Назначение уплотнений – защитить полость подшипника от проникновения в неё пыли, влаги, абразивных частиц и препятствовать вытеканию смазочного материала. По принципу они делятся на контактные, бесконтактные, комбинированные. В контактных герметизация достигается за счёт плотного прилегания уплотняющих элементов к подвижной поверхности вала. В бесконтактных – за счёт малых зазоров между сопрягаемыми элементами.
На рис.3.26 показаны контактные уплотнения:
а – войлочными кольцами (сальниконовые), работает на пластичном смазочном материале. Контакт колец 2 с валом обеспечивается за счёт предварительного натяга;
б – манжетное. Контакт рабочей кромки манжеты 3, изготовленной из резины, с валом 1 обеспечивается за счет предварительного натяга и поджатием браслетной пружины 2. Кромка-пыльник 5 для защиты от пыли;
в – манжетное с фасонной шайбой 2, шайба фиксируется гайкой 1 толщиной 0,3…0,5 мм.
Бесконтактные уплотнения работают за счёт сопротивления протеканию смазочного материала через узкие щели или каналы с резко изменяющимися проходными сечениями. Они делятся на статические и динамические.
г – щелевое, степень герметизации уплотнения зависит от величины зазора и длины щели;
д – жировыми канавками, которые при сборке заполняют пластичным смазочным материалом;
е – лабиринтное радиальное;
ж – аксиальное лабиринтное, лабиринтная втулка 4 составная;
з – спиральное, нарезка прямоугольного или треугольного профиля обеспечивает перемещение смазочного материала во внутреннюю полость узла.
Соединения
Соединения делятся на разъемные и неразъемные.
Разъемные соединения допускают сборку и разборку без повреждения материалов деталей. К ним относятся резьбовые, шпоночные, шлицевые, штифтовые, профильные.
Резьбовые соединения
Основные детали резьбовых соединений – болты, винты, шпильки, гайки и шайбы. Болт это стержень с головкой 1 на одном конце и резьбой на другом, на который навинчивается гайка 3 (рис. 3.27а). Шайба 2 подкладывается под головку болта для снижения напряжений смятия материала детали, для предохранения защитного покрытия соединяемых деталей. Болты применяются для соединения деталей сравнительно небольшой толщины. Нарезать резьбу в сое
диняемых деталях при этом не требуется.
Если одна из деталей имеет большую толщину, в ней нарезается резьба. Вворачиваемый в неё стержень называется винтом (рис.3.27б). В шпильке оба конца являются нарезными (рис.3.27в). Их применяют вместо винтов, если материал соединяемой детали с резьбовым отверстием не обеспечивает прочности резьбы при частых сборках и разборках.
Основным элементом резьбового соединения является резьба.
По назначению резьбы делятся на крепежные и резьбы для ходовых механизмов, по направлению линии витков на правые и левые, по числу заходов на однозаходные и многозаходные.
Основной крепежной резьбой является метрическая резьба с треугольным профилем витка (рис.3.28 а). Она характеризуется параметрами: наружный d, средний d 2 и внутренний d 1 диаметры, шаг p, угол профиля α, высота исходного треугольника H, рабочая высота профиля h. Основной является резьба с крупным шагом. Стандартом предусмотрены резьбы с мелкими шагами p /3, p /4, p /5.
Трубная резьба предназначена для герметичного соединения труб (рис.3.28б). Она имеет треугольный профиль, но со скругленными вершинами и впадинами.
В массовом производстве резьба получается накаткой. Все резьбы при стационарных нагрузках являются самотормозящимися. При работе в условиях систематических вибраций условия самоторможения нарушаются.
Стопорение резьбовых соединений осуществляется применением: а – контргаек; б – пружинных шайб (Гровера) в – шайб стопорных с наружными или внутренними зубьями (рис3.29).
