1. Обточка поверхности А и расточка поверхности Б на величину 2-3 мм для снятия литейной корки. Вырезание контрольного кольца.
2. Нарезка колец с припуском на обработку.
3. Прорезка замка на величину теплового зазора δ с припуском на припиловку.
4. Растянуть разрезанные кольца на величину 1,2·А, насадить на оправку и закрепить.
5. Заложить оправку с кольцами в термическую печь до 350-450 ˚С, поднять температуру до 580-620 ˚С и выдержать при этой температуре кольца 0,5-1 ч с последующим охлаждением на открытом воздухе.
6. Снять кольца с оправки и обжать каждое кольцо 2-3 раза до соприкосновения стыков.
7. Шлифовать торцы колец предварительно, с двух-трех установок на каждый торец.
8. Набрать кольца в барабан, насадить на оправку и сжать с торцов, после чего барабан убрать, а кольца, собранные на оправку, обточить по наружному диаметру в размер по чертежу.
9. Снять кольца с оправки и, последовательно устанавливая каждое кольцо в специальное приспособление, расточить внутреннюю поверхность, обточить и расточить с двух сторон фаски 1х45˚.
10. Проверить каждое кольцо в кольце-калибре или фальшцилиндре с припиловкой замка до получения заданного теплового зазора δ.
11. Шлифовать торцы кольца окончательно и в размер.
12. Размагнитить кольца.
13. Нанести покрытие для улучшения износостойкости.
Лист |
КР44.180403.65.06.ПЗ |
Лит |
№ докум. |
Изм. |
Подп. |
Дата |
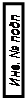

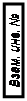
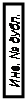

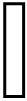

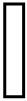
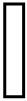

Рекомендации по повышению надежности и улучшению износостойкости поршневых колец
Повышение упругости
Для повышения упругих свойств кольца и стойкого сохранения упругости в эксплуатации при не очень высоких эксплуатационных температурах, можно непосредственно после термофиксации провести насечку внутренней поверхности кольца. Этот процесс осуществляют на специальных станках или вручную. Начинают насечку от замка, все время увеличивая силу удара к середине кольца.
Улучшение износостойкости
Готовые кольца необходимо подвергнуть фосфатированию для создания покрытия толщиной 3-6 мкм, улучшающего приработку. Плёнка сохраняет устойчивость до 400–500 °С и хорошо удерживает смазку, что снижает коэффициент трения. Фосфатирование осуществляется погружением изделий в нагретый до 90–100 °С раствор фосфатов железа, марганца, цинка и кадмия. Промышленность выпускает готовый концентрат солей «мажеф» (сокращенно от марганец, железо, фосфор). Обычно процесс продолжается около 1 ч. После Фосфатирование и сушки изделие пассивируется в слабом хроматном растворе. Применяется также электрохимическое фосфатирование (на переменном или постоянном токе); длительность такой обработки 15–20 мин.
Лист |
КР44.180403.65.06.ПЗ |
Лит |
№ докум. |
Изм. |
Подп. |
Дата |
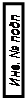

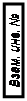
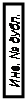

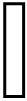

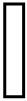
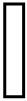

Список используемой литературы
1. Блинов И.С. Справочник технолога механосборочного цеха судоремонтного завода.Изд. 5-е, перераб. и доп. М.: Транспорт, 1979. – 704с.
2. Косилова А.Г., Мещеряков Р.К., Справочник технолога. Том 1.-М., Машиностроение, 1973 г.
3. Косилова А.Г., Мещеряков Р.К., Справочник технолога. Том 2.-М., Машиностроение, 1973 г.
4. Гуревич И.М., Зеличенко А.Я., Кулик Ю.Г. Под ред. И.М.Гуревича.Технология судостроения и судоремонта. Учебник для ВУЗов водн.трансп. М.:Транспорт, 1976. – 416с.
5. Дорошенко П.А., Рохлин А.Г. Технология производства судовых энергетических установок: Учебник.-Л., Судостроение, 1988. – 440 с.
Лист |
КР44.180403.65.06.ПЗ |
Лит |
№ докум. |
Изм. |
Подп. |
Дата |
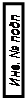

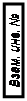
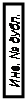

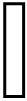

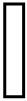
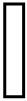
