Глава 3. Основы проектирования деталей машин
Основные понятия
Деталь – изделие, изготовленное из однородного по наименованию и марке материала без применения сборочных операций.
Сборочная единица – изделие, составные части которого подлежат соединению между собой сборочными операциями на предприятии-изготовителе.
Механизм – совокупность сборочных единиц и деталей, которые находятся в определённой взаимосвязи и обеспечивают необходимое функционирование.
Привод – устройство для приведения в действие машин и механизмов. Он состоит из двигателя, передаточного механизма и системы управления.
Машина – система, осуществляющая механическое движение, необходимое для выполнения рабочего процесса.
Машины делятся на транспортные, энергетические, технологические и др.
Классификация деталей машин
Соединения предназначены для фиксации взаимного положения деталей и объединения их в сборочные единицы и узлы, например, сварные, заклёпочные.
Передачи осуществляют передачу энергии от двигателя к исполнительному органу:
– передачи зацеплением (цилиндрические, конические, червячные, цепные), трением (ременные, фрикционные);
– элементы, преобразующие движение (рычажные, кулачковые).
Несущие и базирующие элементы:
– валы и оси;
– подшипники;
– направляющие, поддерживающие поступательно движущиеся детали;
– корпусные и несущие детали – основные части редуктора, воспринимающие нагрузки.
Особые группы:
– устройства для защиты от загрязнений и смазывания (уплотнения, кожухи, крышки);
– упругие элементы (пружины, рессоры, амортизаторы).
Требования к деталям машин
Работоспособность – способность изделия выполнять заданные функции с параметрами, установленными в техническом задании.
Техническое обслуживание – этап эксплуатации, направленный на поддержание надёжности и готовности технических объектов и их элементов.
Надёжность – свойство изделия выполнять в течение заданного времени или заданной наработки свои функции, сохраняя в заданных пределах эксплуатационные показатели.
Долговечность – свойство изделия, позволяющее ему сохранять работоспособность до предельного состояния с необходимыми перерывами для технического обслуживания и ремонта.
Ремонт – совокупность технических мероприятий, осуществляемых с целью восстановления работоспособности устройства.
Механические передачи
Механической передачей называется механизм, передающий энергию от двигателя к исполнительному органу машины с преобразованием скоростей, сил и моментов, а иногда характера и закона движения.
Редуктор – передаточный механизм, служащий для понижения частоты вращения, увеличения вращающего момента. Мультиприкатор – механизм, повышающий частоту вращения.
На рис. 3.1 показаны редукторы:
а – одноступенчатый с цилиндрическими зубчатыми колесами;
а) |
Рис.3.1 |
д) |
г) |
в) |
б) |
б – одноступенчатый с коническими зубчатыми колесами;
в– червячный;
г – двухступенчатый коническо-цилиндрический;
д – двухступенчатый соосной схемы (оси валов I и III совпадают).
Двухступенчатые редукторы обеспечивают получение больших передаточных отношений i, от 6,3 до 64.
Корпуса редукторов обычно делают составными из двух частей с осевой или радиальной сборной. При осевой сборке разъем корпуса выполняют перпендикулярно осям валов (рис. 3.2а), а при радиальной – по плоскости, проходящей через оси валов (рис. 3.2б).
а) |
б) |
Рис.3.2 |
О |
О |
Разъем |
К |
К |
На рис. 3.3 показан двухступенчатый редуктор с радиальной сборкой и цилиндрическими колёсами, типичный для общего машиностроения. Корпус состоит из основания 5 и крышки 4. Они соединены болтами 6 и штифтами 9. Крышка 3 с отдушиной 2 служит для осмотра и заливки масла, пробка 8 для слива масла, маслоуказатель 7 для определения уровня масла, рем-болты 1 для переноса подъемным краном. Внутри корпуса располагаются тихоходный вал 11 с зубчатым колесом 10, промежуточный вал 14 с нарезанными зубьями и насаженным зубчатым колесом, быстроходный вал с нарезанными зубьями 15 и подшипники.
