоконагруженных передач малых и средних размеров разных степеней точности.
Азотирование – поверхностное насыщение зубьев азотом. Оно обеспечивает малую толщину упрочненного слоя, равную 0,2…0,5 мм, что не позволяет применять этот вид упрочнения при работе передачи с ударными нагрузками или интенсивным износом. Этот вид термообработки применяют при необходимости обеспечения высокой стойкости передачи к задиру. Применяется для быстроходовых точных передач.
Нитроцементация – насыщение поверхностных слоев зубьев углеродом и азотом в газовой среде с последующий закалкой и низким отпуском. Этот вид химико-термической обработки обеспечивает высокую прочность, износостойкость и сопротивление заеданию, в связи с чем получает всё более широкое распространение.
Несколько меньшую твердость Н = 48…56 HRCЭ обеспечивает поверхностная закалка токами высокой частоты (ТВЧ). Этот вид термообработки вследствие высокой технологичности широко применяется для средненагруженных зубчатых колес. В связи с тем, что нагреваются слои в течение 20…50 с, деформации при закалке невелики и можно обойтись без последующего шлифования зубьев (однако это понижает точность на одну – полторы степени).
Закалка с нагревом ТВЧ может также применяться для шестерен, работающих с улучшенными колесами Н < 350 НВ, для обеспечения равнопрочности и прирабатываемости.
Недостатком этого вида термообработки для мелкомодульных передач является прокаливание мелких зубьев насквозь, что приводит к их короблению. Поэтому при модуле зацепления до 6 мм рекомендуется применять сталь пониженной прокаливаемости.
Объемная закалка до твердости Н = 45 … 55 HRCЭ, не сохраняет вязкую сердцевину, что приводит к хрупкому разрушению зубьев при динамических нагрузках. Поэтому такой вид термообработки для зубчатых колес не рекомендуется.
Улучшение (закалка с высоким отпуском) применяется для зубчатых колес мелкосерийного и единичного производства при отсутствии жестких требований к габаритам. Чистовое нарезание зубьев улучшаемых колес проводят после термической обработки, что облегчает их изготовление и исключает необходимость их шлифования при обеспечении достаточной точности. Твердость улучшенных колес ограничивают технологическими условиями обеспечения достаточной стойкости инструмента: для небольших колес Н = 260…320 НВ, для крупных колес Н = 200…240 НВ. Применяется для редукторов средних размеров и передач с небольшими нагрузками.
Нормализация (нагрев с охлаждением на воздухе) до твердости Н = 150…220 НВ применяется только для крупногабаритных колес. Позволяет получить лишь низкую нагрузочную способность. Используют для поковок и отливок из среднеуглеродистых сталей; передачи хорошо и быстро прирабатываются. Применяют для редукторов больших размеров в единичном производстве для малонагруженных передач.
В таблице 5 приведены некоторые марки сталей, применяемые для изготовления зубчатых колес, размеры их заготовок и получаемая поверхность при различных видах упрочняющей обработки.
Таблица 5 – Некоторые стали, применяемые для зубчатых колес
Марка стали | Размеры, мм | НВ (сердцевины) | HRCэ, НRC (поверхности) | sв, МПа | sт, МПа | Термическая обработка | |
D* | S* | ||||||
любой | любая | 163 – 192 | – | Нормализация | |||
любой | любая | 179 – 207 | – | Нормализация | |||
235 – 262 | – | Улучшение | |||||
269 – 302 | – | Улучшение | |||||
40Х | 235 – 262 | – | Улучшение | ||||
40Х | 269 – 302 | – | Улучшение | ||||
40Х | 269 – 302 | 45 – 50 | Улучшение + закалка ТВЧ | ||||
35ХМ | 235 – 262 | – | Улучшение | ||||
35ХМ | 269 – 302 | – | Улучшение | ||||
35ХМ | 269 – 302 | 48 – 53 | Улучшение + закалка ТВЧ | ||||
40ХН | 235 – 262 | – | Улучшение | ||||
40ХН | 269 – 302 | – | Улучшение | ||||
Продолжение таблицы 5 | |||||||
40ХН | 269 – 302 | 48 – 53 | Улучшение + закалка ТВЧ | ||||
20ХНМ | 300 – 400 | 56 – 63 | Улучшение + цементация + закалка | ||||
18ХГТ | 300 – 400 | 56 – 63 | Улучшение + цементация + закалка | ||||
12ХН3А | 300 – 400 | 56 – 63 | Улучшение + цементация + закалка | ||||
25ХГМ | 300 – 400 | 56 – 63 | Улучшение + цементация + закалка | ||||
40ХНМА | 269 – 302 | 50 – 56 | Улучшение + азотирование | ||||
35Л | любой | любая | 163 – 207 | – | Нормализация | ||
45Л | 207 – 235 | – | Улучшение | ||||
Примечание – D*, S* –предельные размеры (диаметр и толщина) заготовки. |
4 РАСЧЕТ ЗАКРЫТОЙ ЦИЛИНДРИЧЕСКОЙ ЗУБЧАТОЙ ПЕРЕДАЧИ
4.1 Допускаемые контактные напряжения при расчете на выносливость активных поверхностей зубьев
Допускаемые контактные напряжения sнр определяются отдельно для шестерни и колеса каждой из рассчитываемых передач:
|
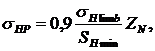
где sнlim b – предел контактной выносливости поверхностей зубьев шестерни (колеса), соответствующий базовому числу циклов напряжений, определяется по таблице 6;
Sн min – минимальный коэффициент запаса прочности: для материалов однородной структуры (улучшение, нормализация, объемная закалка) Sн min = 1,1; при поверхностном упрочнении зубьев (цементация, азотирование, закалка ТВЧ) Sн min = 1,2;
ZN – коэффициент долговечности для шестерни (колеса) (п. 4.1.1).