В верхней части самоконтрящейся гайки делают прорези. После нарезания резьбы верхнюю часть гайки обжимают, уменьшая диаметр. Самоконтрящаяся гайка также выполняется с завальцованным внутрь полиамидным кольцом. Резьба в нем образуется после навинчивания гайки (рис.3.29г). Корончатые гайки стопорят шплинтами (рис.3.29д).
Расчет болтов
Если болт поставлен в отверстие с зазором и работает на растяжение, внутренний диаметр резьбы болта определяется из условия
,
где допускаемое напряжение [ σ ] принимается равным (0,2...0,4) σ т.
Если болт поставлен без зазора, является призонным и нагружен поперечными силами
,
где допускаемое напряжение [ τ ср] = (0,2...0,3) σ т.
Если болт поставлен с зазором и работает на срез, взаимное смещение деталей предотвращается созданием силы трения затяжкой соединения. При коэффициенте трения в контакте деталей f = 0,1...0,2 внутренний диаметр резьбы определяется зависимостью
.
Диаметр болта с предварительной затяжкой в 2-3 раза больше чем призонного болта.
Шпоночные соединения
Для соединения вала со ступицей насаженной на него детали используются призматические, сегментные цилиндрические шпонки (рис.3.30а,б). Напряженные соединения выполняются с клиновыми шпонками (рис. 3.31).
В паз на валу эти шпонки устанавливаются по посадке с натягом, а в ступицу детали – с зазором. Работают шпонки на срез и смятие. Лимитирующим является расчет на смятие
где М – вращающий момент;
d – диаметр вала;
l p – рабочая длина шпонки;
t 2 – глубина врезания шпонки в ступицу;
[ σ см] – допускаемое напряжение, принимается равным 0,8 σ т при постоянной нагрузке, 0,4 σ т при переменной.
Шлицевые соединения
Шлицевые соединения образуются выступающими на валу 1 зубьями и шлицами на детали 2 (рис.3.32). Их размеры назначаются в зависимости от диаметра вала. Центрирование деталей осуществляют по внутреннему или наружному диаметру, либо по боковым граням. Шлицевые соединения обеспечивают передачу больших моментов, более высокую прочность вала. Шлицы шлицевых соединений рассчитываются на смятие
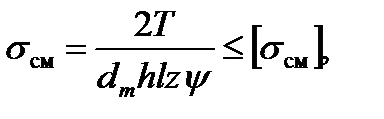
где dm – средний диаметр соединения;
h – высота поверхностей контакта зубьев;
l –длина шлицев;
ψ = 0,7...0,8 – коэффициент, учитывающий неравномерное распределение нагрузки между зубьями.
Штифтовые соединения
В слабонагруженных передачах вращающего момента, а также для фиксации положения одной детали относительно другой применяют штифтовые соединения. Используются штифты цилиндрические, конические с конусностью 1:50, пружинные. Размеры штифтов характеризуются диаметром d шт и длиной l. При установке штифтов отверстия в соединяемых деталях сверлят и развертывают в сборе. В соединениях, требующих частой сборки и разборки, штифты ставятся по переходной посадке. От выпадения они фиксируются пружинным кольцом (рис.3.33а). На рис.3.33б показано неразборное соединение ступицы зубчатого колеса и вала с помощью цилиндрического штифта. Концы штифта кернят или засверливают и после сборки
раз
валь
цовывают.