На рис.3.4 представлен внешний вид редукторов:
а – цилиндрического двухступенчатого; б – одноступенчатого косозубого; одноступенчатого конического.
По способу передачи движения от ведущего звена к ведомому различают передачи трением и зацеплением. Передачи зацеплением с непосредственным контактом: зубчатые, червячные, цепные.
Рис.3.3 |
Уровень масла |
Рис.3.4 |
б) |
а) |
в) |
На рис. 3.5 показаны передачи:
а – цилиндрическая прямозубая передача с параллельными осями и внешним зацеплением;
а) |
Рис. 3.5 |
б) |
в) |
г) |
д) |
е) |
Рис. 3.5 |
в – косозубая цилиндрическая передача с внешним зацеплением;
г – прямозубая коническая передача с пересекающимися осями;
д – косозубая коническая передача;
е – червячная передача.
Цилиндрические зубчатые передачи
Это передачи с параллельными осями. Они бывают с прямым, косым зубом и шевронные. Передачи с шевронным и косым зубом имеют преимущества: большая прочность зуба, большая плавность зацепления и малый шум, меньшие динамические нагрузки.
На рис. 3.6 показана передача с наружным зацеплением, где n 1, n 2 – частоты вращения шестерни 1 и колеса 2, z 1 и z 2 – числа их зубьев, d 1 и d 2 – диаметры делительных окружностей.
Отношение частот вращения называется передаточным отношением i 12. В отличие от передаточного числа u 12 оно имеет знак.
Из очевидных равенств скоростей точек колеса и шестерни, расположенных на делительных окружностях
,
получаем передаточное отношение
,
Чаще всего используют зубчатые колёса с эвольвентным зацеплением, которое обеспечивает постоянное передаточное отношение и малое скольжение зубьев. Рабочая поверхность зуба имеет форму эвольвенты. Эвольвентой называется кривая, которую описывает точка N 1, образующей прямой N - N при перекатывании без скольжения по окружности (рис. 3.7). Окружность, по которой перекатывается образующая кривая N - N называется основной. Радиус кривизны эвольвенты переменный. При увеличении радиуса основной окружности до бесконечности радиус кривизны эвольвенты в любой ее точке также становится бесконечно большим, т.