5.1. Общие сведения. Получение изделий и фасонных заготовок для них заливкой жидкого металла в литейные формы с его последующим затвердеванием называют литейным производством. Получаемая отливка имеет конфигурацию и размеры, придаваемые ей литейной формой. Преимущества литейного производства: 1). Получение отливок любой сложности из труднообрабатываемых материалов – чугуна, высокоуглеродистой стали и т.п. 2). Неограниченная масса отливок (от нескольких граммов до сотен тонн). 3). Конфигурация и размеры отливок близки к форме и конечным размерам изделия, т.е. обладают малыми припусками на обработку, и зачастую не требуют обработки. 4). Максимальный КИМ и минимальная стоимость; отходы могут быть переплавлены и вновь залиты в литейную форму.
В конструкциях самолетов применяются литые детали из высокопрочных сталей и титановых сплавов. Наиболее нагруженные детали реактивных двигателей (лопатки турбины, соплового аппарата и др.) до недавнего времени могли быть изготовлены только литьем.
5.2. Схема технологического процесса литейного производства.
Разработка чертежа отливки и методики литья
|
Разработка чертежей оснастки (моделей, стержневых ящиков и т.д.)
|
Приготовление формовочных смесей
|
Шихта – это материалы, загружаемые в плавильные печи: первичные металлы, сплавы, лом и отходы (поступающие со стороны и собственного производства). Металлы и сплавы поставляются в виде чушек, прутков, листов и гранул. Все шихтовые материалы имеют сертификаты, в которых указываются по ГОСТу марка материала, химический состав его основных компонентов и примесей. Перед использованием все материалы очищают от грязи и влаги.
Флюсы – это неметаллические материалы, применяемые для защиты расплава от окисления, газонасыщения и для удаления вредных примесей. Температура плавления флюсов должна быть ниже температуры плавления шихты. Кроме того, флюсы должны обладать хорошей текучестью в расплавленном состоянии и не взаимодействовать с футеровкой (рабочим слоем) печи. Для приготовления флюсов используют кварцевый песок, кальцинированную соду, углекислый кальций, различные соли, бой стекла и другие материалы.
В процессе плавки возможен угар металла – его потери за счет испарений, вызванных образованием соединений отдельных компонентов сплава с различными газами. В результате изменится количественный состав компонентов сплава и, следовательно, его свойства. В целях уменьшения угара необходимо как можно меньше перегревать металл, как можно быстрее вести процесс плавки и не передерживать готовый расплав в печи. Поэтому для получения сплава с определенным химическим составом необходимо перед плавкой произвести расчет количества загружаемой шихты. Для расчета берут химический состав получаемого сплава и исходных шихтовых материалов. Содержание того или иного элемента в шихте определяют по формуле:
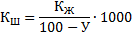
где КШ и КЖ - содержание элемента в шихте и в жидком сплаве, %; У - угар элемента при плавке, % (из таблиц его средних значений для каждого элемента).
5.3. Плавильные агрегаты. Печи шихтного типа (пламенные, на коксе) – вагранки применяются в основном для плавки чугуна. В зависимости от диаметра печей их производительность – от 0,5 до 30 т/ч, а продолжительность плавки составляет от 2 до 22 часов. Для получения отливок высокого качества в авиационной промышленности применяют главным образом электрические плавильные агрегаты, в которых нагрев и плавка производятся благодаря преобразованию электрической энергии в тепловую. По сравнению с пламенными электропечи имеют следующие достоинства: - более высокий КПД (до 0,9), - более высокое качество металла, благодаря отсутствию контакта с продуктами сгорания, - значительное снижение угара металла, - возможность автоматического регулирования температуры процесса, - лучшие санитарно-гигиенические условия труда.
В зависимости от способа преобразования электрической энергии используются: 1). Тигельные печи с нагревательными элементами (печи сопротивления) для плавки алюминиевых, магниевых, цинковых сплавов при температуре до 850°С. 2). Индукционные печи высокой частоты для плавки тех же сплавов и чугуна. 3). Дуговые печи с вольфрамовым или графитовым электродом для плавки титановых и других жаропрочных сплавов. 4). Электронно-лучевые печи для плавки тугоплавких сплавов на основе молибдена, ниобия и вольфрама. Высокую температуру нагрева металла обеспечивает поток электронов, излучаемых высоковольтной электронной пушкой. Электронный нагрев обеспечивает желаемую концентрацию тепла и скорость плавки, что позволяет использовать этот метод для переработки разнородной шихты: гранул, лома, отходов. 5). Плазменно-дуговые и плазменно-индукционные печи. Для получения плазмы (высокоионизированного электрически нейтрального газа, существующего в природе при температуре выше 10000°К) используют электрический разряд и индукционный нагрев в среде инертного газа. Особенность метода – получение высоких регулируемых температур, большая скорость плазменного потока и экономичность.
5.4. Формовка – технологический процесс изготовления литейных форм. Формы бывают разовые (сырые, сухие, корковые, изготовленные из полимеров, песчано-смоляных, стекольных и кварцевых химически твердеющих смесей) и постоянные, многократно используемые, изготовленные из чугуна, стали и алюминиевых сплавов: - кокили, в которые металл поступает под действием собственной силы тяжести, - пресс-формы для литья под давлением и - изложницы для центробежного литья (для получения деталей тел вращения). Для предохранения постоянных форм от разрушения применяют опоки – контейнеры, изготовленные из чугуна, стали и алюминиевых сплавов. Для изготовления форм больших размеров в литейных цехах применяют кессоны – глубокие бетонированные ямы. Для изготовления отливок небольших размеров применяется безопочная формовка.
Формовочные смеси должны обладать высокой прочностью, газопроницаемостью (способностью пропускать через стенки формы газ, образующийся при заливке) и огнеупорностью.
Отдельно изготовляемыми частями литейной формы являются стержни, предназначенные для образования в отливке углублений, внутренних полостей и отверстий. Так же, как и при штамповке, для облегчения выемки изделия из формы их стенки делают с уклонами, называемыми формовочными уклонами.
5.5. Литье. Один из самых прогрессивных видов получения отливок – литье под давлением. Сущность процесса состоит в том, что в стальную пресс-форму под большим давлением и с большой скоростью вводится расплавленный металл. При этом происходит мгновенной заполнение всей полости формы любой конфигурации. Для производства ответственных деталей авиационной техники применяется метод литья под давлением в вакууме из алюминиевых и титановых сплавов. Для производства крупногабаритных тонкостенных деталей фюзеляжей самолетов используется метод литья выжиманием, когда при кристаллизации сплава стенки формы сжимаются, выжимая избытки жидкого металла. Литьем под давлением можно получать детали с отверстиями диаметром от 1мм, с резьбой шагом от 1мм и с толщиной стенок от 1мм (причем, чем меньше толщина стенок, тем выше удельная прочность вследствие быстрого охлаждения металла).
Большинство машин литья под давлением работают по автоматическому циклу, поскольку весь цикл литья длится несколько секунд. В современных литейных цехах серийного и массового производства практически все процессы (в том числе и контроль) литья автоматизированы с помощью транспортеров, формовочных машин и автоматов по производству отливок.