МЕТОДИЧЕСКИЕ УКАЗАНИЯ К ЛАБОРАТОРНЫМ РАБОТАМ
ПО ДИСЦИПЛИНЕ «ТЕХНОЛОГИЧЕСКАЯ ОСНАСТКА»
Рекомендовано кафедрой «Конструкторско-технологическая подготовка
машиностроительных производств» 01.010.2013 г. (протокол № 110)
и Ученым советом института «Современные технологии машиностроения, автомобилестроения и металлургии» 06.11.2013 г. (протокол № 4)
для использования в учебном процессе в качестве методических указаний для студентов, обучающихся по направлению 150900.62 – Технология,
оборудование и автоматизация машиностроительных производств»
и студентов очной и заочной форм обучения обучающихся
по направлению 151000 – Конструкторско-технологическое обеспечение
машиностроительных производств»
по специальности 151001 – Технология машиностроения
при изучении дисциплины «Технологическая оснастка»
Ижевск 2013
Лабораторная работа №1
РАЗРАБОТКА КОНСТРУКТИВНЫХ СХЕМ И РАСЧЕТ НА ТОЧНОСТЬ СВЕРЛИЛЬНЫХ ПРИСПОСОБЛЕНИЙ
Цель работы: углубление и расширение навыков конструирования, изучение методики расчета на точность сверлильных приспособлений.
Общие сведения
В условиях автоматизации крупносерийного и массового производств при выполнении сверлильных операций рационально использование специальных приспособлений, в которых кроме базирования и закрепления заготовки осуществляется направление осевого режущего инструмента (сверла, зенкера, развёртки). Применение таких приспособлений позволяет исключить операции разметки, предотвратить увод и повысить радиальную жесткость режущего инструмента, увеличить точность диаметральных размеров и взаимного расположения осей обрабатываемых отверстий. Указанные преимущества обеспечиваются благодаря предусмотренным в конструкции приспособлений направляющим деталям, которые называются кондукторными втулками.
В конструкциях сверлильных приспособлений для крупносерийного и массового производств наиболее распространены сменные кондукторные втулки, которые быстро заменяют при изнашивании. Установку сменных кондукторных втулок производят в кондукторные плиты приспособлений через промежуточные втулки.
Конструкции, размеры и точность изготовления сменных втулок регламентированы ГОСТ 15362-73 и ГОСТ 18431-73, промежуточных – ГОСТ 18433-73 и ГОСТ 18434-73. Отверстия в сменных кондукторных втулках в зависимости от вида обработки (сверление, зенкерование, развёртывание) выполняют с полем допуска F8, G7, G6. Эксцентриситет наружной поверхности втулок относительно внутренней не более 5 мкм. Сопряжение сменных кондукторных втулок с промежуточными втулками производится по посадке H7/g6, H6/g5. Промежуточные втулки устанавливают в кондукторную плиту по посадке H7/n6. Сопряжение рабочей части сверл, зенкеров, разверток с кондукторными втулками осуществляется в системе вала. Для определения предельных зазоров в сопряжении инструмента с втулкой допуски на диаметр инструмента берут по соответствующим стандартам.
Ориентировочный срок изнашивания кондукторных втулок 10000-15000 сверлений. Для уменьшения износа кондукторной втулки между ее нижним торцом и поверхностью заготовки предусматривается зазор е (рис. 1), через который отводится стружка. Этот зазор принимают равным: при сверлении по чугуну, бронзе и другим хрупким материалам;
при сверлении стали и других вязких материалов; 0,3 d при зенкеровании (d – диаметр направляющего отверстия кондукторной втулки).
|
|
|
|


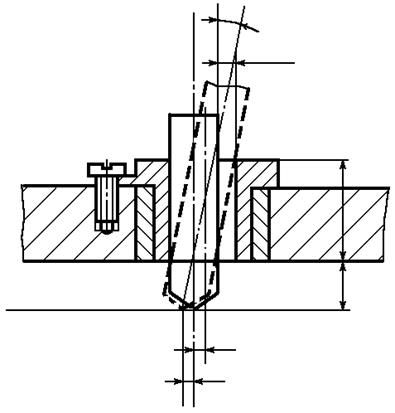
Рис. 1. Схема для расчета перекоса и смещения сверла в кондукторной втулке
От значения е зависит точность положения оси просверливаемого отверстия. Если перекоса сверла нет, то максимальное смещение оси сверла от среднего положения равно половине наибольшего диаметрального зазора
(рис. 1). При перекосе сверла во втулке к параллельному смещению оси отверстия
прибавится смещение
, пропорциональное углу перекоса
и зазору e.
,
где L – высота кондукторной втулки, которая равна (1,5-2) d.
Суммарное смещение инструмента при этом:
.
При разработке чертежа общего вида сверлильного приспособления и его рабочих чертежей конструктор должен устанавливать допуски размеров, которые по точности разбиваются на три группы. К первой группе относятся размеры, непосредственно определяющие точность обработки (например, точность расстояния между осями обработанных отверстий, допустимое отклонение от параллельности или перпендикулярности осей отверстий и др.), а также размеры установочных и направляющих элементов. Во вторую группу входят размеры деталей и сопряжений приспособления, погрешность которых не влияет на точность обработки (размеры сопряжений зажимных устройств и приводов, вспомогательных устройств). В третью – размеры несопрягаемых и необработанных поверхностей деталей приспособления. Наибольшую важность представляет определение допусков на размеры первой группы, которые должны быть отражены в технических требованиях на сборку. Существуют практические рекомендации по выбору этих допусков, согласно которым их принимают в 2-3 раза меньше, чем допуски размеров деталей, выдерживаемых при обработке. Однако более целесообразно определять эти допуски расчетно-аналитическим путём, поскольку только такая постановка способствует повышению точности детали, ресурса эксплуатации приспособления и его экономичности. Методика расчета сверлильных приспособлений на точность, основанная на применении теории размерных цепей, в разделе "Пример оформления отчета" настоящих указаний.
Допуски на размеры второй группы определяют в зависимости от назначения механизма, а также характера и условий работы рассматриваемых сопряжений. Обычно здесь допуски берут по 7-9-му квалитетам точности. Свободные размеры выполняют по 14-му квалитету точности для обработанных и по 16-му для необработанных поверхностей деталей приспособления.
Порядок выполнения работы
1. Изучить методическое руководство по работе, а также ознакомиться с конструкциями сверлильных приспособлений, макеты которых представлены в лаборатории кафедры.
2. Получить у преподавателя операционный эскиз и чертеж детали, в которой выполняется операция сверления, согласовать с ним дополнительные исходные данные, необходимые для разработки конструктивной схемы приспособления (тип производства, модель оборудования, на котором будет производиться операция, материал заготовки, тип приспособления и др.), и сформулировать техническое задание на проектирование.
3. Выбрать тип установочных и зажимных элементов, вид привода, тип и размеры направляющих элементов.
4. Разработать конструктивную схему приспособления, реализующую принятую схему базирования и закрепления заготовки.
5. Установить размеры приспособления, непосредственно определяющие точность обработки на операции сверления, и путем расчёта приспособления на точность определить допуски выполнения этих размеров. Сформулировать технические требования на сборку приспособления.
6. Определить допуски размеров и выполнить эскизы деталей приспособления, определяющие точность обработки.