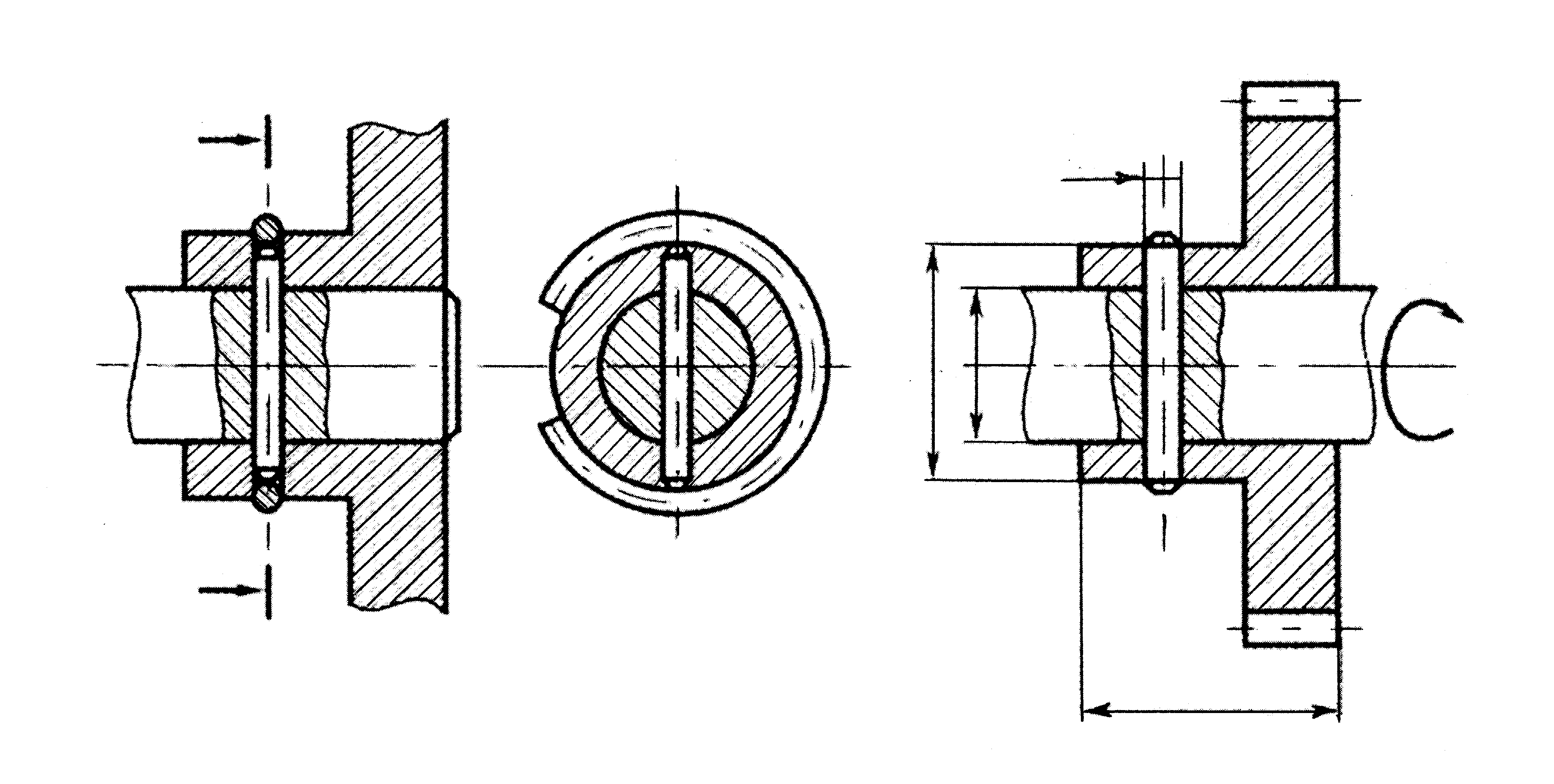
Штифты рассчитывают на срез и смятие. Условие прочности на срез
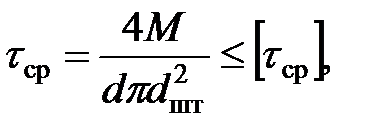
где [ τ ср] = 35...75 МПа – допускаемое напряжение на срез.
При проверке на смятие вычисляется напряжение
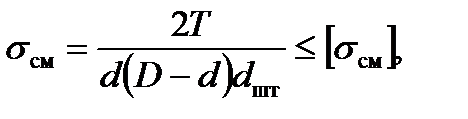
где D, d – наружный и внутренний диаметр ступицы.
