Управление движением материальных потоков в производстве может осуществляться с использованием модели «воронки». Воронка служит для упрощенного описания процесса движения материальных потоков в отдельных звеньях логистической цепи. В качестве реального объекта модели могут выступать: цех, участок, рабочее место, система складов или транспортная система.
Принципиальная схема прохождения материальных потоков через «воронку» представлена на рисунке 8.
Заказы в обработке |
Поступление заказов |
Максимальная пропускная способность Приоритетные закупки |
Выбытие заказов |
Средняя длительность цикла заказа ТЦ |
Средний запас Zн ср |
Запуск |
Выпуск |
Исследуемый период Время |
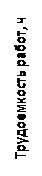
Рис. 8. Воронкообразная модель логистической системы
Поступающие в воронку заказы изображены на рисунке в виде шаров различной величины. Объем шара соответствует трудоемкости заказа. Система имеет максимальную пропускную способность (мощность), которая достигается при условии рационального планирования материальных потоков (распределения заказов по отрезкам планового периода и формирования очередности выполнения работ). Процесс поступления и выбытия заказов изображается в виде ломаной лини «запуска» или «выпуска», средняя длительность цикла заказа устанавливается исходя из объема незавершенного производства и реальной пропускной способности системы по формуле:
, (3)
где ТЦ – длительность цикла выполнения заказа;
Zн ср – средняя величина незавершенного производства;
Nср – усредненное число выполненных заказов в единицу времени.
Последовательность прохождения заказов через звенья логистической цепи устанавливается с помощью правил распределения работ (обслуживания заказов), предписывающих те или иные приоритеты при выполнении работ. В практике управления материальными потоками используются правила приоритетов, позволяющие сократить время ожидания и среднюю длительность цикла выполнения заказа:
|
FIFO – «первый пришел – первый ушел», т.е. наивысший приоритет придается заказу, который раньше других поступил в систему;
LIFO – «последний пришел – первый обслужен», т.е. наивысший приоритет придается заказу, поступившему на обслуживание последним. Это правило наиболее часто применяется в системах складирования в тех случаях, когда материалы уложены таким образом, что достать их можно только сверху;
SPT – «правило кратчайшей операции», наивысший приоритет придается заказу с наименьшей длительностью выполнения в данном звене. В тех случаях, когда целью управления материальными потоками является обеспечение установленных сроков поставки, используются правила управления, учитывающие информацию о времени выполнения заказов;
MST – «минимальный резерв времени», наивысший приоритет придается заказу, имеющему наименьшее резервное время. Резервное время определяется как разность между сроком выполнения заказа и сроком, к которому заказ может быть выполнен при отсутствии межоперационного пролеживания;
EDD – «наиболее ранний срок исполнения», т.е. наивысший приоритет придается заказу с наиболее ранним сроком выполнения.
ОТВЕТИТЬ НА ВОПРОСЫ
1. Функции производственной логистики.
|
2. Воронкообразная модель логистической системы.
3. Правила приоритетов в выполнении заказов.
4. Выталкивающая и вытягивающая системы управления.
5. Организация и управление материальными потоками.
6. Системы управления материальными потоками.
Рекомендуемая литература
1. Гаджинский A.M. Логистика Учебник для высших и средних специальных учебных заведений - 7-е издание, М.: 2013 г. – 420 с.
2. Логистика: Учеб. пособие/под ред. Б.А. Аникина М.: ИНФРА - М, 2013 г.– 432 с.
Дополнительные источники:
3. Джонсон, Джеймс, Вуд, Дональд, Ф., Вордлоу, Дениэл, Л., Мерфи - мл., Поль, Р. Современная логистика, 7-е издание: Пер. с англ. - М.: Издательский дом «Вильяме», 2015. - 624 с.