Таблица 6 – Предел контактной выносливости, sнlim b
Термическая или химико–термическая обработка зубьев | Средняя твердость поверхностей зубьев | Сталь | sнlim b , МПа |
Нормализация, улучшение | Менее 350 НВ | Углеродистая и легированная | sнlim b = 2ННВ+70 |
Объемная и поверхностная закалка | 38 … 50 HRCЭ | sнlim b = 17НHRCэ+200 | |
Цементация и нитроцементация | Более 56 HRCЭ | Легированная | sнlim b = 23НHRCэ |
Азотирование | 550 …750 HV | sнlim b = 1050 |
Расчетные допускаемые контактные напряжения передачи определяются:
1) для прямозубых цилиндрических и конических передач с разностью твердостей HB1сp – НВ2ср = 20…50 по меньшему значению
|
2) для косозубых, с круговым зубом и шевронных передач при разности твердостей HB1сp – НВ2ср ³ 70 или твердости зубьев колеса £ 350 НВ по формуле
|
При этом sHP £ 1,25sHPmin для цилиндрических передач и sHP £ 1,15sHPmin, для конических передач. В противном случае sHP = 1,25sHPmin и sHP = 1,15sHPmin.
Формулой (15) учитывается повышение нагрузочной способности косозубой и шевронной передач при разной твердости зубьев шестерни и колеса.
4.1.1 Определение коэффициента долговечности
Коэффициент долговечности определяется в зависимости от отношения NNE/NHlim b по формуле
|
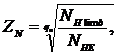
где NНlim b – базовое число циклов контактных напряжений шестерни (колеса), определяется по формуле
|

При твердости Н ³ 550 НВ (HRCЭ ³ 56) базовое число циклов NНlim b = 120×106.
Сравнение чисел твердости НВ (по Бринеллю), HRCЭ (по Роквеллу), HV (по Виккерсу) приведено в таблице 7.
NНЕ – эквивалентное число циклов контактных напряжений на зубьях шестерни (колеса), определяемое в зависимости от режима нагружения и продолжительности работы привода.
Показатель степени в формуле (16)
qН = 6 при NНЕ £ NНlim b;
qН = 20 при NНЕ > NНlim b;
Таблица 7 – Сравнительные значения твердости металлов и сплавов по различным шкалам
Твердость по Бринеллю, МПа | Твердость по Роквеллу, МПа | Твердость по Виккерсу, МПа | Твердость по Бринеллю, МПа | Твердость по Роквеллу, МПа | Твердость по Виккерсу, МПа |
Продолжение таблицы 7 | |||||
|
NНЕ = 60 c×n×t,
где с – число зацеплений зуба за один оборот колеса (с равно числу колес, находящихся в зацеплении с рассчитываемым);
n – частота вращения вала, на котором установлено рассматриваемое зубчатое колесо, мин–1 (таблица 4);
t – время работы (ресурс) передачи за весь срок службы привода, определяемое техническим заданием, ч.
Обычно срок службы привода задается числом лет работы. В этом случае ресурс передачи определяется по формуле
|
где L – срок службы привода, лет;
Кгод – коэффициент использования привода в течение года;
Ксут – коэффициент использования привода в течение суток.
При переменном режиме нагрузки и постоянной частоте вращения вала при любой нагрузке эквивалентное число циклов контактных напряжений
|
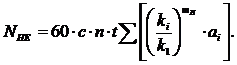
При переменном режиме нагрузки и переменной частоте вращения вала при любой нагрузке эквивалентное число циклов контактных напряжений
|
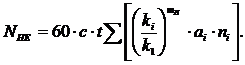
В формулах (20) и (21) величина коэффициентов ki, ai определяется по графику нагрузки, указанном в техническом задании на курсовой проект; показатель степени mH = 3.
При использовании типовых режимов нагружения (рисунок 1) по ГОСТ 21354 эквивалентное число циклов напряжений определяется
NHE = mH × NK; NFE = mF × NK
где mH, mF – коэффициенты, зависящие от типового режима нагружения (таблица 8);
NK – число циклов напряжений соответствует заданному сроку службы при работе передачи с постоянной нагрузкой; определяется по формуле (18), в которой NНЕ = NK.