Допускаемое напряжение смятия [ σ см] принимается равным 150...180 МПа.
Заклепочные соединения
Заклепочные соединения относятся к классу неразъемных соединений. Они применяются в особо ответственных конструкциях (пятник вагона, мостовые фермы), конструкциях воспринимающих вибрационные нагрузки, для соединения несвариваемых деталей.
На рис.3.34 показан мост Свободы через реку Дунай в Будапеште, соединяющий Буду и Пешт, имеющий длину 333 м, ширину 20 м. Он был построен в 1894-1896 годах по проекту Яноша Фекетехази, собран на заклепках.
Заклепка представляет собой стержень круглого поперечного сечения с головками на концах (рис.3.35а). Закладная головка выполняется заодно со стержнем, а замыкающая формируется при клепке. Заклепочные соединения образуют постановкой заклепок в совмещенные отверстия соединяемых элементов и расклепкой с осаживанием стержня. Заклепки стягивают соединяемые детали, в результате чего вся внешняя нагрузка или её часть передается силами трения на поверхности стыка.
Заклепочные соединения делятся на прочные и прочноплотные.
Прочные соединения служат для восприятия внешней нагрузки и передачи её с одного элемента на другой. Прочноплотные обеспечивают также герметичность баков, кабин и других сборок. В несиловых соединениях применяют заклепки с сердечником. Такая заклепка состоит из сердечника 1 и пистона 2 (рис.3.35б). Замыкающая головка образуется при протягивании сердечника через отверстие пистона. Выступающую часть сердечника удаляют.
Расчет элементов соединения проводят на срез заклепок и листа, разрыв листа и срез края листа. Трением между соединяемыми деталями пренебрегают.
Необходимое число заклепок определяют из условий:
прочности заклепок на срез
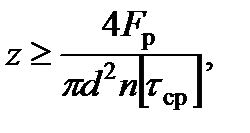
где F р – расчетная сила, F р = F э f;
F э – эксплуатационная нагрузка;
f = 1,5...2,0 – коэффициент безопасности;
n – число плоскостей среза;
– диаметр заклепки;
δΣ – сумма толщин соединяемых деталей,
смятие соединяемых деталей
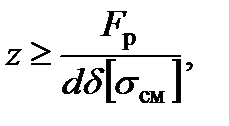
где [ τ ср] = 0,2 σ в, [ σ см] = (0,4...0,5) σв.
Соединяемые листы рассчитывают на разрыв между заклепками
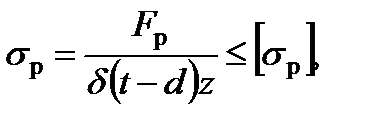
и на срез края листа

где t – расстояние между осями заклепок;
е – расстояние от оси заклепки до края листа.
Сварные соединения
Сварные соединения образуются за счет сил молекулярного взаимодействия материалов соединяемых деталей при местном нагреве до расплавленного состояния или при пластическом деформировании нагретых деталей. Они имеют низкую стоимость изготовления, обеспечивают прочность близкую к прочности основного материала.
Недостатки сварных соединений: появление остаточных напряжений, внутренних дефектов, коробление деталей. Разогрев деталей осуществляется термическим, термомеханическим или механическим способом. Процессы сварки могут быть ручными или автоматическими. При дуговой сварке разогрев деталей осуществляется электрической дугой, возникающей между металлическим электродом 1 и свариваемыми деталями (рис.3.36а). Для защиты от окисления деталей из легированных сталей и цветных сплавов сварку проводят под слоем флюса или в среде инертных газов – аргона или гелия. Толщина свариваемых деталей может быть от 1 до 130 мм.