е. основная окружность и эвольвента превращаются в прямые линии. Эвольвентное зубчатое колесо превращается в зубчатую рейку с прямолинейным профилем зуба.
Рис.3.7 |
Рис.3.6 |
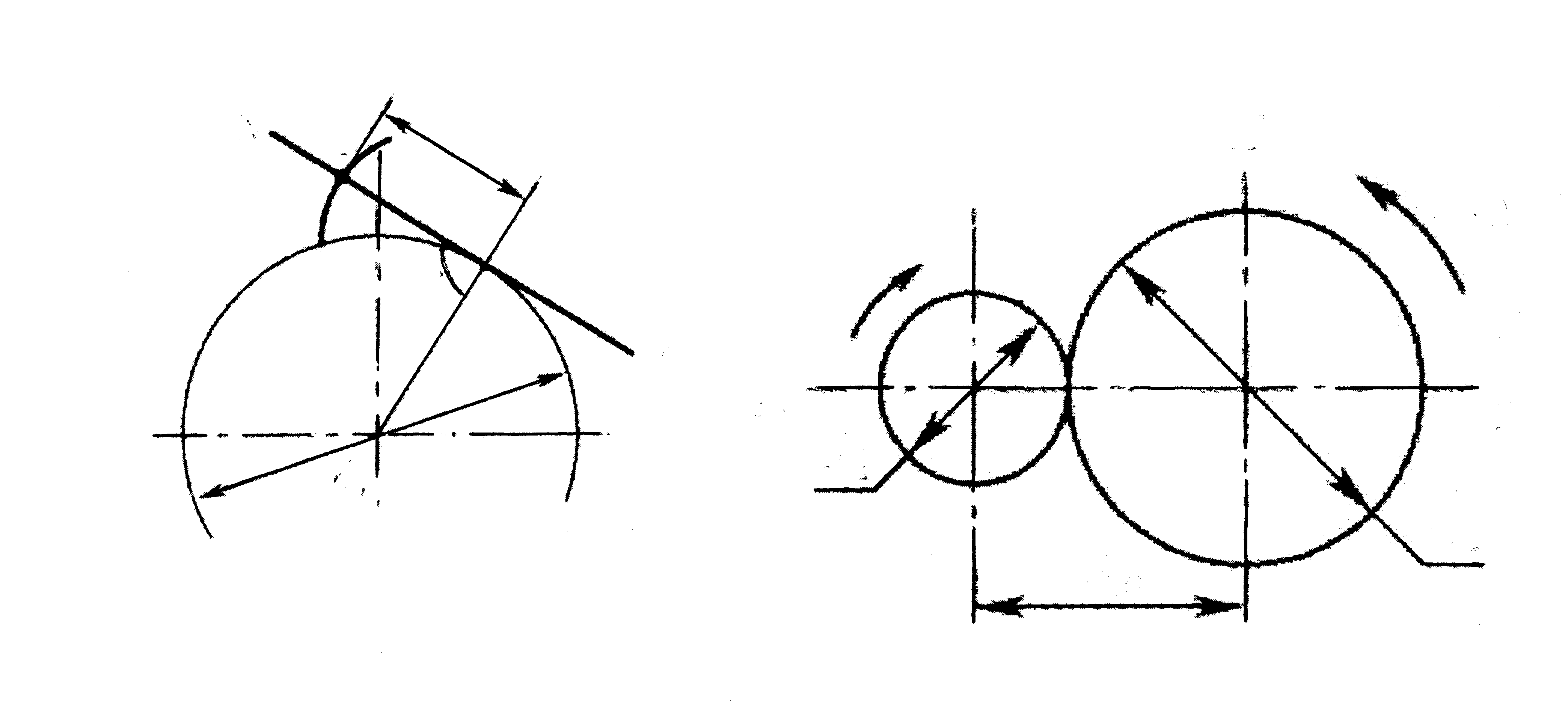
n 1 |
aw |
n 2 |
d 1 |
z 1 |
d 2 |
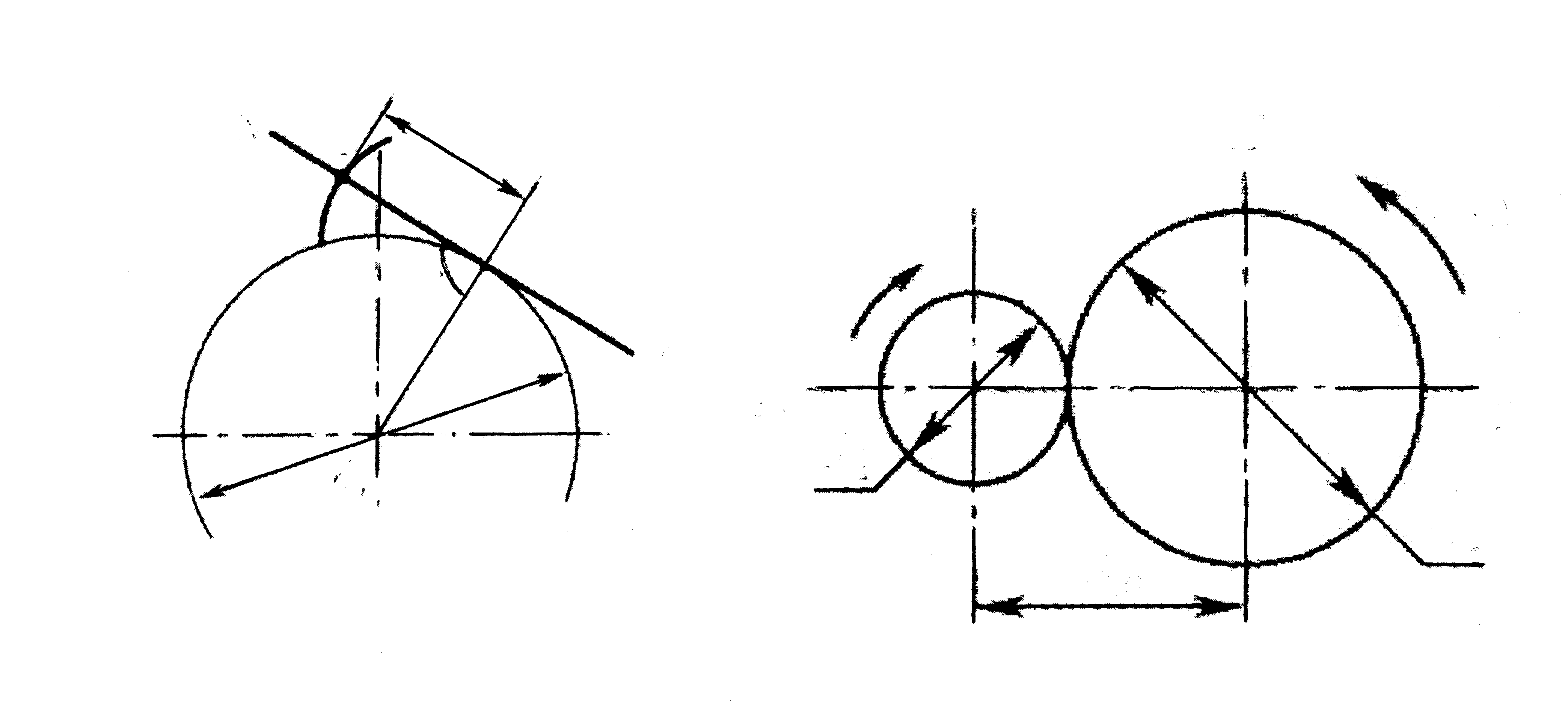
N |
N |
N 1 |
90° |
ρ |
db |
Прямозубое колесо нарезается с помощью долбяка или инструментальной рейки (рис.3.8а,б). Долбяк совершает возвратно-поступательное движение вдоль оси заготовки и вращается вместе с ней. При нарезании зуборезной гребенкой заготовка вращается вокруг своей оси, а рейка 1 совершает возвратно-поступательное движение параллельно оси заготовки 2 и поступательное движение по касательной к ободу заготовки.
Окружность зубчатого колеса, на которой шаг p и угол зацепления равны углу и шагу профиля α инструментальной рейки называется делительной. Её диаметр обозначают d. На рейке делительной плоскостью называют такую, на которой толщина зуба равна ширине впадины (рис.3.9).
