![]() | ![]() | ||||||||
![]() | |||||||||
| |||||||||
| |||||||||
Расстояния | Габаритные размеры станков | |||||||
до 1,8х0,6 м | до 4,0х2,0 м | св. 4,0х2,0 м | ||||||
Между станками по фронту а (схема а) Между тыльными сторонами станков в (схема а)" Между станками при расположении их фронтом один к другому и обслуживании: одним рабочим одного станка (схема в) с одним рабочим двух станков (схема в) h. Между станками при расположении их "в затылок" d (схема б) | – | |||||||
От стен или колонн здания (схема г): до тыльной стороны станка е до боковой стороны станка р до фронта станка l | ||||||||
Оптимальным считается тот вид транспортных средств, при использовании которого приведенные затраты на транспортирование грузов будут наименьшими.
При выборе транспорта рекомендуется учитывать следующее. У каждого рабочего места располагают две тары: одна – для заготовок, поступающих на обработку, другая – для обработанных деталей, которые надо передать на следующую операцию.
Перемещение тары от операции к операции осуществляют рабочие-станочники; время на транспортирование перекрывается машинным временем, так как обработка деталей ведется на автоматизированном оборудовании.
К недостаткам указанного способа межоперационного транспортирования заготовок следует отнести загромождение площади пола в пролете, что затрудняет уборку помещения, затрату оператором физического усилия (до 200 – 2500 Н) при перемещении заполненной тары, наличие повышенного межоперационного задела деталей, что увеличивает стоимость незавершенного производства.
При транспортировании обрабатываемых деталей от станка к станку с помощью склизов или скатов, в которых используется гравитационный принцип действия, уменьшается незавершенное производство и затраты труда рабочих. Эти устройства представляют собой стационарные сварные конструкции из углового профиля с наклонными желобами (уклон 1:10; 1:15), свободно устанавливаемые в пролете. Скаты применяются для деталей типа тел качения, склизы – для деталей, не являющихся телами качения.Указанные транспортные устройства отличаются долговечностью и малой стоимостью, однако они также загромождают площадь цеха и затрудняют уборку помещения.
Межоперационное транспортирование мелких и средних деталей может осуществляться в тележках, движущихся по узким путям, которые проходят перед рабочим, если позволяет оборудование, что показано на рис. 5,а,б
Рис.5
При параллельно работающих станках в путь встраивают выдвижные секции, позволяющие по одному пути передавать тележки к нескольким станкам. С помощью тележек можно обслуживать станки с разной высотой загрузки, для чего встраивают пневмоподъемники, а пути делают с уклоном. Для удобства обслуживания станков путь оборудуют поворотными и откидными секциями для прохода рабочих.
Весьма распространенным средством для немежоперационного транспортирования тяжелых крупногабаритных деталей (блоков-, тормозных барабанов, картеров) являются приводные и неприводные роликовые конвейеры (рольганги), при этом применяются подъемные механизмы типа пневмо- или электроталей для установки деталей на станки или снятия с них. Если транспортируемые грузы не имеют плоской опорной поверхности (картер редуктора, коленчатый вал и др.), то их можно перемещать на поддонах по роликам конвейера. Преимущество роликовых конвейеров состоит в том, что они допускают пробуксовывание грузов и являются одновременно транспортными средствами и накопителями. Для деталей с массой до 200 кг усилие толкания на неприводных роликовых конвейерах (рольгангах)не превышает 40–60 Н, а время установки и снятия деталей со станка с помощью электротали составляет около 0,2 мин. Цена I м конструкции может быть принята равной 40 руб. при одинарной ширине рольганга и длине роликов 600 мм.
В случае обработки корпусных деталей роликовые конвейеры располагают так, чтобы образовались отводы от основной трассы к станкам, а также разрывы для прохода рабочих при многостаночном обслуживании. Если необходимы широкие (до 0,6 м) проходы, то на главной трассе могут быть сделаны откидные секции, обрывающие проход с помощью противовеса и перекрывающие его под действием силы тяжести перемещаемой детали. Поворотный стол и опрокидывающая секция, встроенные в роликовый конвейер, позволяют придавать тяжелой обрабатываемой детали нужное положение для последующей обработки.