Рисунок 1– Типовые режимы нагружения:
0 – постоянный; 1 – тяжелый; 2 – средний равновероятный;
3 – средний нормальный; 4 – легкий; 5 – особо легкий
Таблица 8 – Коэффициенты для вычисления эквивалентного
Числа циклов
Номер режима | mH | mF | |
qF = 6 | qF = 9 | ||
0,500 | 0,300 | 0,200 | |
0,250 | 0,143 | 0,100 | |
0,180 | 0,065 | 0,036 | |
0,125 | 0,038 | 0,016 | |
0,063 | 0,013 | 0,004 |
Коэффициент долговечности ZN должен быть в пределах:
1) для материалов однородной структуры (улучшение, нормализация, объемная закалка)
0,75 £ ZN £ 2,6;
2) для материалов неоднородной структуры – при поверхностном упрочнении зубьев (цементация, азотирование, закалка ТВЧ)
0,75 £ ZN £ 1,8.
Если значение коэффициента долговечности ZN выходит за указанные пределы, то он принимается равным соответствующему пределу.
4.2 Допускаемые предельные контактные напряжения
Допускаемые предельные контактные напряжения, не вызывающие остаточных деформаций или хрупкого разрушения поверхностного слоя зубьев при пиковых перегрузках кратковременного действия, определяются по формулам, приведенным в таблице 9.
Расчетным допускаемым предельным контактным напряжением для передачи является меньшее из значений, вычисленных для шестерни и колеса.
Таблица 9 – Допускаемые предельные контактные напряжения, sнр max
Термообработка | Формула для расчета допускаемых предельных контактных напряжений, МПа |
Цементация, нитроцементация, цианирование, закалка ТВЧ | sнр max = 44 НHRCэ |
Азотирование | sнр max = 3HHV |
Нормализация, улучшение, объемная закалка | sнр max = 2,8sT |
Примечание – sT – предел текучести материала зубчатого колеса при растяжении [1,т.1]. |
4.3 Проектный расчет закрытой цилиндрической зубчатой передачи на контактную выносливость активных поверхностей зубьев
Цель расчета – определение основных геометрических размеров зубчатых колес из условия предотвращения усталостного выкрашивания активных поверхностей зубьев. Основной расчетный параметр – межосевое расстояние передачи. Вычислению межосевого расстояния предшествует выбор материалов, термообработки и определение допускаемых напряжений в зубчатой передаче, выбор ряда расчетных коэффициентов.
4.3.1 Выбор материалов, термообработки зубчатых колес ирасчет допускаемых контактных напряжений sНР – (п. 3 и 4.1).
4.3.2 Коэффициент ширины зубчатого венца
|

выбирают по таблице 10 в зависимости от твердости рабочих поверхностей зубьев и расположения опор. Большие значения коэффициента Ybd следует принимать для тихоходных более нагруженных передач, причем в соосных цилиндрических двухступенчатых редукторах для большей загруженности быстроходной малонагруженной ступени эта разница должна быть (2…3) – кратной, соответственно значения коэффициента ширины для быстроходной ступени могут быть меньше указанных в таблице.
Таблица 10 – Рекомендуемые значения коэффициента ширины Ybd
Расположение колеса относительно опор | Твердость рабочих поверхностей зубьев | |
Н1 > 350 НВ Н2 £ 350 НВ или Н1 и Н2 £ 350 НВ | Н1 и Н2 > 350 НВ | |
Симметричное | 0,8 …1,4 (1,6) | 0,4 … 0,9 (1,0) |
Несимметричное | 0,6 … 1,2 (1,25) | 0,3 … 0,6 (0,8) |
Консольное | 0,3 … 0,4 (0,7) | 0,2 … 0,25 (0,45) |
Примечания: 1. Большие значения для постоянных и близких к ним нагрузок, для жестких конструкций валов, установленных на роликоподшипниках. 2. Для шевронных передач, где bw – сумма полушевронов, Ybd можно увеличить в 1,3…1,4 раза. 3. В скобках указаны максимальные значения коэффициента Ybd. |
В формуле (22):
bw = b2 – рабочая ширина зубчатых венцов, равная ширине зубчатого венца колеса, являющегося более узким звеном;
dw1 – начальный диаметр шестерни.
Затем определяется коэффициент ширины венца зубчатого колеса в долях межосевого расстояния передачи
|
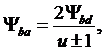
где u – передаточное число передачи;
знак "+" для внешнего зацепления, знак "–" для внутреннего.
Для стандартных редукторов коэффициент Ybа, округляется до значений; 0,1; 0,125; 0,16; 0,20;.0,25; 0,315; 0,40; 0,50; 0,63; 0,80; 1,0; 1,25. Значения 0,63…1,25 –для шевронных передач.
Рекомендуется принимать Ybа = 0,315…0,5 для колес из улучшенных сталей с Н < 350НВ; Ybа = 0,2…0,315 для колес с Н >350 НВ.
Числовые значения ширины зубчатых колес округляются до ближайшего числа из ряда Ra 20 по ГОСТ 6636 [1].
4.3.3 Коэффициент КHb, учитывающий неравномерность распределения нагрузки по длине контактных линий при расчете на контактную выносливость активных поверхностей зубьев. Принимается по рисунку 2 в зависимости от параметра Ybd, твердости и расположения зубчатых колес относительно опор вала.
Рис