Для соединения деталей из легированных сталей, алюминиевых и медных сплавов, тугоплавких металлов применяют электронно-лучевую сварку, а деталей малой толщины 0,1...0,5 мм – плазменно-лучевую. При электронно-лучевой сварке разогрев осуществляется в вакуумной камере потоком электронов, испускаемых вольфрамовой спиралью 1, проходящих через кольцевой анод 2 (рис.3.36б).
Плазменно-лучевая сварка проводится струей нейтрального газа, ионизированного при пропускании через электрическую дугу между вольфрамовым электродом 1 и медным соплом 2 (рис.3.36в). Струя плазмы формируется электромагнитным полем. Её температура достигает 4000°С.
При газовой ацетилено-кислородной сварке детали разогревают высокотемпературным пламенем (рис.3.36г). В качестве присадочного материала для заполнения шва используют стальную проволоку.
При термомеханической сварке разогрев происходит при прохождении электрического тока между двумя электродами, сдавливающими соединяемые детали.
При точечной сварке детали располагаются между электродами 1 и 2, которые периодически сжимаются, образуя точечный шов. При роликовой сварке образуется сплошной шов (рис.3.36д, е).
В зависимости от расположения деталей различают сварные соединения стыковые, нахлесточные, с накладками, угловые и тавровые.
Стыковые соединения выполняют стыковыми швами (рис.3.37) односторонними или двухсторонними. На кромках деталей большой толщины выполняют фаски.
Нахлесточные соединения могут быть с односторонним или двухсторонним швом (рис.3.38). Различают лобовые б), фланговые в) и косые г) швы.
Соединения с накладками применяют в случаях, когда стыковые соединения не обеспечивают требуемой прочности. Они бывают с одной и двумя накладками (рис.3.39).
Тавровые и угловые соединения выполняют угловыми швами. В угловых соединениях детали свариваются по кромкам (рис.3.40б), а в тавровых одна деталь кромкой приваривается к боковой поверхности другой (рис.3.40а).
По форме швы бывают: равнобедренный треугольник с катетом k – нормальный шов (рис.3.41а); с соотношением сторон 1:1,5 или 1:2 (рис.3.41б); выпуклый (рис.3.41в); вогнутый (рис.3.41г).
Расчет швов на прочность
Если стыковой шов нагружен растягивающей силой P и моментом M, действующим в срединной плоскости соединяемых листов, условие прочности для него
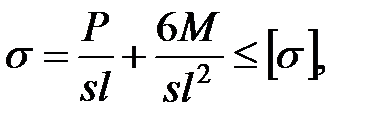
где s – толщина швов;
l – длина шва;
[ σ ] – допускаемое напряжение для основного материала деталей.
Прочность угловых швов нахлестного соединения (рис.3.42) рассчитывается
при нагружении силой Р
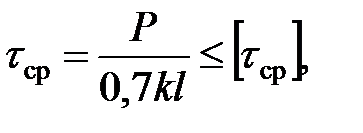
где k – катет шва;
l - суммарная длина шва;
[ τ ср] = (0,5...0,65) [ σ р] – допускаемое напряжение среза шва,
при нагружени моментом М

где ρ max– расстояние наиболее удаленной точки от центра тяжести опасных сечений швов, которые рассматриваются как прямоугольники со сторонами, одна из которых равна длине шва, а другая 0,7 k;
Jp = Jx + Jy – полярный момент инерции площади сечений шва.
Муфты
Муфты – устройства для соединения валов и передачи вращающего момента без изменения угловой скорости. Концы соединяемых валов имеют отклонения от требуемого взаимного расположения, обусловленные погрешностями монтажа, вызванные эксплуатационными нагрузками: осевое ∆, радиальное δr, угловое α (рис.3.43). Муфты могут компенсировать погрешности расположения осей валов, демпфировать крутильные колебания, предохранять механизмы от перегрузок.
По принципу действия муфты делятся на механические, электрические и гидравлические. По управляемости они бывают неуправляемые, не позволяющие рассоединять валы в процессе работы, управляемые, позволяющие принудительно соединять и рассоединять ведущий и ведомый валы при работе, самоуправляемые, которые автоматически рассоединяют валы при изменении заданного режима работы.