В качестве межоперационных транспортных средств в поточных линиях применяются подвесные приводные и неприводные конвейеры локального действия; их используют даже на небольших участках линии в сочетании с рольгангами, скатами, склизами, электро- и пневмоподъемниками. Планировка участка с конвейерами локального действия показана на рис.6. Локальный конвейер представляет собой трассу из балок специального профиля, подвешиваемых к перекрытию или к невысоким металлоконструкциям (при наличии в пролете мостовых кранов). По полкам балок движутся каретки на роликах.
Рис.6
Транспортирование тяжелых крупных деталей или деталей в таре осуществляется подвесными конвейерами, при этом навеска и съем грузов (рис.7) производятся автоматически пневмоподъемниками. Далее грузы транспортируются напольными роликовыми конвейерами (приводными или неприводными).
![]() ![]() ![]() |
Рис.7
Движение кареток приводных подвесных конвейеров осуществляется с помощью разборной цепи от электродвигателя через редуктор. Обрабатываемые детали могутнавешиваться к кареткамна этажерочных подвесках (рис.8).
|
|
|
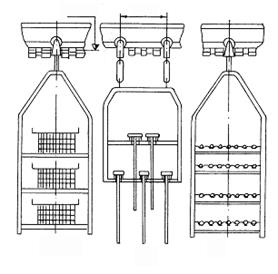
Рис.8
Скорость V конвейера (в м/мин):
V = аКн/(itk и ),
где а - шаг подвесок, м; К н– коэффициент неравномерности загрузки конвейера; К н = 1,0¸1,5; i - количество изделий на одной подвеске; k и = 0,85 ¸0,95.
В случае многооперационной обработки деталей (например, коленчатого вала двигателя), когда производительность станка сильно колеблется при среднем объеме выпуска мин. (2 < Т < 10) применяются неприводные подвесные конвейеры со свободным перемещением подвесок вручную, так же, как на рольганге, но при этом не загромождается площадь пола. В отличие от конвейера непрерывного действия в этом случае не требуется согласования скорости перемещения детали с тактом.
В современном массовом поточном производстве для автоматизации межоперационного транспортирования, установки на станки и снятия с них обрабатываемых крупных и средних деталей широко применяются устройства с гибкими связями. Эти устройства можно применять для однотипных деталей различных размеров, они допускают изменение межоперационных расстояний между станками, а также установку между ними накопителей межоперационных заделов. Кроме того, описываемые устройства не связаны между собой и не требуют жесткой конструктивной связи со станками. Вследствие этого транспортные устройства с гибкими связями имеют ряд преимуществ: при их применении возможны смена и подналадка инструмента на любом станке линии независимо от работы других станков, что повышает эффективность использования оборудования; в линию могут быть встроены новые операции или добавлены станки на "узких местах" при изменении объема выпуска. При серийном выпуске стоимость устройств с гибкими связями меньше стоимости транспортирующих механизмов с жесткими связями.
К основным элементам устройств, применяемых для автоматизации межоперационного транспортирования и установки деталей с помощью гибких связей, относятся автоматические руки (рис.9) или роботы, действующие по заданной программе.
Рис.9
Для перемещения обрабатываемых деталей от одних станков или автоматических линий к другим в соответствии с технологическим процессом служат транспортеры. Транспортер доставляет очередную обрабатываемую деталь на исходную позицию для захвата ее автоматической рукой и приемки детали, обработанной на данной операции, для дальнейшего перемещения.
В качестве транспортирующего механизма, а также для связи автоматических линий между собой широко применяются шаговые транспортеры, укладывающие при перемещении обрабатываемые детали в приемные гнезда напольных трасс. Наклонные участки, связывающие транспортерные установки одну с другой и служащие магазином-накопителем межоперационных заделов, представляют собой гравитационные трассы с подпружиненными флажками, по которым безударно скатываются обрабатываемые детали.
