Введение.
Изм. |
Лист |
№ докум. |
Подпись |
Дата |
Лист |
ФГБОУ ВПО РГАТУ |
Разраб. |
Провер. |
Иванова И.А. |
Реценз. |
Н. Контр. |
Утверд. |
Метрология, стандартизация, сертификация. |
Лит. |
Листов |
Качественные показатели современных изделий машиностроения (точность, долговечность, надёжность и др.) в значительной мере зависят от правильности выбора посадок, т.е. характера сопряжения деталей, и правильность выбора допусков формы и расположения.
Изделия машиностроения – не простая совокупность деталей. В собранном изделии детали находятся во взаимосвязи и взаимозависимости. По этой причине при выборе посадок, допусков размеров деталей, а также допусков формы и расположения следует учитывать: назначение деталей в сборочной единице, роль отдельных поверхностей, влияние отклонений размеров и т.п.
Качество и конкурентоспособность выпускаемой продукции находятся в прямой зависимости от точности её изготовления, от количества и качества измерений, с помощью которых контролируются как значения параметров, характеризующих эту продукцию, так и значения параметров внешних воздействующих факторов. Таким образом, возникают задачи обеспечения точности изготовления продукции и обеспечения единства измерений и достоверности испытаний, решение которых предусматривает соблюдение требований стандартов к точности изготовления и единства методов и средств измерений. Отсюда следует, что обеспечение высокого качества выпускаемой продукции возможно только при совместной деятельности в области стандартизации и её раздела взаимозаменяемости, метрологии и сертификации.
Определение зазоров и натягов в соединениях.
Изм. |
Лист |
№ докум. |
Подпись |
Дата |
Лист |
Контрольная работа по МСС РГСХА |
Задание 1. Определить зазоры и натяги в соединениях:
а) б)
в)
Рассмотрим задание а: .
1.1. Согласно приложения 4 – 7 находим значения предельных отклонений размеров соединяемых деталей и определяем их предельные размеры и допуски:
а) для отверстия H7: 55+0,030
Dmax = DH + ES = 55 + 0,030 = 55,030 мм
Dmin = DH + EI = 55 + 0,000 = 55,000 мм
TD = Dmax – Dmin = 55,030 – 55,000 = 0,030 мм = 30 мкм
б) для вала g6:
dmax = dH + es = 55 + (–0,010) = 54,990 мм
dmin = dH + ei = 55 + (–0,029) = 54,971 мм
TD = Dmax – Dmin = 54,990 – 54,971 = 0,019 мм = 19 мкм
1.2. Определим предельные и средние зазоры и допуски посадок:
Smax = Dmax – dmin = ES – ei = 0,030 – (–0,029) = 0,059 мм = 59 мкм
Smin = Dmin –dmax = EI – es = 0,000 – (–0,010) = 0,010 мм = 10 мкм
Sc = 0,5(Smax + Smin) = 0,5(0,059 + 0,010) = 0,0345 мм = 34,5 мкм
TS = Smax – Smin = TD + Td =0,030 + 0,019 = 0,049 мм = 49 мкм
Данная посадка выполняется с зазором.
1.3. Выберем шероховатость сопрягаемых поверхностей и вид окончательной механической обработки деталей по , приложение 10 и 11.
Для отверстия H7:
- шероховатость: Rа = 3,2 мкм;
- вид обработки: чистовое протягивание.
Для вала g6:
- шероховатость: Rа = 1,6 мкм;
- вид обработки: обычное полирование.
1.4. Построим схему расположения полей допусков отверстия и вала с указанием на них номинальных размеров, предельных отклонений, предельных и средних зазоров (рис.1)
1.5. Вычертим эскизы соединений (в узле и подетально) и проставим условные обозначения и цифровые значения расположения полей допусков и шероховатостей (рис.2).
Изм. |
Лист |
№ докум. |
Подпись |
Дата |
Лист |
Контрольная работа по МСС РГСХА |
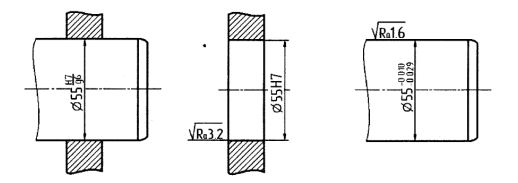
Рис.2. Эскизы соединения и соединяемых деталей.