+x |
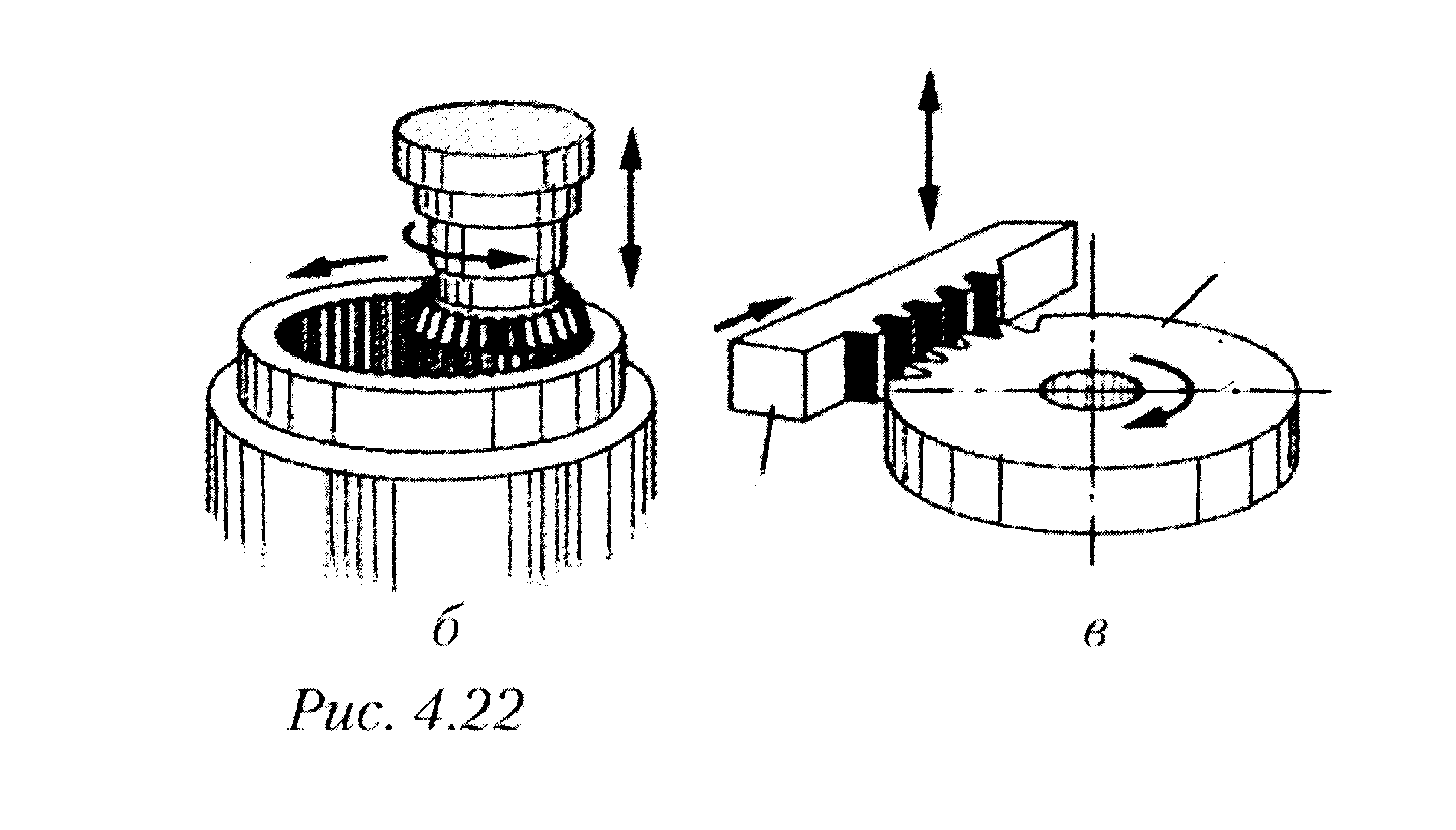
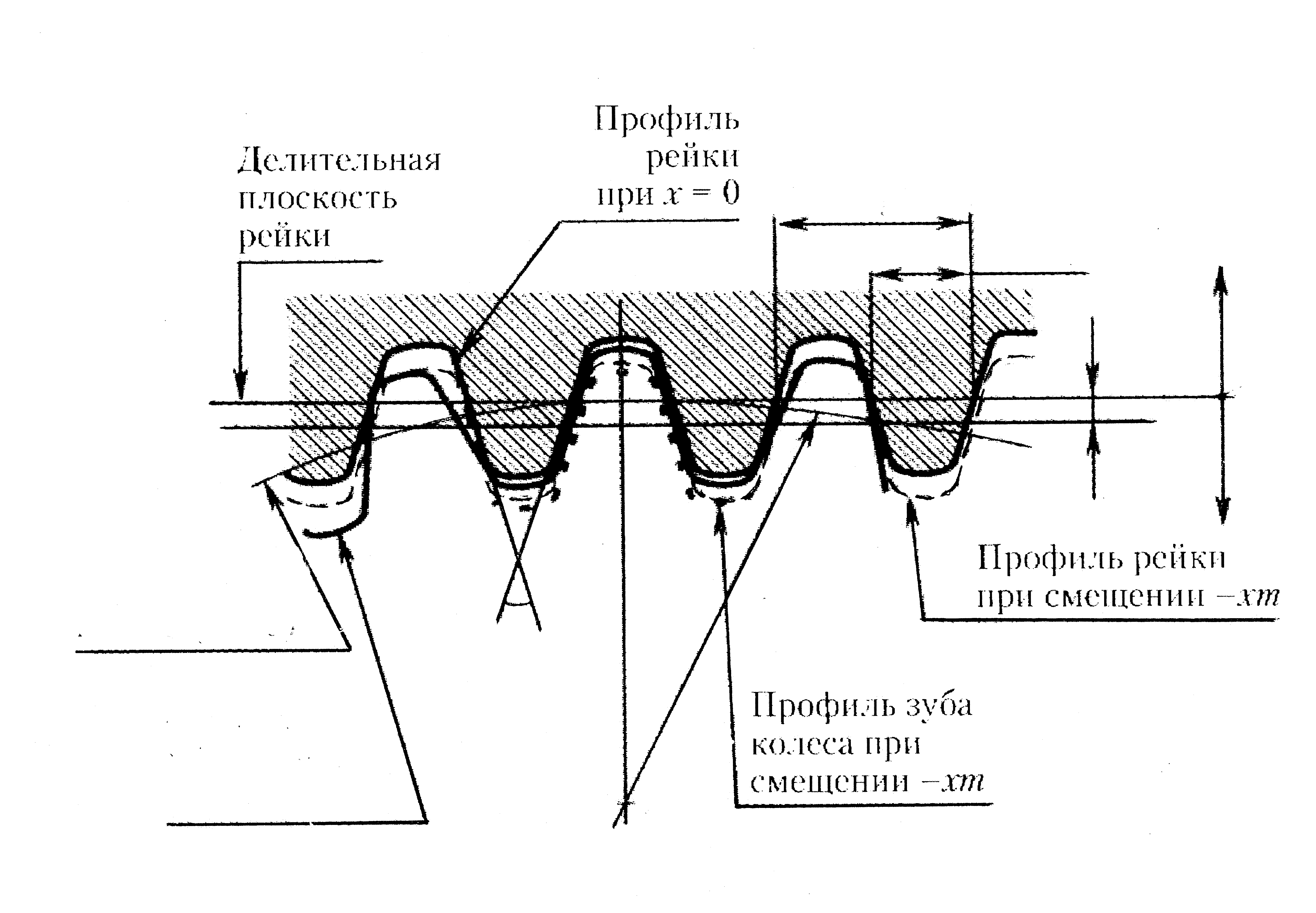
Рис.3.9 |
Рис.3.8 |
б) |
а) |
Делительная окружность колеса |
Профиль зуба колеса (х = 0) |
Профиль зуба колеса (- xm) |
Профиль рейки при смещении х = 0 |
Делительная плоскость рейки |
Профиль рейки (- xm) |
pt |
0,5 pt |
- x |
- xm |
d |
2 α |
O |
При вращении зубчатых колёс зуб колеса 2 входит в контакт с вершиной зуба колеса 1 в точке В (рис.3.10а). При дальнейшем вращении контакт смещается к его вершине от впадины. Геометрическое место точек контакта профилей, которое они занимают в процессе работы пары зубьев, называется линией зацепления. Эвольвентные профили зубьев в точке контакта имеют общую нормаль, представляющую собой прямую касательную к основным окружностям колёс, независимо от расположения контакта. Поэтому линия зацепления N - N является прямой. Эта линия определяет начало входа пары зубьев в зацепление и выхода из него. Отрезок АВ, ограниченный окружностями вершин зубьев колеса и шестерни, называется активным участком линии зацепления. Нормальные силы в контакте двух зубьев направлены по нормалям к их профилям, то есть вдоль линии зацепления. Это обеспечивает постоянство передаточного отношения по вращающему моменту.