Ограничимся рассмотрением некоторых типов неуправляемых муфт.
Глухие муфты
На рис.3.44а,б показаны глухие втулочные муфты, а на рис.3.44в фланцевая муфта. Глухие муфты допускают радиальное смещение осей валов не более 0,05 мм. Помимо крутящего момента они предают изгибающий момент, поперечные и осевые усилия.
Втулочная муфта представляет собой втулку, соединяющую ведущий и ведомый валы. С валом она соединяется коническими штифтами, шпонками, либо посредством шлицевого соединения. Расчет элементов муфт на прочность выполняется методами, рассмотренными для соединений вала со ступицей.
Поперечно-свертная фланцевая муфта состоит из двух полумуфт 2 и 4, плоскость стыка которых перпендикулярна оси вала (рис.3.44в). Полумуфты соединяются между собой болтами. Если используются призонные болты 3, их рассчитывают на срез
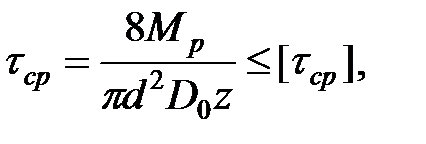
где d – диаметр стержня болта;
z – число болтов;
Mp = K 1 K 2 M ном,
Mp, M ном – расчетный и номинальный крутящие моменты;
K 1 – коэффициент безопасности, K 1 = 1,0…1,8;
K 2 – коэффициент режима работы, K 2 = 1,0 – при равномерной нагрузке, K 2 = 1,8…1,5 – при ударной нагрузке.
При установке болтов в отверстия фланцев с зазором центрирование полумуфт осуществляется по специальным пояскам. Вращающий момент передается силами трения. Усилие затяжки болтов определяют с использованием зависимости
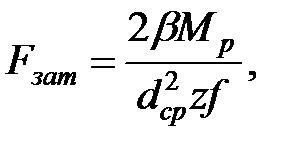
где β = 1,2…3,5 – коэффициент запаса сцепления;
dср – средний диаметр кольцевой поверхности трения;
f = 0,15…0,2 – коэффициент трения.
Компенсирующие муфты
Компенсирующие муфты предназначены для компенсации осевых, радиальных и угловых смещений валов.
Поводковая муфта состоит из двух полумуфт и пальца 1, закрепленного на плоской пружине 2, соединенной с одной из полумуфт (рис.3.45а). Палец входит в паз, выполненный во второй полумуфте. Муфта позволяет компенсировать радиальную погрешность установки валов до 5 мм. Она применяется в механизмах приборного типа.
Зубчатая муфта состоит из двух обойм 1 с внутренними зубьями, находящимися в зацеплении с двумя зубчатыми втулками 2 (рис.3.45б). Заготовку втулки под нарезку зубьев обтачивают по сферической поверхности. Обоймы стягиваются болтами. Смещения валов компенсируются перекосом втулок относительно обойм за счет осевых зазоров и сферической поверхности вершин зубьев втулок. Напряжения смятия в контакте зубьев сильно зависят от угла перекоса осей. При изменении его от 0 до 1°30´ они увеличиваются в 3 раза.
Кулачково-дисковая муфта позволяет соединить валы со значительным радиальным смещением, до 0,04 d, где d – диаметр вала. Она допускает незначительные угловые смещения. Муфта состоит из двух полумуфт и промежуточного диска с кулачками (рис.3.45в), расположенными крестообразно и входящими в пазы полумуфт. Критерием работоспособности таких муфт является износостойкость рабочих граней.
Шарнирная муфта состоит из двух вильчатых втулок 1 и крестовины 2, шарнирно соединенной с концами вилок (рис.3.45г). Она допускает угловые смещения осей валов до 45°. Критерием работоспособности шарнирных муфт является величина давления в подшипниках скольжения. Допускаются давления до 35…40МПа.