Рассмотрим задание б: .
1.1 1.1. Согласно приложения 4 – 7 находим значения предельных отклонений размеров соединяемых деталей и определяем их предельные размеры и допуски:
а) для отверстия H8: 78+0,046
Dmax = DH + ES = 78 + 0,046 = 78,046 мм
Dmin = DH + EI = 78 + 0,000 = 78,000 мм
TD = Dmax – Dmin = 78,046 – 78,000 = 0,046 мм = 46 мкм
б) для вала u8:
dmax = dH + es = 78 + 0,148 = 78,148 мм
dmin = dH + ei = 78 + 0,102 = 78,102 мм
Td = dmax – dmin = 78,148 – 78,102 = 0,046 мм = 46 мкм
1.2. Определим предельные и средние натяги и допуски посадок:
Nmax = dmax –Dmin = es – EI = 0,148 –0,000 = 0,148 мм = 148 мкм
Nmin = dmin –Dmax = ei – ES = 0,102 –0,046 = 0,056 мм = 56 мкм
Nc = 0,5(Nmax + Nmin) = 0,5(0,148 + 0,056) = 0,102 мм = 102 мкм
TN = Nmax – Nmin = TD + Td =0,046 + 0,046 = 0,092 мм = 92 мкм
Данная посадка выполняется с натягом.
1.3. Выберем шероховатость сопрягаемых поверхностей и вид окончательной механической обработки деталей по , приложение 10 и 11.
Для отверстия Н8:
- шероховатость: Rа = 3,2 мкм;
- вид обработки: чистовое протягивание.
Для вала u8:
- шероховатость: Rа = 3,2 мкм;
- вид обработки: чистовое растачивание.
1.4. Построим схему расположения полей допусков отверстия и вала с указанием на них номинальных размеров, предельных отклонений, предельных и средних натягов (рис.3).
Изм. |
Лист |
№ докум. |
Подпись |
Дата |
Лист |
Контрольная работа по МСС РГСХА |
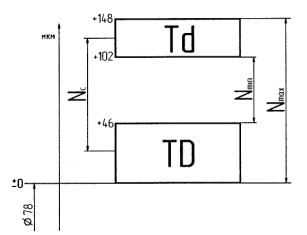
Рис. 3 Схема расположения полей и допусков посадки с натягом.
1.5. Вычертим эскизы соединений (в узле и подетально) и проставим условные обозначения и цифровые значения расположения полей допусков и шероховатостей (рис.4).
Рис. 4 Эскизы соединения и соединяемых деталей.
Рассмотрим задание в:
1.1. Согласно приложения 4 – 7 находим значения предельных отклонений размеров соединяемых деталей и определяем их предельные размеры и допуски:
а) для отверстия М7: 25-0,021
Dmax = DH + ES = 25 + 0,000 = 25,000 мм
Изм. |
Лист |
№ докум. |
Подпись |
Дата |
Лист |
Контрольная работа по МСС РГСХА |
Dmin = DH + EI = 25 + (–0,021) = 24,979 мм
TD = Dmax – Dmin = 25,000 – 24,979 = 0,021 мм = 321 мкм
б) для вала h6:
dmax = dH + es = 25 + 0,000 = 25,000 мм
dmin = dH + ei = 25 + (–0,013) = 24,987 мм
Td = Dmax – Dmin = 25,000 – 24,987 = 0,013 мм = 13 мкм
1.2. Определим предельные и средние зазоры (натяги) и допуски посадок:
Smax = Dmax – dmin = ES – ei = 0,000 – (–0,013) = 0,013 мм = 13 мкм
Nmax= dmax – Dmin = es – EI = 0,000 – (–0,021) = 0,021 мм = 21 мкм
Nc = 0,5(Nmax – Smax) = 0,5(0,021 – 0,013) = 0,004 мм = 4 мкм
TN(S) = Smax + Nmax = TD + Td =0,013 + 0,021 = 0,034 мм = 34 мкм
Данная посадка переходная.