Линия, соединяющая центры зубчатых колес называется межосевой. Точка пересечения линии зацепления и межосевой называется полюсом зацепления. Окружности, перекатывающиеся одна по другой без скольжения, называются начальными. Их диаметры обозначаются dω 1и dω 2. Полюс может быть определен как точка касания начальных окружностей. Угол α, образованный перпендикуляром к межосевой линии с линией зацепления называется углом зацепления.
Окружной делительный шаг p – это расстояние между одноименными профилями соседних зубьев, измеряемое по дуге делительной окружности. Основным параметром зубчатого зацепления является модуль, представляющий собой отношение делительного шага к числу π
Рис.3.10 |
M 1 |
a) |
б) |
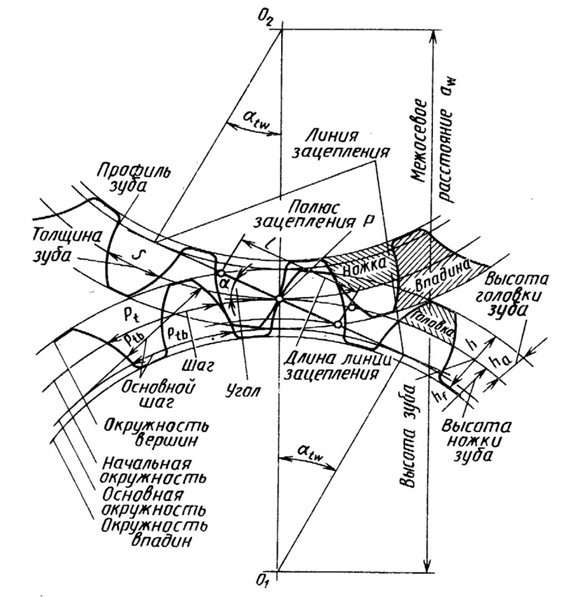
dw 1 |
O1 |
A |
O2 |
M 2 |
dw 2 |
da 1 |
da 1 |
df 1 |
df 2 |
α |
α |
αw |
ρ 1 |
ρ 2 |
z 1 |
z 2 |
N |
N |
P |
B |
90° |
90° |
bw |
aw |
ГОСТ предусматривает угол зацепления α = 20°, высоту головки зуба ha = m, высоту ножки зуба hf = 1,25 m (рис.3.10б).
Диаметры делительных окружностей колес определяются через модуль зацепления зависимостями
где z 1, z 2 – число зубьев первого и второго колеса.
Силы в зацеплении цилиндрических передач
Рассмотрим цилиндрическую передачу с косым зубом. Угол наклона зуба к осевой линии зубчатого колеса β составляет 8...20° (рис.3.11). Сверху показано сечение зуба нормальной плоскостью n - n. В контакте зубьев возникает нормальная сила направленная вдоль нормали к поверхностям зубьев, составляющей угол αn – угол зацепления в нормальном сечении. Начало координат выберем в полюсе зацепления на середине зубчатого венца.
Сила взаимодействия раскладывается на три составляющие
где Ft = 2 M/d – окружная сила;
M – вращающий момент;
– радиальная сила;
αt – угол зацепления в торцевом сечении;
Нормальная к поверхности зуба сила равна
В расчётах зубьев на прочность учитывают динамические нагрузки путём умножения номинальных момента и силы
на коэффициент динамичности k дин
,
,
где k дин принимают равным 1,05...2.
β |
n |
Fn |
αn |
Fz |
Ft |
Fxz |
Fn |
Fy |
Fy |
Ft |
Fz |
Fxz |
n |
β |
αt |
βb |
αn |
z |
x |
а) |
Рис.3.11 |
б) |
Удельная нагрузка в расчётах на контактную выносливость определяется с учетом ряда коэффициентов
где
– коэффициент, учитывающий распределение нагрузки между зубьями;
– коэффициент, учитывающий неравномерность распределения нагрузки по ширине зуба;
– коэффициент, учитывающий дополнительную динамическую нагрузку.