Для межоперационного транспортирования тяжелых деталей (например, блока цилиндров от одной автоматической линии с жесткими
связями к другой) применяются приводные рольганги или рольганги, в которых используется принцип гравитации.
Такие устройства делают даже многоэтажными (в два, три и четыре этажа), чтобы создать необходимые емкости для подвижного межоперационного задела при большом объеме выпуска. При снабжении их пневмоподъемными столиками, заталкивателями и выталкивателями, приводимыми в действие путевыми конечниками, они образуют автоматически действующие системы, легко приспосабливаемые к нужным межоперационным расстояниям и емкостям согласно требованиям производства.
2.3.5. Общая компоновка механосборочных цехов
Для разработки компоновочного плана цеха (корпуса), т.е. решения вопросов размещения всех входящих в него подразделений, технологу-проектанту необходимо предварительно определить основные параметры здания, обеспечивающие наиболее рациональное взаимное расположение участков с учетом существующих между подразделениями технологических связей и требований строительной техники.
I. Выбор параметров здания
Площадь и конфигурацию в плане зданий, предназначаемых для размещения механосборочных цехов, определяют предварительно по укрупненным показателям при разработке ТЭО строительства завода. В проектах механосборочных цехов эти данные окончательно уточняются на основании технологических расчетов.
Наиболее распространенной конструкцией зданий для размещения механосборочных цехов являются одноэтажные многопролетные здания прямоугольной формы с полом на бетонном основании и перекрытием, поддерживаемым системой колонн, образующих пролеты цеха. Колонны соединяются стропильными и подстропильными фермами, на которых укладываются перекрытия цеха.
Производственные здания, как правило, состоят из нескольких параллельных, по возможности однотипных пролетов, образуемых рядами колонн. Основными строительными параметрами такого здания в зависимости от характера размещаемого в нем производства, являются ширина пролета L – расстояние между продольными осями колонн; шаг колонн t 1– расстояние между их поперечными осями; высота пролета H – расстояние от поверхности чистого пола до низа несущих конструкций покрытия (рис.10). Ширина пролета и шаг колонн характеризует сетку колонн L × t 1.
В тех случаях, когда это вызывается требованиями технологического процесса, допускается наличие в одном здании пролетов различной ширины с разным шагом и высотой колонн. Такие многопролетные здания имеют покрытия с внутренними водостоками, что позволяет перекрывать большие производственные площади (в несколько сот тысяч квадратных метров). Форма зданий механосборочных цехов в плане преимущественно имеет вид прямоугольника или нескольких прямоугольников П- или Ш-образной конфигурации. Соотношение сторон прямоугольника в зависимости от общей площади здания, характера технологического процесса и организации производства выбирают равным 1:2 для зданий площадью до 100 тыс.м2 и 1:3 и более при больших площадях.
Рис.10. Основные размеры пролета здания и сетки колонн:
L – ширина пролета; t 1– шаг колонн; H – высота пролета;
L к– пролет мостового крана; Н к– высота расположения подкрановых путей;
1 – ось подкрановых путей; 2 –разбивочная ось здания
Выбор основных параметров здания – этажности, сетки колонн и высоты пролета определяется технологическим процессом, а также требованиями экономичности строительства, достигаемой при максимальном применении унифицированных строительных элементов и типовых конструкций.
Для многоэтажных зданий принята сетка колонн 6,0 х 6,0 мс допускаемой нагрузкой на междуэтажные перекрытия 10 – 25 кПа и сетка колонн 9,0 х 6,0 мс допускаемой нагрузкой 5 – 15 кПа (при высоте этажей 3,6; 4,8; 6,0 м).
Размеры унифицированных пролетов и грузоподъемность подъемно-транспортных средств в одноэтажных зданиях приведены в табл.19.
Таблица 19