1.3. Выберем шероховатость сопрягаемых поверхностей и вид окончательной механической обработки деталей по , приложение 10 и 11.
Для отверстия М7:
- шероховатость: Rа = 3,2 мкм;
- вид обработки: чистовая притирка.
Для вала h6:
- шероховатость: Rа = 1,6 мкм;
- вид обработки: чистовая притирка.
1.4. Построим схему расположения полей допусков отверстия и вала с указанием на них номинальных размеров, предельных отклонений, предельных и средних зазоров (натягов) (рис.5).
Изм. |
Лист |
№ докум. |
Подпись |
Дата |
Лист |
Контрольная работа по МСС РГСХА |
1.5. Вычертим эскизы соединений (в узле и подетально) и проставим условные обозначения и цифровые значения расположения полей допусков и шероховатостей (рис.6).
Рис.6 Эскизы соединения и соединяемых деталей.
Расчёт и выбор посадок.
При выборе переходных посадок необходимо учитывать то, что для них характерна возможность получения как натягов, так и зазоров. Чем больше вероятность получения натяга, тем более прочной является посадка. Для более точного центри
Изм. |
Лист |
№ докум. |
Подпись |
Дата |
Лист |
Контрольная работа по МСС РГСХА |
Посадки H/n, N/h являются наиболее прочными из переходных посадок. Их назначают для соединений, передающих большие усилия, при наличии ударов и вибраций, преимущественно для соединений, разбираемых редко, обычно только при капитальном ремонте изделия.
Переходные посадки предусмотрены только в квалитетах 4 – 8. Точность отверстия в них должна быть на один квалитет ниже точности вала. Посадки повышенной точности выполняются по 4, 5, 6-му квалитетам, пониженной – по 7-му и 8-му квалитетам.
Трудоемкость сборки и разборки соединений с переходными посадками, так же как и характер последних, во многом определяется вероятностью получения в них натягов и зазоров, при расчёте которой обычно исходят из нормального закона распределения.
Задание 2. Рассчитайте и выберите переходную посадку для следующих условий: d=45 мм; детали соединения неподвижны; масса их небольшая, разборка производится редко.
2.1. По заданным техническим и эксплуатационным требованиям, предъявляемым к соединению, по приведённым выше сведениям, согласно приложение 32 таблица 4, выбираем необходимую посадку и рассчитываем Smax, Nmax, Nc, TD, Td.
Выберем соединение .
а) для отверстия H7: 45+0,025
Dmax = DH + ES = 45 + 0,025 = 45,025 мм
Dmin = DH + EI = 45 + 0,000 = 45,000 мм
TD = Dmax – Dmin = 45,025 – 45,000 = 0,025 мм = 25 мкм
б) для вала n6:
dmax = dH + es = 45 + 0,033 = 45,033 мм
dmin = dH + ei = 45 + 0,017 = 45,017 мм
Td = dmax – dmin = 45,033 – 45,017 = 0,016 мм = 16 мкм
в) определим предельные и средние зазоры и допуски посадок:
Smax = Dmax – dmin = ES – ei = 0,025 – 0,017 = 0,008 мм = 8 мкм
Nmax= dmax – Dmin = es – EI = 0,033 – 0,000 = 0,033 мм = 33 мкм
Nc = 0,5(Nmax – Smax) = 0,5(0,033 – 0,008) = 0,0125 мм = 12,5 мкм
TN(S) = Smax + Nmax = TD + Td =0,025 + 0,016 = 0,041 мм = 41 мкм
2.2. Определим среднее квадратическое отклонение натяга и предел интегрирования
:
По найденному значению находим по
, приложение 14, значение функции Ф (
) и определяем вероятность появления соединений с натягом и зазором:
при ;
вероятность натяга:
;
вероятность зазора:
процент соединения с натягом:
процент соединения с зазором:
2.4. Построим дифференциальную функцию распределения натягов и зазоров (рис.7)
Изм. |
Лист |
№ докум. |
Подпись |
Дата |
Лист |
Контрольная работа по МСС РГСХА |
Рис.7 Распределение зазоров и натягов в соединении