При расчете на выносливость при изгибе удельная нагрузка определяется с учетом аналогичных коэффициентов.
Расчёт зубьев на прочность
Расчет по контактным напряжениям
Переменные контактные напряжения являются причиной усталостного разрушения рабочей поверхности зубьев. Они приводят к появлению в поверхностном слое трещин и выкрашиванию частиц материала.
Максимальные контактные давления определяются по формуле Герца
где – удельная нагрузка;
– удельная окружная сила;
– приведенный модуль упругости;
Е 1, Е 2 –модули упругости материалов колес;
– приведенный радиус кривизны поверхностей зубьев, знак + берётся для выпуклых поверхностей.
Контактные напряжения не одинаковы по высоте зуба. В связи с тем, что выкрашивание наблюдается у делительной окружности, максимальное напряжение определяют для положения, когда начальная точка контакта зубьев находится в полюсе зацепления.
Если контакт зубьев располагается в полюсе P, радиусы кривизны профилей зубьев равны (рис.3.10)
Учитывая это, а также выражение для q, для максимальных контактных напряжений, получаем
,
где u – передаточное число,
знак «+» берется при внешнем зацеплении;
– коэффициент, учитывающий форму поверхностей зубьев в полюсе, при α = 20°, ZH = 2,5;
– коэффициент, учитывающий механические свойства материалов колёс, для стальных колёс
– коэффициент, учитывающий суммарную длину контактных линий с учётом перекрытия.
Коэффициент торцевого перекрытия определяет плавность работы передачи. Он равен отношению угла поворота колеса от входа торцового профиля зуба в зацепление до выхода к угловому шагу 2 π / z, или отношению длины активного участка линии зацепления к окружному шагу. Для прямозубых передач он должен быть 1,25..1,9.
Приближённая формула для его определения
В расчётах на выносливость используется кривая контактной выносливости. Если задан ресурс работы зубчатой передачи Th, то число циклов изменения контактных напряжений равно
NHЕ = 60 сnTh,
где с – число контактов одной поверхности зуба за один оборот;
n – частота вращения.
σH lim i |
σH lim |
NH |
NHE |
Рис.3.12 |
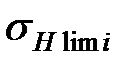
Допускаемые контактные напряжения равны
,
где SH = 1,2...1,35 – запас прочности.
Условие контактной прочности
Межосевое расстояние для стальных колёс определяют по формуле
где М 1 – расчётный вращающий момент на шестерне в H·мм;
коэффициент KH учитывает неравномерность распределения нагрузки по ширине зуба;
– относительная ширина зуба, принимается равной 0,1…0,3.
Модуль связан с межосевым расстоянием зависимостью
Расчет зуба на прочность при изгибе
Рис.3.13 |
опасное |
сечение |
Ft |
F |
Fr |
d |
df |
σ |
σсж |
σи |
s |
h 1 |
α |
F |
Ft = 2 M 1/ d 1, Fr = Ft tg α.
После введения коэффициента KF, учитывающего распределение нагрузки между зубьями, неравномерность его по ширине зуба и динамическую добавку, внутренние усилия в опасном сечении зуба равны
M из = FtKFh 1,
N = Fr = FtKF tg α.
Растягивающие напряжения в опасной точке сечения
где – момент сопротивления;
A = bs – площадь сечения;
s – толщина зуба у основания.
После умножения и деления на m получаем
где – коэффициент формы зуба.
Для внешнего зацепления
Если задан ресурс Th, число циклов нагружения зуба равно
NNE = 60 cnTh.
С использованием кривой выносливости по значению
NNE определяется предел ограниченной выносливости зубьев при изгибе для отлулевого цикла σF lim.
Допускаемое напряжение в опасном сечении зуба равно
,
где SF = 1,55…1,75 – коэффициент запаса прочности при изгибе.