Упругие муфты
В упругие муфты включаются элементы, предназначенные для уменьшения динамических нагрузок при крутильных колебаниях, обеспечения угловых, осевых и радиальных смещений соединяемых валов. В качестве упругих элементов используют вкладыши из резины, полиуретана, металлические пружины, пластины, или пакеты пластин.
Муфта с упругим элементом в виде тороидальной оболочки состоит из двух полумуфт с упругим элементом в виде выпуклой или вогнутой оболочки, работающей на сдвиг, и фланцев, зажимающих оболочку (рис.3.46а). В зависимости от размеров муфт они допускают смещения: радиальное 1…5 мм, осевое 2…6 мм, угловое 1,5…2°. Муфты с упругими элементами из эластомеров более технологичны, однако менее долговечны.
Втулочно-пальцевая муфта состоит из двух полумуфт и пальцев 1, закрепленных на фланце полумуфты ведущего вала(рис.3.46б). На пальцы напрессованы резиновые втулки 2, входящие в отверстия на фланце полумуфты ведомого вала. Пальцев может быть 4-10. Резиновые втулки работают на сжатие. Их расчет ведётся из условия прочности по допускаемым давлениям между пальцами и резиновыми втулками

где
d п – диаметр пальца;
z – число пальцев;
Mp – вращающий момент;
l – длина втулки;
Dm – диаметр окружности, на которой расположены центры пальцев.
Допускаемое давление принимают равным 3 МПа.
Пальцы рассчитывают на изгиб.
ЛИТЕРАТУРА
1. Тарг С.М. Краткий курс теоретической механики/ С.М. Тарг. – М.: Высш. шк., 2008. – 416 с.
2. Мещерский И.В. Сборник задач по теоретической механике/ И.В. Мещерский. – М.: Наука, 2008. – 448 с.
3. Сборник заданий для курсовых работ по теоретической механике/ под ред. А.А. Яблонского. – М.: Высш. шк., 2008. – 382 с.
1. Феодосьев В.И. Сопротивление материалов. Учеб. для вузов. Изд. 13-е стереотип.– М.: Изд-во МГТУ им. Н.Э. Баумана, 2005. – 592 с.
2. Сакало В.И. Сопротивление материалов: учебное пособие/ В.И. Сакало. – Брянск: БГТУ, 2009. –528 с.
3. Писаренко Г.С., Яковлев Л.П., Матвеев В.В. Справочник по сопротивлению материалов. – Киев: Наукова думка, 1975. – 704 с.
4. Сакало В.И. Сборник заданий для расчетно-графических работ по сопротивлению материалов [Текст] + [Электронный ресурс] / В.И. Сакало.– Брянск: БГТУ, 2011. – 251 с.
5. Сборник задач по сопротивлению материалов с теорией и примерами /Б.А. Антуфьев, А.Г. Горшков, О.В. Егорова и др.; Под ред. Академика А.Ю. Ишлинского – М.: Изд-во МАИ, 2001. – 544 с.
6. Джамай В.В., Самойлов Е.А., Станкевич А.И., Чуркина Т.Ю. Прикладная механика: учебник для бакалавров / В.В. Джамай, Е.А. Самойлов, А.И. Станкевич, Т.Ю. Чуркина под ред. В.В. Джамая. – 2-е изд. испр. и доп. - М.: Юрайт, 2013. – 360 с.
Гоголина И.В. Детали машин. Контрольные задания. Примеры решения: Учебно-методический комплекс для студентов механических и технологических специальностей заочной формы обучения / И.В. Гоголина, А.М. Попов, М.С. Сорочкин.- Кемерово: КемТИПП, 2003 – 132 с.
8. Решетов Д.Н. Детали машин: учебник для студентов машиностроительных и механических специальностей вузов.– М.: Машиностроение, 1989.–496 с.